Liquid nitrogen is widely used across industries—ranging from food preservation to medical applications—yet its price remains volatile globally. While fluctuations are common, Brazil stands out with persistently high liquid nitrogen costs. This article examines the unique industrial, logistical, and structural factors behind this anomaly, aiming to provide a comprehensive understanding of Brazil’s liquid nitrogen supply chain.
At the heart of the issue lies a critical question: why is liquid nitrogen significantly more expensive in Brazil compared to other countries with similar industrial needs? The answer, as we’ll uncover, is not merely about production costs—it’s about infrastructure gaps, centralized supply chains, and limited local generation capabilities. Addressing these systemic weaknesses is key to reversing the cost imbalance.
By the end of this article, you’ll gain clarity not only on the “why” behind the pricing puzzle but also on practical solutions that industries and policymakers can adopt. Whether you’re a procurement officer, hospital administrator, or industrial investor, the insights shared here—including local production models supported by reliable partners like MINNUO—will help you envision a more resilient and cost-efficient future for Brazil’s nitrogen ecosystem.
1. Structural Challenges Behind Liquid Nitrogen Costs
Despite the fact that the manufacturing process of liquid nitrogen itself has matured globally, its price in Brazil remains high. This phenomenon is not due to a single factor, but rather to a combination of structural factors.
The industrial gas market is overly concentrated, with significant monopoly influence
The Brazilian industrial gas market is dominated by a very small number of large multinationals with highly concentrated market shares. Because of this, the pricing power of liquid nitrogen is basically in the hands of these headline companies, and there is a lack of effective competition mechanisms. What’s more, once a company experiences equipment maintenance, logistics disruption or raw material fluctuations, the impact can spread to the entire region, creating a vicious cycle of “sharp price fluctuations – collective price increases”.
Weak local production capacity, highly dependent on imported equipment and core technology
Although Brazil has a certain number of air separation equipment, but most of them are dependent on imports, the core components, cold box systems, control modules, etc. are mainly provided by European, American and Asian companies. Once the international market supply is tight or the exchange rate fluctuates drastically, the operating cost of local liquid nitrogen plants will climb rapidly. At the same time, domestic manufacturers lack the ability to manufacture cryogenic separation equipment on their own, which also limits the flexibility and responsiveness of capacity expansion.
Uneven distribution of liquid nitrogen production and regional supply imbalance
Most liquid nitrogen plants are concentrated in industrial areas along the southeast coast (e.g., São Paulo, Rio de Janeiro), while supply from vast inland agricultural areas, remote healthcare markets, and even the northern Amazon region is highly dependent on long-distance transportation across state lines. Liquid nitrogen is typically a low value-added, highly logistics-sensitive product that requires continuous cold chain security during transportation and is highly susceptible to road conditions, weather conditions, etc. Ultimately, transportation costs significantly raise the terminal selling price in remote areas.
Practical Impact and Thoughtful Suggestions
SMEs and organizations in remote areas are most susceptible to price fluctuations and transportation delays, and liquid nitrogen for medical use may even affect clinical operations due to logistics disruptions.
If they wish to escape from this passive situation, they should explore localized nitrogen production solutions, such as deploying a small-scale local liquid nitrogen generation system (Micro-LIN Plant) or introducing vehicle-mounted deep-cooling nitrogen production units, so as to alleviate their reliance on centralized plants and cold-chain logistics.
