Hello, boss. If you’re looking to buy an air separation device for your industry, this paper explains the manufacturing technology, equipment configuration, selection criteria, and maintenance of industrial oxygen and nitrogen machines. It also covers usage and market trends, offering detailed technical analysis. This is ideal for technical reports or industry research, providing strong theoretical and data support for purchasing oxygen and nitrogen machines.
The use of industrial oxygen and nitrogen production
The use of the industrial oxygen production
Oxygen’s strong flammability makes it essential for high-temperature industries like steelmaking, smelting, and glass melting. It boosts production efficiency, especially in metallurgical and chemical sectors, by speeding up reactions. For safety and environmental protection, using oxygen in sewage treatment, waste incineration, and optimizing combustion in thermal power plants reduces pollution and fire risk effectively. Hospitals will also need to use oxygen therapy and hyperbaric oxygen chambers.
The use of industrial nitrogen production
Nitrogen’s low reactivity makes it essential in metal heat treatment, electronics manufacturing, and food preservation, preventing oxidation and contamination. Its inert properties help prolong food shelf life and reduce oxidative deterioration. In the oil and gas industry, nitrogen is essential for pipeline purging, explosion prevention, and gas field pressurization to ensure safety. Liquid nitrogen, widely used in scientific research, preserves biological samples, freezes laboratory materials, and supports specialized processing tasks. Both oxygen and nitrogen are crucial to modern industry, driving production efficiency, safety, environmental protection, and technological advancement.
A brief history and development trend of air separation technology
A brief history of technology
At the end of the 19th century, German chemist Linde (Carl von Linde) invented the first air liquefaction unit, which laid the foundation for the deep cold air separation technology. However, it was not until the early 20th century that cryogenic separation technology became widely used for industrial oxygen production in steel mills and chemical plants. In the 1970s, pressure change adsorption (PSA) and membrane separation technology appeared for small-scale gas production and efficient gas purification. After entering the 21st century, automation and intelligent technology have been applied to air separation equipment to realize remote monitoring and efficient operation.
Trend of development
Air separation technology is expected to integrate with IoT, improving equipment efficiency and fault detection. The focus will be on green manufacturing, energy savings, reducing consumption, boosting oxygen and nitrogen production, and cutting carbon emissions to meet environmental standards. As demand for liquid oxygen and nitrogen grows, liquefaction equipment will rise in popularity.
With accelerating industrialization in emerging markets like Asia and Africa, regional demand for oxygen and nitrogen will expand. Air separation advances not only enhance gas production efficiency but also drive industrial progress, paving the way for future innovations in intelligence, energy conservation, and environmental protection.
Principles of air separation technology
Cryogenic Air Separation
Cryogenic Air Separation is to obtain high purity oxygen, nitrogen (oxygen> 99.5%, nitrogen> 99.999%) by liquefaction of air and distillation of other rare gases (such as argon), and is suitable for large-scale gas production. But its investment and operation costs are high, the equipment is huge, suitable for the fixed plant station.
- Air compression: compress the air to a certain pressure.
- Pre-cooling: use cold water or a freezer to cool the air to near zero to remove water and carbon dioxide.
- Air liquefaction: the air enters the heat exchanger to cool below-170℃, part of the air is liquefied.
- Distillation: Using different boiling points of oxygen (-183℃) and nitrogen (-196℃) to separate them step by step.
- Purification and collection: to obtain a high purity of industrial oxygen, nitrogen, and argon.
Pressure Swing Adsorption, PSA
Pressure Swing Adsorption, PSA uses the selective adsorption of adsorbent (such as molecular sieve) at different pressures to separate oxygen or nitrogen. And low energy consumption, simple equipment structure, rapid start and stop, suitable for small and medium-scale gas production. However, the gas purity is limited (oxygen about 93% ± 3%, nitrogen maximum 99.99%), and the adsorbent also needs to be replaced and maintained regularly.
- Air compression: to compress the air to a certain pressure.
- Adsorption separation: compressed air into the adsorption tower, the adsorbent selectively adsorbed nitrogen (oxygen) or oxygen (nitrogen) in the air.
- Desorption regeneration: when the adsorbent is near saturation, reduce the pressure in the tower and release the adsorbed gas to regenerate the adsorbent.
- Rotation operation: the twin towers run alternately to achieve continuous gas production.
Membrane Separation
Membrane Separation uses special polymer film to different speed of gas to achieve gas separation. The components such as oxygen and nitrogen have different penetration rates when crossing the membrane material to achieve the separation. The equipment is compact, easy to move, suitable for field applications, easy to operate, and easy to start and stop. However, the gas purity is low, usually oxygen in 30% -40%, nitrogen can be up to 95%, the membrane maintenance and life span have high requirements.
- Air compression: compress the air into the membrane assembly.
- Membrane filtration: oxygen passes through the membrane more quickly, while nitrogen passes through it more slowly.
- Separation product: High concentrations of oxygen or nitrogen are isolated according to the rate of gas flow through the membrane.
