Nitrogen generators are widely used in industrial fields, and their stable operation is crucial to many production processes. The dust emission problem in nitrogen generators is a common and harmful issue that significantly impacts nitrogen quality, equipment lifespan, and production efficiency.
To address the dust emission problem in nitrogen generators, three aspects need to be considered: Regular monitoring and timely replacement of adsorbents, some of which can be regenerated, should be carried out; high-precision multi-stage filtration and dewatering should be used in the intake pre-treatment system, with regular maintenance of equipment; improvements should be made to the airflow distribution system, pressure stabilization devices should be installed, and compressor control to stabilize pressure should be optimized.
This article will analyze, from a professional and academic perspective, the hazards, causes, and comprehensive solutions to the dust emission phenomenon in nitrogen generators.
1. Hazards of the Dust Emission Problem in Nitrogen Generators
1.1 Impact on Product Quality
In the food industry, nitrogen is commonly used for modified atmosphere packaging to preserve food. If a nitrogen generator produces dust emissions, the dust will enter the packaging along with the nitrogen and directly contaminate the food. This not only lowers the sensory quality of the food but may also introduce microorganisms or harmful substances, endangering consumer health and seriously damaging the brand’s reputation.
In the electronics chip manufacturing process, the cleanliness of the environment is highly critical. The number of particles larger than 0.1μm per cubic meter of air must be controlled below the hundred or even ten levels. The dust particles introduced by the ash emission, even those as tiny as they may be, can cause short circuits, open circuits, or other performance defects in critical process steps like photolithography and etching.
For example, at a semiconductor manufacturing company, an issue with the nitrogen generator’s ash emission led to a sharp increase in the chip defect rate in the short term, resulting in significant economic losses.
1.2 Impact on Equipment Operation
Dust entering the downstream pipeline system of the nitrogen generator will gradually accumulate on the pipe walls, reducing the effective cross-sectional area of the pipeline and increasing gas flow resistance. According to fluid dynamics principles, this will cause an increase in system pressure drop, and in order to maintain normal gas flow, the compressor will need to consume more energy, thereby increasing energy consumption.
Additionally, uneven dust deposition can lead to localized corrosion in pipelines, reducing their lifespan. In severe cases, it may even cause pipeline rupture, resulting in gas leaks and posing safety risks. For equipment such as valves and filters, dust accelerates the wear of seals and filtering elements.
For instance, in some factories, the ash emission has caused significant wear on valve seals, leading to issues with valve sealing, while filters frequently fail due to dust clogging. The constant need for equipment repairs and replacements not only increases maintenance costs but also disrupts production, affecting production continuity.
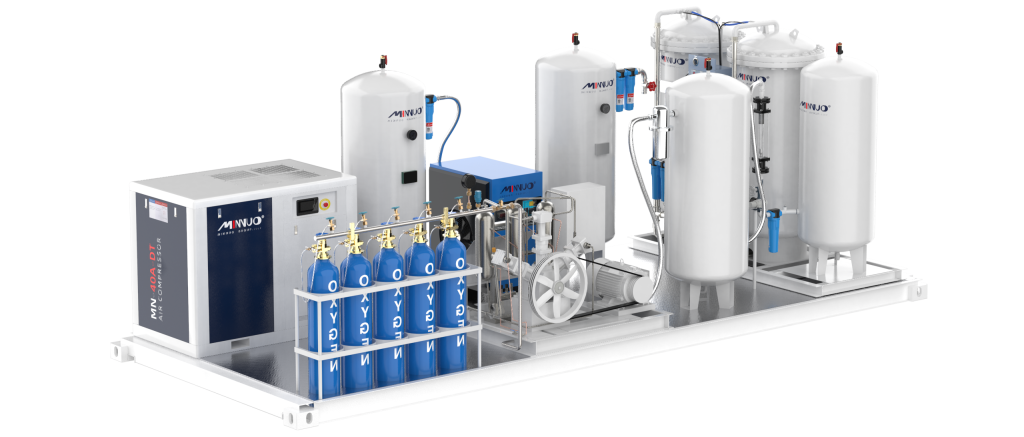
2. Causes of the Dust Emission Problem in Nitrogen Generators
2.1 Adsorbent-Related Factors
2.1.1 Adsorbent Pulverization
Common adsorbents used in nitrogen generators, such as molecular sieves, primarily separate nitrogen by adsorbing impurities like oxygen, carbon dioxide, and moisture from the air. During long-term pressure swing adsorption cycles, the adsorbent continuously experiences pressure changes during adsorption and desorption, as well as the impact of airflow. When the adsorbent’s strength is insufficient to withstand these mechanical forces, pulverization occurs.
