Nitrogen generators (also known as nitrogen gas generators) are widely used across industries such as manufacturing, chemicals, and electronics for the separation and supply of nitrogen. Proper commissioning of these systems is crucial, as it determines the equipment’s long-term stability and efficiency. Adequate pre-use commissioning ensures smooth operation. This article provides a detailed guide on nitrogen generator pre-use commissioning methods, helping users optimize performance and maximize operational efficiency.
Nitrogen generator pre-use commissioning methods include key steps such as equipment installation, pipeline connection, control system settings, and both no-load and load tests. By correctly selecting installation locations, fine-tuning control system parameters, and conducting comprehensive tests, it is possible to ensure the equipment achieves the desired nitrogen purity and flow rate while running efficiently and stably. Additionally, the article highlights diagnostic troubleshooting and solutions during the commissioning process, along with detailed guidance for creating commissioning reports, ensuring long-term, stable, and efficient performance.
Preparation and Inspection Before Installing the Nitrogen Generator
The installation of the nitrogen generator is the first step in the commissioning process. Proper installation not only ensures the equipment’s stability but also provides a solid foundation for subsequent commissioning.
Selecting the Right Installation Location
Choosing an appropriate location for the nitrogen generator is critical. The right location not only supports efficient operation but also prolongs the lifespan of the equipment. Key considerations include:
- Good Ventilation: The nitrogen generator requires adequate heat dissipation and airflow, so choose a location with proper ventilation.
- Suitable Temperature: The equipment typically operates best within a temperature range of 5°C to 40°C. Extremes of temperature can negatively affect performance.
- Avoiding Vibration: Install the generator away from large machinery or vibration sources to prevent external vibrations from destabilizing the system.
- Avoid Corrosive Gases: The generator should not be installed in environments with corrosive gases, which could damage the machine and pipeline systems.
Power and Pipeline Connections
During installation, ensure the power, air supply, and pipeline connections are stable and reliable:
- Power Supply: Verify that the voltage matches the generator’s specifications and ensure proper grounding to prevent electrical faults.
- Air Supply Pipeline: Connect the compressed air source, ensuring the air supply is sufficient and the connections are tight to prevent leaks.
- Exhaust Pipeline and Nitrogen Outlet: Install appropriate exhaust pipes to ensure smooth venting. The nitrogen output pipeline must be securely connected to the gas-use system to prevent leaks.
Level Installation
Use a spirit level to check the equipment’s alignment. Any tilt could affect the nitrogen flow and cause instability. Ensure the equipment is perfectly level.
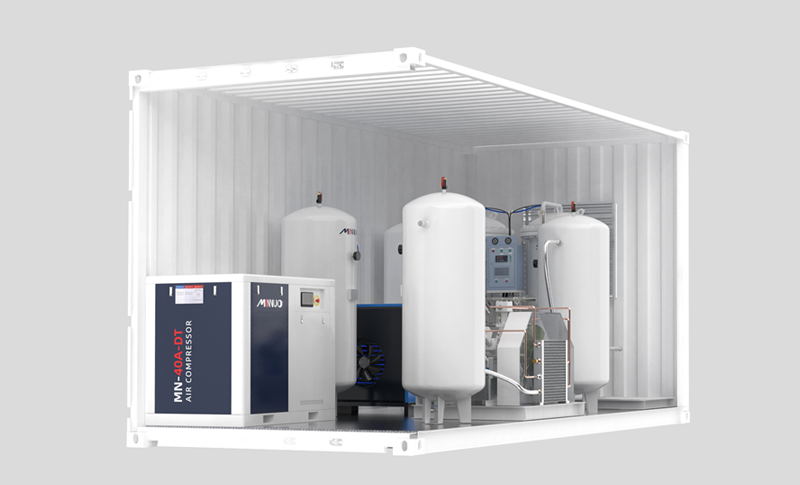
Commissioning the Control System
Most nitrogen generators come equipped with an automatic control system that monitors and adjusts operating parameters. Commissioning the control system ensures the equipment is always running in optimal condition.