Comparison of the various techniques
technology | pureness | production capacity | capitalized cos | energy consumption | applicable scene |
Cryogenic Air Separation | O₂ >99.5% N₂ > 99.999% | large-scale | high | high | iron and steel, chemical industry, large gas plant and station |
Pressure Swing Adsorption, PSA | O₂ 93±3% N₂ >99.99% | Small and medium-sized | middle | middle | medical use, electronic use, and food preservation |
Pressure Swing Adsorption, PSA | O₂ 30%-40% N₂ about95% | small-scale | low | low | food packaging, pipe purging |
Each technology, according to different scenarios and needs, plays its own advantages in production. In the future, with the promotion of the concept of intelligent and green environmental protection, various separation technologies will continue to improve and complement each other.
Industrial oxygen production and equipment configuration
PSA oxygen generator process
A PSA (Pressure Swing Adsorption) oxygen generator uses clean compressed air as the raw material, with high-quality zeolite molecular sieves as the adsorbent. Oxygen is produced from air under a certain pressure. The compressed air is purified, dried, and introduced into the adsorbent. Through pressurization and desorption, nitrogen is adsorbed more quickly by the zeolite due to its faster diffusion rate compared to oxygen. As nitrogen is absorbed, oxygen is enriched in the gas phase, forming the final oxygen product.
To regenerate the adsorbent, the pressure is reduced to atmospheric levels, allowing the nitrogen and other impurities to be desorbed. The system typically includes two adsorption towers: one for oxygen production and the other for desorption and regeneration. A PLC program controls the pneumatic valves, allowing the towers to alternate, ensuring continuous production of high-purity oxygen (93% ± 3%).
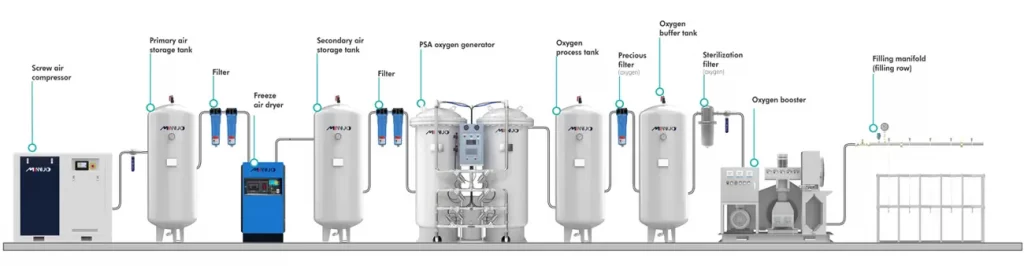
Process flow chart of the PAS nitrogen generator
Operation of the PSA oxygen production equipment
- Start-up preparation: check the status of the equipment to ensure the normal operation of the air compressor and cold dryer. Ensure that the filter and adsorption tower are in good condition, with no abnormal sound and vibration.
- Start the equipment: start the air compressor, set the pressure and flow rate. Start the cold dryer and filter to ensure that the air is dry and clean.
- Monitoring operating parameters: oxygen purity, flow, pressure and temperature, ensure within the set range. Check the pressure change of the adsorption tower regularly to determine the saturation state of the adsorbent.
operating process: | |
Boot preparation | Check the status of the equipment to ensure that the air compressor and cold dryer operate normally.Ensure that the filter and adsorption tower are in good condition, with no abnormal sound and vibration. |
starting device;trigger | Start the air compressor and set the pressure and flow rate.Start the cold dryer and filter to ensure that the air is dry and clean. |
Monitor operating parameters | Monitor oxygen purity, flow, pressure and temperature to ensure within the set range. Check the pressure change of the adsorption tower regularly to determine the saturation state of the adsorbent. |
machine halt | Close the oxygen output valve and gradually reduce the pressure when stopping.Check the operation of the equipment regularly and record the data for analysis. |
Industrial nitrogen production system and equipment configuration
PSA nitrogen generator process
- There are two adsorption towers equipped with A carbon molecular sieve. When one tower (A) works, the other tower (B) desorbes under reduced pressure.
- When clean air enters the adsorption tower (A), the molecular sieve adsorbs the oxygen, carbon dioxide, and water, allowing nitrogen along with trace amounts of argon and oxygen to flow to the outlet.
- The other tower, known as the stripping tower (B), removes the absorbed oxygen, carbon dioxide, and water from the pores of the molecular sieve. It then releases them into the atmosphere.
- In this way, the two towers take turns to complete the nitrogen and oxygen separation, and continuously output the nitrogen gas.
- 95% -99.9% of the output of nitrogen nitrogen into the nitrogen purification equipment.
- Then through the dryer deep drying (two adsorption drying tower alternately: one adsorption drying and dehydration, the other heating desorption drainage), then the purity of nitrogen can reach 99.9997%.
- The final product is high pure nitrogen produced on site, which costs far below the price of a liquid or bottled gas.
Video display of PSA nitrogen manufacturing machine process flow
Selection and design of industrial oxygen and nitrogen generator
When selecting oxygen production equipment, gas production capacity should match actual demand to meet peak requirements. Different industries have varying oxygen purity needs, so it’s essential to choose the right technology, such as PSA or cryogenic separation. The equipment layout should also be designed based on plant size and production capacity to ensure easy operation and maintenance. Opting for energy-efficient compressors and dryers helps reduce energy consumption and comply with environmental standards.