On a microscopic level, the crystal structure of the adsorbent particles undergoes dislocations and slipping due to repeated stress, eventually leading to particle breakage. Additionally, if the adsorbent has quality defects, such as internal pores or impurities, its strength is reduced, accelerating the pulverization process.
2.1.2 Adsorbent Poisoning
If certain impurities in the raw air, such as sulfides or phosphides, react chemically with the adsorbent, they will occupy or alter the adsorbent’s active sites, causing the adsorbent to lose its adsorption capacity, i.e., poisoning. After poisoning, the chemical structure of the adsorbent changes, and its physical properties are also affected, making it more brittle and prone to breaking under airflow impact.
For example, active aluminum oxide groups in molecular sieves react with sulfides to form stable metal sulfides, which destroy the crystal structure of the molecular sieve and reduce its mechanical strength.
2.2 Intake Pre-treatment System Issues
2.2.1 Inadequate Filtration
The filters in the intake pre-treatment system are crucial for removing dust and impurities from the raw air. If the filter’s filtration precision is insufficient, it will not effectively trap fine particles in the air, allowing these particles to enter the nitrogen generator. These particles will collide and rub against the adsorbent, accelerating its wear. Additionally, if the filter material is of poor quality or has been in use for too long, leading to material degradation or blockages, the filtration efficiency will be severely compromised.
For example, standard paper filters, when exposed to moist environments, may deform and reduce filtration efficiency, and the paper filter material itself may break down under airflow impact, contributing to dust emission.
2.2.2 Incomplete Dewatering
Raw air usually contains a certain amount of moisture. If the dewatering equipment is ineffective or malfunctioning, moisture will enter the nitrogen generator along with the air. After the adsorbent adsorbs moisture, it expands, increasing the pressure between adsorbent particles. During pressure swing adsorption, the frequent pressure changes make the expanded adsorbent particles more prone to breaking. Additionally, moisture can condense inside the pipes and equipment, forming a slurry-like mixture when combined with dust, further exacerbating corrosion and wear, and increasing the risk of dust emission.
For instance, a malfunction in the refrigeration system of a refrigerated dryer, which is unable to lower the air temperature enough to remove moisture, or failure in the adsorbent of an adsorption dryer, can lead to incomplete dewatering.
2.3 Equipment Structure and Operational Parameters Issues
2.3.1 Uneven Airflow Distribution
The airflow distribution system inside the nitrogen generator plays a key role in evenly distributing the airflow within the adsorption tower. If the airflow distribution system is poorly designed, such as having uneven hole distribution or improperly angled airflow guides, it will cause airflow deviation in the adsorption tower. In areas with excessively high airflow speed, the adsorbent will experience strong scouring, which increases the friction and collision forces between the adsorbent particles, thus accelerating wear and pulverization.
According to fluid dynamics simulations, when the airflow speed uniformity exceeds a certain threshold, the wear rate of the adsorbent increases exponentially.
2.3.2 Excessive Pressure Fluctuations
During operation, the stability of system pressure is critical for the proper functioning of the adsorbent. Excessive pressure fluctuations can be caused by various factors, such as frequent starting and stopping of the compressor or instability in pipeline pressure. When pressure suddenly increases, the compressive force on the adsorbent particles increases abruptly, which may cause the particles to break. Conversely, when pressure decreases suddenly, the release of internal stress in the adsorbent particles can lead to rebound, causing violent collisions between particles, which also promotes particle breakage. Moreover, pressure fluctuations can disturb the balance between adsorption and desorption processes, reducing the nitrogen generation efficiency and purity of the nitrogen.
