In modern cable manufacturing, the annealing and cooling processes of copper conductors require extremely stable atmospheres. Insufficient nitrogen purity or interrupted supply can directly cause oxidation, performance degradation, or even batch rejection. Therefore, this article comprehensively analyzes the usage precautions of PSA nitrogen generators in cable production, focusing on PSA nitrogen technology principles, gas standards for cable annealing processes, system operation control points, and usage considerations.
In cable production, PSA nitrogen generators are mainly used in copper conductor annealing, cooling, and packaging stages to provide high-purity nitrogen that prevents oxidation and ensures stable product performance. To guarantee effective use, attention must be paid to key parameters such as nitrogen purity, flow rate, and pressure; appropriate system capacity selection; regular maintenance of filters and pipelines; avoidance of frequent start-stop cycles; and ensuring coordinated control between the nitrogen generation system and the annealing process.
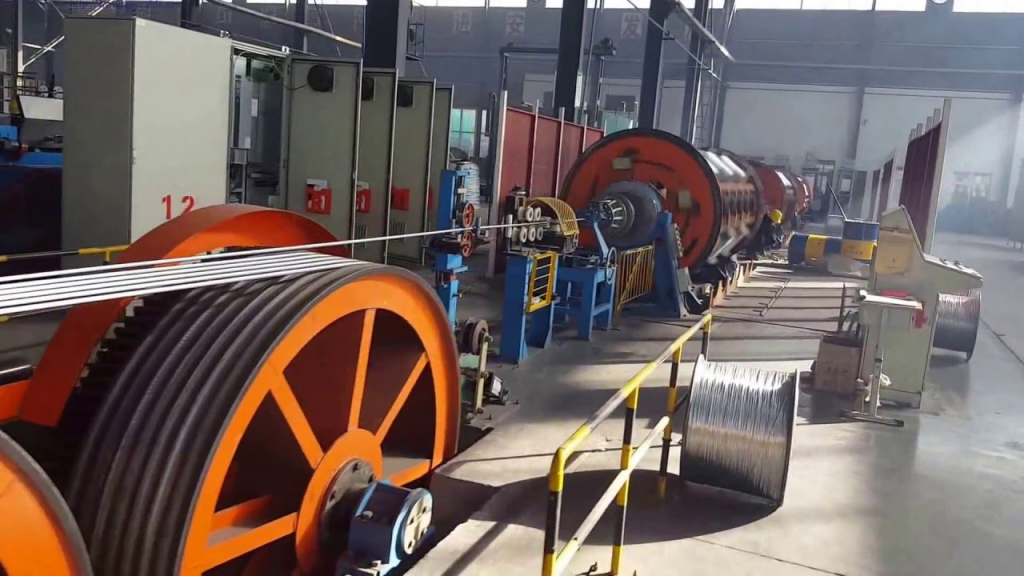
1. Technical Principles of PSA Nitrogen Generation Systems
1.1 Modular Gas Separation Mechanism
PSA (Pressure Swing Adsorption) systems operate on the selective adsorption principle based on the kinetic diameter of carbon molecular sieves (CMS). At an adsorption pressure of 0.6–1.0 MPa, continuous nitrogen supply is achieved by alternating dual towers in cycles. Key technical parameters include:
- Adsorption cycle: 45–240 seconds (dynamically adjusted according to purity requirements)
- Desorption pressure: Gradient control from -70 kPa to atmospheric pressure
- Carbon molecular sieve lifespan: ≥8 years (compliant with ISO 8573-1:2010 particulate control standards)
1.2 Gas Quality Assurance System
A three-stage filtration configuration is adopted in the pretreatment unit (see Table 1) to meet cable conductor surface cleanliness requirements:
Filtration Stage | Technical Specification | Treatment Target |
Primary Filter | 3 μm stainless steel sintered filter | Oil mist ≤0.01 ppm |
Precision Filter | 0.01 μm ultra-fine glass fiber | Particulates ≤ Class 1 |
Activated Carbon Tower | ASTM D3860 standard activated carbon | VOC ≤0.1 mg/m³ |
Basic Process Flow:
- Air compression system provides feed gas;
- Pretreatment system removes oil, water, dust, and impurities;
- Two adsorption towers operate alternately for adsorption-desorption cycles;
- Stable gas output is ensured through an online nitrogen purity monitoring system;
- Nitrogen enters a downstream buffer tank for end-use supply.
This system enables rapid gas production within 15–30 minutes, supports continuous 24-hour operation, and features easy operation, unattended running, low energy consumption, and low operating costs, making it ideal for long-term industrial gas use.
