Oxygen generators are essential equipment in various industries, particularly in medical and industrial applications, where a continuous and reliable supply of oxygen is vital. However, like any complex machinery, these generators can experience issues that affect their performance. This is where understanding error codes and alarms becomes crucial. These systems are designed to alert users about potential problems, allowing for quick identification and resolution, thus minimizing downtime and ensuring that the equipment continues to function optimally.
Troubleshooting guides are incredibly valuable tools for maintaining the reliability of oxygen generators. They provide step-by-step instructions on how to interpret error codes and alarms, helping users to effectively address common problems without requiring extensive technical expertise. By following these guidelines, users can prevent small issues from becoming major failures, keeping the system running smoothly and maintaining a high level of oxygen purity.
It is important to stay calm and follow the troubleshooting steps carefully when encountering an issue with the generator. While dealing with malfunctioning equipment can be stressful, these systems are typically designed with clear instructions for resolving most problems. This article will help you understand how to approach common error codes, what to do when alarms are triggered, and how following a systematic troubleshooting process can resolve issues efficiently. By the end of this guide, you’ll be better equipped to ensure your oxygen generator continues to operate at its best, ensuring consistent oxygen delivery when it’s needed most.
1.Common Error Codes and Their Meanings: Oxygen Generator Troubleshooting
Error Code 1: Low Oxygen Pressure
Meaning: The oxygen generator is unable to maintain the desired output pressure, leading to insufficient oxygen flow or delivery.
Possible Causes:
Blockage in the oxygen flow path, such as clogged filters or tubes
Low air intake pressure, preventing the generator from compressing air effectively
A malfunctioning or faulty pressure sensor that inaccurately detects pressure levels
Solution:
Check and clean the intake filter: Air filters can accumulate dirt and debris over time, restricting airflow. Clean or replace the filter as needed.
Inspect hoses for blockages: Ensure that all hoses are clear of debris and obstruction. Regular maintenance of the airflow system can prevent blockages.
Verify the pressure valve: Check the pressure valve to ensure it’s functioning correctly and is not obstructed.
Reset the system: After cleaning, reset the system and verify that the pressure readings are within the desired range.
Error Code 2: High Oxygen Purity
Meaning: The oxygen purity exceeds the preset limit, which could potentially indicate a malfunctioning sensor.
Possible Causes:
Sensor failure that inaccurately detects oxygen purity levels
Calibration errors that cause the system to misinterpret purity levels
Solution:
Inspect the oxygen sensor: Check for damage or malfunctioning of the sensor. Sensors may wear out over time or become contaminated.
Recalibrate or replace the sensor: If the sensor is damaged or not working properly, recalibrate it or replace it to ensure accurate readings.
Reset the system: After addressing the sensor issue, reset the system to verify that it operates correctly.
Error Code 3: Low Flow Rate
Meaning: The flow rate of oxygen is lower than expected, which can result in inadequate oxygen delivery to the system.
Possible Causes:
Blockage in the airflow, including clogs in the tubing or filters
A faulty flow meter that provides inaccurate readings of oxygen output
Solution:
Inspect and clean the flow meter: The flow meter might be obstructed by debris, reducing the flow rate. Regular cleaning is essential.
Check for obstructions in the tubing: Ensure that the tubes are free of any blockages or kinks that could restrict airflow.
Verify that the system is not in bypass mode: Bypass mode can sometimes reduce flow if the system has been incorrectly switched.
Error Code 4: High Temperature
Meaning: The temperature inside the oxygen generator is too high, which can affect its functionality and efficiency.
Possible Causes:
Overuse or inadequate ventilation leading to excessive heat build-up
Faulty cooling system components, such as malfunctioning fans or cooling coils
Solution:
Check air ventilation and clean the fans: Overheating often occurs when the cooling fans or ventilation system is clogged. Clean the fans and ensure proper airflow to prevent the generator from overheating.
