Nitrogen generators are widely used in industries such as chemicals, electronics, pharmaceuticals, and food processing. Their operation involves complex processes such as high-pressure gas handling, power systems, and inert gas discharge. Improper management may lead to serious accidents. This article systematically outlines the common safety hazards of nitrogen generators and provides targeted solutions to help enterprises achieve safe production, ensuring both employee safety and the protection of company property.
During operation, nitrogen generators are exposed to multiple safety hazards such as PLC misoperation, high-pressure leakage, oxygen-rich emissions, asphyxiation risks, and electrical faults. Without proper prevention and control, these risks can easily lead to personal injury and property loss. By implementing power lockouts, optimizing pipeline structures, improving exhaust and ventilation systems, deploying oxygen content/electrical monitoring devices, and enhancing operational training and emergency drills, a multi-layered safety protection system can be established to ensure the safe management of nitrogen equipment throughout its entire lifecycle.
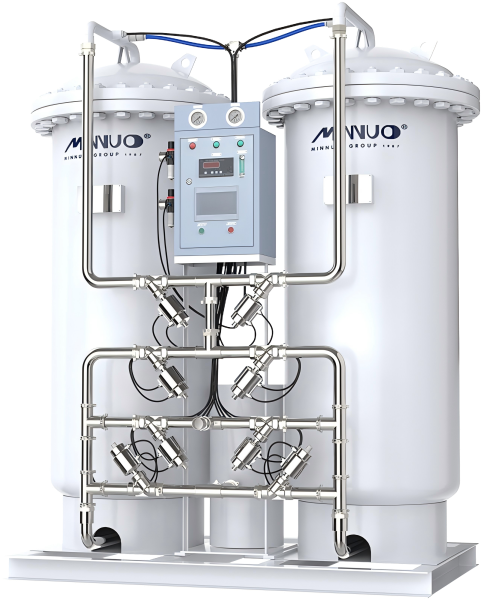
I. PLC Misoperation Risk: Cut Off Accidental Startups at the Source
Problem Analysis
The PLC (Programmable Logic Controller) of a nitrogen generator is regarded as the “brain” of the equipment, responsible for the system’s automated logic control. It governs key processes such as air compressor start/stop, dryer system switching, and adsorption tower transitions. However, during maintenance or servicing, if the PLC is not powered off or access is not restricted, accidental restarts due to misoperation may cause sudden equipment movements, resulting in injury.
Potential Risks
- Personal injury: Sudden startup during servicing may cause crushing or pinching injuries.
- Equipment damage: Unexpected starts can cause motor overcurrent, valve misalignment, or even damage control components.
- Production interruptions: Emergency shutdowns after misoperation may interrupt production and delay deliveries.
Solutions
Strict Power Management:
- Disconnect the main power before maintenance, and hang a clear “Under Maintenance, Do Not Switch On” sign.
- MINNUO recommends implementing a dual power isolation system that automatically disconnects PLC power during maintenance.
- Use electrical locks to prevent unauthorized personnel from accessing the system.
Access Level Control:
- Set hierarchical access in the PLC program; only personnel with high-level authorization can modify operating parameters or start equipment.
- Restrict access using IC cards, passwords, or physical keys to avoid accidental touch.
- Equip emergency stop buttons (E-Stop) for immediate power-off in critical situations.
Hardware Interlock Protection:
- Install mechanical or electrical interlock switches on control cabinets or maintenance chambers; opening the cabinet door triggers automatic power cut.
- Integrate interlock with PLC I/O points for logic control, ensuring misoperations are invalidated.
II. High-Pressure Gas Leakage and Pipe Rupture: Preventing “Invisible Bombs”
Problem Analysis
The nitrogen system operates under high pressure throughout its workflow—from compressor output to drying, purification, and storage in nitrogen buffer tanks. Systems running at 0.6–1.0 MPa are especially vulnerable. If pipes, valves, or joints leak, the escaping high-pressure gas may cause injuries due to airflow impact or flying debris, creating an “invisible bomb” scenario.
Typical Accident Scenarios
- Discharge hose not securely fastened, whipping around under high pressure and injuring workers.
- Adsorption tower flange gasket failure leading to high-pressure gas jet, causing equipment vibration and injury.
Solutions
Optimized Piping Structure:
- Design pipes according to ASME B31.3 industrial standards; recommend using high-strength seamless steel pipes like 304 stainless or galvanized steel.
- Use metallic spiral-wound gaskets for all flanged connections to enhance sealing and pressure resistance.
- Avoid PVC materials to prevent brittleness under high pressure and temperature.
Regular Leak and Pressure Testing:
- Perform ultrasonic leak detection quarterly, focusing on joints and pressure points.
- Conduct static pressure tests annually, holding 1.5x working pressure for 30 minutes to verify system tightness.
- Install pressure gauges and safety valves at exhaust ports to prevent overpressure operation.
Enhanced Safety Protection:
- Install mufflers and protective covers at exhaust outlets to prevent injury from direct gas flow.
- Mark pipe surroundings with warning lines and “High Pressure Hazard” signs to restrict access to trained personnel.
III. Fire Hazards from Oxygen-Rich Emissions: Eliminate the Combustion Triangle
Problem Analysis
In PSA (Pressure Swing Adsorption) nitrogen systems, exhaust gas is primarily composed of oxygen-rich gas, with concentrations reaching up to 95%—far higher than the 21% in ambient air. Such environments drastically lower ignition points and accelerate combustion. If this gas leaks near oil or chemicals, it significantly raises the risk of fire or explosion.
