As the demand for high purity oxygen in the medical, industrial and environmental protection fields continues to grow, the traditional oxygen cylinder and liquid oxygen distribution model can no longer meet the demand for efficient, safe and energy-saving on-site oxygen supply. This trend has led to the continuous evolution of oxygen generators equipment technology, and the variable pressure adsorption oxygen generation technology has gradually become the mainstream. Among all pressure swing adsorption solutions, PSA (Pressure Swing Adsorption) and VPSA (Vacuum Pressure Swing Adsorption) are the two most representative processes.
Although they are both adsorption separation routes, there are significant differences in working pressure, energy efficiency characteristics, core component configurations and applicable working conditions. For example, PSA is commonly used in small and medium-sized oxygen production facilities, emphasizing flexibility and speed of deployment, while VPSA is more suitable for large-scale industrial continuous oxygen supply scenarios, which is characterized by low energy consumption.
In this article, we will analyze the working principle, energy consumption, oxygen purity, typical application scenarios and investment cost structure of these two systems, and combine them with industry cases and technical selection suggestions to help users make a scientific judgment based on actual needs: whether to choose PSA, which has a fast response and a small footprint, or VPSA, which is energy-efficient and suitable for batch operation If you are planning for the upgrade of your oxygen system or project procurement configuration, please continue to read below. If you are planning an oxygen generation system upgrade or project procurement configuration, please read on for a more comprehensive reference.
1. Basic Principles
PSA systems compress everything in the air, which is about 78% nitrogen and 21% oxygen and 1% Argon. VPSA systems only compress oxygen, hence reducing the amount of energy used for compression.
1.1 PSA (Pressure Swing Adsorption)
How it works:
PSA system separates oxygen and nitrogen by “pressurized adsorption + depressurized resolution”. In a pressurized adsorption tower, the nitrogen in the air is preferentially adsorbed by molecular sieve, while the oxygen is output through the tower; then the nitrogen is desorbed and the molecular sieve is regenerated through depressurization (often down to atmospheric pressure or slightly negative pressure), and the next cycle begins.
Key features:
Conventional air compressor is used for gas supply, and the working pressure range is generally 0.6~0.8 MPa
Does not depend on vacuum system, compact structure, suitable for small and medium scale continuous oxygen supply
Continuous gas supply can be realized by double tower switching structure
Applicable scenarios:
Continuous gas supply for 93%~95% oxygen purity is required in hospital ICU, operating room, industrial ozone preparation, glass cutting, food oxygen-enriched packaging and other scenarios.
✅ Practical Tips: PSA is more suitable for users with “medium flow rate + medium-high purity + flexible deployment”.
1.2 VPSA (Vacuum Pressure Swing Adsorption)
Working Mode:
VPSA technology continues the logic of PSA adsorption and desorption, but introduces a vacuum pump to assist the resolution in the desorption process, which further reduces the pressure to -0.05 ~ -0.09 MPa, so as to realize a more complete regeneration of adsorbent and improve the oxygen production and energy-saving efficiency. Oxygen production and energy saving efficiency.
Key features:
Adsorption tower operating pressure is lower (close to atmospheric pressure), significantly reducing the energy consumption of air pressure.
The simple pressure reduction is replaced by vacuum pumping in the resolving stage, which has better energy consumption.
Suitable for large flow rate oxygen production system (generally 500Nm³/h for a single set of system to start with).
Higher requirements for the volume of adsorption tower and the configuration of the vacuum system, and larger equipment size.
Applicable scenarios:
Large-scale iron and steel metallurgy factories, desulfurization and denitrification of power plants, regional oxygen supply centers, centralized oxygen supply stations for medical treatment, and other daily gas supply stations, etc. Centralized oxygen supply station, etc. Daily gas supply ≥1000Nm³, sensitive to the operating costs of the scene.
✅ Practical tip: VPSA is more suitable for “high flow rate + operation continuity + energy-saving projects”, but the initial investment is relatively high.