Ensure proper air circulation around the unit: Make sure that the unit has adequate space for ventilation. Avoid placing the generator in enclosed or poorly ventilated spaces.
Reset the system after cooling down: Once the generator has cooled, reset the system to ensure it resumes functioning as expected.
Error Code 5: Power Supply Failure
Meaning: The generator is not receiving power, or there is a voltage irregularity, disrupting the operation of the oxygen generation system.
Possible Causes:
Electrical issues, such as loose wiring or a tripped circuit breaker
Power surges or voltage drops affecting system stability
Solution:
Check the power supply and cables: Inspect the power cables for any damage or disconnections. Ensure that the power source is stable and providing the correct voltage.
Reset the circuit breaker: If a power interruption has tripped the circuit breaker, reset it and verify the system is receiving stable power.
Inspect internal wiring for loose connections: If the issue persists, check internal wiring connections to ensure that there are no loose or disconnected parts.
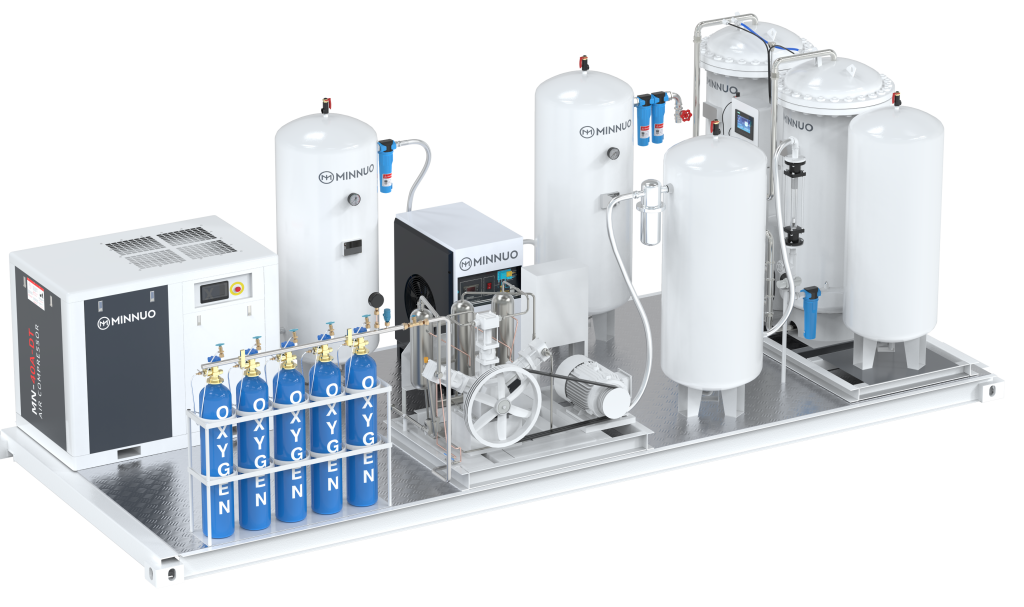
2.Alarm Indicators and Their Meanings: Understanding and Troubleshooting
Green LED Light
Meaning: The system is operating normally. This indicates that the oxygen generator is functioning as expected without any issues.
Solution:
No action is required when the green LED light is on. However, it’s important to monitor the system periodically to ensure that the generator continues to operate without interruptions. If the green light goes off unexpectedly, investigate the issue immediately.
Yellow LED Light (Warning)
Meaning: A minor issue exists that does not stop the generator from functioning but should be addressed. This could be caused by inconsistencies like low airflow or minor pressure fluctuations.
Solution:
Check for minor issues: Inspect components such as intake filters or air filters for clogging, which could lead to airflow restrictions.
Monitor pressure levels: Ensure that pressure readings are within the expected range. Fluctuating pressures can indicate issues with the system that may require adjustment or maintenance.
Perform regular maintenance: Even if the issue is minor, regular servicing (filter cleaning, valve checks) should be scheduled to prevent the problem from escalating.
