In the electronics manufacturing industry, Surface-Mount Technology (SMT) is a key process for producing high-precision electronic components. With the widespread adoption of lead-free soldering and increasing environmental requirements, nitrogen protection technology has become an indispensable part of SMT soldering. In this process, nitrogen generators, as the equipment that produces nitrogen, play a crucial role. This article will detail the core applications and technical advantages of nitrogen generators in SMT soldering.
The application of nitrogen generators in SMT soldering primarily involves providing a high-purity nitrogen environment to prevent oxidation, enhance soldering reliability, and meet the needs of lead-free soldering. The protective effect of nitrogen effectively reduces soldering defects, improves the appearance and consistency of solder joints, and simultaneously reduces thermal stress and PCB deformation. Compared to traditional liquid nitrogen, PSA nitrogen generators have lower operating costs and greater flexibility, providing customized nitrogen solutions that help enterprises improve production efficiency, reduce costs, and ensure product quality.
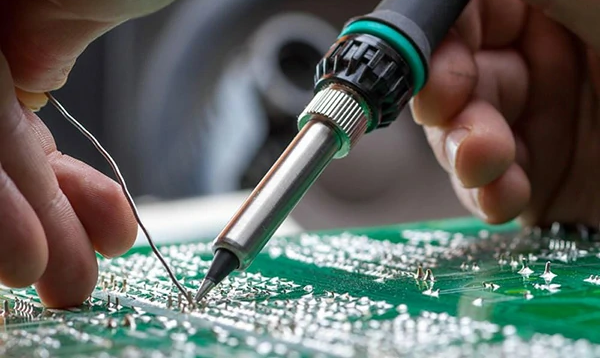
1. Core Role of Nitrogen in SMT Soldering
1.1 Preventing Oxidation and Improving Soldering Reliability
During SMT soldering, the high-temperature environment causes solder to react with oxygen in the air, potentially leading to solder defects such as solder balls or cold joints. Oxidation not only affects soldering quality but may also lead to circuit board malfunctions and even damage to components. Nitrogen, as an inert gas, effectively isolates oxygen and reduces the oxygen content in the soldering area. When oxygen content is controlled below 100ppm, the oxidation reaction is nearly suppressed, thus effectively preventing oxidation defects in the solder joints. This process ensures smooth and strong solder joints, improving soldering quality and reliability.
1.2 Meeting Lead-Free Process Requirements
With the gradual increase in environmental regulations, the electronics manufacturing industry has been transitioning to lead-free soldering. Lead-free solders have a higher melting point, usually above 200°C, and oxidize faster. Nitrogen protection can effectively delay the oxidation process of lead-free solder, helping maintain better wettability of the solder and reducing solder paste residues, thereby improving soldering results. Additionally, nitrogen protection enhances the repeatability and consistency of solder joints, particularly in high-precision soldering scenarios such as fine-pitch components and flip-chip applications, where nitrogen’s role is especially significant.
1.3 Enhancing Solder Joint Appearance and Consistency
Residues from flux are an important factor affecting the appearance of solder joints during soldering. Nitrogen environments effectively reduce flux residues, making the surface of the solder joint smoother and shinier. At the same time, nitrogen protection reduces the risk of copper oxidation, preventing quality issues caused by oxidation of copper substrates during soldering. By controlling the atmosphere during the soldering process, nitrogen helps ensure the consistent appearance of each solder joint, improving the overall quality and usability of the final product.
1.4 Reducing Thermal Stress and Deformation
In SMT soldering, especially in wave soldering, thermal stress can cause deformation of the circuit board, affecting soldering quality. The rapid cooling characteristics of nitrogen during soldering can significantly reduce thermal stress, preventing PCB deformation. This ensures stable soldering and further enhances the overall performance of electronic components. The use of nitrogen not only ensures soldering quality but also improves production efficiency and product stability.
2. Technical Advantages and Key Considerations for Selecting Nitrogen Generators
2.1 Efficient Nitrogen Production Technology: PSA Pressure Swing Adsorption
PSA (Pressure Swing Adsorption) nitrogen generators are one of the most widely used technologies in the electronics manufacturing industry. This technology selectively adsorbs oxygen from the air using carbon molecular sieves, directly separating nitrogen. By controlling the adsorption and desorption processes, PSA nitrogen generators can continuously and stably provide nitrogen with a purity of 99.9% to 99.999%, meeting the high-quality nitrogen requirements of SMT soldering processes. Compared to traditional liquid nitrogen technologies, PSA nitrogen generators offer several technical advantages:
- Low Operating Costs: The production cost of nitrogen per cubic meter is only approximately 0.05–0.1 USD, which is more than 50% cheaper than liquid nitrogen, resulting in significant cost savings for enterprises.
