In the field of oxygen applications, from medical rescue to industrial processes, from steel smelting to electronics and semiconductors, purity standards have always been a key variable in system performance and cost control. This article focuses on 99.5% high-purity oxygen, a widely adopted yet often overlooked “golden middle ground,” systematically outlining its technical application scenarios, the actual differences between 90%, 93%, and 99.99% oxygen, and its strategic significance in terms of safety, energy efficiency, and long-term operations, helping readers make more targeted selection decisions.
Have you ever wondered: Why is 99.5% oxygen so frequently used in actual projects? What exactly are the differences between it and 93% and 99.99% oxygen? Is higher purity always better? Does cost also increase accordingly? This article will clarify the true relationship between oxygen purity and application requirements, pointing out that in different industrial contexts, higher purity does not always equate to better cost-effectiveness, and that 99.5% oxygen strikes the optimal balance between “purity, safety, and efficiency.”
After reading this article, you will gain insights into the specific oxygen purity requirements of various real-world scenarios, how industry engineers balance efficiency and compliance, and why MINNUO recommends 99.5% as one of the preferred standard configurations for most industrial applications. If you are selecting an oxygen system or considering upgrading your existing system to a high-purity oxygen mode, this article will provide critical decision-making criteria.
1. Common and high-value applications of 99.5% oxygen
1.1 Medical and healthcare applications
Does the oxygen supply standard in operating rooms meet 99.5%?
During surgery, oxygen purity directly impacts patient safety and post-operative recovery. 99.5% pure oxygen significantly reduces risks associated with oxygen concentration fluctuations during anesthesia. Especially in sterile operating rooms, low oxygen purity may lead to infection control issues.
Why is oxygen purity emphasized in ICU hyperbaric oxygen systems?
In ICU settings, patients often rely on mechanical ventilation or high-flow oxygen delivery systems. 99.5% pure oxygen helps improve the efficiency of blood oxygen saturation recovery, particularly in critical care scenarios such as traumatic shock or ARDS (Acute Respiratory Distress Syndrome).
Can 93% oxygen replace 99.5%? Answer: Not recommended.
While 93% oxygen may meet basic requirements in some respiratory treatments, in special scenarios such as pulmonary fibrosis, chronic obstructive pulmonary disease (COPD), or high-altitude hypoxia, 99.5% oxygen ensures greater stability and therapeutic efficacy in sustained oxygen supply.
1.2 Industrial Manufacturing
Why is 99.5% oxygen strongly recommended for metal cutting and welding?
In plasma cutting and laser welding processes, oxygen not only serves as an oxidizer but also plays a decisive role in flame temperature and stability. 99.5% pure oxygen significantly improves the smoothness of cut edges and prevents the formation of oxidation residues.
Glass Manufacturing: Does low-purity oxygen lead to reduced product quality?
High-temperature combustion in glass furnaces requires extremely high oxygen purity. Using 99.5% oxygen reduces the interference of nitrogen content on glass color and uniformity, thereby improving light transmittance and stability, meeting the production requirements for high-end glass products.
Why can’t 93% oxygen be used for analytical gases or silicon wafer annealing?
In high-temperature reduction reactions or semiconductor manufacturing processes, impurity control is critical. 99.5% oxygen effectively reduces reaction shifts caused by impurity gases, making it suitable for analytical-grade or electronic-grade applications, ensuring reaction reproducibility and safety.
1.3 Environmental and biotechnology
Oxygen selection in wastewater treatment systems: Why is 99.5% superior to 99.999%?
In industrial-scale biological wastewater treatment processes, 99.5% oxygen offers more controllable costs and already meets microbial oxygen requirements. Unless used for special microbial adaptation or experimental reactions, ultra-high-purity oxygen may not necessarily yield increased benefits.
Does oxygen purity affect microbial stability in fermentation systems?
In certain antibiotic or enzyme fermentation processes, there are specific requirements for oxygen mass transfer rates. 99.5% oxygen can consistently provide the required dissolved oxygen (DO) levels, promoting high-yield strain growth while avoiding metabolic pathway changes caused by low-purity oxygen.
Can ordinary oxygen be used as a substitute in CO₂ capture comparison experiments?
Not recommended. In carbon capture technology (CCUS) experiments, high-purity oxygen ensures the stability of experimental variables, avoids the impact of nitrogen on absorption rates, and improves data comparability and reproducibility, making it the preferred choice for most universities and environmental research institutions.