Initial Control System Settings
During commissioning, set the operating parameters according to actual needs, including nitrogen purity, inlet pressure, and gas flow rate. The process includes:
- Setting Nitrogen Purity: Set the target nitrogen purity based on industry requirements. For industrial applications, 95%-99% purity is common, while medical applications often require higher purity.
- Inlet Pressure Settings: Ensure the incoming air pressure meets equipment specifications. Too high or too low of a pressure can impact efficiency.
- Flow Rate Adjustment: Adjust the gas output to meet the required flow, ensuring sufficient nitrogen supply.
Control System Calibration
Calibration ensures the control system measures accurately. Common calibration operations include:
- Nitrogen Purity Calibration: Use a standard gas analyzer to calibrate the nitrogen purity, ensuring the output meets the preset purity level.
- Pressure Sensor Calibration: Use a standard pressure gauge to calibrate the pressure sensors, ensuring accurate measurements.
- Flow Meter Calibration: Calibrate the flow meter to ensure it is within the correct flow range, as it plays a crucial role in controlling nitrogen output.
Control System Testing
After calibration, conduct a full system test to ensure the equipment operates correctly and responds to control signals. Key tests include:
- Automatic Mode Startup: Switch the system to automatic mode and check if the control system adjusts the working conditions as required.
- Fault Alarm Test: Simulate common faults, such as high or low pressure, and verify whether the control system alarms and takes appropriate safety actions.
- Data Monitoring Function: Ensure the system accurately records and displays real-time data, such as flow rate, pressure, and nitrogen purity.
No-Load and Load Testing
Once the control system is commissioned, perform both no-load and load testing to verify the generator’s stability under different operating conditions.
No-Load Operation Test
No-load testing is the first step in evaluating the equipment’s basic functionality, ensuring the generator starts up and runs smoothly without load. During the test, check the following:
- Startup Function: Ensure that the equipment powers on and all functions, such as the display panel and control system, operate correctly.
- Pressure and Temperature Monitoring: Monitor the pressure and temperature of the gas to ensure they are within normal operating ranges.
- Nitrogen Purity Check: Use a gas analyzer to verify that nitrogen purity meets the set value.
Load Operation Test
Load testing simulates real-world conditions and tests the generator’s stability under high demand. During the load test, focus on the following:
- Stability of Nitrogen Flow and Pressure: Ensure the generator consistently delivers stable nitrogen flow and maintains the required pressure under load conditions.
- Nitrogen Purity Verification: Check nitrogen purity under load to ensure the system can maintain high purity levels.
- Long-Term Stability: Perform extended load tests to ensure the generator operates without faults over extended periods.
Recording Commissioning Results and Reporting
The data obtained during the commissioning process, following the nitrogen generator pre-use commissioning methods, should be carefully recorded for future maintenance and performance optimization. The commissioning report is an essential reference document for the long-term operational management of the equipment.
Data Recording and Analysis
Record all critical parameters during operation, including nitrogen purity, flow rate, pressure, and temperature. These data help maintenance personnel identify potential issues and make necessary adjustments.
Writing the Commissioning Report
The commissioning report should include the following:
- Installation and Commissioning Steps: Document key operations during installation and commissioning to ensure they align with equipment requirements.
- Test Results: Include all data from no-load and load tests, with a focus on key parameters such as nitrogen purity, flow rate, and pressure.
- Issues and Solutions: Record any problems encountered during commissioning and the solutions implemented to resolve them, providing useful information for future maintenance.
