Customized CNG Refueling Station Solutions
Comprehensive Coverage from Gas Treatment to Compression and Storage
We provide fully integrated CNG refueling systems, including gas drying, compression, storage, and dispenser interfaces, suitable for mother station/child station applications.
Full-Process CNG Refueling Station System
MINNUO’s full-process CNG refueling station system includes a complete set of refueling infrastructure, with seamless coordination between each component.
- Natural Gas Pre-treatment Unit: Utilizing advanced technology, this unit efficiently removes water and sulfur from natural gas, strictly controlling sulfur content to ≤5mg/Nm³ and water dew point to ≤-40°C, providing clean gas for subsequent processes.
- High-Pressure CNG Compressor: Available in single or multi-stage configurations, with a working pressure range of 250-300 bar and a flow rate from 300 to 3000+ Nm³/h, meeting the needs of refueling stations of various scales.
- Buffer Storage System: Featuring ASME-certified vertical storage tanks, along with skid-mounted or underground bottle groups. The underground bottle groups are coated with anti-corrosion layers for long-term stable operation.
- Refueling Dispensers and Control Valves: Available in dual or quadruple dispenser configurations, employing precise metering technology with an error rate ≤1.5%, providing accurate data support for vehicle refueling.
- Quick Installation Skid Layout: Featuring modular design that significantly optimizes the installation process, reducing the installation period by 40% compared to traditional methods.
- Optional Expansion Modules: Includes tanker loading interfaces, compatible with L-type/T-type connectors for easy tanker filling, catering to diversified operational needs.
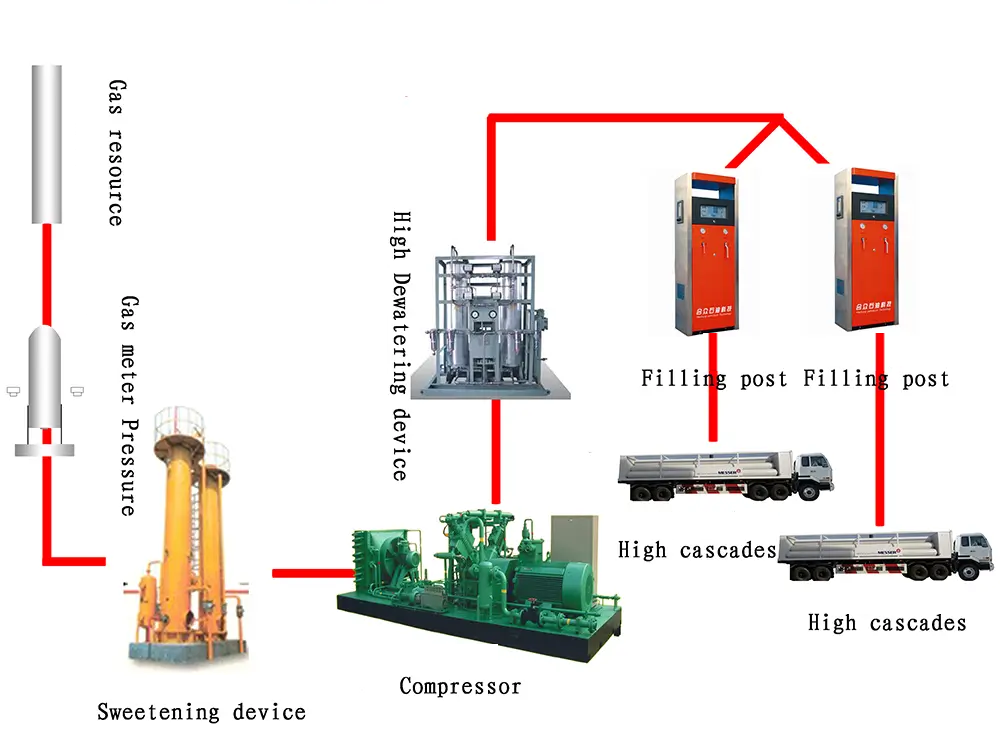
Supported Station Types
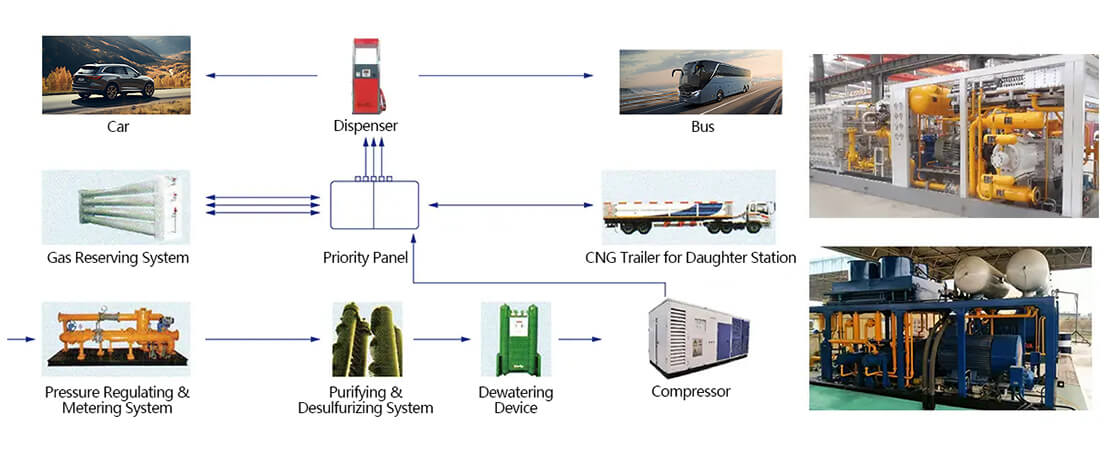
CNG Mother Station
Directly connects to the natural gas pipeline, with a daily processing capacity of 5000 to 20,000 Nm³, and a tanker loading efficiency ≥95%, ensuring efficient large-scale refueling operations.
