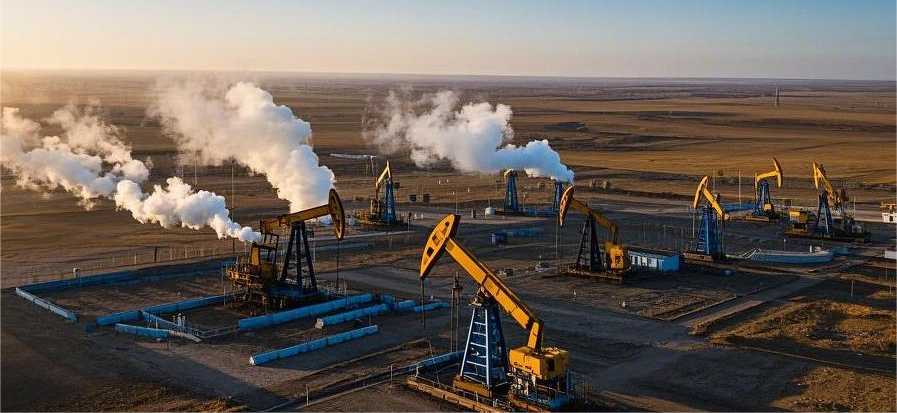
In the modern petroleum industry, oil field development faces challenges like improving crude oil recovery, ensuring safety, and reducing costs. Nitrogen generators in oil fields, as key equipment for on-site nitrogen production, play an essential role due to their efficiency and flexibility. With advancing technology, their performance and reliability have significantly improved, making their applications more widespread. This progress has been crucial in promoting the sustainable development of oil fields.
Nitrogen generators are primarily used in oil fields to provide on-site nitrogen, supporting production safety and enhancing oil and gas recovery. They are widely applied in different stages of oil field operations, such as improving crude oil recovery, preventing explosions and fires, isolating harmful gases, and reducing corrosion. Additionally, nitrogen generators are used in fracturing operations, gas protection, and equipment cleaning, thereby enhancing production efficiency and lowering operational costs.
1. Working Principles and Technical Features of Nitrogen Generators
1.1 Pressure Swing Adsorption (PSA) Nitrogen Generation Technology
PSA nitrogen generators separate nitrogen based on the differential adsorption capacities of adsorbents for different gas molecules. Commonly used adsorbents, such as carbon molecular sieves, have a strong affinity for impurity gases like oxygen and carbon dioxide but a weaker affinity for nitrogen. During the pressurization process, impurity gases in the air are adsorbed by the carbon molecular sieve, allowing nitrogen-rich gas to pass through. During depressurization, the adsorbed impurity gases are desorbed and expelled, regenerating the adsorbent and enabling continuous nitrogen production.
This process involves complex adsorption kinetics and thermodynamic principles. The adsorption process follows the Langmuir adsorption isotherm model, where the adsorption capacity has a specific functional relationship with gas partial pressure. By precisely controlling operational parameters such as adsorption time, pressure, and temperature, the nitrogen generation process can be optimized to improve nitrogen purity and production efficiency. Advanced PSA nitrogen generators typically employ automated control systems to monitor and adjust operational parameters in real-time, ensuring stable nitrogen purity between 99.9% and 99.999%, meeting the stringent requirements of oil fields for high-purity nitrogen.
1.2 Membrane Separation Nitrogen Generation Technology
Membrane separation nitrogen generators utilize special polymer membrane materials to separate gases based on differences in permeation rates. When air is driven through the membrane module under pressure, small molecules such as oxygen and water vapor, which have higher diffusion coefficients, permeate the membrane preferentially, while nitrogen is enriched on the other side of the membrane.
The membrane separation process follows the solution-diffusion mechanism, where gas molecules first dissolve on the membrane surface and then diffuse through the membrane under a concentration gradient. The performance of the membrane material, including its selectivity, permeability, and stability, plays a crucial role in nitrogen generation efficiency. In recent years, the development and application of new membrane materials, such as polyimide and fluoropolymers, have significantly enhanced the performance of membrane nitrogen generators. These generators offer advantages such as simple equipment structure, compact size, and fast start-up, making them suitable for applications with relatively lower purity requirements, typically between 95% and 99%.