2. Gas Control Standards in Cable Annealing Processes
2.1 Dynamic Nitrogen Protection Model
According to annealing furnace types (pit-type / horizontal / continuous), differentiated airflow control models are established:
- Open annealing furnace: flow velocity ≥12 m³/h·㎡ (furnace cross-sectional area)
- Closed nitrogen circulation system: oxygen concentration gradient control <50 ppm (inlet) to 5 ppm (outlet)
- Gas replacement rate in cooling zone: ≥8 times/hour (per NFPA 86 thermal equipment standard)
2.2 Key Quality Indicator Comparison
Conductor Type | Nitrogen Purity Requirement | Dew Point Temperature | Allowed Oxygen Increment |
Ultra-fine copper wire (Φ0.05 mm) | ≥99.9995% | ≤ -70°C | ≤3 ppm / cycle |
Medium-voltage power cable | ≥99.99% | ≤ -40°C | ≤15 ppm / cycle |
Special alloy conductor | ≥99.999% | ≤ -60°C | ≤5 ppm / cycle |
3. System Operation Risk Control Matrix
3.1 Equipment Failure Early Warning Mechanism
A monitoring system based on FMEDA (Failure Modes, Effects, and Diagnostic Analysis) is established:
- Solenoid valve response time monitoring: <50 ms (per ASTM F1375 standard)
- Molecular sieve saturation alert: differential pressure sensor accuracy ±0.25% FS
- Emergency backup system: UPS power + atmospheric pressure storage tank (providing 30 minutes of emergency gas supply)
3.2 Key Process Control Points
- Dynamic purity compensation algorithm: Real-time adsorption cycle adjustment via PID controller to counteract inlet pressure fluctuations (±5%)
- Redundancy design: Critical solenoid valve groups adopt 1+1 hot standby configuration with switching time <100 ms
- Pipeline passivation: Stainless steel pipelines electrolytically polished inside (Ra ≤0.8 μm), helium leak rate <1×10⁻⁹ Pa·m³/s
4. Full Lifecycle Management Standards
4.1 Preventive Maintenance Plan
Maintenance Item | Interval | Technical Standard |
Molecular sieve activation regeneration | 8000 h | 250°C nitrogen purge, moisture ≤300 mg/kg |
Diaphragm valve seal testing | 2000 h | Leakage rate <0.1% bubble/min (ASME B16.34) |
Online oxygen analyzer calibration | 720 h | NIST traceable standard gas calibration |
4.2 Energy Efficiency Optimization Strategies
- Use of VSD (Variable Speed Drive) air compressors, saving 23%–35% energy compared to traditional units
- Waste heat recovery system: using 55–65°C exhaust heat for pretreatment unit regeneration
- Intelligent load regulation: integrated via OPC UA protocol with MES system for gas consumption predictive control
5. Core Applications of PSA Nitrogen Generators in Cable Production
5.1 Copper Wire Annealing Protection
Annealing relieves internal stress via heating. High-purity nitrogen is injected into the annealing furnace to prevent reaction with atmospheric oxygen at high temperatures, ensuring a bright surface and preserved conductivity.
5.2 Oxygen Isolation in Cooling Zones
Continuous nitrogen injection is required in the cooling area to avoid re-oxidation of inadequately cooled copper wires. In tandem annealing equipment, nitrogen pipeline layout critically affects product quality.
5.3 Finished Cable Packaging Protection
For some high-end cables, nitrogen is injected during packaging or storage to isolate moisture and oxygen, extending service life.
5.4 Nitrogen as a Key Quality Control Parameter
Nitrogen purity, flow rate, and pressure stability directly influence copper wire performance. Visualized management and precise control via PSA nitrogen systems are essential quality assurance measures.
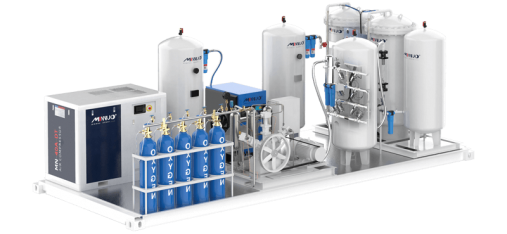
6. Professional Precautions for Using PSA Nitrogen Generators
6.1 Purity and Oxygen Monitoring
Regularly test nitrogen purity and residual oxygen content (recommended online oxygen monitoring with real-time alarms, maintaining purity ≤10 ppm).
6.2 System Capacity Matching
Select system capacity based on actual gas demand (consider annealing furnaces, working hours, and flow requirements to avoid over/undersizing).
6.3 Filter and Pipeline Maintenance
Regularly service filters (precision filters, activated carbon adsorbers) and pipelines to prevent impurity contamination. For high-end cables, add sterilizing filters at system outlets.
6.4 Flow Velocity and Pressure Control
Optimize outlet location and size (recommended pressure: 0.1–0.3 MPa). Use adjustable valves and pressure gauges; consider nitrogen recirculation design.
6.5 Avoid Frequent Start-Stop Cycles
Frequent cycling risks valve failure. Implement annual maintenance plans and stock critical spare parts.
6.6 Alarm and Control Systems
Install pressure/flow alarm systems (e.g., trigger alarms at pressure <0.05 MPa). Integrate with PLC for centralized and remote monitoring.
6.7 Gas Outlet Layout
Separate outlets for annealing and cooling zones in tandem equipment. Use CFD simulation to optimize flow field and prevent stagnation/backflow.
6.8 Interlinked Control with Annealing Equipment
Ensure nitrogen supply precedes equipment startup and shuts off automatically upon shutdown for safety and energy savings.
6.9 Safety Training and Compliance
Train operators on equipment operation, alarm handling, and emergency procedures in line with National Special Equipment Safety Law and pressure vessel codes.
7. MINNUO PSA Nitrogen Generator Advantages
As a gas equipment R&D and manufacturing leader, MINNUO offers PSA nitrogen systems with:
- Modular design for easy installation and expansion;
- Remote control and operation data logging;
- Efficient carbon molecular sieves and intelligent control valves (extended lifespan);
- Multi-stage filtration for high gas cleanliness;
- Professional selection, commissioning, and overseas remote maintenance support.
8. Conclusion
The engineering application of PSA nitrogen systems in cable manufacturing must adhere to the three-dimensional principles of “process-matched design, risk prevention, and effective management.” For tailored solutions for your annealing production line, contact MINNUO’s technical team for one-on-one guidance and customized designs to enhance cable quality and production efficiency.