The Nitrogen generator is more and more widely used in various industries, especially in the fields of chemical, pharmaceutical, food packaging and metal processing. They not only play an important role to providing high-purity nitrogen, but also make great contributions in reducing production costs and improving production efficiency(by calculate purity and flow). The performance of nitrogen generators directly affect the efficiency and safety of these industries.
In this article, we will focus on the influence of purity and flow rate on the performance of equipment in nitrogen generator selection, and help enterprises how to calculate the appropriate nitrogen generator specifications according to the actual needs, so as to ensure that the equipment meets the specific requirements of industrial applications. In addition, we will also provide some selection suggestions and considerations to help enterprises better cope with the selection and use of nitrogen generation equipment.
Through an in-depth analysis of the common challenges and solutions in the selection process of nitrogen generators, this article helps you have a clearer understanding of the role of nitrogen generators in different applications and how to optimize the selection based on flow rate, purity and other parameters to ensure a long-term stable gas supply. At the same time, we will also introduce how to select a suitable nitrogen generator through customized design to meet the special needs of the industry and ensure the efficient operation and reliability of enterprise equipment.
I. Basic working principle of nitrogen generator
1. Overview of PSA Technology
PSA (Pressure Swing Adsorption) technology is one of the most commonly used technologies for nitrogen generation. The technology utilizes the properties of adsorbent materials (e.g. molecular sieves) to adsorb and desorb gases at different pressures, thus separating nitrogen and oxygen in the air. A PSA system usually consists of two main steps: adsorption and desorption.
Adsorption stage: Under high pressure, air is introduced into the adsorption tower, and the molecular sieve adsorbs the oxygen and moisture from the air, and the remaining nitrogen is separated and exported.
Desorption stage: By lowering the pressure, the adsorbed oxygen and moisture are released and recycled again, thus maintaining the long-lasting adsorption capacity of the molecular sieve.
PSA nitrogen generators usually consist of two adsorption towers working alternately, each adsorbing and desorbing at different pressures, ensuring a continuous supply of nitrogen.
Technical Advantages:
Efficient Nitrogen Separation Capability: PSA systems are capable of delivering high purity nitrogen on demand, typically with purities ranging from 95% to 99.9%.
Continuous operation: The technology operates 24/7, making it suitable for industrial environments where a continuous supply of nitrogen is required.
Energy-saving and cost-effective: Compared with the traditional way of transporting liquid nitrogen, the PSA system reduces transportation and storage costs by producing nitrogen on site.
2. Applicable Scenarios and Practical Applications
The selection of nitrogen generators does not only depend on the technical principle, but is also closely related to the industrial application scenarios and practical requirements.
Application examples:
Oil and gas industry: In the inert treatment of oil and gas pipelines, downhole stimulation and high-pressure testing, the purity and flow rate of nitrogen are crucial to the stability of the system.
Food and beverage industry: Nitrogen is used in packaging and storage processes, where its primary function is to replace oxygen in order to extend product shelf life. Such applications usually require relatively low nitrogen purity, but still need to ensure a stable flow rate to ensure efficient production.
Metal processing industry: Used in welding or cutting process to protect metal surface from oxidation, the purity and flow rate of nitrogen directly affect the process quality.
How to choose:
According to the application needs, determine the purity and flow rate requirements of nitrogen, and then choose the right generator:
Low purity needs: such as gas separation, welding and other fields, PSA system can provide enough nitrogen.
High Purity Requirements: For industries requiring higher purity nitrogen, such as electronics manufacturing or certain chemical processes, a VPSA system is the preferred choice.