- Modular Design: The modular design of PSA nitrogen generators allows the equipment to be flexibly expanded. Users can choose to parallel multiple units based on the different scale requirements of the production line to meet the growing nitrogen demand.
- Automated Control: PSA nitrogen generators are typically equipped with fully automated control systems that can monitor nitrogen purity and flow in real-time, with automatic alarms in case of equipment failures. This system significantly reduces manual intervention and increases production automation.
2.2 Key Selection Parameters
When selecting a nitrogen generator, the following key parameters need to be considered:
- Purity Requirements: Depending on the soldering process, the required nitrogen purity will vary. For SMT processes, the nitrogen purity typically needs to be 99.9% (1000ppm oxygen content) or higher (e.g., 99.99%). The choice of purity standard should be made based on the specific production requirements.
- Flow Matching: The nitrogen demand for SMT production lines usually ranges from 10 to 30Nm³/h, so flow matching is critical during selection. The flow rate should be adjusted according to the reflow soldering furnace model, PCB size, and production scale to ensure stable supply during production.
- Energy Consumption Optimization: Efficient PSA nitrogen generators consume only 0.42 kWh of electricity per cubic meter of nitrogen, significantly reducing the long-term operational costs of the equipment.
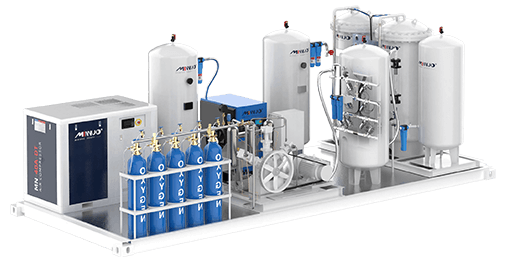
3. Economic Analysis and Case Comparisons
3.1 Economic Advantages Compared to Traditional Liquid Nitrogen
Traditional liquid nitrogen typically requires storage and transportation, which not only makes the cost of liquid nitrogen higher but also adds extra costs for transportation and storage. In contrast, PSA nitrogen generators produce nitrogen on-site, avoiding transportation and storage costs, resulting in significant cost savings.
For a production line with an annual nitrogen production of 2.6 million cubic meters, after using a PSA nitrogen generator, the nitrogen cost is only 0.05 USD per cubic meter, compared to the 0.2–0.4 USD per cubic meter for liquid nitrogen, saving a substantial amount. Based on these calculations, annual savings can reach 200,000 USD.
Additionally, PSA nitrogen generators have a short payback period, typically around 1.5 years. In a case with an electronics manufacturer, after adopting MINNUO nitrogen generators, the soldering defect rate decreased by 30%, production efficiency improved by 15%, and the payback period shortened to 18 months. This demonstrates that with reasonable equipment investment, companies can recover their investment in a short period and start enjoying the cost advantages of nitrogen production.
3.2 Reducing Production Costs and Improving Efficiency
In addition to direct cost savings, nitrogen generators also help reduce production costs by improving production efficiency. The protective effect of nitrogen reduces soldering defects, lowers rework rates, and increases product yield. By optimizing the nitrogen environment, the stability of the production line is enhanced, further reducing downtime and maintenance frequency, and improving overall equipment utilization.
4. Core Value of MINNUO Nitrogen Generators
As a professional nitrogen generator supplier, MINNUO offers several core advantages in its nitrogen solutions:
- Customized Solutions: MINNUO provides highly customized nitrogen solutions tailored to the specific needs of the SMT industry. Whether it’s nitrogen purity or flow rate, adjustments can be made flexibly based on specific production needs.
- High Stability and Low Maintenance: MINNUO nitrogen generators use advanced technology to ensure long-term stable operation of the equipment. Additionally, their modular design makes cleaning and maintenance easier, significantly reducing maintenance costs and frequency.
- Environmental Protection and Safety: MINNUO nitrogen generators comply with international environmental standards, using zero-pollution emission technology. They not only meet lead-free production requirements but also provide strong support for the sustainable development of enterprises.
5. Conclusion
As the electronics manufacturing industry continues to demand higher soldering precision and environmental protection, the application of nitrogen generators in SMT soldering will become increasingly important. MINNUO, with its advanced PSA nitrogen technology and extensive industry experience, provides efficient and reliable nitrogen solutions to global customers, helping enterprises reduce production costs while improving product quality and production efficiency.
Contact MINNUO Nitrogen Generators now and start your smart soldering journey today!