With the arrival of summer, high-temperature environments pose significant challenges to the PSA nitrogen generators’ operation efficiency, nitrogen purity, and core component lifespan. Based on actual user conditions and the latest industry research, this article will analyze in depth the causes, impacts, and systematic solutions for high temperatures, helping users achieve stable equipment operation while reducing costs and improving efficiency.
The impact of high-temperature environments on PSA nitrogen generators is mainly reflected in reduced heat dissipation efficiency, uncontrolled compressed air temperature, design flaws in key components, and improper operating parameters. Solutions include upgrading the heat dissipation and cooling systems, dynamically optimizing operational parameters, designing key components for high-temperature resistance, implementing intelligent monitoring and emergency response mechanisms, and adopting preventive maintenance and spare parts management.
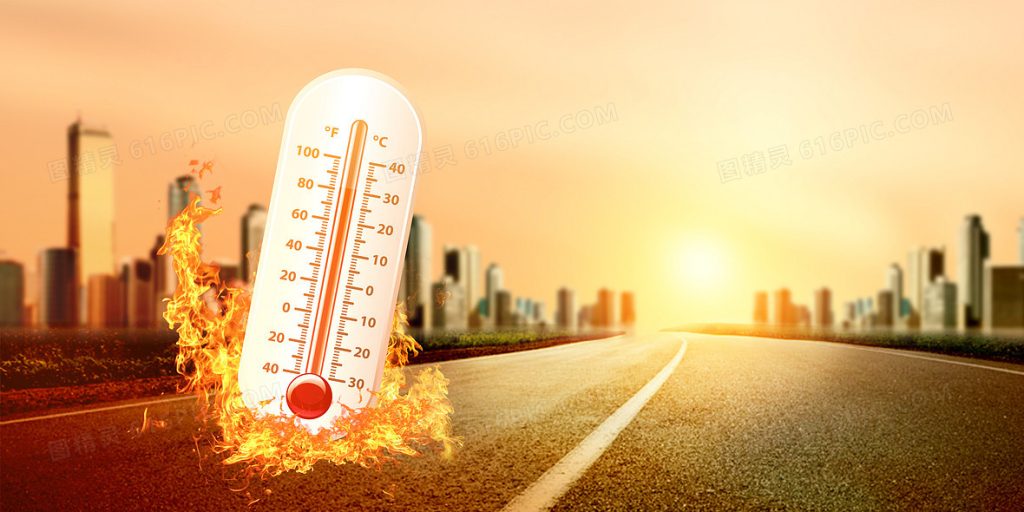
I. Multidimensional Analysis of High-Temperature Causes
1.1 Environmental Temperature and Imbalance in Heat Dissipation Efficiency
When the ambient temperature exceeds 35°C during summer, the heat dissipation efficiency of the equipment decreases significantly. Studies show that for every 5°C increase in ambient temperature, the failure rate of the nitrogen generator increases, and the risk of nitrogen purity fluctuations rises. In open equipment rooms without forced ventilation (airflow speed ≥ 2 m/s), the adsorption capacity of the molecular sieve in the adsorption tower will degrade due to heat accumulation, resulting in reduced nitrogen production efficiency.
1.2 Uncontrolled Compressed Air Temperature
If the compressed air at the compressor outlet is not effectively cooled (e.g., if a rear water-cooled unit is not installed), high-temperature gas entering the adsorption tower will intensify the heat-absorbing reaction of the molecular sieve. Experimental data shows that as compressed air temperature increases, the adsorption efficiency of the molecular sieve decreases, while the bed temperature rises cumulatively, accelerating the risk of molecular sieve powdering.
1.3 Design and Maintenance Defects in Key Components
- Improper Compression Method: Spring or cylinder compression structures are prone to loosening during transportation or in vibrating environments, causing molecular sieve settlement, powdering, and further performance degradation in high-temperature conditions. While head compression methods are inconvenient to maintain, their one-time compression formation can effectively address the vibration issue in mobile equipment, reducing powdering rates.
- Electromagnetic Valve Overheating: When the ambient temperature exceeds 60°C, the electromagnetic valve coil is prone to overheating and failure, leading to stuck valve cores or aging and expansion of seals, causing abnormal adsorption cycle switching and pressure fluctuations.
1.4 Static Operating Parameters and Lack of Dynamic Adjustment
In high temperatures, without shortening the adsorption cycle (e.g., changing from 8 seconds to 6 seconds), the molecular sieve continues to absorb heat, resulting in incomplete regeneration; insufficient backflush air volume further exacerbates heat accumulation. Additionally, if the compressor outlet pressure is not dynamically adjusted, the compression heat generated increases, forming a vicious cycle.
1.5 Lubrication and Molecular Sieve Aging Issues
Ordinary lubricants lose viscosity and degrade in performance under high temperatures, increasing mechanical wear; if the molecular sieve is not periodically regenerated at high temperatures (e.g., every quarter at 230°C), its adsorption capacity decreases at a fixed annual rate, leading to equipment overload.
II. Systematic Solutions for High-Temperature Environments
2.1 Heat Dissipation and Cooling System Upgrade
- Forced Ventilation Retrofit: Install industrial-grade exhaust fans (air exchange ≥ 3000m³/h) with airflow speeds ≥ 2 m/s, and add dust filters to avoid reduced heat dissipation efficiency.
