Air dryers are essential components in any compressed air system, preventing water vapor from damaging equipment and reducing operational efficiency. Whether you’re dealing with an industrial setup, an automotive air compressor, or even a home air dryer, understanding how these systems work can significantly enhance your equipment’s longevity and performance.
What is the function of an air dryer?
An air dryer removes moisture from compressed air systems to prevent corrosion, equipment damage, and reduced efficiency. Without dry air, condensed water can cause rust, freezing in pipelines, and contamination of end products.
Want to know how air dryers whisk away water in seconds? Join us as we explore the fascinating mechanics that keep dry!
What is an Air Dryer
An air dryer is a device used to remove water vapor from compressed air. Moisture in the air can condense inside a compressed air system, causing issues like corrosion, equipment failure, and decreased efficiency. Air dryers ensure the air used in pneumatic tools, machines, or systems remains dry and free of water particles.
How Does an Air Dryer Work?
The working principle of air dryers varies by type, but they all operate on the core concept of removing moisture from the air before it reaches equipment or storage. Below is an overview of the main air dryer types and their processes:
- Refrigerated dryers cool the air to condense moisture, then remove it.
- Desiccant dryers use adsorbents like silica gel to absorb moisture from the air.
- Membrane dryers use special fibers to allow moisture to escape through a selective barrier.
Each of these systems plays a vital role in industries where dry air is necessary, including automotive, manufacturing, and food processing.
Why Do Compressed Air Systems Need Dry Air?
Compressed air systems are widely used in industries, but they also generate a considerable amount of water due to the process of compressing air. Moisture in these systems is detrimental and can lead to:
- Corrosion and Rust: Water can corrode metal parts, valves, and pipelines, leading to expensive repairs or replacements.
- Freezing in Cold Conditions: Moisture in the air can freeze, blocking or bursting pipelines.
- Reduced Efficiency: Moisture affects the efficiency of pneumatic tools and machinery.
- Product Contamination: In food, pharmaceutical, and medical industries, even the slightest moisture can lead to contamination, spoiling entire production batches.
Studies show that up to 90% of the problems in compressed air systems are moisture-related. A well-maintained air dryer can reduce maintenance costs by as much as 40%, with an increase in overall system efficiency by 25%.
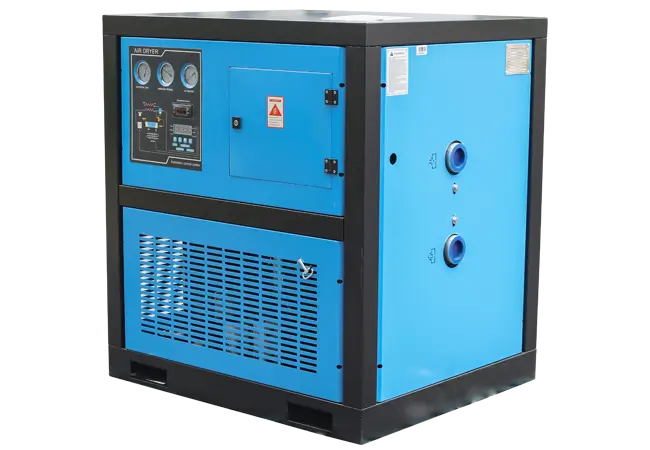
Types of Air Dryers
There are several types of air dryers, each designed for specific needs and environments. Here’s an overview of the most common systems:
Refrigerated Air Dryers
Refrigerated air dryers cool the air to around 3°C (37.4°F), causing the moisture to condense. The condensed water is then removed from the system. This type is widely used due to its efficiency and cost-effectiveness in industrial air compressor dryer setups.
- Advantages: Cost-effective, low maintenance, and energy-efficient.
- Disadvantages: Not suitable for environments requiring ultra-low dew points.
Desiccant (Adsorption) Air Dryers
These dryers use a desiccant material (e.g., silica gel or activated alumina) to absorb moisture from the air. They can achieve very low dew points, making them ideal for applications requiring extremely dry air, such as in pharmaceutical or electronic manufacturing.
- Advantages: Achieves very low dew points (-40°F to -100°F).
- Disadvantages: Higher maintenance and operational costs.
Membrane Air Dryers
Membrane air dryers use a selective barrier that allows water vapor to pass through while retaining the dry air. They are ideal for low-flow applications and are often used in instrument air dryer systems or smaller-scale industrial operations.
- Advantages: Compact, energy-efficient, and low-maintenance.
- Disadvantages: Slower process and less effective for large-scale operations.
How Air Dryers Work: Step-by-Step Process
Let’s take a closer look at the air drying process. Whether you’re working with a truck air dryer system or an industrial dryer, the basic stages remain the same:
- Inlet Stage: Compressed air enters the dryer system after passing through a compressor. In this stage, the air is saturated with moisture.
- Moisture Removal Stage: Depending on the type of dryer, moisture is removed either through refrigeration, absorption by a desiccant, or filtration in membrane dryers.