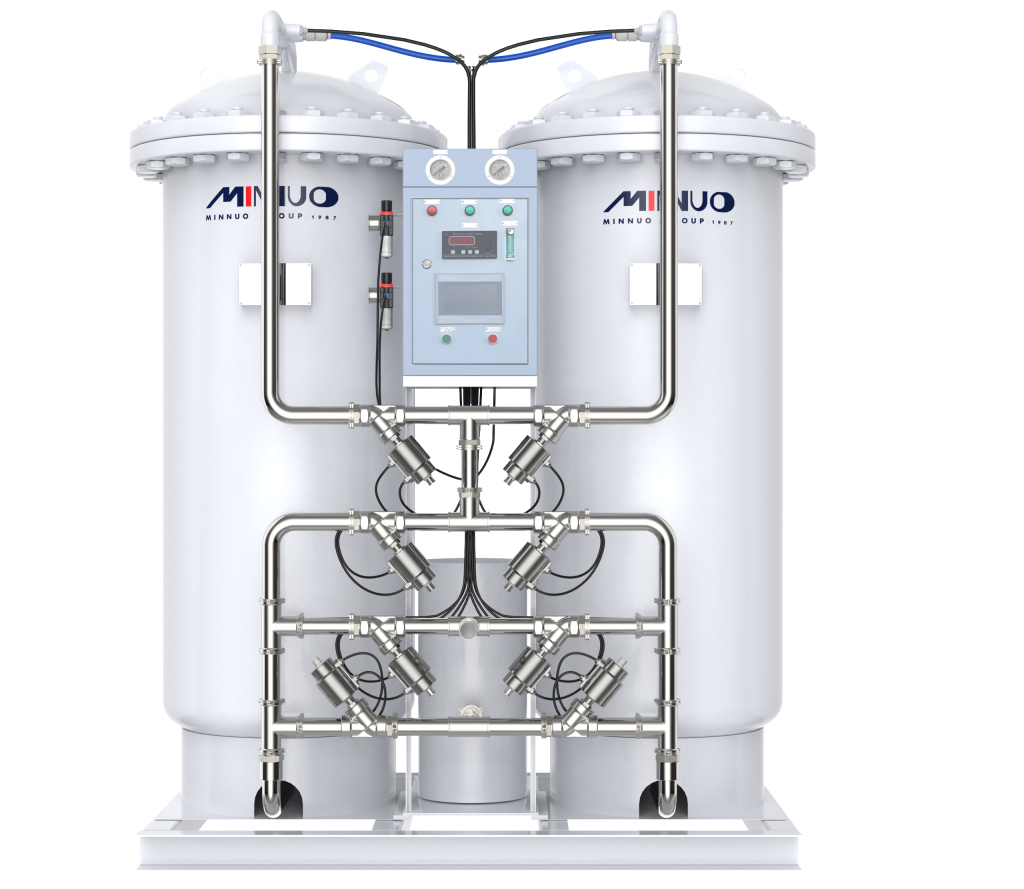
3. Solutions to the Dust Emission Problem in Nitrogen Generators
3.1 Adsorbent Maintenance and Management
3.1.1 Regular Inspection and Replacement
Establish a complete adsorbent inspection system and regularly test its performance. Methods such as X-ray diffraction (XRD), scanning electron microscopy (SEM), and other analytical techniques can be used to assess the adsorbent’s crystal structure, particle morphology, and surface characteristics, evaluating the degree of pulverization and changes in activity. Based on inspection results, usage time, and operating conditions of the nitrogen generator, a reasonable replacement cycle should be determined. When the attrition rate of the adsorbent exceeds a certain percentage (e.g., 20%) or its adsorption performance declines to the point where it can no longer meet production requirements, timely replacement is necessary to ensure the proper operation of the nitrogen generator.
3.1.2 Adsorbent Activation and Regeneration
For adsorbents that have deteriorated due to poisoning or mild pulverization, activation and regeneration techniques can be employed to extend their service life. For instance, activated carbon adsorbents that have been poisoned by organic impurities can be regenerated through thermal desorption. By heating the adsorbent to a specific temperature (e.g., 300℃ – 500℃) in an inert gas atmosphere, organic impurities are vaporized and desorbed, restoring the adsorbent’s activity. Molecular sieve adsorbents can be regenerated by reducing pressure and increasing temperature to remove impurities adsorbed on their surface and within their pores. However, it is important to strictly control the regeneration conditions to avoid further damage to the adsorbent.
3.2 Optimize Intake Pre-treatment System
3.2.1 Upgrade Filtration Equipment
Choose high-precision, high-performance filters, such as folding fiber filters, metal mesh filters, or electrostatic filters, to improve the filtration efficiency of dust and impurities in the raw air. These filters have larger filtration areas, higher dirt-holding capacities, and good mechanical strength, making them effective at trapping fine particles. Additionally, a multi-stage filtration approach can be adopted, setting up coarse filters, medium filters, and high-efficiency filters in sequence, depending on the particle size.
For example, a coarse filter can be installed at the intake to remove larger dust particles, followed by medium and high-efficiency filters to further purify the air and ensure that the dust content in the air entering the nitrogen generator meets requirements.