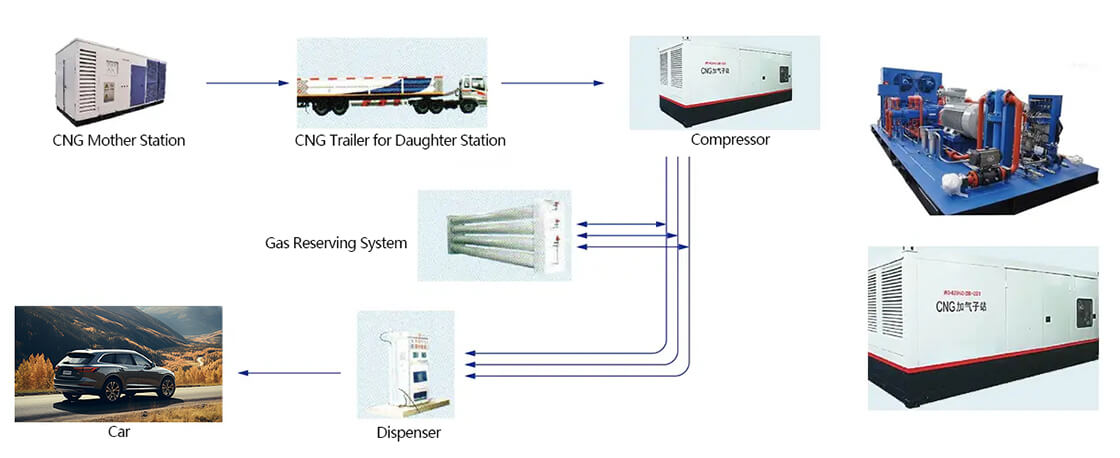
CNG Child Station
With a tanker offloading pressure adaptive range of 50-250 bar, it can quickly refuel vehicles to meet daily operational needs.
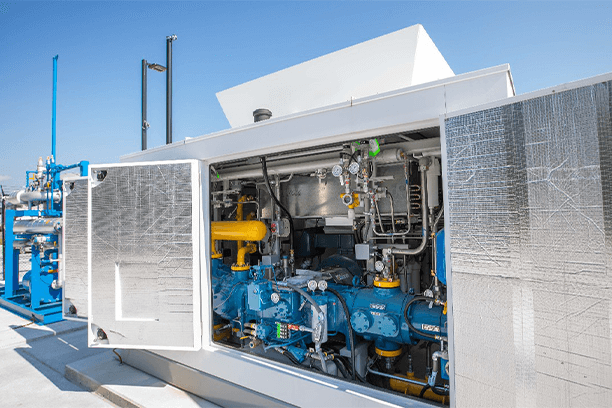
Co-constructed Station
Features a dual-gas source redundant design, with an intelligent switch between pipeline and tanker interfaces to ensure stable gas supply.
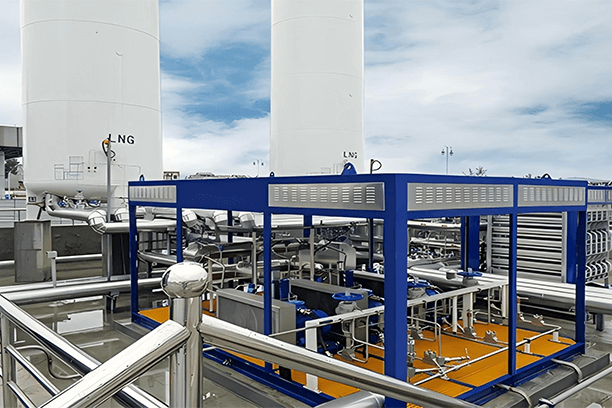
Modular Mobile Station
Available in containerized (ISO standard) and vehicle-mounted types, which can be deployed quickly within 72 hours, offering flexibility for different scenarios.