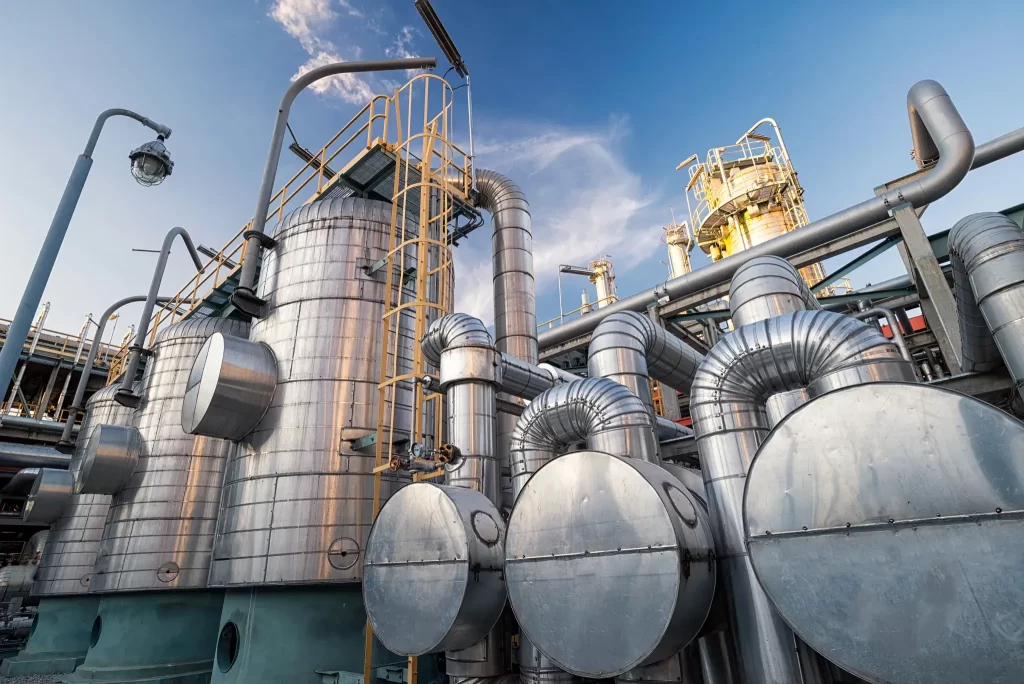
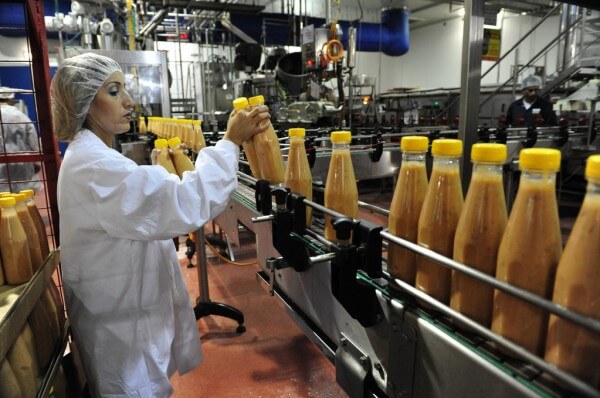
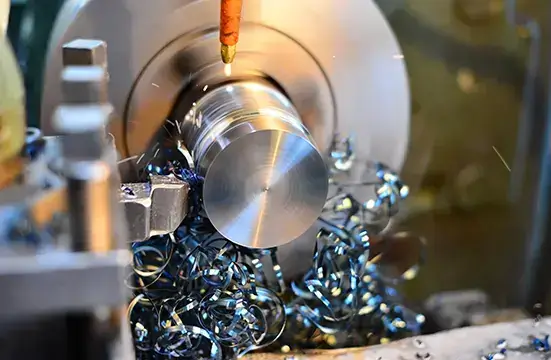
II. Definition and Effects of Purity and Flow Rate
1. Definition of Nitrogen Purity
Nitrogen purity refers to the amount of nitrogen molecules in nitrogen gas, relative to the proportion of oxygen and other impurities. The purity of nitrogen is usually expressed as a percentage (%). For example, 99.9% nitrogen means that out of every 100 gas molecules, 99.9 are nitrogen molecules, while the remaining 0.1% may consist of oxygen, carbon dioxide, or other gases.