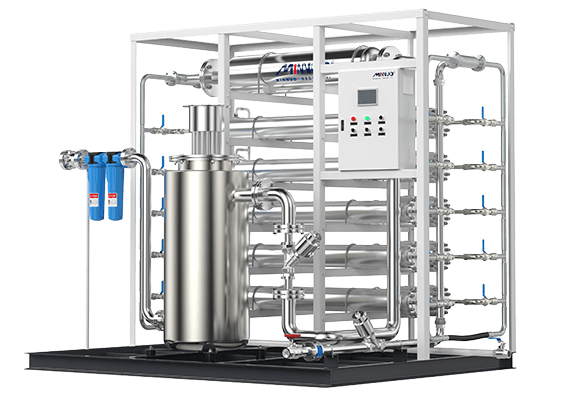
2. Applications of Nitrogen Generators in Oil Fields
2.1 Nitrogen Flooding and Enhanced Oil Recovery
During the middle and late stages of oil field development, reservoir pressure declines, and crude oil recovery faces bottlenecks. Nitrogen generated by nitrogen generators is used for nitrogen flooding, an effective tertiary recovery technique. By injecting nitrogen into the reservoir, the formation energy is replenished, and the immiscibility of nitrogen with crude oil creates a gas-driven oil flow, pushing residual oil toward production wells.
In low-permeability reservoirs, nitrogen flooding is particularly effective. According to the principle of seepage mechanics, the injection of nitrogen changes the seepage state of the fluid in the reservoir, reduces the viscosity of crude oil, thereby increasing the permeability of the oil phase and ultimately improving the fluidity of crude oil. Studies show that in specific low-permeability reservoirs, nitrogen flooding can enhance crude oil recovery by 10% to 20%, effectively extending the reservoir’s production life.
2.2 Gas Lift and Stable Oil Well Production
For deep wells or wells with low liquid production, gas lift is a crucial method for maintaining stable production. High-pressure nitrogen provided by nitrogen generators is injected into the annular space between the tubing and casing, reducing the liquid density in the wellbore and increasing the pressure difference between the liquid column and the formation, facilitating the flow of crude oil from the bottom of the well to the surface.
The gas lift process involves multiphase flow theory, and the selection of nitrogen injection volume, injection pressure, and gas lift method must be precisely optimized based on the well’s geological parameters and fluid properties. By establishing mathematical models of the gas lift system and combining them with numerical simulation techniques, the gas lift effect can be maximized. In practical applications, proper gas lift parameter settings can increase well production by 30% to 50%, ensuring stable well production.
2.3 Nitrogen Well Control and Workover Safety
During workover operations, balancing well pressure and preventing blowouts are critical for ensuring safety. Nitrogen produced by nitrogen generators serves as an inert well control medium, offering advantages such as non-contamination of the reservoir and easy post-operation removal. Based on pressure balance principles, precise calculation of nitrogen well control parameters, considering reservoir pressure, wellbore liquid column pressure, and pressure fluctuations during operations, allows for stable well pressure control by adjusting nitrogen injection volume and pressure.
Case studies show that using nitrogen for well control during workover operations effectively avoids reservoir contamination caused by traditional well control fluids, reduces reservoir damage, improves post-workover well productivity recovery, and ensures the safety of personnel and equipment.
2.4 Nitrogen Well Flushing and Well Productivity Restoration
Nitrogen plays a significant role in well flushing operations. High-pressure nitrogen mixed with flushing fluid enhances the carrying capacity of the flushing fluid, more effectively removing wellbore impurities, sediments, and blockages, and restoring well productivity.
From a fluid mechanics perspective, the addition of nitrogen alters the rheological properties of the flushing fluid, increasing turbulence and enhancing the scouring force on the wellbore and tubing surfaces. Experimental data indicate that nitrogen well flushing improves pollutant removal rates by 20% to 30% compared to conventional methods, significantly enhancing flushing efficiency while minimizing reservoir damage, thereby protecting long-term well productivity.