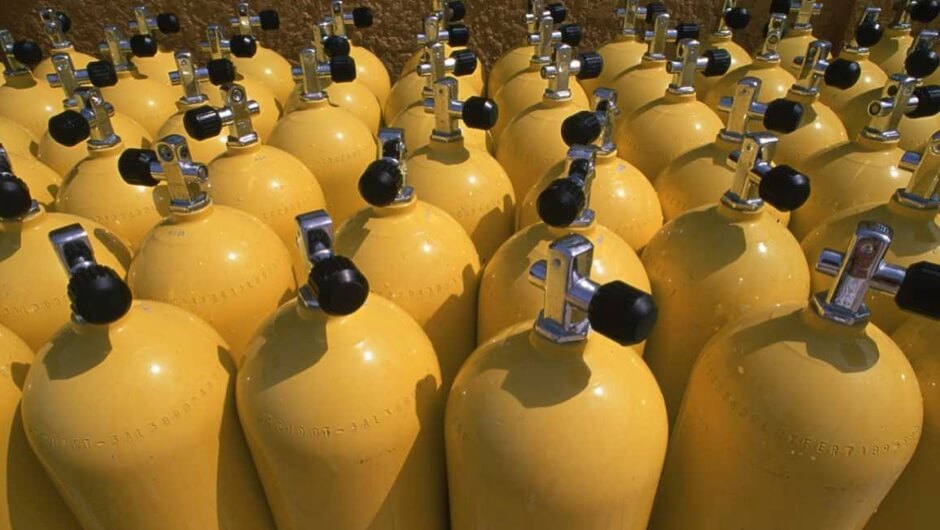
2. Matters that customers often overlook but should inquire about
When purchasing or using 99.5% pure oxygen equipment, many customers overlook the importance of the “supporting system” and focus only on the oxygen production equipment itself, which in turn affects the final purity and system stability. The following are four issues that must be taken seriously but are often overlooked:
2.1 How to choose the appropriate dryer or filtration system?
Core issue: Oxygen purity is directly linked to dew point control
Inadequate dew point control can lead to moisture accumulation in pipelines, fostering microbial growth, corrosion, or oxidative side reactions, which in turn affect oxygen purity and equipment lifespan.
Recommended approach: Select a low dew point drying system (e.g., desiccant dryer) and assess whether dual-stage dehumidification (pre-cooling dryer + post-desiccant) is necessary based on local climate conditions.
✅ Recommended configuration: Dew point ≤ -40°C, paired with a three-stage filter (particle, oil mist, precision filtration).
2.2 Are the pipeline material and valve grade compatible with the requirements for 99.5% high-purity oxygen?
Core issue: High-purity oxygen has extremely stringent requirements for material cleanliness.
Oxygen is highly oxidizing and flammable, so pipeline materials must avoid metals containing impurities or oil-containing materials such as copper, brass, and carbon steel.
Recommended practice: Use 316L stainless steel clean pipelines with oil-free and burr-free processing, and select medical-grade or industrial O₂ dedicated valve bodies.
Ignoring this could lead to oxidation reactions, valve leaks, or even safety incidents.
2.3 Configuration considerations for high-temperature, high-humidity, and dusty environments
Core issue: Environmental factors significantly impact equipment performance.
In regions with high humidity and heat, such as Southeast Asia, Africa, and the Middle East, equipment should be equipped with anti-condensation and corrosion-resistant protection.
In dusty environments (e.g., cement plants, steel mills), a dust removal pre-treatment unit should be installed upfront.
✅ Supplementary measures: The enclosure protection rating is recommended to be upgraded to IP55 or higher, and the filtration system can opt for a self-cleaning structure.
2.4 How to ensure a continuous output of 99.5% when load fluctuations are large or oxygen usage is unstable?
Core issue: Load fluctuations can cause abnormal tower pressure and switching frequencies, affecting oxygen purity.
If oxygen demand fluctuates significantly, it can trigger frequent switching of the PSA unit, resulting in temporary purity reduction or decreased desorption efficiency.
Recommended approach: Add an integrated buffer tank (≥30% of system flow) + high-speed automatic valve + PID control logic to intelligently regulate system operating frequency.
If conditions permit, it is recommended to incorporate a flow automatic regulation module to achieve “on-demand oxygen supply.”