Technical specifications | PSA | VPSA |
Adsorption pressure | Medium pressure (0.6~0.8 MPa) | Near normal pressure (0.05~0.1MPa) |
Resolution | Reduced pressure to atmospheric | Vacuum pump pumping resolution |
Energy performance | General | Lower, energy saving 10~25% |
Equipment composition | Compact, suitable for modularity | The base needs to be large, need to configure the vacuum system |
Start-up time | Fast, several minutes | Relatively long |
Typical output | 10~500 Nm³/h | ≥500 Nm³/h |
Recommended users | Medical systems, medium-sized plants | Large metallurgy, centralized gas supply station, environmental protection system, etc. |
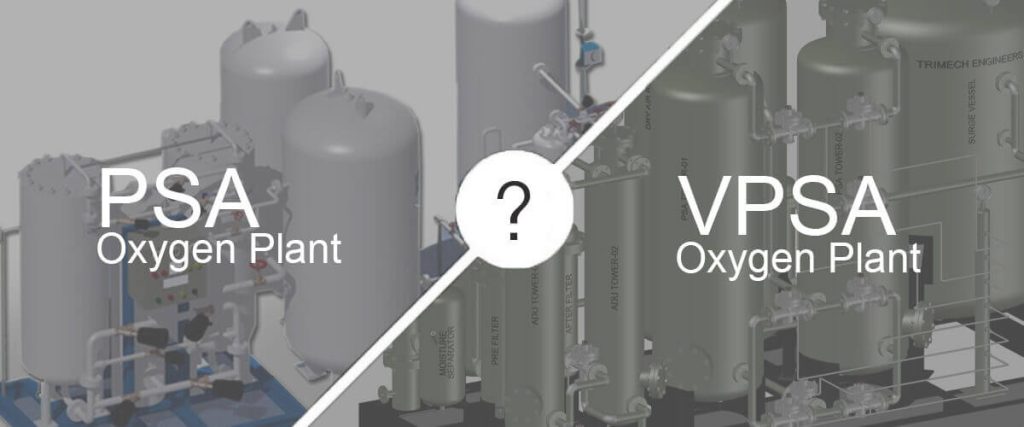
2.Application Scenarios
Although the principles of PSA and VPSA are similar, there are significant differences in application positioning and system configuration. The following is an in-depth analysis of the suitability of the two types of systems from the perspective of “typical use scenarios”:
2.1 Typical Applications of PSA Systems
PSA oxygen equipment is widely used in small and medium-sized places with its advantages of compact structure, rapid startup, flexible deployment, etc. It is especially suitable for the following needs:
Medical Scenarios:
Hospitals, ICUs, intensive care units, general wards, community health centers, emergency vehicle oxygen systems, mobile/field clinic stations with short deployment cycles. Medical Scenarios: Hospital ICU intensive care unit, general ward
Community health center, emergency vehicle oxygen supply system
Mobile/field clinic station with short deployment cycle
Small-scale industrial/laboratory oxygen generation:
Ozone generator for oxygen distribution (e.g., water treatment in water plant/swimming pool)
Laboratory analytical reaction gas, suitable for 93%~95% stable oxygen supply
Emergency Oxygen Supply System for High Plains or Remote Areas:
Combination of Portable + Oxygen Tank System to meet the >3000m elevation Oxygen supplementation for emergency command tent and field construction area
✅ Summary of features:
Suitable for small and medium-sized systems with daily oxygen production <1000Nm³ from a single set of equipment;
Advantages include compact structure, flexible modules, easy operation and maintenance, and high cost-effectiveness.
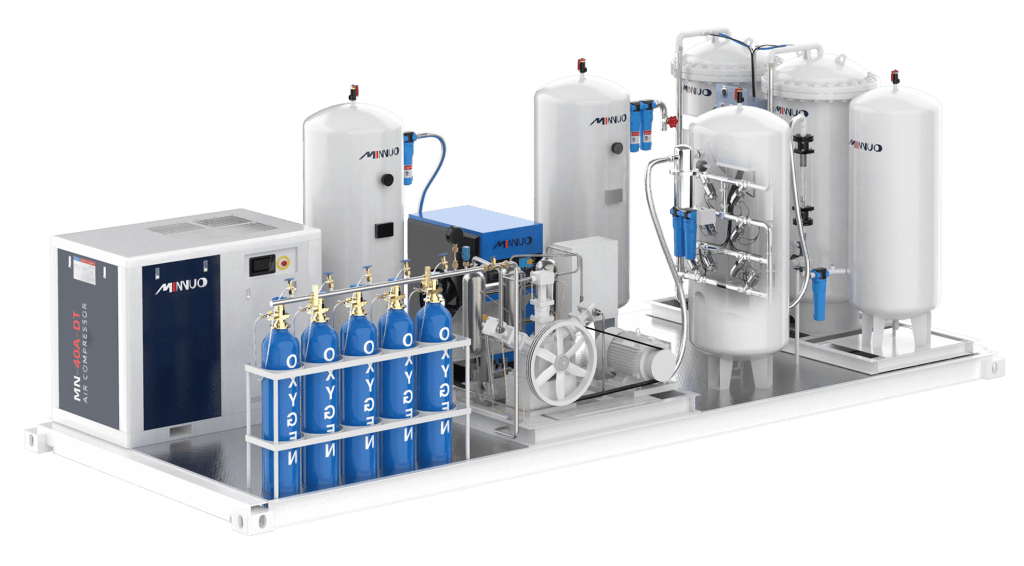
2.2 Typical Applications of VPSA System
VPSA system is more suitable for large-scale centralized oxygen supply scenarios with high throughput, high requirements on energy efficiency and operation cost control. Mainly include:
Large-scale iron and steel/nonferrous smelting industry:
Ironmaking blast combustion, converter oxygen-enriched desulfurization system
Blast furnace oxygen injection to raise the temperature of the furnace gas to strengthen combustion reaction
Environmental protection and power plants:
Thermal power plant desulfurization and denitrification reaction device (SDS), ozone oxidation reaction
Municipal wastewater/waste incineration plant ozone oxygen supply system
Medical centralized oxygen supply station (high-flow gas supply type):
City regional medical oxygen supply center
Tertiary hospitals daily oxygen > 1500Nm³ application scenarios. 1500Nm³ Application Scenario
✅ Summary of features:
Suitable for large-scale scenarios with daily gas production ≥ 1000Nm³ and the pursuit of low energy consumption and high stability;
has lower energy consumption per unit of oxygen production, and is more suitable for long-cycle heavy-duty operation.