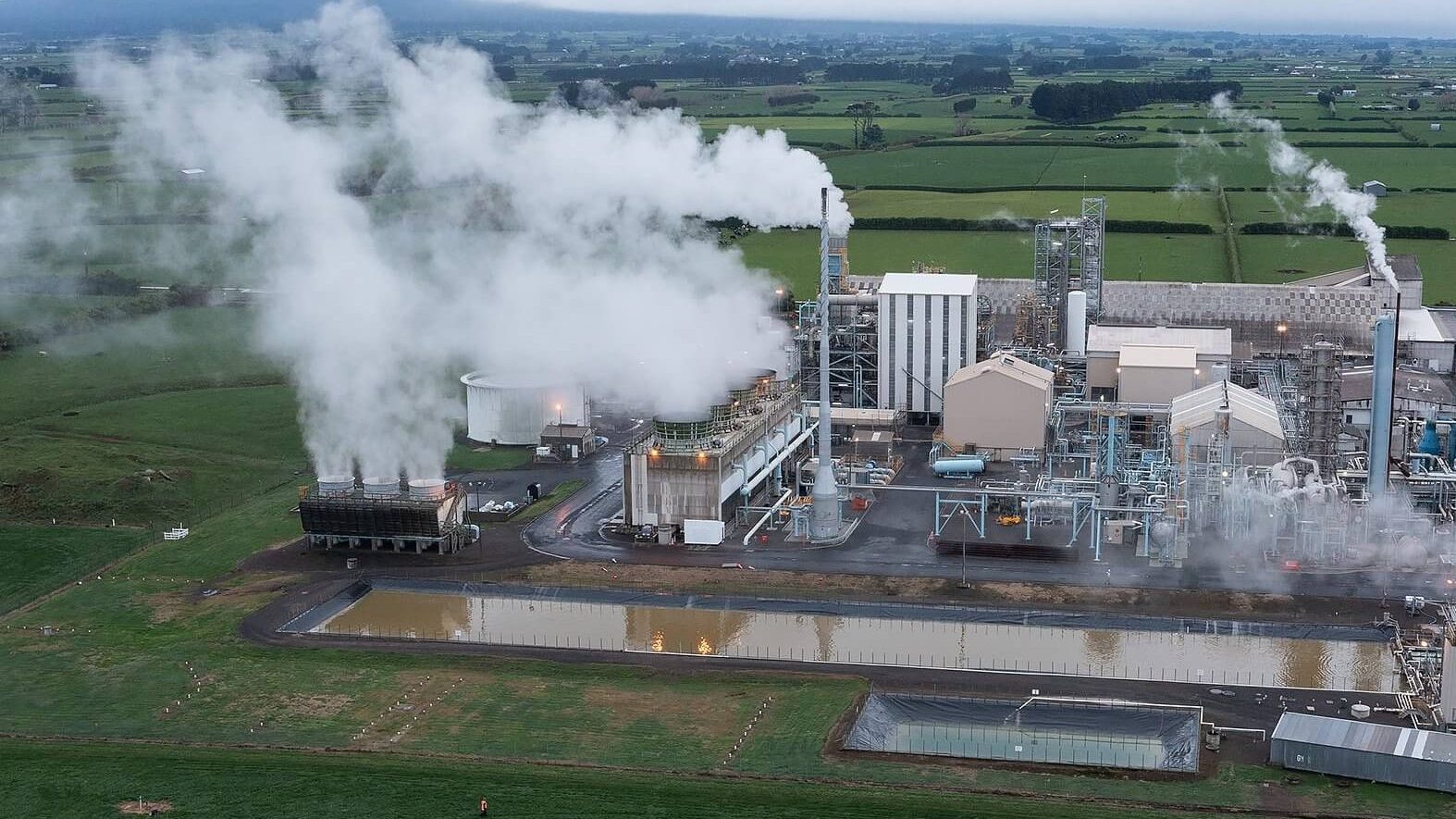
2. The Hidden Cost of Outsourcing: Risks of Relying on External Suppliers
Beyond the apparent price, relying on external liquid nitrogen suppliers hides a series of unseen but real costs. These “hidden costs” are often the root cause of persistently high prices.
Increased risk of supply chain instability
For countries with an uneven industrial base, such as Brazil, reliance on external suppliers can lead to disruptions in the supply of liquid nitrogen in the event of plant failures, extreme weather conditions, geopolitical instability, or strikes, with knock-on effects in downstream manufacturing, food, and healthcare sectors. Recovery time is long and costly, especially in the absence of a local emergency reserve system.
Weakened bargaining power and frequent price fluctuations
Purchasing companies are unable to dominate the pricing mechanism, and are in a passive position when faced with large gas suppliers, especially during periods of concentrated demand, when there are frequent price increases but no bargaining space. In addition, long-term agreements often have fixed supply quantities and binding terms, even if the market situation changes, it is difficult to adjust flexibly.
Untimely service response and long maintenance cycle
The problem of untimely service response is particularly prominent under the outsourcing model because of the high-frequency and timely requirements for the transportation and refilling of liquid nitrogen. For example, the long maintenance cycle of the supplier, inability to refill on time, and equipment failure that cannot be quickly repaired will directly affect the normal operation of the customer.