- Exit Stage: Once the moisture is removed, the dry air flows out of the system, ready for use in pneumatic tools, manufacturing processes, or storage tanks.
- Energy Efficiency: Modern air dryer systems, especially those with intelligent control units, monitor energy use and adjust to maintain optimal performance without wasting energy.
Choosing the Right Air Dryer
When selecting an air dryer system, it’s crucial to match the dryer to your system’s needs. Key factors to consider include:
- Flow Rate: Ensure the dryer can handle the flow of compressed air your system produces.
- Pressure: Check that the dryer can work at the pressures required by your equipment.
- Dew Point: The dew point your system needs will depend on the application (e.g., refrigerated dryers can handle a dew point of around 3°C, while desiccant dryers can go much lower).
- Maintenance Requirements: Factor in ongoing maintenance and operational costs. Minnuo’s self-developed air dryer can realize efficient water removal and has high price advantage, which is worth recommending!
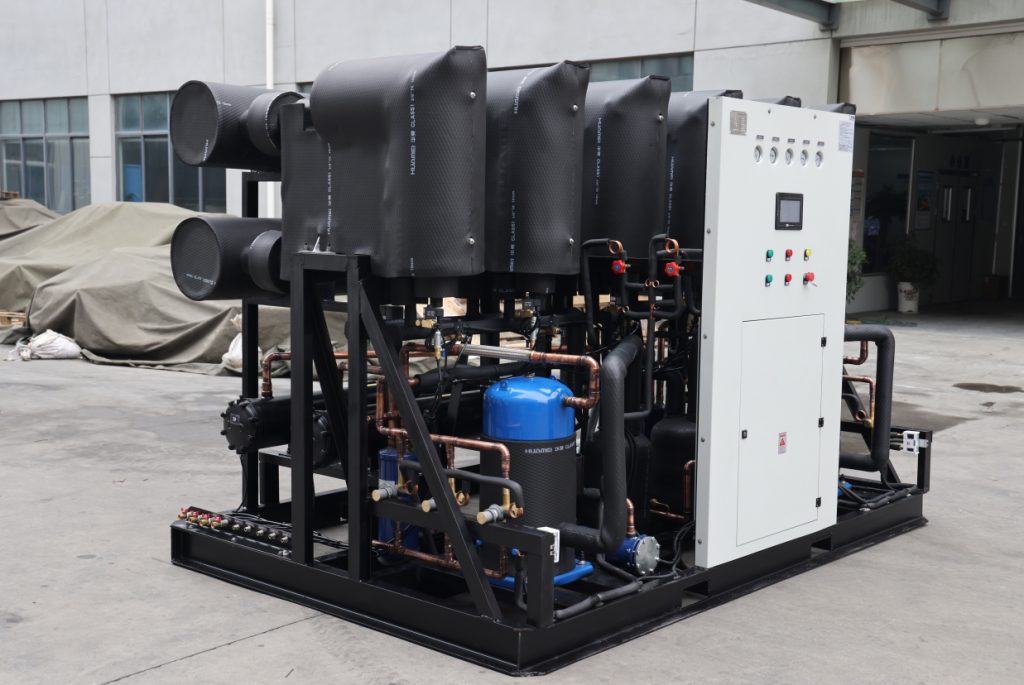
Common Issues with Air Dryers and How to Fix Them
While air dryers are essential, they can occasionally experience issues. Here are some common problems and solutions:
- Excess Moisture in the Air: This could be due to a malfunctioning desiccant in a desiccant dryer or inadequate cooling in a refrigerated dryer. Regular maintenance can prevent this issue.
- Increased Pressure Drop: If you notice a drop in pressure, your dryer may be clogged. Clean or replace filters regularly to maintain optimal airflow.
- Freezing in Cold Weather: Use heat tracing or insulated piping to prevent freezing in air lines during winter months.
Air Dryer Innovations and Future Trends
The future of air dryers looks promising, with advancements in:
- Energy Efficiency: More efficient models are reducing energy consumption by as much as 50%, a critical feature for industries focused on sustainability.
- Smart Technology: Intelligent air dryers monitor system conditions in real-time, adjusting for performance and providing predictive maintenance alerts.
Conclusion
Understanding how air dryers work and why they are crucial for compressed air systems can significantly improve the longevity of your equipment, reduce costs, and increase efficiency. Whether you’re running an industrial air compressor and dryer system or using a home air dryer, choosing the right system for your needs is vital for optimal performance.
FAQs
Consider factors like your system’s flow rate, pressure, and the required dew point. Refrigerated dryers are ideal for general applications, while desiccant dryers are better for extremely dry air requirements.
Yes, smaller air dryers like inline air dryers are available for home air compressor systems. These are ideal for DIY projects, painting, or powering pneumatic tools.
Maintenance frequency depends on the type of dryer. Refrigerated dryers require filter cleaning and cooling checks every 3-6 months, while desiccant dryers need desiccant replacement every 2-5 years.