Red LED Light (Critical Error)
Meaning: A critical error has occurred that requires immediate attention, such as high temperatures or low oxygen output, both of which can seriously affect the generator’s operation and performance.
Solution:
Immediately shut down the system: To prevent any damage to the system, immediately turn off the oxygen generator. This will also prevent overheating or further damage to internal components.
Inspect for failure points: Check for possible causes, such as faulty sensors, blockages in the airflow, or issues with the cooling system. Pay close attention to any warning signs or irregularities in system behavior.
Consult the user manual: Refer to the manual for corrective steps specific to the error. If the problem persists, contact technical support for expert troubleshooting and resolution.
Check temperature and oxygen output: In case of high temperature, verify the cooling system and ensure there is no overuse. For low oxygen output, check for faults in the oxygen separation process or adsorbent materials.
General Troubleshooting Tips:
Proactive Monitoring: Regularly monitor system performance by checking LED lights and ensuring that the system is functioning as expected. Periodic checks can catch small issues before they turn into major problems.
Maintenance Schedule: Implement a consistent maintenance routine, including cleaning filters, checking pressure readings, and inspecting components such as sensors, valves, and cooling systems. Regular upkeep can extend the life of the generator and minimize unexpected shutdowns.
Contacting Support: For critical errors that cannot be resolved with basic troubleshooting, reach out to the manufacturer’s technical support. Their expertise can assist with identifying underlying causes and provide guidance on repairs or part replacements.
3. Common Troubleshooting Steps for Oxygen Generators
Step 1: Identify the Issue
Before diving into complex troubleshooting, start by identifying the root cause of the issue. This involves checking error codes, LED lights, and any alarms that the system may have triggered.
Check Error Codes and Lights:
Review the display screen for any error messages or LED indicators that point to specific system malfunctions, such as low oxygen pressure, high temperature, or power supply issues. Refer to the manual for the meanings behind these codes or alarms.
Determine the Type of Issue:
Assess whether the issue is related to key system components:
Pressure: Is there a significant drop in oxygen pressure?
Flow: Are the flow rates abnormal?
Temperature: Is the system overheating?
Power Supply: Is the generator receiving the necessary power supply, or are there electrical disruptions?
This step helps narrow down the problem, saving time and effort in resolving the issue.
Step 2: Perform Basic Maintenance
Regular maintenance can prevent most issues before they become major problems. If the system is showing any signs of malfunction, start with these simple maintenance tasks:
Clean Filters and Sensors:
Over time, filters and sensors can become clogged with dust or debris, affecting performance. Regularly clean or replace filters as needed. Ensure that sensors are free from dust or contaminants, as this can affect the system’s ability to correctly measure oxygen levels and pressure.
Check Tubes and Hoses:
Inspect the oxygen flow path to make sure that all hoses are securely connected and free of blockages. This will ensure that oxygen is delivered smoothly through the system without interruptions.
Inspect the External Environment:
Ensure the system is operating in a clean, well-ventilated area. Oxygen generators require proper airflow to function efficiently, so inspect the air intake and ventilation systems to prevent overheating or improper oxygen flow.
Step 3: Consult the User Manual
If performing basic maintenance does not resolve the issue, consult the manufacturer’s user manual for more specific troubleshooting guidance. The manual often provides additional steps or checks for diagnosing problems and error codes.
Cross-Reference Error Codes:
Look up the specific error code displayed by the system in the troubleshooting section of the manual. Often, it will provide exact causes and solutions, such as recalibrating sensors or checking pressure valves.
Review Alarm Descriptions:
Alarms related to high temperature, low pressure, or electrical issues are commonly addressed in the manual. Follow the corrective steps listed to resolve the issue efficiently.
Step 4: Reset the System
Many minor system errors can be resolved by simply resetting the system. This helps clear temporary issues such as sensor errors or software glitches.