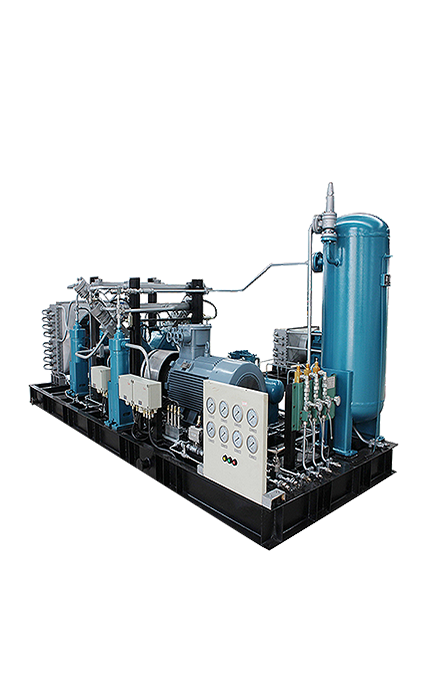
Core Advantages
By choosing MINNUO, you gain the following distinct advantages:
- Super High-Pressure Stable Output:Capable of continuous compression at 300 bar, with pressure fluctuation ≤±2%, ensuring stable refueling processes.
- Intelligent Safety System:ATEX Zone II explosion-proof certification, equipped with 24-hour gas leak detection and automatic shutdown devices, ensuring safe operation of the refueling station.
- Extreme Environment Compatibility:Operates in a wide temperature range of 40°C to 55°C, with no performance degradation even at altitudes of 5000 meters.
- Digital Control: Utilizing Siemens PLC and a 10-inch HMI touchscreen, supporting SCADA remote monitoring for real-time station management.
- EPC Turnkey Service:Offering one-stop delivery services from solution design, equipment supply, to commissioning and training, saving time and effort.
Featured Equipment Modules
MINNUO Core Equipment Technology Breakdown
1.Natural Gas Pre-treatment Unit
- Function: Integrates desulfurization, dehydration, and filtration functions.
- Technical Parameters: Sulfur content purified to ≤5mg/Nm³, compliant with GB17820 Class II; employs molecular sieve adsorption + refrigerant drying dual-mode, with a water dew point of ≤-40°C; equipped with triple stainless steel filters, dust filtration precision of 0.01μm.
- Core Advantage: Effectively prevents compressor corrosion and dispenser clogging; molecular sieve life ≥8000 hours with automatic regeneration control to extend service life; modular design reduces maintenance time by 50%. Suitable for coalbed gas/biogas purification with sulfur content >20mg/Nm³.
2.High-Pressure CNG Compressor
- Function: Boosts natural gas to 200-300 bar.
- Technical Parameters: Flow range 300-4000 Nm³/h, available in three or four-stage compression; power range 55kW-250kW, with ±5% flow adjustment through variable frequency control; oil-free piston technology, oil content ≤0.1ppm.
- Core Advantage: 15% more energy-efficient than traditional models, using smart unloading valve + waste heat recovery technology to reduce energy consumption; 24-month warranty on key components, including crankshaft/piston rod/seals; supports API 11P/ISO 13631 standards.
- Recommended Models: MTW 4000 large-flow multi-stage compressors for mother stations, MTC 800 compact skid-mounted units for child stations.
3.Gas Storage System
- Function: Provides buffering and pressure stabilization.
- Technical Parameters: Vertical tank capacity of 20-80m³, designed according to ASME Section VIII; underground bottle groups have 8-48 bottle modules, made of X70 steel + 3PE anti-corrosion; working pressure 250-300 bar, safety factor ≥2.4.
- Core Advantage: Vertical tanks save 40% of space compared to horizontal tanks; underground bottle groups are resistant to typhoons and UV, with a lifespan >20 years; optional pressure equalizer to reduce fluctuation to ±1.5%.
4. Intelligent Refueling Dispenser
- Function: Provides accurate vehicle refueling and data management.
- Technical Parameters: Dual or quadruple dispenser configurations, refueling speed of 15-25 Nm³/min; uses mass flow meters + temperature compensation, with a metering accuracy of ±1.0%; supports RFID cards/QR codes/vehicle license plate recognition payment systems.