- Water Cooling System Optimization:
- Add a water cooling unit at the rear of the compressor to stabilize compressed air temperature below 40°C, improving adsorption efficiency.
- Retrofit external circulating water cooling for the adsorption tower, combined with PLC temperature control algorithms, to narrow the temperature fluctuation range and maintain nitrogen purity within a certain range.
2.2 Dynamic Optimization of Operating Parameters
- Intelligent Adjustment of Adsorption Cycle: Based on ambient temperature sensor data, automatically adjust adsorption/regeneration times (e.g., 8 seconds → 6 seconds) to reduce heat absorption duration, while increasing backflush air volume to ensure thorough regeneration.
- Pressure and Flow Control: Use variable frequency technology to lower the compressor outlet pressure, reducing compression heat generation. Add a gas buffer tank (volume ≥ 30% of the equipment’s hourly gas output) to balance peak and valley gas demand, preventing temperature fluctuations caused by frequent startups and shutdowns.
2.3 High-Temperature Design and Maintenance for Key Components
- Molecular Sieve Compression Technology: Use head compression and snowstorm-style filling processes to improve the filling density of the molecular sieve, preventing loosening during transportation and enhancing service life.
- Electromagnetic Valve Protection Upgrade: Use fluororubber seals (temperature range -20°C to 200°C), add ≥ 50CFM cooling fans, and install magnetic filters to reduce valve core sticking rates.
- Lubrication System Optimization: Replace with ISO VG68-grade high-temperature synthetic lubricants, improving high-temperature viscosity retention, shortening oil change intervals, and synchronously replacing high-precision oil filters.
2.4 Intelligent Monitoring and Emergency Response Mechanisms
- Multi-Parameter Real-Time Monitoring: Integrate temperature sensors, oxygen analyzers, and PLC control systems to monitor adsorption tower temperature (with threshold settings), nitrogen purity (fluctuation range), and pressure stability, automatically reducing load to 60% operation when alarms are triggered.
- Emergency Cooling Plan:
- Activate backup nitrogen generator units, switching the main equipment to low-load mode.
- Temporarily deploy mist cooling systems (avoiding electrical components) and use thermal imaging to locate overheating sources (e.g., electromagnetic valves, local areas in the adsorption tower).
2.5 Preventive Maintenance and Spare Parts Management
- Molecular Sieve Activation Plan: Perform high-temperature regeneration treatment at 230°C each quarter, increasing the filling amount to compensate for high-temperature capacity loss. Test the molecular sieve powdering rate every 2 years (standard).
- Spare Parts Reserve Strategy: Reserve high-temperature-certified spare parts in advance, including oil filters (replacement cycle 300 hours), temperature sensors (precision), and molecular sieves (stock in proportion to annual consumption), extending equipment service life.
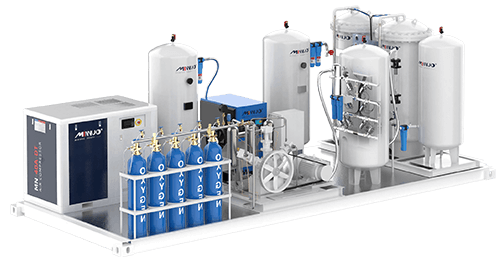
III. MINNUO’s Technological Innovations and Scenario-Based Applications
3.1 Modular Heat Dissipation Design
MINNUO’s patented technology modularizes the heat dissipation system, supporting quick assembly and customized upgrades:
- External water-cooled jackets for the adsorption tower to improve heat exchange efficiency.
- Independent heat dissipation channels for electromagnetic valves, equipped with temperature-controlled fans (50-100CFM adjustable), ensuring component temperature ≤ 55°C.
3.2 Intelligent Temperature Control Algorithm
Based on machine learning models, the temperature change trend is dynamically predicted, and operating parameters are adjusted in advance:
- When ambient temperature ≥ 38°C, automatically shorten the adsorption cycle and increase the cooling water flow rate.
- Optimize molecular sieve regeneration temperature curves based on historical data, reducing energy consumption.
3.3 Scenario-Based Solutions
- Mobile Nitrogen Generator: Uses head compression + container shockproof design, improving molecular sieve vibration resistance, suitable for oil extraction, emergency rescue, and other scenarios.
- Semiconductor Industry: Equipped with 0.01μm precision filters and oil-free compressors, nitrogen purity ≥ 99.9995%, dew point ≤ -70°C, meeting the high cleanliness requirements of wafer manufacturing.
IV. Industry Data and User Benefit Analysis
According to industry reports, high-temperature optimization solutions can bring significant benefits to users:
- Energy Consumption Reduction: Dynamic parameter adjustment + water cooling system upgrade results in a comprehensive decrease in energy consumption.
- Maintenance Cost Savings: Preventive maintenance strategies reduce unplanned downtime, lowering annual maintenance costs.
- Service Life Extension: The molecular sieve and key components’ service life extension shortens the equipment’s return on investment period.
V. Conclusion
The challenges posed by high-temperature environments to PSA nitrogen generators must be addressed through technological iterations and systematic management. MINNUO, with its focus on efficient heat dissipation, intelligent regulation, and long-term protection, provides a full-chain solution from hardware upgrades to digital operation and maintenance. Contact us now to obtain a customized high-temperature protection plan and equipment health diagnosis service, ensuring stable nitrogen production even in the scorching summer heat!