Rising inventory costs and cash flow pressure co-exist
In order to cope with unstable supply, many enterprises have to increase their inventory in advance, which undoubtedly increases the management costs of storage, transportation, liquid nitrogen evaporation and so on. At the same time, prepayments and uncertain supply cycles can also cause financial cash flow constraints.
Suggestion: Moderate “localization” is key
To reduce the risk of external dependence, companies are advised to assess the feasibility of deploying liquid nitrogen production units locally or leasing small nitrogen generators. For example, a simple nitrogen production unit using membrane separation + cooling technology can be used on demand according to actual production line needs, ensuring independent supply capacity in case of emergency.
In addition, reaching a spare parts cooperation mechanism with local equipment suppliers, building regional cold stations or sharing liquid nitrogen reserve centers can also help improve response speed and risk resistance.
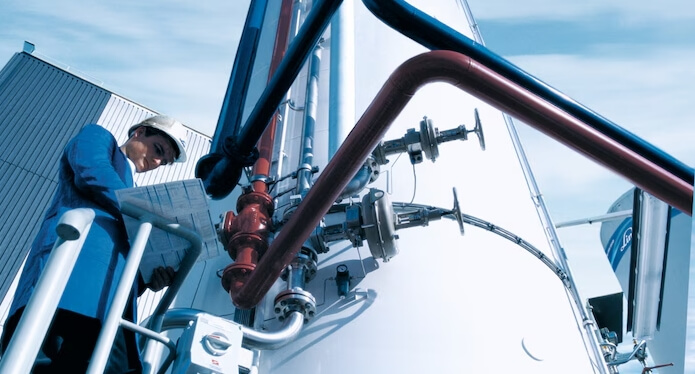
3. The Cryogenic Cold Chain Dilemma: Transportation and Distribution Challenges
The transportation of cryogenic products, such as liquid nitrogen, faces significant challenges in remote markets in Brazil and South America, especially in scenarios involving medical care, vaccines, and industrial oxygen production, where cryogenic requirements are stringent. The challenges are especially prominent in scenarios involving medical care, vaccines, and industrial oxygen production.
3.1 Weak Road Infrastructure and Restricted Transportation Radius
Many roads in remote areas are in disrepair and have potholes, which make it difficult for transportation vehicles to pass through, and the effective radius of liquid nitrogen transportation is greatly reduced, which seriously limits the service coverage and timeliness.
3.2 Doubling or even tripling the cost of liquid nitrogen in remote areas
Due to the long transportation path, high return empty rate, and the scarcity of specialized cryogenic tanker vehicles, the distribution cost per unit of liquid nitrogen has been rapidly raised in remote areas, which directly restricts the frequency and scale of use in the industrial and medical sectors.
3.3 Long time transportation is easy to cause liquid nitrogen loss, and the loss rate remains high
Liquid nitrogen will continue to evaporate naturally during transportation, and the loss rate can be up to 15%-30% if the vehicle tank has insufficient thermal insulation and stays for too long. In the absence of sufficient replenishment points, customers often receive products with insufficient liquid level, or even directly scrapped.
3.4 Cold Chain System Lacks Digitalization and Automation Management Capability
Currently, cold chain transportation in most Brazilian and neighboring countries is still based on manual ledgers and lacks real-time monitoring of key data such as temperature, liquid level, and location. There is no early warning of liquid nitrogen leakage or temperature abnormality, resulting in difficult to guarantee product quality and uncontrollable service.
✔ Solution Idea: Establish Local Liquid Nitrogen Mini Station with Digital Monitoring Platform
To solve these problems, it is recommended to set up mini liquid nitrogen gasification stations in small and medium-sized cities to reduce long-distance transportation dependence; meanwhile, supporting intelligent monitoring platform to realize temperature tracking, liquid level alarm, geographic location tracking and other functions for the transportation process, so as to improve safety and service stability. In addition, the development of modular tanks and integrated terminal solutions suitable for low-temperature transportation can also reduce the logistics chain and optimize the cost structure to a certain extent.
4. Energy Prices and Operating Costs
Energy prices are not a single variable but a key control point in the cost structure of liquid nitrogen. In the South American market, especially in Brazil, the level of electricity prices and the energy mix have a direct impact on the economics of liquid nitrogen plants, which further determines the likelihood of market penetration and sustainability.