Power Cycle the System:
Turn off the generator and wait for a few minutes before turning it back on. This can help reset the internal sensors and clear any temporary issues that may have occurred.
Check for Recurring Problems:
After resetting the system, monitor whether the issue reappears. If the system continues to malfunction, this indicates a deeper problem that requires further investigation.
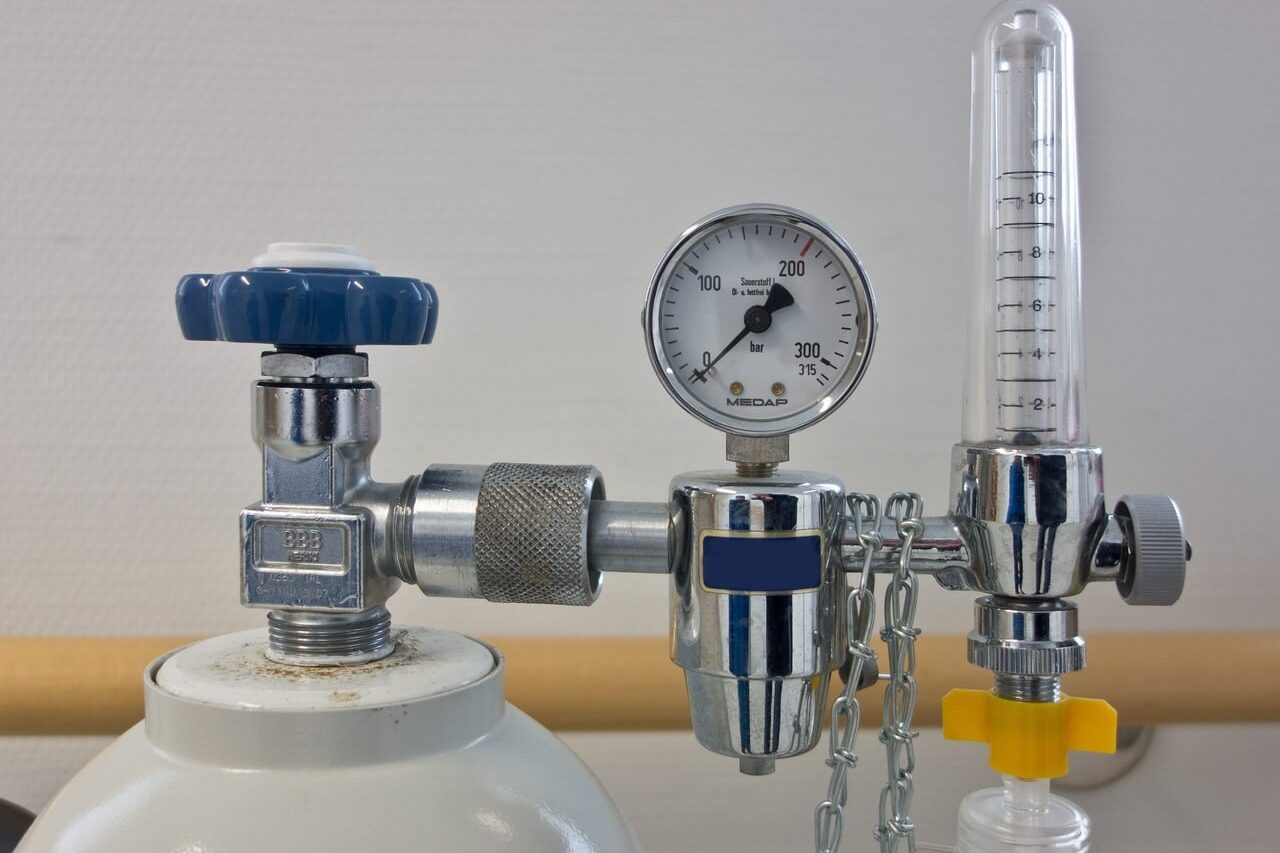
4. Preventative Maintenance Tips for Oxygen Generators
Ensuring your oxygen generator remains in optimal condition involves proactive maintenance. By following these preventative maintenance tips, you can reduce the risk of unexpected breakdowns, enhance the system’s reliability, and improve overall operational efficiency.