Moreover, equipment design should prioritize ease of maintenance and operation, minimizing downtime and maintenance costs. Safety is a key priority. The equipment must comply with all safety standards. This includes precautions for high-voltage components. Monitoring systems should also be in place.
In summary, the design and selection of oxygen production equipment should consider several factors. These include gas production capacity and purity. Equipment scale and layout are also important. Energy efficiency and environmental impact should be taken into account. Ease of maintenance and safety are key considerations as well. This ensures the equipment operates efficiently, safely, and meets the actual production needs.
Maintenance and maintenance of industrial oxygen and nitrogen generator
Daily maintenance and maintenance of the oxygen generator
To ensure the proper operation of the oxygen generator and extend its service life, regular maintenance is essential. It mainly includes the following aspects:
- Equipment appearance: Inspect the equipment shell, pipes and valves regularly to ensure no leakage, corrosion or other damage. Connections: Check all connections and pipes to prevent gas leakage.
- Air filter: Replace the air filter regularly according to the running time to ensure good air quality and prevent impurities from entering the equipment.
- Oxygen filter: Oxygen filters should be checked and replaced regularly to ensure the purity and safety of oxygen.
- Filter replacement: The performance of the molecular sieve is monitored regularly and replaced if necessary to ensure oxygen yield and purity.
- Lubrication and cleaning: Lubricate the compressor and moving parts regularly to avoid wear.
- Cleaning: Clean the heat sink of the cold dryer, cooler and other equipment to ensure a good heat dissipation effect.
- Data logging: Record the parameters of the equipment operation (such as flow, pressure, temperature, etc.), analyze the data regularly, and handle the abnormal situation in time.
Common problems and solutions of the nitrogen generator
In the process of using the nitrogen generator, there may be some common problems, and their corresponding solutions:
- Nitnitrogen purity: molecular sieve saturation, filter blockage or improper operation. Solution: Check and replace the molecular sieve and filter to ensure that the operation is according to specification.
- Equipment vibration or excessive noise: wear or loosening of mechanical parts. Solution: Check the installation and connection of the equipment, and tighten or replace the worn parts if necessary.
- Frequent equipment shutdown: insufficient air source pressure or system failure. Solution: Check the gas source pressure, confirm that the gas supply system is normal, and conduct maintenance if necessary.
- Insufficient nitrogen flow rate: adsorption tower blockage or equipment failure. Solution: Check the adsorption tower status, clean or replace if necessary.
Equipment shutdown and troubleshooting process
Equipment shutdown and troubleshooting are important links to ensure the normal operation of the equipment. The specific process is as follows:
- Downtime preparation: Close the oxygen or nitrogen output valve to reduce the pressure. Record the equipment operation parameters before shutdown and save the data for subsequent analysis.
- Confirmation of fault: collect operator feedback and confirm fault type and performance.
- Check the power supply and control system: Ensure the power supply is normal and check the control system for alarm information.
- Equipment appearance inspection: Check for obvious damage or leakage outside the equipment.
- Confirmation of fault: collect operator feedback and confirm fault type and performance.
- Check the power supply and control system: Ensure the power supply is normal and check the control system for alarm information.
- Equipment appearance inspection: check for obvious damage or leakage outside the equipment.
- Step by step Sub-system inspection: Check one by one according to the equipment structure, such as compressor, filter, adsorption tower and other components.
- Data monitoring: check the operating data and analyze the fault causes.
- Repair and reset Repair or replace any fault fault. After completion, do the system reset and prepare to restart the equipment.
- Restart the device: After confirming that all problems are resolved, gradually start the equipment and monitor the operating parameters to ensure that everything is normal.
The maintenance of industrial oxygen and nitrogen generators is crucial for ensuring efficient and stable operation. Regular maintenance, timely troubleshooting, and effective management can greatly extend equipment life, lower the failure rate, and increase production efficiency.
Application of technological innovation in the production of oxygen and nitrogen generator in MINNUO industry
Technological innovation is the core power to promote the progress of industrial gas production. The application of new technologies has played an important role in improving production efficiency, reducing energy consumption and improving gas purity.
- MINNUO advanced separation technology: such as membrane separation, deep cold separation and improved pressure change adsorption (PSA) technology, improve the efficiency and economy of gas separation.
- MINNUO energy saving and environmental protection technology: develop efficient and energy-saving compressor, cold dryer and filtration equipment to reduce the energy consumption and carbon emissions of industrial gas production.
- MINNUO intelligent equipment: introduce the Internet of Things, big data and artificial intelligence technology to realize the intelligent monitoring and prediction maintenance of equipment, and improve the operation reliability of equipment.
Conclusion
If you need oxygen and nitrogen production machines, trust MINNUO’s technology, equipment configuration, selection tips, and maintenance. We continuously optimize our products, adapting to green manufacturing trends and sustainable development, to offer you the most reliable solutions.