Electricity costs account for more than 60% of the pricing structure of liquid nitrogen
In processes such as variable pressure adsorption oxygen generation and liquid nitrogen liquefaction, compressors, chillers and vacuum systems consume a lot of electricity, and a small fluctuation in electricity prices can lead to significant changes in the overall cost of nitrogen generation/liquefaction. For example, in the industrial area of São Paulo, Brazil, the price of commercial electricity is generally higher than the national average, which severely restricts the operating budget of large nitrogen users.
✅ Suggested Strategy: Consider introducing a grid-connected photovoltaic system for self-generated electricity during the day and staggered peaks at night, complemented by energy-efficient compression system upgrades to reduce power consumption targets.
The difference in industrial electricity consumption between different states is as high as 1.5 times, and site selection errors will drag down the ROI of the project in the long term.
Electricity prices in the south of Brazil (e.g., Paraná) are generally higher than those in the north (e.g., Mato Grosso), and if the deployment of equipment does not adequately take into account the differences in electricity pricing policies, the project may be faced with the problem of high marginal costs in the early stage, which affects the customer’s willingness to purchase and cooperate.
✅ Suggestion for site selection: Promote the deployment of equipment oriented by “electricity economy”, such as setting the optimal layout of energy consumption zones by combining local policy subsidies with the method of comparing electricity price maps.
The energy consumption characteristics of the liquid nitrogen preparation process are limited by the local energy mix and infrastructure.
Liquid nitrogen liquefaction requires high cooling efficiency and stable power, but many emerging industrial parks have high energy supply fluctuations and unstable three-phase voltage, which directly lead to frequent alarms or reduced load factor. Inadequate local natural gas and electricity synergy mechanisms also limit the application of hybrid energy solutions.
✅ Suggestions for upgrading the technology path: Deploy liquid nitrogen equipment with high energy efficiency ratio and load adaptive adjustment capability; e.g., modular system with intelligent frequency conversion, energy consumption warning and remote diagnosis capability, which helps to cope with unstable energy environment.
Environmental regulations drive process modifications, leading to new increases in operating costs
Brazil has recently introduced stricter carbon and refrigerant regulations for industrial gas projects, requiring traditional energy-intensive equipment to be upgraded or retrofitted with environmentally compliant components, such as replacing refrigerants with low GWP values and introducing energy efficiency labeling systems. Such hidden costs are often underestimated in the early stages of a project, and will significantly affect O&M costs in later stages.
✅ Direction of solution: Promote environmentally friendly liquid nitrogen systems certified by CE or ISO14001, and pre-set low carbon process standards to reduce the risk of passive upgrading due to compliance in the future.
5. What Buyers Can Do: Strategic Solutions for Liquid Nitrogen Users
5.1 Localized guidance around usage strategy
In the context of different countries and different industrial uses, it is recommended to formulate liquid nitrogen usage suggestions closer to the endpoints. For example:
In the food processing, electronics manufacturing, and pharmaceutical cold chain industries, which use nitrogen frequently, it is recommended to set up daily/weekly nitrogen usage assessment models to improve the utilization rate.
Introduce automatic metering and alarm mechanism in enterprises with fluctuating demand to avoid excessive purchasing and waste.
5.2 Multi-channel cooperation to build a more robust supply network
Do not rely on a single liquid nitrogen supplier to avoid the risk of supply cut-off.
Guide enterprises to establish a dual supply strategy (main supplier + local emergency supplier).
Strive for index-linked pricing in supply contracts to buffer the impact of energy price fluctuations.
5.3 Invest in onsite nitrogen production systems and shift to self-production and self-consumption.
Particularly suitable for enterprises with stable demand and large consumption, such as electronics factories and scientific research bases.
Matching with liquid nitrogen deep-cooling equipment (e.g. LIN skid unit), to ensure onsite production for immediate use.
The cost recovery cycle is often 1.5~2 years, which is more economical in the long term.
Avoiding the problems of external dependence such as evaporation loss during transportation, tanker truck deployment, etc.
5.4 Refinement of storage management and reduction of waste.
Introducing Dewar’s tanks/micro liquid nitrogen tanks with RFID label identification, to realize the management of lot/capacity tracking.
Optimizing the structure of the cold-retaining layer of the tank to improve the efficiency of insulation. Optimize the structure of the cold-keeping layer of storage tanks, improve the efficiency of heat preservation, and reduce the rate of static loss.