2.5 Inerting Protection and Oil Field Safety
In oil field storage facilities and production areas, such as tank farms and gathering stations, flammable and explosive oil-gas mixtures are present. Nitrogen provided by nitrogen generators is used for inerting protection, reducing oxygen concentration in the environment to achieve an inert state, effectively preventing fires and explosions.
According to combustion reaction kinetics, when oxygen concentration is reduced below 12%, the risk of combustion and explosion for most flammable gases and dust is significantly reduced.In actual applications, by continuously filling nitrogen, the oxygen concentration in the oil tank is maintained between 8% and 10%, ensuring the safe operation of the oil tank area.
2.6 Nitrogen Fire Suppression and Emergency Fire Handling
In the event of a fire in an oil field, nitrogen produced by nitrogen generators can serve as an efficient and environmentally friendly fire suppression medium. Its inert and asphyxiating properties rapidly dilute oxygen concentration in the combustion area, inhibiting the combustion reaction and extinguishing the fire. Compared to traditional fire suppression methods, nitrogen fire suppression is pollution-free and causes minimal damage to equipment and the environment.
At fire scenes, nitrogen fire suppression systems can extinguish flames in a short time, reducing fire losses. For example, in an electrical equipment fire at an oil field, nitrogen fire suppression significantly reduced equipment damage, and post-fire repair time was shortened by over 50%, ensuring the continuity of oil field production.
2.7 Pressure Testing and Equipment Safety Evaluation
In oil field infrastructure construction and routine maintenance, pressure testing is a critical step to ensure the safety and reliability of pipelines, pressure vessels, and other equipment. Stable nitrogen provided by nitrogen generators is used for pressure testing, following Boyle’s law, to accurately determine the presence of leaks or structural defects by monitoring pressure changes.
In practice, nitrogen at a certain pressure is injected into the equipment to be tested, and high-precision pressure sensors monitor pressure changes in real-time. If the equipment has minor cracks, nitrogen will slowly leak, causing a pressure drop and allowing timely detection of safety hazards. Analysis of pressure testing data from numerous equipment pieces shows that using nitrogen as the testing medium can detect leaks as small as 0.1 mm², effectively ensuring equipment safety.
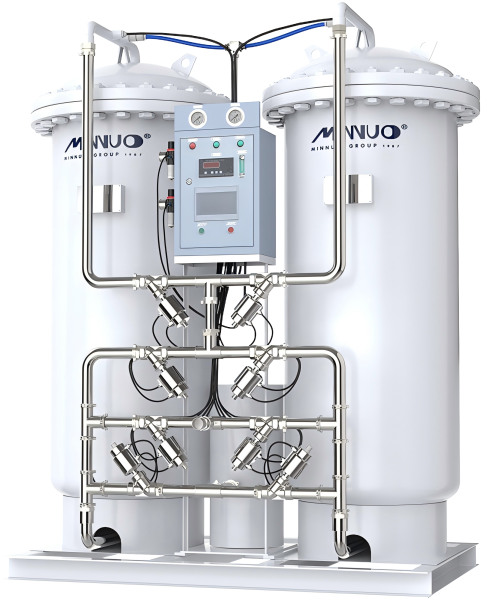
3. Performance Comparison and Selection Strategy of Different Nitrogen Generation Technologies
3.1 Purity and Flow Rate Performance Comparison
PSA nitrogen generation technology can produce high-purity nitrogen, with purity levels ranging from 99.9% to 99.999%, but with relatively lower flow rates. It is suitable for applications requiring high nitrogen purity and relatively lower demand, such as special reservoir development and high-end well testing. Membrane separation nitrogen generation technology produces nitrogen with purity levels between 95% and 99%, but with higher flow rates, making it suitable for applications requiring large nitrogen volumes and relatively lower purity, such as general gas lift operations and large-scale inerting protection in oil fields.