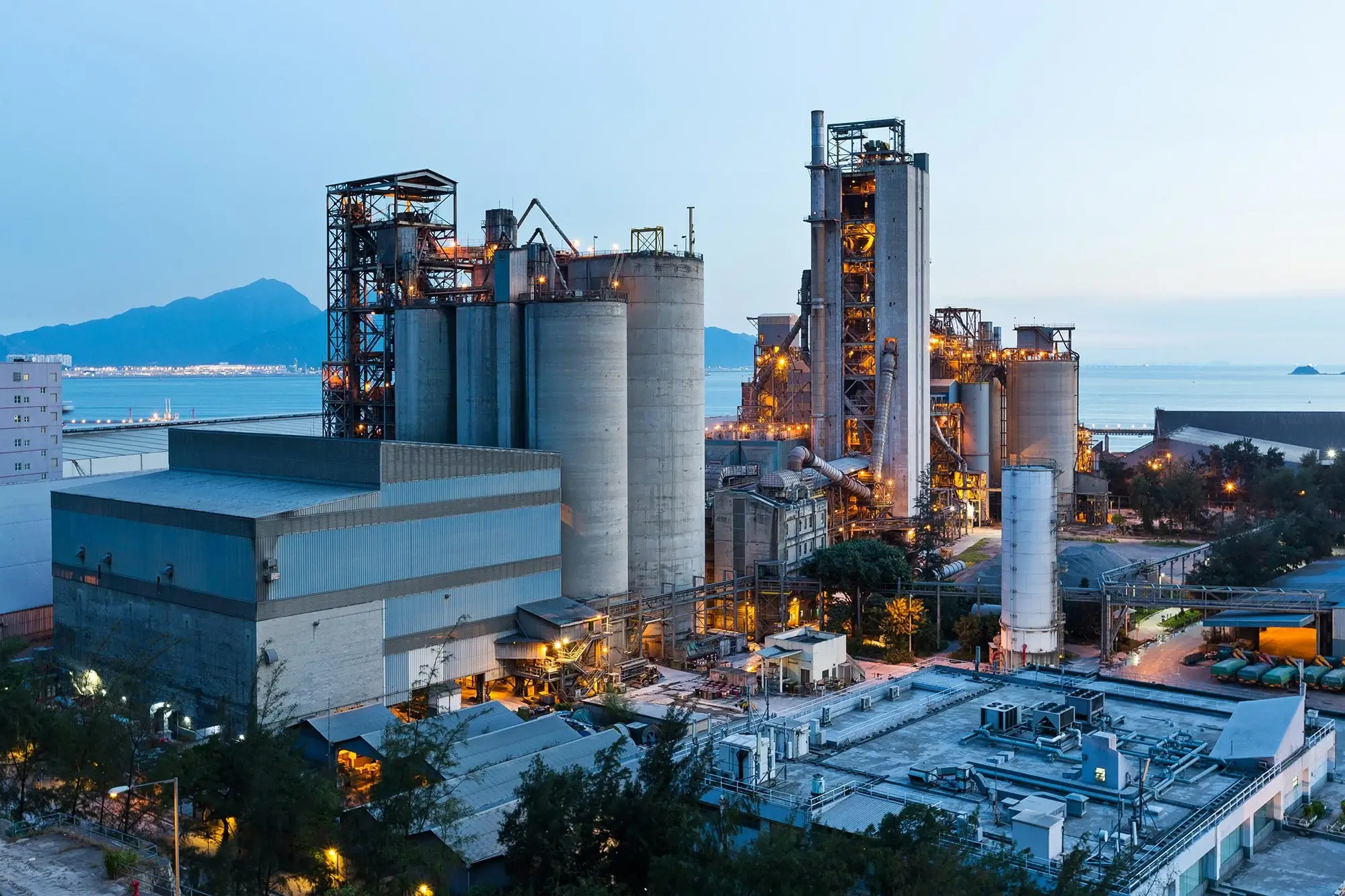
3. Economic and Technical Feasibility: When 99.5% is “Just Right”
3.1 A Realistic Comparison of Annual Operating Costs for Oxygen Purity Levels of 95%, 99.5%, and 99.999%
Many users focus solely on the initial equipment cost, overlooking the significant differences in long-term operating costs. Take an industrial user consuming 100 Nm³ of oxygen per day as an example:
A PSA system using 95% oxygen is typically cheaper, but it cannot meet the requirements of applications sensitive to oxygen content, such as precision welding and electronic packaging;
Upgrading to 99.5% allows the system to meet the needs of most medical, food processing, and high-temperature combustion applications that are more sensitive to impurities, with energy consumption increasing by only 8%–12%, but the product’s value significantly increases;
If one blindly pursues 99.999% purity, a deep cryogenic air separation system must be introduced, resulting in a 2–3-fold increase in annual electricity, maintenance, and spare parts costs, significantly extending the payback period.
