Industrial production necessitates nitrogen gas of a certain purity level, yet many individuals may lack understanding regarding the methods of extracting nitrogen from the air. Not to worry, this article will enlighten you on how to separate nitrogen from the air. Read on to discover the following.
Why Do We Separate Nitrogen from Air?
In the atmosphere, nitrogen makes up a large proportion—at around 78%. Nitrogen is notably easy to obtain in high purity. Moreover, in addition to its accessibility, nitrogen offers a host of benefits. Non-toxic and non-flammable, nitrogen is a stable gas that resists reactions with other gases. As a gas commonly used for food preservation, its safety credentials are undoubtedly trustworthy.
How to Separate Nitrogen from Air?
· Cryogenic Distillation
Low-temperature distillation is quite a complex process. Initially, air is compressed, cooled to 10°C, and then purified using filtration equipment. As the temperature drops below the condensation point inside the expansion unit, nitrogen liquefies and is transferred to a storage tank. While storage tanks are cost-effective, transportation can present safety concerns such as delays and corrosion, resulting in both time and financial losses.
· Membrane Nitrogen Generator
Membrane nitrogen generation involves compressing air into compressed air, filtering out water vapor and impurities, and then removing gas pollutants through an activated carbon scrubber. Finally, after processing through the semipermeable membrane, nitrogen with a purity ranging from 95% to 99.5% is collected.
Membrane nitrogen generation utilizes the different permeation rates of gases to separate nitrogen. Since nitrogen permeates quickly while gases like oxygen have slower rates, the nitrogen can be collected early for industrial use. Membrane systems are cost-effective and occupy minimal space.
· PSA Nitrogen Generator
Pressure swing adsorption nitrogen generation utilizes the distinctive adsorption properties of gases to produce nitrogen, primarily through two processes: adsorption and desorption. The carbon molecular sieve acts as the adsorbent, responsible for adsorbing gases other than nitrogen, predominantly oxygen. The process involves pressurized adsorption and depressurized desorption. When the carbon molecular sieve is operational, pressure increases, causing oxygen to be adsorbed by the sieve. Once the carbon molecular sieve reaches its adsorption capacity, pressure decreases, releasing oxygen to be expelled from the system while nitrogen is collected and stored. The nitrogen purity achievable with pressure swing adsorption nitrogen generators ranges from 95% to 99.999%, offering high purity levels. Furthermore, in comparison to cryogenic distillation nitrogen generation, pressure swing adsorption nitrogen generation boasts lower costs.
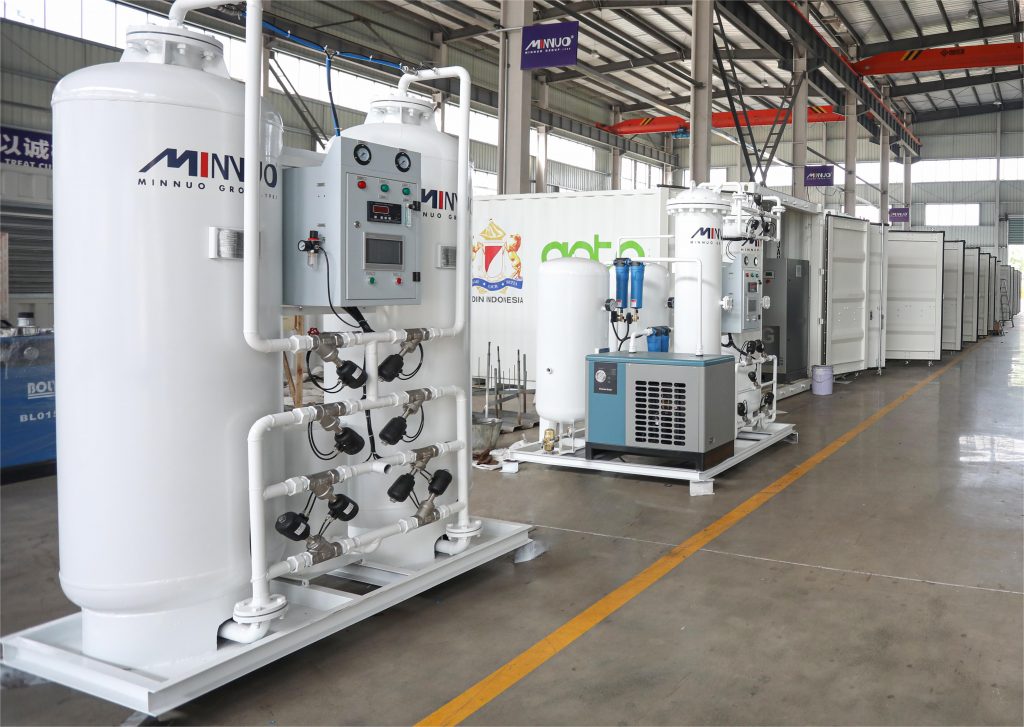
Nitrogen Generator VS. Nitrogen Gas Cylinder
Nitrogen generators provide a stable nitrogen supply, enabling continuous 24-hour operation to ensure consistent production. Compared to nitrogen cylinders, nitrogen generators require regular maintenance to guarantee uninterrupted supply. While nitrogen cylinders offer flexibility with easy mobility and lower upfront costs, their long-term expenses can be higher. Additionally, transport issues can arise with nitrogen cylinders. Despite the higher initial investment, nitrogen generators have lower operating costs in the long run.
Nitrogen applications
- Food Industry: Used for food preservation to prevent oxidation.
- Medical Industry: Utilized for surgical anesthesia, treatment, and sample preservation.
- Electronics Industry: Employed for cleaning, drying, and as a protective agent.
- Chemical Industry: Used for corrosion prevention and explosion prevention.
- Manufacturing Industry: Utilized for product protection.
Future Trends
Current nitrogen separation technology still has shortcomings, including high energy consumption, high costs, and low efficiency. Traditional nitrogen separation techniques require a significant amount of energy for nitrogen purification, involve complex equipment, and come with high costs. Furthermore, the restricted technological capabilities limit their applicability in various fields. With the advancement of technology and innovation, future nitrogen production techniques will undoubtedly become more intelligent and digitized. Many current technological bottlenecks and limitations will have good solutions to address their application domains. In the future, nitrogen separation technology will become more sustainable and environmentally friendly.
Conclusion
This article primarily focuses on three methods of nitrogen production and their respective advantages and disadvantages. If you are interested in learning more about nitrogen production, you can engage in discussions and potential collaborations with our company. Thank you for reading!