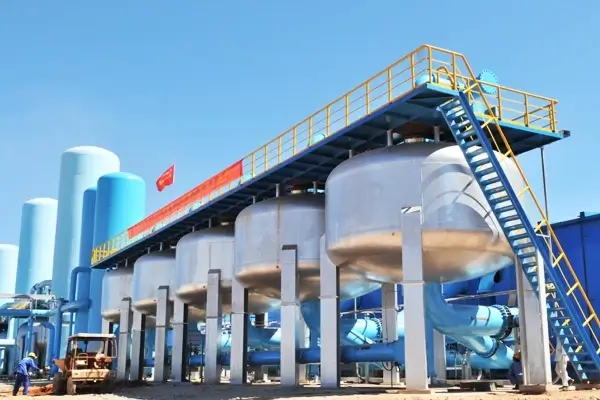
Practical selection suggestions:
Daily gas supply (Nm³/h) | Recommended Oxygen Generation Methods | Reasons |
≤ 1000 Nm³/h | Preferred PSA | Low cost, quick to install, compact and suitable for flexible deployment |
≥ 1000 Nm³/h | Preferred VPSA | Lower energy consumption per unit, more suitable for large, long-term operation sites |
3. Investment and O&M Cost Comparison
Comparison of investment and operation cost
In the selection process of oxygen generation system, “initial investment vs. long-term operation cost” is one of the core elements that enterprises must weigh. PSA and VPSA technologies have significant differences in terms of procurement budget, operation energy consumption and maintenance frequency due to the differences in the system structure and working mode:
3.1 PSA: compact structure, suitable for small and medium-sized projects
Equipment features:
Modular small system, simple structure, the core consists of a double-tower adsorption system + molecular sieve, the control system is PLC-based, no need for large vacuum pumps or complex pipelines, and a short construction cycle.
Initial investment:
✅ Obvious advantages: low overall system investment (for <1000 Nm³/h), low civil construction requirements, short installation and commissioning cycle, especially suitable for medical, laboratory, small industrial customers.
Maintenance cost:
⛔ Relatively frequent: core consumables such as molecular sieve life of about 8000 ~ 12000 hours, the replacement cycle of about 2 ~ 3 years; filter element, air compressor oil separator core, etc. need to be replaced regularly.
Unit energy consumption:
average power consumption is high (about 0.6~0.8 kWh per Nm³ oxygen), but it still has good economy in small and medium flow demand scenarios.
✅ Suitable scenarios: small hospitals, clinics, ozone generation, small glass furnaces, emergency projects, etc., emphasizing fast deployment, low up-front investment and flexible use.
3.2 VPSA: high investment but excellent long-term benefits
Equipment features:
system is huge, configured with vacuum pump, variable frequency blower, centralized exhaust network, operating pressure close to atmospheric pressure, energy efficiency performance is better, suitable for more than 1,000Nm³/h of oxygen demand.
Initial investment:
⛔ High budget requirements: the investment of a single set of system is usually 1.5 to 2 times of PSA, and it has high requirements on plant, power capacity, ventilation, exhaust pipe network and other civil construction.
Running cost:
✅ Long-term more energy-saving: under high-flow operation, the energy consumption is 20%-30% lower than PSA, and each Nm³ oxygen consumes about 0.4-0.6 kWh; it is suitable for industrial mainline projects running for 24h.
Maintenance cost:
Initial parts are more expensive, but with long service life, high system stability, longer replacement cycle (e.g. high grade LiX molecular sieve can last up to 5~7 years), and low frequency of manual inspection.
✅ Suitable scenarios: steel mills, blast furnaces, power plant denitrification, oversized hospital central oxygen supply stations, urban centralized gas supply systems.