3.2 Key point: 99.5% oxygen achieves the best cost-effectiveness in most industrial/medical applications.
Technical implementation pathways: PSA/VPSA/deep cryogenic air separation technology compatibility comparison
To achieve 99.5% oxygen purity, PSA/VPSA technology is the current mainstream method, suitable for flow rates ranging from 10 to 3,000 Nm³/h. It features a simple system structure, compact footprint, and low operational costs. However, if customers select the wrong equipment and use deep cryogenic systems to meet moderate purity requirements, it will result in “technological overkill” and investment waste.
Technical Approach | Applicable oxygen flow rate | Oxygen purity capacity | Initial investment | Operating costs | Applicable customer types |
PSA System | 10 to 800 Nm³/h | 93% to 99.5% | Low | Low | Small and medium-sized factories, clinics, welding points |
VPSA System | 300 to 3000 Nm³/h | 93% to 99.5% | Medium | Medium | Medical systems, food factories, etc. |
Deep Cryogenic Air Separation System | >1000 Nm³/h | ≥99.999% | Very high | Extremely high | Oxygen cylinder filling plants, steel smelting, etc. |
3.3 Selecting the appropriate technical path is essential for controlling costs and preventing redundant construction.
How do you determine if you truly require 99.999% purity?
Customers often fall into the psychological trap of assuming “higher is better,” overlooking the actual oxygen purity requirements of the process:
Incorrect example: An electronics factory customer planned to purchase 99.999% oxygen for wave soldering, but after testing, it was found that 99.5% was sufficient to maintain bright, clean solder joints without oxidation.
Correct approach: Prioritize confirming the “end-use purity requirements” of oxygen rather than pursuing “supply-side purity.” If extremely high purity is still required afterward, a small-scale purifier can be installed at the end to locally purify the oxygen, avoiding the high costs of building an entire system.
➡ Conclusion: 99.5% purity is the optimal balance point for most “industrial high-demand but non-extreme” scenarios.
4. Real-world case studies
4.1 Middle East gas plant: Replacing liquid oxygen with 99.5% oxygen saves nearly 18% in annual operating costs
The plant had previously relied on imported liquid oxygen, consuming over 150 tons monthly for metal cutting and welding. After introducing a PSA system to produce 99.5% pure oxygen, annual operating costs decreased from $450,000 to $368,000, with stable energy savings and a 30% extension in equipment maintenance cycles. The site also achieved unmanned operation through an automated monitoring system, significantly enhancing safety and operational efficiency.
4.2 Medical scenario upgrade: 93% to 99.5%, ICU oxygen therapy equipment runs more smoothly
A county-level hospital in South Asia originally used a 93% medical molecular sieve oxygen generator, which caused frequent fluctuations in oxygen supply and resulted in a high alarm rate for intensive care unit equipment. After upgrading to 99.5% high-purity oxygen equipment, the alarm rate of oxygen therapy equipment decreased by 75%, and medical staff feedback indicated more stable system operation. This solution does not require the use of expensive liquid oxygen and does not significantly increase daily operational expenses, achieving a balance between safety and economy.
4.3 European biotech company: 99.5% oxygen improves fermentation efficiency by 12% and shortens production cycles
This biotechnology company specializes in microbial metabolic engineering, where oxygen purity significantly impacts fermentation efficiency. After replacing the original 93% oxygen system with a 99.5% PSA oxygen production solution, the fermentation cycle was reduced from 72 hours per batch to 63 hours, with a 9% decrease in energy consumption per unit. The higher oxygen purity improved microbial activity, resulting in more stable batch yields and consistency.