3.2.2 Improve Dewatering Process
Optimize the selection and operating parameters of dewatering equipment to ensure effective moisture removal. For raw air with high moisture content, a multi-stage dewatering process can be employed. First, a refrigeration dryer can lower the air temperature to condense most of the moisture into liquid water and separate it out. Then, an adsorption dryer can further remove the residual moisture, lowering the dew point to the required level. Regular maintenance of dewatering equipment should be carried out, including checking the refrigeration system’s operation, inspecting the performance of adsorbents, and replacing defective components to ensure stable operation of the dewatering system.
3.3 Equipment Structural Optimization and Operational Parameter Adjustment
3.3.1 Improve Airflow Distribution System
Using numerical simulations and experimental research methods, optimize the design of the airflow distribution system in the nitrogen generator. Based on the structure and size of the adsorption tower, parameters such as the hole distribution, hole size, and the angle of the airflow guides should be carefully considered to ensure that airflow is evenly distributed within the adsorption tower. During the actual retrofit process, new types of airflow distributors, such as multi-porous plates combined with guide tubes, can be used to improve the uniformity of airflow distribution and reduce scouring of the adsorbent.
3.3.2 Stabilize System Pressure
Install pressure stabilizing devices, such as storage tanks and pressure regulators, to stabilize the intake and system pressure of the nitrogen generator. The storage tank can buffer the effects of frequent compressor start/stop cycles and pipeline pressure fluctuations, ensuring a smoother airflow into the nitrogen generator. Pressure regulators can automatically adjust the valve opening based on system pressure changes to maintain the pressure within the desired range.
Additionally, optimizing the compressor’s operating control strategy by using variable-frequency drive technology can automatically adjust the compressor’s speed according to actual gas consumption, reducing the frequency of compressor starts and stops and thus minimizing pressure fluctuations. Regular inspection and maintenance of pipelines, including repairing leaks promptly, will also ensure pressure stability.
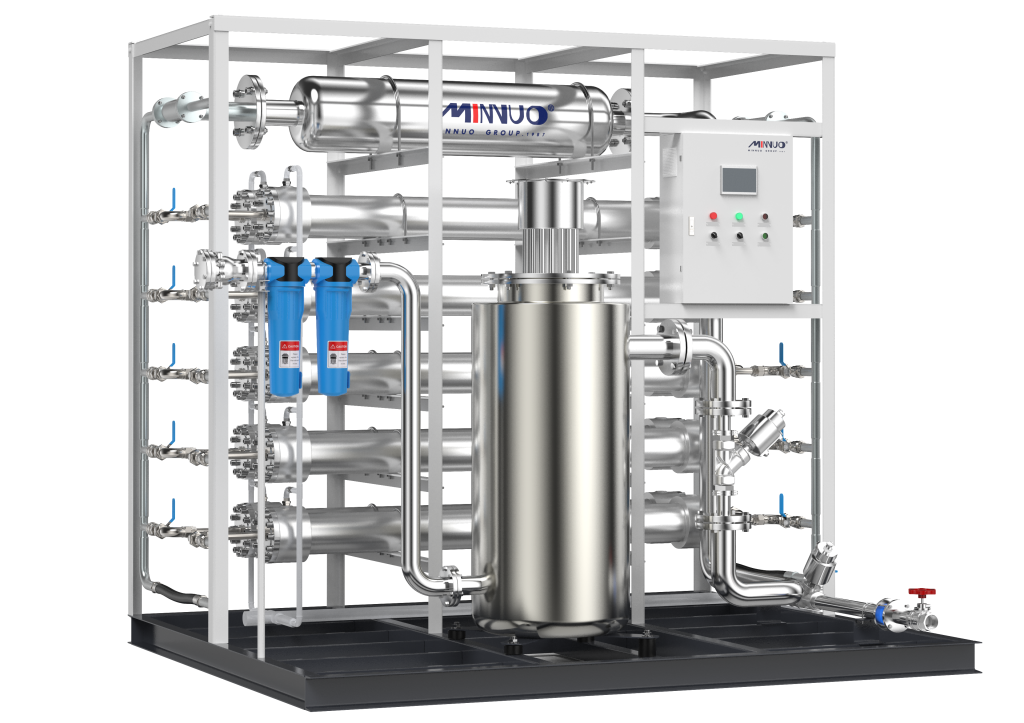
4. Conclusion
In practical applications, addressing the dust emission problem in nitrogen generators requires a comprehensive approach, tailored to the specific situation and production needs. Of course, with MINNUO products, there’s no need to worry about such issues. Our engineers have continuously innovated and optimized technology for over 30 years, ensuring that our nitrogen generators remain highly efficient and reliable.
If you want to learn more about MINNUO, feel free to consult us!