- Core Advantage: Explosion-proof rating ExdⅡBT4, usable in flammable environments; automatically matches pressure, with inlet 20-250 bar adaptive; supports cloud data synchronization, enabling data collection for refueling volume, fault codes, and user behavior.
Project Case Study
Middle East 2000 Nm³/h CNG Mother Station Project
- Core Equipment: Uses a three-stage reciprocating compressor (300 bar) + molecular sieve dehydration unit.
- Storage Module: Equipped with 24 sets of underground storage tanks, with a total capacity of 4800 Nm³.
- Intelligent Control: Features explosion-proof control cabinets (IP65) + 4G remote diagnostics.
Project Outcome: From shipment to commercial operation in just 45 days, with 35 tankers refueled daily.
FAQ
A1:
Yes. We consider the diverse needs of our customers and support the separate purchase of any unit, as well as custom procurement bundles. To ensure compatibility when connecting to existing systems, we offer standardized interface adaptation services, reducing the difficulty of equipment integration and assisting customers in upgrading and optimizing their systems easily.
A2:
Our standard compressor models have a flow range of 300-3000 Nm³/h and a pressure range of 200-300 bar, meeting the operational needs of most conventional refueling stations. For customers with large-scale refueling needs, such as large mother stations, we also provide custom services to create high-flow models exceeding 4000 Nm³/h for efficient station operations.
A3:
Yes. Considering the infrastructure limitations in remote areas, we offer vehicle-mounted and containerized mobile station solutions. These solutions are equipped with diesel generator interfaces for external power supply, eliminating dependence on fixed power grids. Additionally, they feature off-grid control modules to allow effective management and control of equipment, even in areas without network coverage.
A4:
The core components of our refueling station system require maintenance intervals of ≥4000 hours, significantly reducing maintenance frequency and operational costs. Furthermore, we have multiple spare parts warehouses worldwide, enabling fast response services for spare part replacements and minimizing downtime, ensuring the continuous and stable operation of refueling stations.
A5:
Yes. With the growing demand for clean energy, we support the installation of LNG vaporization modules for existing CNG refueling stations. This modification allows the station to supply both LNG and CNG, meeting the diverse needs of different customers, enhancing the station’s market competitiveness, and upgrading it into a dual-energy station.
Related Solutions
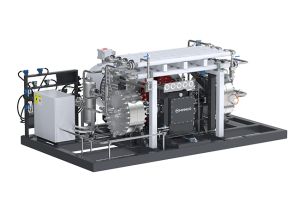
Hydrogen Compressor
Hydrogen Compressor With over 30 years of expertise in hydrogen compression technology, MINNUO is a leading provider in the world. More than 2,000 of our
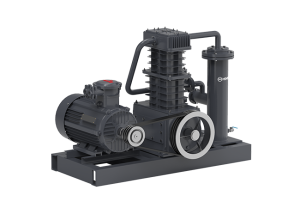
LPG Compressor
LPG Compressor MINNUO LPG compressors are specifically designed for industrial gas compression scenarios, suitable for the unloading, pressurization, and steam recovery of media such as
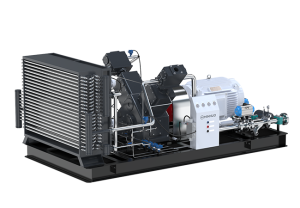
CNG Compressor
CNG Compressor The MINNUO CNG compressor is a reciprocating piston-type compression device specifically designed for demanding industrial environments. It is capable of handling multiple mediums,
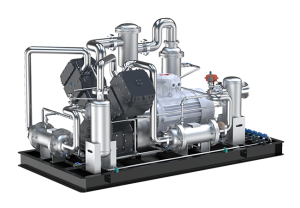
Ammonia Compressor
Ammonia Compressor MINNUO ammonia compressors are specifically designed for the chemical, refrigeration, and industrial sectors, offering a wide range of compression support for various scenarios
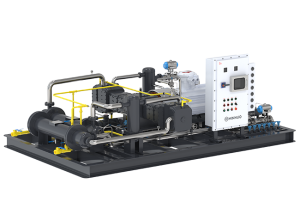
Helium Compressor
Helium Compressor MINNUO helium compressors are specially designed for industrial applications, utilizing reciprocating piston technology to efficiently compress helium gas to high pressures ranging from
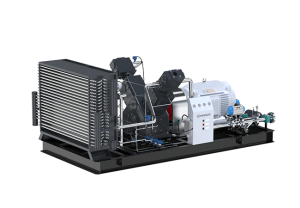
CNG Refueling Station Solution
Customized CNG Refueling Station Solutions Comprehensive Coverage from Gas Treatment to Compression and Storage We provide fully integrated CNG refueling systems, including gas drying, compression,