In industrial and medical applications, the purity of nitrogen has a direct impact on the effectiveness of the use. For example:
EOR (Enhanced Oil and Gas Recovery): In oilfield development, nitrogen is injected downhole to increase the pressure and push the remaining oil and gas to the surface. High purity nitrogen (99.9% or higher) prevents reactions and contamination and enhances oil and gas recovery.
Welding: During metal welding, the high purity of nitrogen effectively prevents oxidizing reactions and protects the welding area.
Food packaging: Nitrogen is used to replace oxygen in packaging to extend the shelf life of food. At this time, the purity of nitrogen does not need to be too high, usually 95% purity can meet the demand.
2. Definition of Nitrogen Flow Rate
Nitrogen flow rate refers to the speed of nitrogen flow in the system, usually expressed in “cubic meters per hour (Nm³/h)” or “liters per minute (L/min)”. The choice of flow rate is usually determined by actual demand and involves a number of factors such as gas supply capacity, piping and equipment design.
Impact of Nitrogen Flow Rate:
Impact of flow rate on the system: too low a flow rate may result in the equipment not being able to perform the required task in the expected time, while too high a flow rate may result in unnecessary waste of energy and overloading of the system.
Matching the flow rate to the equipment: Depending on the application, the flow rate needs to be matched to the equipment’s gas passages, pipe capacity and other parameters. For example, during the welding process, if the flow rate is too low, the nitrogen cannot effectively cover the welding area, which may lead to oxidization; if the flow rate is too high, it may waste energy and increase system pressure.
Purity and Flow Rate Correlation:
In many applications, purity and flow rate go hand in hand. For example, in the inerting of oil and gas pipelines, nitrogen not only requires high purity (99.9%) to avoid the risk of explosion, but also high flow rates to quickly remove oxygen from the pipeline to ensure safe operation.
On the other hand, in some simple food packaging applications, where flow rates are required to be lower, nitrogen purity can be appropriately lowered, thus reducing operating costs.
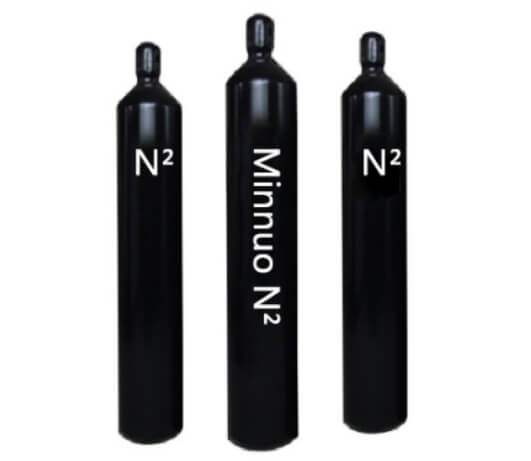
III. How to Calculate the Specification of Nitrogen Generator
1. Calculate Nitrogen Flow Rate
Calculation of nitrogen flow rate is one of the key factors in selecting a suitable nitrogen generator. The flow rate (usually expressed in “cubic meters per hour (Nm³/h)” or “liters per minute (L/min)”) determines the capacity of nitrogen supply, which directly affects the stability and efficiency of the system.
Calculation formula for flow rate:
Calculation formula for flow rate: Flow rate = Usage demand / Flow rate coefficient
where the usage demand is based on the amount of nitrogen required for industrial applications such as welding, packaging, EOR, etc. The flow rate is based on the amount of nitrogen used in the application.
The flow coefficient is used to correct for influencing factors in the actual application, e.g. ambient temperature, pressure, etc.
Example:
Welding application: If a nitrogen supply of 100 m3/hour is required during welding and the flow coefficient is 1.1 (taking into account ambient temperature and pressure variations), the required flow rate is: 100 m3/hour × 1.1 = 110 m3/hour.
Pressure testing applications: such as pipeline pressure testing, it is necessary to ensure that the continuous flow rate of nitrogen is sufficient to complete the test within the specified time. For example, if the hourly flow rate requirement is 150Nm³, the actual selection of the nitrogen generator needs to meet this flow rate requirement.