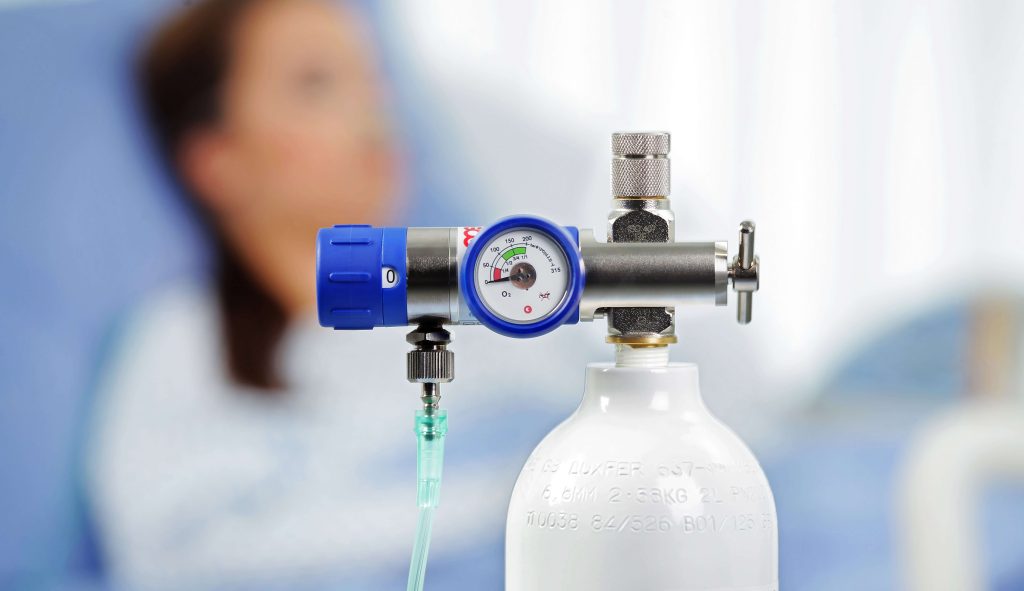
5. Key technical considerations when purchasing 99.5% oxygen
When selecting and purchasing 99.5% high-purity oxygen equipment, it is not just the “oxygen purity” parameter itself that matters, but also the system’s overall measurement accuracy, material compatibility, and gas supply strategy. These factors directly impact whether the equipment is truly suitable for your specific application.
5.1 Oxygen analyzer detection accuracy and error range: How to verify purity authenticity?
Many devices claim to output “99.5%” oxygen, but the actual error range of the oxygen analyzer may be ±0.5% or even wider. This means that the “99.5%” you see may actually be below 99%. Therefore, the following three points must be considered during equipment selection:
Whether the analyzer uses paramagnetic or laser principles, which are more stable and resistant to interference compared to electrochemical sensors;
Whether the detection instrument has been calibrated by a third-party organization (e.g., SGS, TÜV) and whether an error curve is provided;
Whether long-term data recording functionality is available to facilitate continuous monitoring of oxygen concentration fluctuations and avoid misinterpretation of instantaneous readings during procurement decisions.
→ Recommendation: For use in ICU or industrial process gas quality control, it is recommended to select instruments with an error range of ±0.1% and require the manufacturer to provide calibration reports.
5.2 Matching standards for oxygen cylinders and oxygen pipeline systems: Not all materials are suitable for transporting high-purity oxygen.
99.5% oxygen is highly reactive, imposing stricter requirements on the sealing, corrosion resistance, and oxidation resistance of the transportation system. Common issues include:
Ordinary carbon steel or un-degreased stainless steel pipes may pose fire risks;
If the inner walls of oxygen cylinders are not degreased, long-term use may lead to oil oxidation and carbon buildup, contaminating gas purity;
If the sealing material at pipe and valve interfaces is low-quality rubber, oxygen leakage and cracking reactions may occur.
→ Recommendation: For applications in food, biotechnology fermentation, or medical settings, it is essential to specify the use of 316L stainless steel oxygen pipelines, with fittings undergoing tertiary degreasing treatment, and compliance with ISO 7396-1 or FDA gas transportation standards.
5.3 Continuous oxygen supply vs. tank oxygen supply: Choosing the wrong mode can increase system instability risks
Customers using 99.5% oxygen often have a misconception: blindly pursuing continuous oxygen supply. However, not all scenarios are suitable for continuous oxygen supply:
Application scenarios | Recommended mode | Reasons |
Hospitals, laboratories | Tank oxygen supply | Stable gas supply with minimal fluctuations; easy maintenance |
Metal cutting, welding | Continuous oxygen supply | High flow rate and continuous gas use to avoid interruptions |
Intermittent process use | Tank + automatic start/stop | Reduce energy waste and improve system response flexibility |
→ Recommendation: Assess your own working conditions and gas usage patterns, and if necessary, choose an “oxygen production + buffer tank + variable frequency gas supply” structure to achieve an efficient and economical oxygen supply strategy.