Typical Case
At an electronics factory, the oxygen vent of the nitrogen generator was within 5 meters of a lubricant tank. The high-concentration oxygen mixed with oil vapors and was ignited by an electric spark, causing a major fire.
Solutions
Isolated Discharge System:
- Route oxygen exhaust pipes to open outdoor areas at least 15 meters away from open flames, power sources, or flammable materials.
- Install flame arrestors at pipe ends to prevent flame backflow into the system.
Real-Time Environmental Monitoring:
- Install oxygen concentration sensors near the equipment, linked to an alarm system to trigger shutdowns if concentration exceeds 23.5%.
- Use explosion-proof electrical components rated Ex d IIB T4 or higher to eliminate ignition sources.
Standardized Operations and Cleaning:
- Prohibit hot work within 5 meters of the operational area.
- Regularly clean carbon deposits and dust from adsorption towers and pipelines to prevent spontaneous ignition.
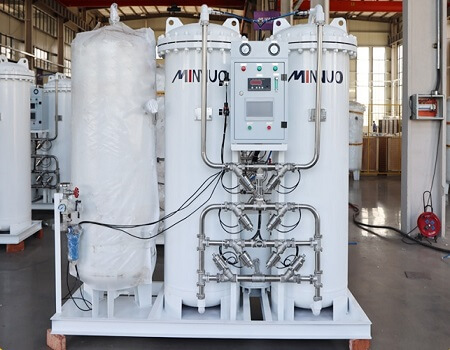
IV. Asphyxiation Risk from High-Purity Nitrogen: Beware of the “Silent Killer”
Problem Analysis
Nitrogen is colorless, odorless, and non-toxic, but has a strong capacity to displace oxygen. In enclosed spaces, nitrogen concentrations over 84% can lead to rapid unconsciousness or death due to hypoxia. Such accidents often occur in tanks, maintenance wells, or poorly ventilated small rooms.
Key Risk Points
- Failure to purge nitrogen from buffer tanks before maintenance, resulting in asphyxiation upon entry.
- Long-term operation of lab-scale nitrogen equipment in sealed rooms leads to nitrogen buildup and poor air quality.
Solutions
Improved Ventilation System:
- Equipment rooms should have ≥12 air changes/hour, using explosion-proof fans to ensure airflow safety.
- Add localized exhaust hoods at nitrogen usage points with extraction speed of at least 0.5 m/s.
Oxygen Deficiency Warning Devices:
- Install wall-mounted oxygen analyzers (0–25% range) to trigger alarms and start ventilation when oxygen drops below 19.5%.
- Link to PLC for automatic shutdown to prevent further gas accumulation.
Emergency Response and Training:
- Personnel entering confined spaces must wear positive pressure air respirators and remain tethered for external communication.
- All rescues require two-person teams; conduct emergency drills every six months to ensure response readiness.
V. Electrical Safety Risks: The Deadly Threat of High Voltage
Problem Analysis
Nitrogen generators typically operate on 380V three-phase AC, with some models containing high-voltage inverters and control cabinets. Improper onsite handling can lead to electric shock, arc burns, or even fire and explosion.
Common Violation
- Replacing contactors under live conditions without power-off procedures.
- Using copper wire in place of fuses, causing uninterruptible short circuits.
- Unauthorized circuit modifications or maintenance without schematics.
Solutions
Enhanced Electrical Protection:
- Control cabinets must meet IP54 standards for dust and splash protection.
- All metal casings and exposed conductors must be properly grounded with resistance ≤4Ω.
- Use transparent barriers around high-voltage components to prevent accidental contact.
Smart Safety Devices:
- Install leakage protectors (trip current ≤30mA) with 0.1-second cut-off response.
- Use thermal relays and electronic modules for dual motor protection with real-time monitoring.
Certified Operators
- All electrical maintenance personnel must hold special operation certificates and undergo professional training.
- MINNUO offers custom training courses covering schematic interpretation, equipment operation, and fault code analysis.
VI. MINNUO Safety Technology Upgrades: Building a Multi-Layered Protection System
To enhance the safety of customers during use, MINNUO continues to integrate advanced safety technologies into its nitrogen generation equipment, creating a multi-layered defense system that combines both proactive defense and passive protection:
- Intelligent Safety Interlocking System (ISL): Monitors key parameters such as pressure, temperature, and oxygen content. In case of any abnormalities, the system immediately shuts down and sends a remote alarm.
- Modular Quick-Assembly Design: Significantly reduces on-site welding work. All flanges are equipped with a safety pin locking mechanism to prevent detachment.
- Remote Monitoring Platform: Supports real-time viewing of equipment operating status on mobile phones or computers, remote diagnostics, and quick response to failures.
- Self-Diagnosis System: Embedded error code prompts within the PLC for rapid fault point identification, reducing maintenance time.
- Customer Safety File Management: Each device that leaves the factory has an operational data file for easy future tracking and safety audits.
VII. Conclusion
Nitrogen generator safety management is a systematic project involving equipment selection, process design, personnel training, and regular inspections. MINNUO urges all business users to establish a “Safety First” mindset from the source, and create a three-dimensional safety system covering “Technical Protection + System Management + Awareness Enhancement.” Only by integrating safety into every detail can long-term stable operation of equipment be ensured, safeguarding the production of enterprises.