Transparent inventory and deployment of liquid nitrogen in stock through the ERP system, to avoid excessive stockpiling or backlogging and failure.
5.5 Open up regional cold-chain resources, and build and share the infrastructure together.
Especially important in the developing markets/newly-built industrial parks.
Encourage the construction of liquid nitrogen storage and distribution stations among industrial parks.
Pursue pipeline transportation or mobile nitrogen storage and distribution mode to reduce the unit distribution cost.
Support staggered nitrogen pickups among users in the parks to reduce the peak demand load.
➤ Supplementary Suggestions
For small and medium-sized enterprises (SMEs) users, they can also adopt the form of “Liquid Nitrogen Sharing Alliance” to jointly bargain for purchasing and build storage and transportation nodes together, so as to realize the scale effect and reduce the pressure on unit price. For SME users, we can also adopt the form of “liquid nitrogen sharing alliance” to jointly bargain procurement and build storage and transportation nodes, so as to realize the scale effect and reduce the pressure on unit price.
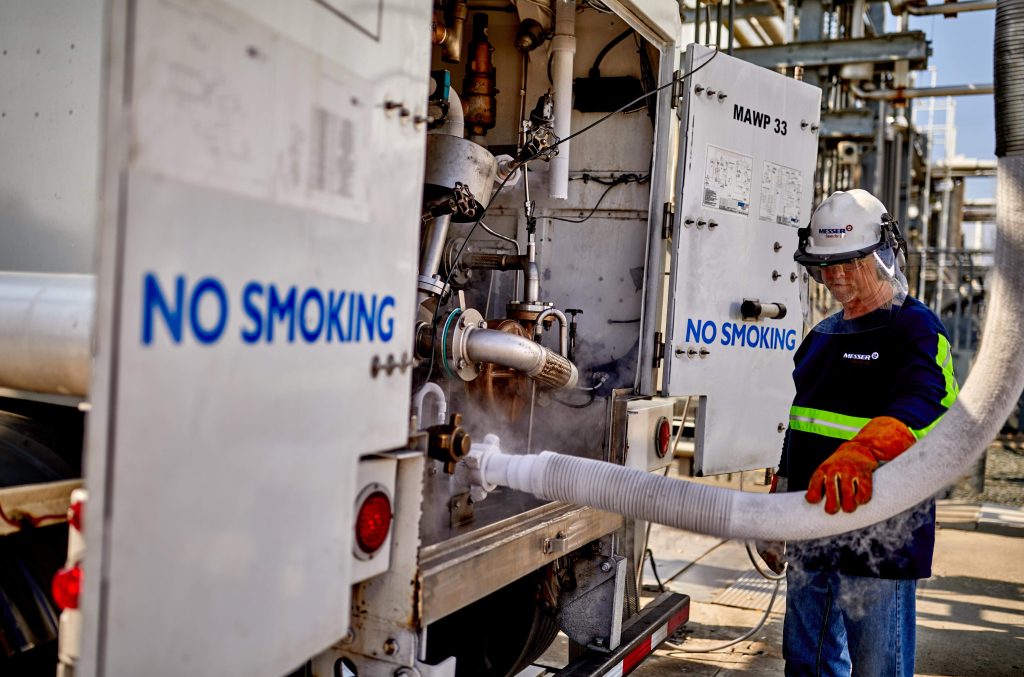
Conclusion
The real reason why liquid nitrogen is so expensive is not because of its high value, but because of the “weak dependence” of the industry chain, which has resulted in a fragile supply, complicated logistics, and out-of-control prices. The solution is not to continue to rely on imports, but to promote Brazilian gas users to build a localized, independent liquid nitrogen supply system.
In the future, with the accelerating trend of “decentralization” of the global manufacturing industry, Brazil will also usher in a strategic window for the local transformation of industrial gases. From hospitals to laboratories, from the food cold chain to metal manufacturing, the localization of liquid nitrogen is not a possibility, but a necessity.
As an international manufacturer of nitrogen generation systems, MINNUO provides one-stop local nitrogen generation solutions, including high-efficiency nitrogen generators, liquid nitrogen generation systems, storage and transportation solutions, and remote monitoring platforms, which have already served many countries and industrial projects worldwide. We welcome more Brazilian partners to explore with us how to build a reliable, efficient and controllable liquid nitrogen localization system.