Air separation equipment and cryogenic air separation technology are essential in modern industrial gas production. Their efficient separation and liquefaction capabilities are widely applied in various fields such as chemicals, metallurgy, and energy. This article will provide an in-depth analysis of the technological system of air separation equipment, the cryogenic air separation process, and its applications across different industries, helping you better understand this advanced industrial gas production technology.
Air separation equipment liquefies air through deep freezing and employs distillation principles to separate gases such as oxygen, nitrogen, and argon. Its primary processes include impurity purification, deep freezing, distillation separation, regeneration cycles, and an intelligent control system. The cryogenic air separation process involves three stages: air compression and purification, low-temperature distillation separation, and liquid nitrogen storage and vaporization, ensuring the production of high-purity gases.
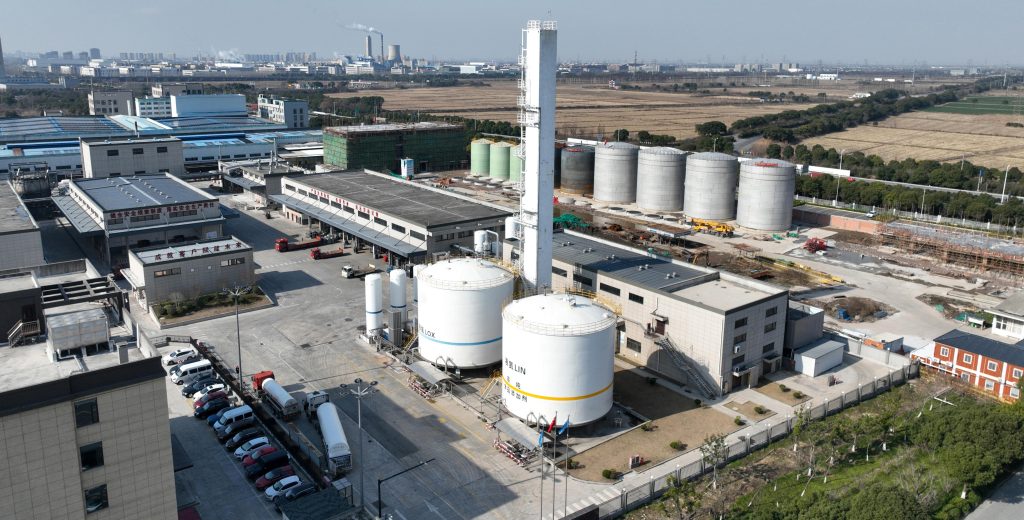
I. Overview of Air Separation Equipment Technology
Air separation equipment (abbreviated as air separation units) is an industrial device that liquefies air using deep freezing technology and separates oxygen, nitrogen, and inert gases such as argon through distillation. As a global leader in air separation equipment manufacturing, MINNUO, with decades of technological expertise, has developed a comprehensive product matrix that covers high-pressure, medium-pressure, high-low pressure, and all-low pressure processes. The equipment capacity ranges from 20m³/h to 50,000m³/h (oxygen), fully meeting the diversified needs of industries like chemicals, metallurgy, and energy.
1. Five Core Systems of Air Separation Equipment
The efficient operation of air separation equipment relies on the collaboration of five key systems:
- Impurity Purification System: Uses multi-stage air filters and molecular sieve adsorbers to precisely remove mechanical impurities, moisture, CO₂, and hydrocarbons such as acetylene from the air, ensuring that the feed gas purity exceeds 99.99%.
- Deep Freezing System: Integrates centrifugal compressors, plate-fin heat exchangers, and turbine expanders to liquefy air through the Joule-Thomson effect, with a temperature gradient control down to -196°C.
- Distillation Separation System: Composed of a double-column structure (upper and lower distillation columns) and a condenser-evaporator, it utilizes the boiling point differences between oxygen (-183°C) and nitrogen (-196°C) to achieve efficient phase separation.
- Regeneration Cycle System: Achieves online regeneration of molecular sieve adsorbents through hot nitrogen gas back-blowing and programmed heating, ensuring continuous production.
- Intelligent Control System: Employs a Distributed Control System (DCS) to monitor over 300 process parameters such as pressure, temperature, and flow in real time, with a fault self-diagnosis accuracy exceeding 99.5%.