2. Calculating Nitrogen Purity
Nitrogen purity refers to the proportion of nitrogen molecules in nitrogen gas, usually expressed as a percentage. Depending on the application requirements, the purity of nitrogen may be different. For example:
EOR (Enhanced Oil and Gas Recovery): the purity requirement is high, usually up to 99.9% to ensure operational safety.
Food Packaging: Nitrogen purity requirements are lower, usually between 95% and 98% to meet the needs.
Calculation of Nitrogen Purity:
Selecting Nitrogen Purity: Select the nitrogen generator according to the specific application requirements and equipment performance. For example, in order to avoid oxidization of metal surfaces during welding operations, the purity of nitrogen gas needs to reach 99.9%. For gas substitution, the purity requirement can be relatively low.
Impact of purity on flow rate:
Higher purity nitrogen may require a higher flow rate to maintain an effective supply, as the higher the purity, the more time and pressure control may be required for the gas separation process in the system.
When selecting a nitrogen generator, the relationship between flow rate and purity needs to be balanced to ensure that the two are harmonized for optimum economics and performance.
3. Select the type of nitrogen generator according to actual needs
Selecting the right type of nitrogen generator (e.g. PSA, Membrane, VPSA) according to different application needs and required flow rate and purity is the key to selection.
PSA Nitrogen Generator: Suitable for most industrial needs, providing higher purity nitrogen, usually used for welding, packaging and some small industrial applications.
VPSA Nitrogen Generators: Suitable for high flow rate low purity nitrogen needs, especially in applications requiring high recovery (e.g. EOR in the oil and gas industry).
Membrane Nitrogen Generators: For low flow rates and low purity requirements, suitable for space-critical locations such as small laboratories or low flow application scenarios.
Key parameters for equipment selection:
Pressure requirements: Different types of nitrogen generators can provide different pressure ranges, and the selection should be matched to the needs of the application scenario (e.g. working pressure).
Working environment: Temperature, humidity and other environmental factors will affect the performance and operating efficiency of the nitrogen generator, and it is necessary to select equipment that is suitable for the environmental conditions.
4. Estimating energy consumption and running cost
Calculating the running cost and energy consumption of nitrogen generator is an important step in the selection process. According to the flow rate, purity and time period of equipment operation, the power consumption of the equipment can be estimated.
Calculation of energy consumption:
Formula for calculating power consumption: Power consumption = Nitrogen generator power × number of hours of use
In general, the energy efficiency of PSA and VPSA systems is different. PSA systems have relatively low power consumption, while VPSA systems have higher power consumption due to the need for vacuum pumps.
IV. Other Factors Affecting the Performance of Nitrogen Generators
1. Influence of external environment
The external environment, especially temperature and humidity, directly affects the operating efficiency and performance of a nitrogen generator. Changes in temperature and humidity will change the flow characteristics of the gas inside the nitrogen generator, thus affecting its gas separation effect and gas production stability.
Temperature influence: High temperature environment may cause gas molecules to move faster, affecting the adsorption efficiency of molecular sieve, while low temperature environment may limit the adsorption capacity of molecular sieve. System design needs to consider the environmental temperature fluctuations to ensure that the equipment can operate stably at different temperatures.
Impact of humidity: High humidity in the air can cause molecular sieves to adsorb water and reduce their adsorption efficiency. Especially in the gas separation process, moisture has a significant impact on the purity of nitrogen. Therefore, the nitrogen generator needs to be equipped with an efficient dehumidification system to ensure the purity and flow stability of nitrogen.
Solution:
Choose a nitrogen generator system that adapts to different ambient temperatures and humidity changes, and use air conditioning or heating devices to adjust the ambient conditions if necessary.
2. Equipment Maintenance and Periodic Inspection
Regular equipment maintenance is essential to ensure the stability and long-term efficient operation of the nitrogen generator. System components such as molecular sieves, compressors, pressure sensors, etc. need to be inspected and maintained periodically to prevent malfunctions from affecting equipment performance.
