In the modern healthcare system, medical oxygen concentrators are critical medical devices widely used in hospitals, clinics, and home care settings. When a medical oxygen concentrator malfunctions, it not only affects patient treatment outcomes but may also pose risks to patient safety. Therefore, a deep understanding of common faults and their solutions is essential to ensure the smooth operation of medical services.
Medical oxygen concentrators are vital in healthcare, but common issues such as startup failures, gas circuit malfunctions, abnormal oxygen concentration, and compressor faults can disrupt their normal operation. Timely diagnosis and repair measures—such as checking power supply, cleaning pipelines, and replacing damaged components—can significantly enhance device stability. Regular maintenance, including cleaning air filters and inspecting wear-prone parts, is also crucial for ensuring the proper functioning of medical oxygen concentrators.
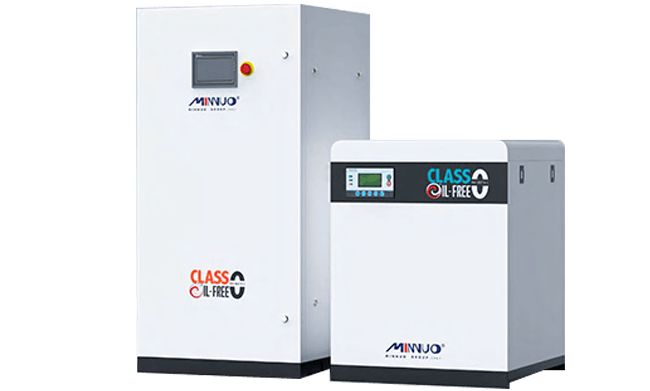
I. Working Mechanism of Medical Oxygen Concentrators
Currently, the most common working principle for medical oxygen concentrators is Pressure Swing Adsorption (PSA) technology, which relies on molecular sieves to separate nitrogen and oxygen from the air.
(1) Key Components:
- Air compressor
- Molecular sieve adsorption towers
- Control valves
- Filters
(2) Workflow:
- Air is compressed by the air compressor to increase pressure.
- The compressed air passes through filters to remove dust, impurities, and moisture.
- The purified air enters the molecular sieve adsorption tower. Under specific pressure, the molecular sieve strongly adsorbs nitrogen, while oxygen is less adsorbed, resulting in high-concentration oxygen at the tower outlet.
- When the molecular sieve becomes saturated with nitrogen, the pressure in the adsorption tower is reduced to release the adsorbed nitrogen, regenerating the molecular sieve for the next cycle of adsorption and separation.
Understanding these key components and workflow helps in diagnosing potential faults and their causes.
II. Common Fault Types and Causes
(1) Startup Failures
1.No Power Response:
Possible causes: Loose or damaged power cord, no power in the socket, or a blown fuse inside the concentrator.
2.Power Indicator Lights Up but No Operation:
- Compressor overheating protection triggered, damaged start capacitor, or motor failure.
- Prolonged continuous operation or poor heat dissipation can lead to overheating.
- Aging or breakdown of the start capacitor affects motor startup; motor winding short circuits or open circuits can also prevent normal operation.
(2) Gas Circuit Faults
1.Insufficient Oxygen Flow:
- Blocked pipelines due to accumulated impurities or foreign objects.
- Malfunctioning flow control valve.
- Insufficient air intake, such as a severely clogged air filter.
2.High-Pressure Alarm in Gas Circuit:
- Blocked outlet causing poor gas discharge and increased pressure.
- Faulty pressure sensor providing false high-pressure signals.
- Clogged muffler preventing gas from being discharged smoothly, leading to increased pressure.
(3) Abnormal Oxygen Concentration
1.Unstable Oxygen Concentration:
- Leaking pneumatic valves affecting gas switching during oxygen production.
- Faulty solenoid valves unable to control gas flow accurately.
- Degraded molecular sieve performance over time, reducing its ability to separate nitrogen and oxygen effectively.