2. Milestones in Technological Development
MINNUO continues to lead industry technology upgrades:
- Capacity Breakthrough: From the early 20m³/h small units to 50,000m³/h large-scale systems, the oxygen extraction rate of single units has increased to 98.7%.
- Energy Efficiency Optimization: The energy consumption of all-low-pressure process equipment has been reduced to 0.38kWh/Nm³, saving over 25% compared to traditional processes.
- Intelligent Upgrade: Integrated AI predictive maintenance systems have reduced key equipment failure warning response times to 30 seconds.
II. In-depth Analysis of Cryogenic Air Separation Nitrogen Production Process
As the gold standard for industrial gas production, the cryogenic air separation nitrogen production process dominates high-end industries such as electronic manufacturing and aerospace with its ultra-high purity of 99.999%.
1. Process Flow in Three Stages
A. Air Compression and Purification:
- Pre-treatment: Coarse filters (G4 grade) capture particles ≥5μm to protect compressor blades from wear.
- Compression and Cooling: A three-stage centrifugal compressor pressurizes air to 0.6-1.2MPa, with a nitrogen water precooling system lowering the temperature to 5-10°C.
- Deep Purification: 13X molecular sieve adsorption towers dynamically adsorb CO₂ to ≤1ppm, controlling acetylene content to ≤0.1ppm.
B. Low-Temperature Separation and Distillation:
- Main Heat Exchanger: Plate-fin heat exchangers enable counterflow heat exchange between returned gas (waste nitrogen, product nitrogen) and incoming air, with temperature difference control ≤3°C.
- Double-Column Distillation: Lower Column Operation: Pressure 0.5-0.6MPa, liquid oxygen concentration 38%-42%. Upper Column Distillation: 99.999% gas nitrogen at the top, with the oxygen-enriched liquid reflux ratio controlled between 1:5 and 1:8.
- Condenser-Evaporator: Uses a falling film structure, with a temperature difference maintained at 1.5-2.5K, and nitrogen condensation capacity reaching 30m³/h·m².
C. Liquid Nitrogen Storage and Vaporization:
- Low-Temperature Storage Tank: Double-layer vacuum insulation design, with a daily evaporation rate ≤0.08%.
- Vaporization System: Combination of air-heated and water-bath vaporizers, with emergency gas supply response time <2 minutes.
2. Key Equipment Technical Parameters
Equipment Name | Technical Features | Performance Indicators |
Centrifugal Compressor | Tri-axial flow impeller design, imported guide vanes + diffuser adjustments | Isothermal efficiency ≥78%, surge margin ≥15% |
Molecular Sieve Adsorber | Double-bed structure (activated alumina + 13X molecular sieve) | CO₂ adsorption capacity ≥12ml/g, lifespan 8-10 years |
Turbine Expander | Centrifugal radial-axial flow, silicon nitride ceramic bearings | Isentropic efficiency ≥85%, speed 30,000rpm |
Distillation Column | Structured packing tower (Sulzer CY), stainless steel corrugated plates | HETP ≤35cm, pressure drop ≤3kPa/m |
Plate-Fin Heat Exchanger | Six-channel layout, serrated fin design | Heat transfer coefficient 3500W/m²·K, end temperature difference ≤3K |
III. Technical and Economic Comparison of Air Separation Processes
MINNUO offers the best solutions for customers by deploying multiple technical routes:
1. Comparison of Three Major Processes
Comparison Dimension | Cryogenic Air Separation | PSA Method | Membrane Separation |
Investment Cost | 5000m³/h unit approx. 280 million RMB | Saves 40% for the same scale | High equipment cost, high maintenance |
Operating Energy Consumption | 0.38-0.42kWh/Nm³ (99.999% nitrogen) | 0.25kWh/Nm³ (99.9% nitrogen) | 0.29kWh/Nm³ (98% nitrogen) |
Startup Time | Cold start 24-36 hours | ≤30 minutes | ≤20 minutes |
Product Flexibility | Can co-produce oxygen, argon, rare gases | Single product, purity range ±1% | Poor purity adjustment |
Applicable Scenarios | Continuous gas consumption (>3500m³/h) in steel, chemical industries | Intermittent gas consumption (<2000m³/h) in electronics, food | Laboratory-scale small flows (<500m³/h) |
2. Technical Selection Recommendations
- Large-scale Demand (>10000m³/h): Prefer an internal compression cryogenic system with an argon extraction system.