Maintenance intervals: Nitrogen generators should be inspected according to the manufacturer’s recommended intervals, especially for molecular sieve replacement and compressor maintenance.
Troubleshooting: Through regular inspections, potential equipment problems, such as malfunctioning pressure sensors or malfunctioning valves, can be found and repaired in a timely manner to avoid interruption of system operation or unstable nitrogen supply.
Solution:
Establish a maintenance program for the equipment and regularly inspect key components, especially molecular sieves and compressors.
Use an automatic monitoring system to provide real-time feedback on equipment operating status and early warning of potential problems.
3. Areas adapted by nitrogen generators
Different application scenarios have different performance requirements for nitrogen generators, especially in special environments, such as high altitude areas or severe cold areas. The equipment must be able to adapt to these special conditions to ensure a stable supply of nitrogen.
High altitude areas: in high altitude places, the air density is low, the adsorption process of the nitrogen generator may be affected, and it is necessary for the equipment to be able to work normally in a low oxygen environment to maintain high nitrogen production.
High temperature or very cold area: In high temperature area, the nitrogen generator needs to have good heat dissipation function; while in cold area, the equipment should be able to withstand low temperature and prevent the equipment damage caused by frost and low temperature.
Solution:
In special environments, choose nitrogen generators with high adaptability and consider additional environmental adjustment measures, such as temperature control systems.
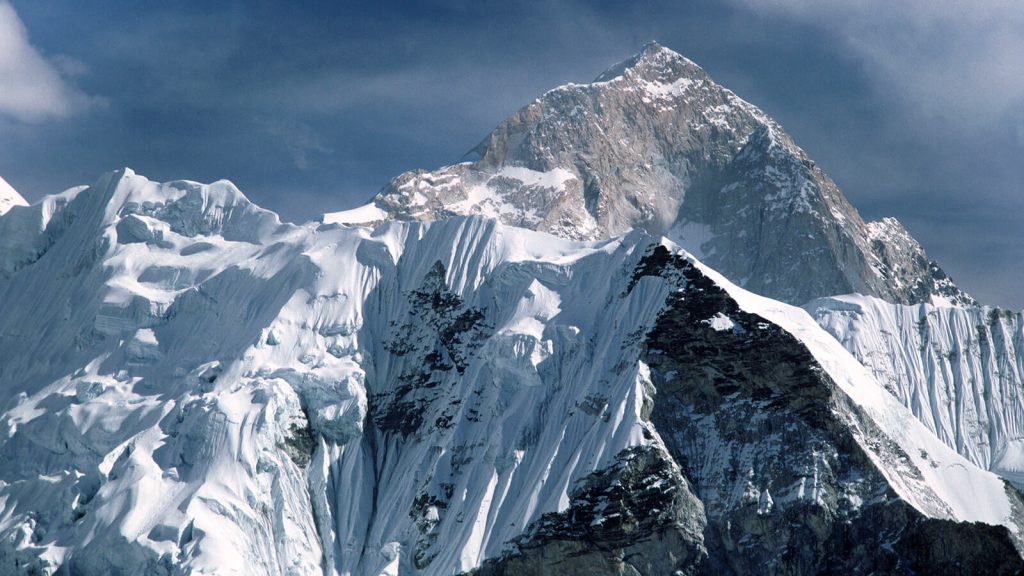
V. Selecting the right model of nitrogen generator
1. Comparison of different brands of nitrogen generators
There are various brands of nitrogen generators in the market, mainly including MINNUO, Air Products, Parker and so on. The performance of different brands of nitrogen generators varies, and users should make a comprehensive comparison of their performance, reliability, maintenance cost and market reputation when choosing.
Comparison of performance: For different brands of nitrogen generators, compare their gas separation efficiency, gas production stability, operating costs and other core indicators. For example, MINNUO’s PSA nitrogen generator provides highly efficient gas separation technology suitable for a wide range of industrial applications, while Air Products and Parker have stronger technological advantages in high-purity nitrogen production.