1. Regular Cleaning and Inspection of Filters, Sensors, and Internal Components
Regular cleaning of key components in the oxygen generation system is crucial to maintaining efficiency and performance. Over time, dust, debris, and moisture can clog filters and sensors, leading to reduced oxygen production and potential system failure.
Air Intake Filters: Clean or replace filters regularly to prevent airflow blockages, which can cause reduced efficiency and increased wear on internal components.
Sensors: Inspect and clean sensors periodically to ensure accurate readings for oxygen concentration, pressure, and temperature. Dirty or faulty sensors can trigger incorrect error codes, disrupting operation.
Internal Components: Periodically inspect the internal components, including air compressors and valves, to ensure they are functioning properly. Lubricate moving parts and replace worn-out seals to prevent leaks or system failure.
2. Periodic Calibration of Sensors
Oxygen generators rely on accurate sensor readings to monitor and adjust oxygen production levels. As sensors can drift over time, regular calibration ensures that they provide accurate data.
Oxygen Concentration Sensors: These should be calibrated at least once a year or when noticeable discrepancies in oxygen purity are observed. Proper calibration ensures that the oxygen purity stays within the desired range, typically 93%-99%.
Pressure and Flow Sensors: These sensors should also be calibrated periodically to ensure that they reflect accurate pressure and flow rates, preventing underperformance or safety concerns in the system.
3. Monitor the Operating Environment for Adequate Ventilation and Temperature Control
The environment where your oxygen generator is located plays a significant role in its performance. Lack of proper ventilation and improper temperature control can cause the system to overheat, affecting its efficiency and longevity.
Ventilation: Ensure that the room or space housing the oxygen generator is well-ventilated, allowing for proper airflow. This prevents the system from becoming too hot and ensures that heat dissipation is adequate.
Temperature Control: Oxygen generators often operate optimally within a specified temperature range. Monitor the temperature of the room and ensure that it doesn’t exceed the recommended limits, as excessive heat can damage sensitive components or trigger system failures.
4. Routine Testing to Ensure System Reliability and Compliance with Medical Standards
Regular testing of the system helps to ensure that it operates within the required safety standards and compliance with medical regulations.
System Testing: Schedule regular functional tests to check the output of oxygen purity, flow rate, and pressure. Perform stress tests to confirm that the system operates efficiently under load.
Compliance with Medical Standards: Ensure that the oxygen generator meets local health and safety regulations. This includes checking the system’s compliance with medical-grade standards for oxygen purity and quality.
Conclusion
In this Oxygen Generator Troubleshooting Guide, we’ve outlined the common error codes, alarm indicators, and practical troubleshooting steps to help you effectively manage your oxygen generator. Understanding and responding to these alerts can significantly reduce operational downtime and maintain system reliability. Many issues can be resolved with basic maintenance practices, such as regular cleaning, recalibration, and ensuring the system’s environment is properly maintained.
It’s important to reassure users that regular maintenance is key to ensuring the longevity and efficiency of the oxygen generator. By staying on top of maintenance tasks and adhering to troubleshooting guidelines, you can avoid common issues, maintain high-purity oxygen output, and reduce the risk of system failure.
However, should any issues persist or if you’re unsure about specific troubleshooting steps, we highly encourage you to reach out to your manufacturer or technician for expert guidance. At MINNUO, we are committed to providing exceptional after-sales support, ensuring that our customers receive expert advice, system optimization, and maintenance services to keep your equipment running smoothly. Whether you’re dealing with a minor issue or a critical failure, our team is always available to assist you in ensuring reliable oxygen delivery for your needs.