6. How MINNUO Supports Customized 99.5% Oxygen Applications
In high-purity oxygen applications, equipment compatibility, data traceability, and system integration capabilities are the key concerns for customers. MINNUO addresses these core needs by offering engineering-driven customized services and comprehensive technical support.
6.1 Dual-track approach of standards and modules: Meeting diverse customization needs
Custom production is supported for PSA oxygen generators or cryogenic air separation oxygen modules, with parameters tailored to customer requirements for oxygen production volume, purity stability, and fluctuating oxygen demand. These solutions are commonly used in industries such as healthcare, electronics manufacturing, and metal cutting. Modular design facilitates installation, scalability, and maintenance, making it suitable for projects with space constraints or those requiring phased expansion.
6.2 Precise data assurance: comprehensive reporting and certification throughout the process
Each unit comes with a complete purity test report traceable to the core testing instruments before shipment. Key indicators such as oxygen purity, flow rate, and dew point can be calibrated as needed, and third-party certification (e.g., ISO 13485, ISO 7396-1, CE) is available to meet stringent quality system requirements for medical and food-grade gases.
6.3 Integrated solutions: Enhancing deployment efficiency and system stability
Customized integration services for compressors, dew point meters, online analyzers, centralized control systems, etc., can be provided based on the customer’s operational environment and technical capabilities, reducing reliance on customer technical personnel and improving overall equipment operational efficiency. For cross-border projects, remote monitoring and technical training services can be provided simultaneously.
6.4 Adapting to Extreme Environments: Scenario-Specific Engineering Solutions
Whether in high-altitude oxygen-deficient environments, extremely cold outdoor deployments, or dusty, high-humidity, and highly corrosive areas, MINNUO offers configuration options such as stainless steel housings, explosion-proof electrical controls, and corrosion-resistant sensors. Additionally, we support customized safety protection for special applications like military and biopharmaceutical industries, ensuring continuous equipment operation in critical scenarios.
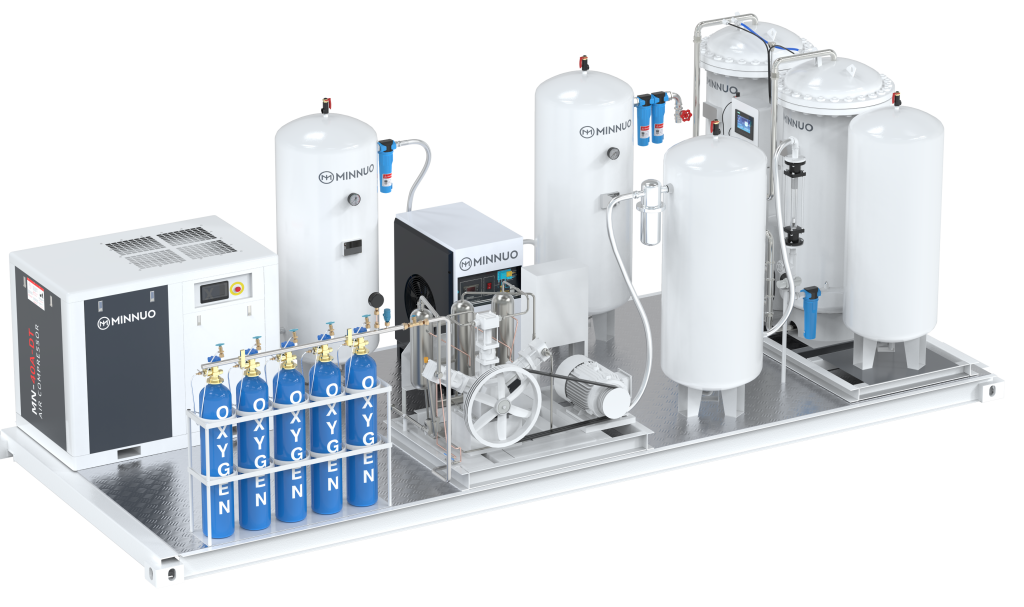
Conclusion
99.5% high-purity oxygen demonstrates significant application potential in medical and industrial fields, with its efficient and cost-effective characteristics becoming key factors in industry process optimization, enhanced safety, and improved economic benefits.
When selecting equipment, companies should consider their own process conditions, end-user oxygen purity requirements, and operational costs to comprehensively evaluate the required technical solutions.
As a reliable system integrator and provider of customized solutions, MINNUO not only offers equipment compliant with international standards such as ISO and CE but also assists customers in building complete system solutions encompassing compression, storage, detection, and control, helping users achieve the optimal balance between performance and cost.