2.Low Oxygen Purity:
- Molecular sieve poisoning due to chemical pollutants or oil impurities in the air.
- Improper switching time between adsorption towers, allowing nitrogen to mix with oxygen before being fully adsorbed.
(4) Compressor Faults
1.Compressor Fails to Start:
- Power issues such as phase loss, low or high voltage.
- Motor faults like burnt windings or short circuits.
- Internal mechanical failures such as stuck pistons or damaged bearings.
2.Compressor Cycles On and Off:
- Faulty pressure switch with inaccurate settings or damage, causing frequent cycling.
- Refrigeration system issues, such as poor condenser heat dissipation or refrigerant leakage, leading to overheating and periodic shutdowns.
3.Compressor Overheating:
- Cooling fan failure preventing proper heat dissipation.
- Insufficient or degraded compressor oil, increasing friction and heat generation.
III. Fault Diagnosis Methods
(1) Initial Visual Inspection
- Check if the power cord is securely connected and undamaged.
- Inspect the fuse on the concentrator panel for signs of blowing; replace if necessary after identifying the cause.
- Observe the status of panel indicators to assess power and operational status.
- Check all pipeline connections for tightness and signs of loosening or detachment.
(2) Systematic Troubleshooting Process
- Start with the power supply, then move to the gas circuit system.
- Inspect the air intake, air filter, compressor, pipelines, valves, and flow control valves for blockages or damage.
- Finally, examine core components like the molecular sieve adsorption towers, pneumatic valves, and solenoid valves for proper operation.
(3) Tool-Assisted Diagnosis
- Use a pressure gauge to measure pressure at various points in the gas circuit to ensure it is within normal operating range.
- Use a leak detector to check for gas leaks along pipelines and valves.
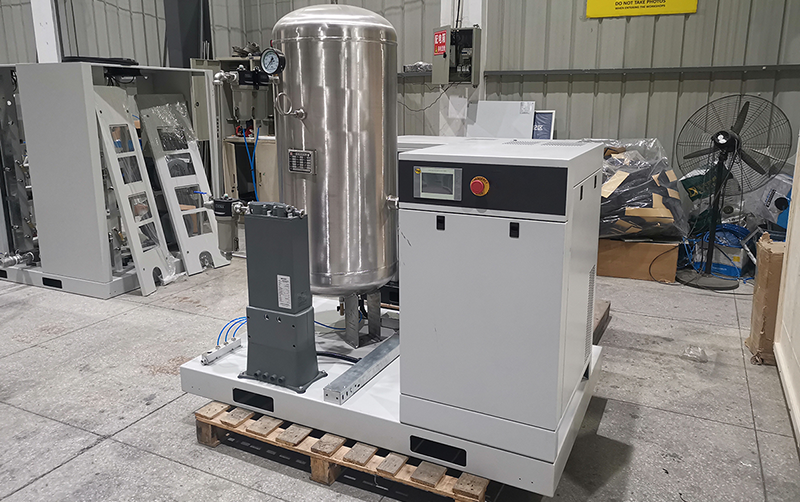
IV. Solutions and Repair Measures
(1) Startup Fault Solutions
1.No Power Response:
- Reconnect the power cord securely; replace if damaged.
- Test the power socket with another device.
- Replace the fuse with one of the same rating and check for short circuits.
2.Power Indicator Lights Up but No Operation:
- Allow the compressor to cool down; check the cooling fan and ventilation.
- Replace the start capacitor.
- Repair or replace the motor if faulty.
(2) Gas Circuit Fault Solutions
1.Insufficient Oxygen Flow:
- Clean or replace blocked pipelines.
- Repair or replace the flow control valve.
- Clean or replace the air filter.
2.High-Pressure Alarm in Gas Circuit:
- Clear blockages at the outlet.
- Calibrate or replace the pressure sensor.
- Clean or replace the muffler.