Cost-benefit analysis: When choosing a nitrogen generator, in addition to considering the initial investment in the equipment, attention should be paid to its long-term maintenance and operating costs. For example, the energy efficiency ratio and maintenance intervals of the equipment directly affect the total cost of ownership.
Solution:
Enterprises should select cost-effective nitrogen generators by comparing different brands of equipment and combining them with specific application requirements.
2. Customized design and selection
The selection of a nitrogen generator is not just about choosing a standard model, but also about customizing the design to meet specific operational needs. These needs may include flow rate, nitrogen purity, working environment conditions, etc.
Customized for specific needs: Different industries have different needs for nitrogen, such as high flow rates and high purity, and customized designs can ensure equipment optimization. For example, the oil and gas industry may require higher purity nitrogen, while the electronics industry requires a low-pollution gas supply. Customized designs can be optimized for production needs, such as adding multi-stage filters, gas recovery systems, etc.
High-flow, large-scale production needs: For large-scale production enterprises, they need to choose nitrogen generators suitable for high flow rates, and design the system according to the production cycle, factory layout and other factors. Large-scale production requires higher stability and continuous operation ability of the equipment, and the customized solution can provide more accurate gas output and avoid system overload.
Solution:
According to the specific needs of the enterprise’s production process (e.g. gas flow, working environment, temperature control, etc.), choose a customizable design of nitrogen generator to ensure its long-term stable operation and meet the gas supply requirements of different production processes.
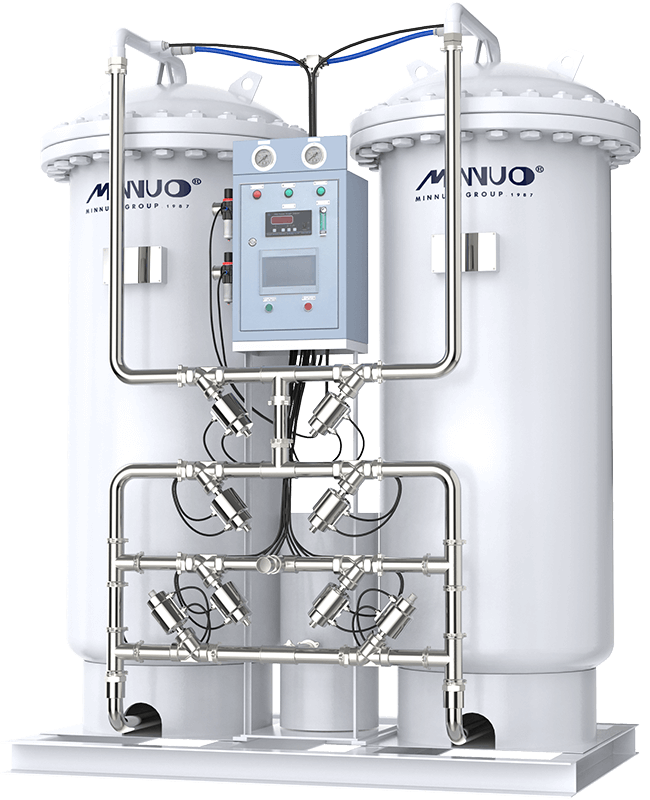
Conclusion
Purity and flow rate play a crucial role in the selection of nitrogen generators. Reasonable calculation of purity and flow rate not only ensures that the equipment meets the requirements of practical applications, but also maximizes the operational efficiency and economy of the system. By scientifically calculating and selecting the appropriate nitrogen generator specifications, companies can ensure the stability and reliability of the nitrogen supply, thus promoting the smooth running of the production process, reducing operating costs and improving overall production efficiency.
In order to better adapt to the needs of the industry, MINNUO Oxygen & Nitrogen provides efficient and stable nitrogen generator solutions, whether it is in the production of high purity nitrogen or under the demand of large flow rate, we can provide customized designs and technical support for all kinds of industries.MINNUO not only pays attention to the optimization of the performance of the equipment, but also provides comprehensive after-sales service for the customers, which can ensure the long-term and stable operation of the equipment and meet the gas demand in the development of the industry.