3.2 Equipment Cost and Operating Cost Analysis
PSA nitrogen generators have relatively complex equipment structures, requiring special adsorbents and precise control systems, resulting in higher equipment costs. However, the adsorbents have a long service life, and maintenance is relatively convenient, leading to stable operating costs. Membrane nitrogen generators have simple equipment structures, compact sizes, and lower equipment costs, but the membrane modules have a limited service life and require regular replacement. Additionally, the pre-treatment requirements for incoming air are higher, leading to relatively higher operating costs.
3.3 Application Scenario Suitability and Selection Strategy
When selecting nitrogen generation technology and equipment, oil fields should consider various factors, including operational requirements, costs, and equipment performance. For operations requiring extremely high nitrogen purity, such as nitrogen flooding in special reservoirs, PSA nitrogen generators should be prioritized. For operations requiring large nitrogen volumes and relatively lower purity, such as gas lift operations in large oil fields, membrane separation nitrogen generators are more suitable. Additionally, factors such as equipment reliability, maintenance convenience, and future production scale changes should be considered to achieve optimal production efficiency and safety. MINNUO’s professional engineering team will customize the most suitable solution for you.
4. MINNUO: A Pioneer in the Industry
Since its inception, MINNUO has been deeply committed to the field of gas separation technology, consistently prioritizing research and innovation. With its profound expertise in the development, production, and sales of nitrogen generators, MINNUO has established itself as an undisputed leader in the industry.
4.1 Experienced Team
The company has assembled a professional engineering team composed of seasoned experts and technical specialists, who possess profound knowledge and extensive practical experience in gas separation technology. The team members are not only capable of accurately understanding the complex needs of oilfield clients at various production stages but also able to provide highly targeted nitrogen generation solutions through interdisciplinary technology integration. From initial site surveys and demand analysis, to mid-term solution design and equipment selection, and finally to post-installation commissioning and after-sales maintenance, MINNUO offers a one-stop service to ensure clients have no worries.
4.2 Product Advantages
MINNUO consistently adheres to a strategy driven by technological innovation, continuously increasing investment in research and development, and exploring new technologies and processes to enhance the performance and quality of its nitrogen generators. The company’s self-developed nitrogen generator products boast numerous advantages:
- Technologically, whether it’s the high-purity nitrogen generators based on Pressure Swing Adsorption (PSA) technology or the high-flow nitrogen generators utilizing membrane separation technology, they all meet advanced industry standards, capable of stably producing nitrogen that complies with the stringent operational requirements of oilfields.
- In terms of equipment stability, MINNUO selects high-quality components, combined with rigorous manufacturing processes and strict quality inspection procedures, ensuring stable and reliable operation of the equipment, effectively reducing the incidence of equipment failures, minimizing downtime, and lowering maintenance costs for clients.
- In adaptability, the company fully considers the harsh and complex working conditions of oilfield operations, specially designing and optimizing the nitrogen generators to enable continuous and stable operation under extreme conditions such as high temperature, high pressure, and high corrosion, providing solid support for oilfield production.
In a competitive market, MINNUO has built a strong reputation through high-quality products and comprehensive services. Its offerings, including nitrogen generators in oil fields, are widely used in major oilfields nationwide, boosting efficiency and safety. Additionally, MINNUO has expanded globally, exporting to numerous countries and regions, earning trust and recognition from clients worldwide.
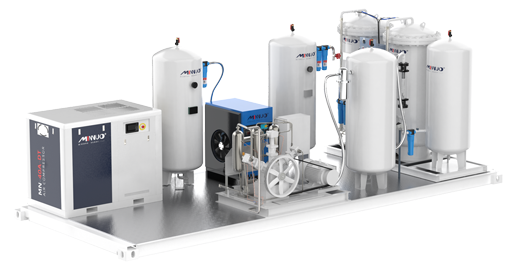
5. Conclusion
The application of nitrogen generators in oil fields covers multiple critical stages, including oil production, workover, safety assurance, and equipment maintenance. By enhancing recovery rates, ensuring operational safety, and reducing equipment wear, nitrogen generators bring significant economic and safety benefits to oil field production.
If you want your oil field operations to be more efficient, safer, and cost-effective, welcome to consult MINNUO!