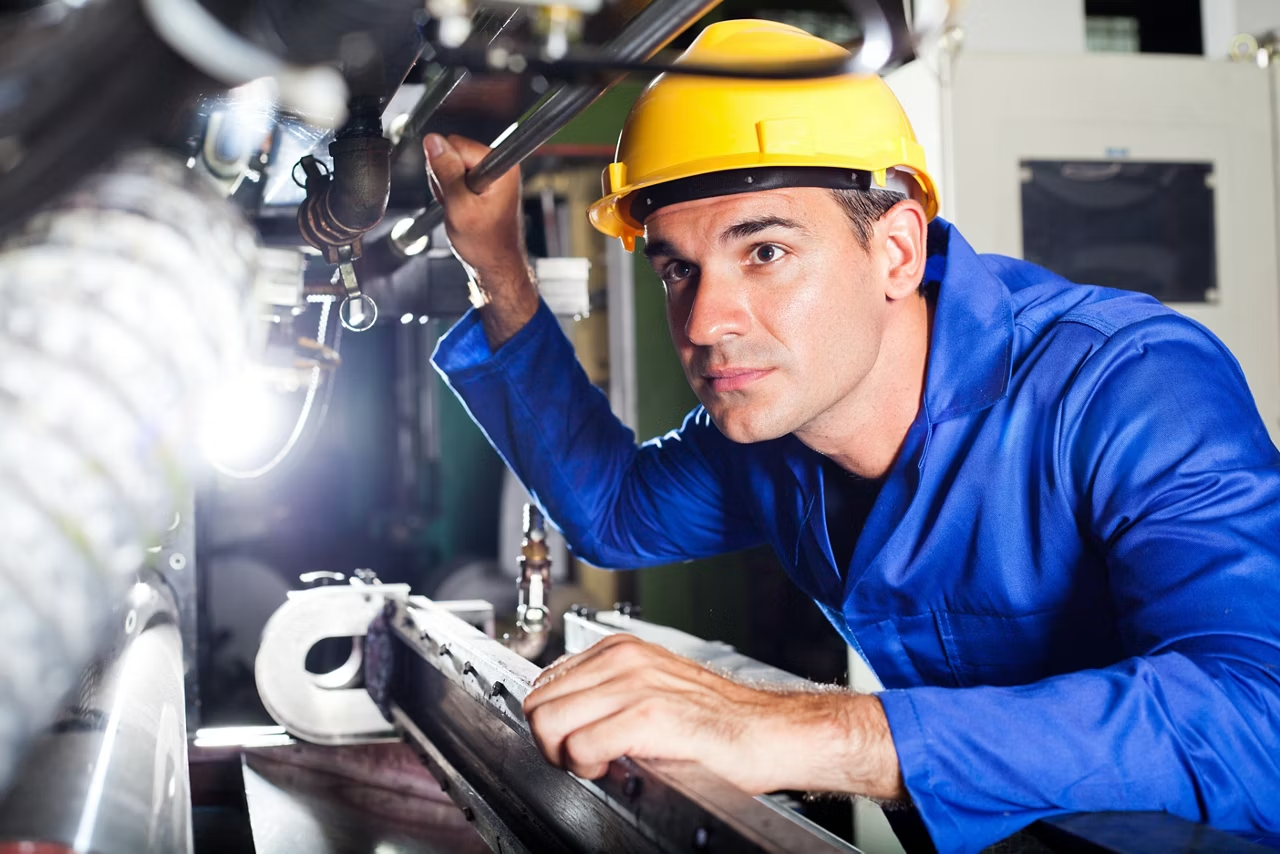
Common Problems and Solutions
During the commissioning process, common issues may arise. Understanding and resolving these problems is crucial for smooth operation.
Unstable Nitrogen Purity
- Cause: The control system parameters may not be correctly set, or the air quality may not meet the required standards.
- Solution: Re-adjust the nitrogen purity settings and check the air quality. Clean or replace filters as needed.
Low or High Gas Pressure
- Cause: Unstable air pressure in the input pipeline, or a malfunction in the internal pressure regulation system.
- Solution: Check the air supply pipeline to ensure it is within acceptable pressure ranges. Inspect the pressure sensors and regulators for functionality.
Frequent Fault Alarms
- Cause: Equipment may be overheating, overloaded, or have sensor malfunctions.
- Solution: Check electrical and mechanical components to ensure they are functioning correctly. If necessary, consult a technician for repairs.
Conclusion
Nitrogen generator pre-use commissioning methods are key to ensuring its efficient and stable operation. By following a detailed commissioning process, you can avoid equipment failure, optimize performance, and increase operational efficiency. By adhering to the steps and methods outlined in this article, you can successfully install and commission your nitrogen generator, preparing it for reliable service.
If you’re seeking professional nitrogen generators or need more technical support, visit MINNUO‘s official website for more information and expert guidance.