Practical Advice:
Comparison Dimensions | PSA system | VPSA system |
Initial investment budget | Lower ($30,000 to $300,000) | Higher ($200,000 to $800,000) |
Energy consumption per unit of operation | 0.6 to 0.8 kWh/Nm³ | 0.4 to 0.6 kWh/Nm³ (suitable for ≥1000Nm³/d) |
Core component life and replacement frequency | Molecular sieves 2 to 3 years, frequent consumable replacements | Molecular sieve 4 to 6 years for a more stable system |
Installation cycle | Fast, 1 to 2 weeks delivery | Longer, usually 1 to 2 months |
O&M labor cost | High (frequent overhaul) | Lower (centrally controlled, automatically monitored) |
❓ Frequently Asked Questions (FAQ)
Q1: What is the difference between the core working principle of PSA and VPSA?
A:PSA (Variable Pressure Adsorption): Adsorption at atmospheric pressure + desorption at reduced pressure, the air source is usually from a stable air compressor, suitable for small and medium flow rate continuous oxygen supply.
VPSA (Vacuum Pressure Pressure Adsorption): low pressure adsorption + vacuum pump assisted desorption, lower energy consumption, suitable for large-scale centralized oxygen supply.
In short, PSA is “pressurized adsorption” and VPSA is “vacuum desorption”. The different pressure ranges of adsorption/desorption between the two determine the differences in system architecture and energy efficiency performance.
Q2: My project uses less than 1000Nm³/h of oxygen per day, which system should I choose?
A: If the daily oxygen supply is <1000Nm³/h, it is recommended to prioritize PSA system because of its simple structure, short construction period and low initial investment, which is suitable for small and medium-sized hospitals, clinics, food factories, welding stations and other daily oxygen consumption scenarios.
Q3: How much higher is the energy efficiency of VPSA than PSA? What is the difference in actual operating cost?
A: The energy consumption per unit of oxygen production of VPSA system is 20%~30% lower than PSA. This is mainly due to its close to atmospheric pressure adsorption + vacuum desorption mode of operation. Although the initial investment of VPSA is higher, it is more energy-efficient and stable in continuous operation scenarios with high flow rates, and the unit cost of oxygen production is lower in the long run.
Q4: Which is easier to maintain, PSA or VPSA? What consumables need to be replaced on a daily basis?
A:PSA: the system structure is compact, the molecular sieve and air compressor cartridge are replaced frequently, which is suitable for users to maintain on their own;
VPSA: the system is bigger, the accessories have a long life, it is recommended to have regular inspection by the professional operation and maintenance team;
✅ PSA is more suitable for customers with “local operation and maintenance ability”;
✅ VPSA is more suitable for customers with “high automation and less maintenance”; ✅ VPSA is more suitable for customers with “high automation and less maintenance”. ✅ PSA is more suitable for customers with “local operation and maintenance capability”; ✅ VPSA is more suitable for gas station projects with high degree of automation and less manual guarding.
Q5: Which system is more recommended for high plateau area or unstable power area?
A: PSA is recommended for plateau/power shortage/emergency deployment scenarios.
PSA system can be configured with plateau-type air compressor, UPS or diesel generator, which provides more deployment flexibility; while VPSA relies more on the power supply, voltage and vacuum pump exhaust system, and has a longer construction period.
Q6: Can MINNUO provide PSA/VPSA dual-route customized solutions?
A:Of course! MINNUO supports the following services:
Customized PSA/VPSA solutions from 5Nm³/h to 3000Nm³/h;
Multi-tower parallel expansion, SCADA/PLC linkage, CE/ISO13485 certifications, etc.;
Optimal system types and installation modes can be configured for different countries or scenarios (e.g., healthcare, industrial, urban gas supply).
If you have project parameters such as gas consumption, tariffs, operating hours, etc., please contact us for a ROI calculation and selection suggestion form.
Conclusion
PSA and VPSA are essentially different realizations of Adsorption technology. The former is known for its flexible deployment and low construction threshold for small to medium flow rates and rapid response to oxygen demand, while the latter is known for its high energy efficiency and continuous operation at high flow rates, making it the preferred solution for industrial-scale centralized oxygen supply systems. Which technology you choose depends on your daily gas consumption, site conditions, budget cycle and system integration needs.
As a professional gas equipment manufacturer, MINNUO provides PSA/VPSA integrated solutions covering 10Nm³/h to 3000Nm³/h, supporting multi-tower expansion, remote control and intelligent operation and maintenance, which are widely used in hospital gas stations, industrial welding, ozone reaction, municipal oxygen supply and other scenarios. If you are planning for oxygen generation system selection, welcome to visit https://minnuogas.com/ for exclusive configuration suggestions and technical support.