(3) Abnormal Oxygen Concentration Solutions
1.Unstable Oxygen Concentration:
- Replace damaged pneumatic valve seals or adjust their parameters.
- Repair or replace faulty solenoid valves.
- Supplement or replace the molecular sieve if performance is degraded.
2.Low Oxygen Purity:
- Replace the molecular sieve if poisoned and improve air intake quality.
- Adjust the switching time between adsorption towers.
(4) Compressor Fault Solutions
1.Compressor Fails to Start:
- Fix power supply issues.
- Repair or replace the motor.
- Repair or replace damaged mechanical components.
2.Compressor Cycles On and Off:
- Calibrate or replace the pressure switch.
- Repair the refrigeration system and replenish refrigerant.
3.Compressor Overheating:
- Repair or replace the cooling fan.
- Replenish or replace compressor oil.
V. Maintenance Recommendations
(1) Regular Inspections
Conduct weekly visual checks and monthly comprehensive inspections, including gas circuit pressure and oxygen concentration tests.
(2)Cleaning and Maintenance
Clean the air filter every 1-2 weeks and the exterior to prevent dust buildup.
(3)Replacement of Wear-Prone Parts
Replace filter elements, lubricants, and molecular sieves as recommended in the user manual.
(4)Operating Environment
Place the concentrator in a dry, well-ventilated area, away from moisture, high temperatures, direct sunlight, chemical pollutants, and strong electromagnetic interference.
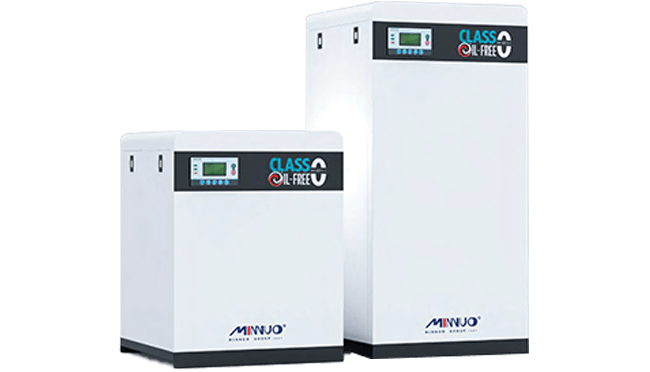
VI. MINNUO Medical Oxygen Concentrators
Among many brands, MINNUO medical oxygen concentrators stand out with their remarkable advantages.
(1) Efficient and Stable Oxygen Production
MINNUO concentrators use advanced molecular sieve technology to deliver high-concentration oxygen reliably. Their specially treated molecular sieves offer high adsorption efficiency and long service life, minimizing oxygen concentration issues. Even during prolonged operation, they maintain stable oxygen levels, ensuring reliable oxygen therapy for patients.
(2) Reliability and Durability
MINNUO concentrators feature high-quality compressors and components. Their compressors have robust power output, excellent heat dissipation, and lubrication systems, reducing failure rates. For example, unique heat dissipation designs and efficient cooling fans keep compressor temperatures within safe limits, while high-quality lubricants minimize wear and extend compressor life. Additionally, precision valves and sealing materials in the gas circuit prevent leaks and flow instability.
(3) User-Friendly Design and Ease of Operation
MINNUO concentrators are designed with user convenience in mind. Their intuitive interface, clear display, and real-time indicators for oxygen flow, concentration, and operational status make them easy to use, even for first-time users. Smart alarm systems notify users of abnormalities, such as low oxygen concentration or pressure issues, ensuring safe operation.
VII. Conclusion
The stable operation of medical oxygen concentrators is crucial for healthcare. Understanding common faults and their solutions, along with regular maintenance, reduces failure rates and ensures reliable oxygen supply for patients. Healthcare professionals and maintenance staff should continuously improve their troubleshooting skills to maintain medical equipment effectively.
Remember, MINNUO, a leading manufacturer of high-end medical oxygen concentrators, is always your trusted partner!