- Medium and Small-scale Demand (500-3000m³/h): Recommend VPSA nitrogen production equipment, with an investment recovery period of <3 years.
- Ultra-Pure Demand (≥99.999%): Cryogenic process is essential, with a low-temperature adsorber.
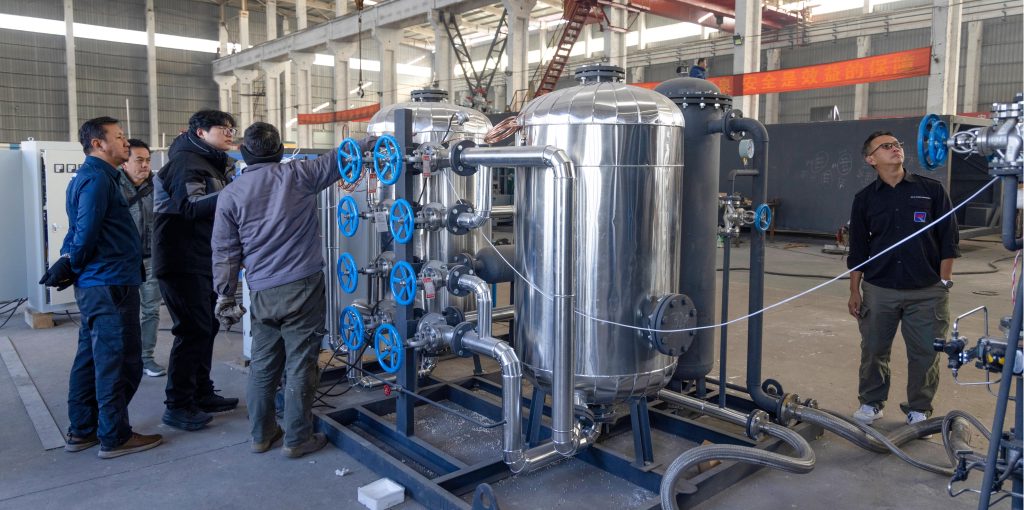
IV. MINNUO Intelligent Solutions
Based on 100+ large projects, MINNUO has developed the Air Separation Industry 4.0 solution:
1. Intelligent Control Three-Layer Architecture
- Equipment Layer: 5G intelligent sensors collect vibration, temperature, and component data in real-time.
- Control Layer: Advanced Process Control (APC) system with self-optimizing reflux ratio of the distillation column with ±0.5% precision.
- Management Layer: Digital twin system achieves 72-hour production simulation, improving scheduling optimization by 18%.
2. Key Technological Breakthroughs
- Surge Control: Neural network-based predictive algorithm, with surge warning accuracy of 99.2%.
- Molecular Sieve Sequence Control: Valve switching time error <0.1 seconds, reducing regeneration gas consumption by 12%.
- Unmanned Operation System: AI visual recognition replaces 95% of manual inspections, with a 100% safety violation detection rate.
V. Industry Applications and Outlook
MINNUO equipment has been successfully applied in:
- Steel and Metallurgy: Supporting 5000m³ blast furnaces, oxygen purity 99.6%, argon extraction rate >95%.
- Electronics Manufacturing: Providing 99.9999% ultra-high purity nitrogen for 12-inch wafer fabs.
- New Energy: Hydrogen liquefaction plants with BOG recovery systems, reducing energy consumption by 30%.
Future technological development directions:
- Zero Carbon Emission: Development of photovoltaic-driven air separation units, with a target carbon reduction of 50% by 2030.
- Miniaturization: Development of containerized cryogenic equipment, reducing footprint to 1/3 of conventional systems.
- Digital Delivery: Building a full-lifecycle management platform, increasing equipment availability to 99.95%.
VI. Conclusion
This article provides a comprehensive analysis of the technical system of air separation equipment and the core advantages of cryogenic processes. Whether for large-scale industrial gas needs or ultra-high purity gas production, MINNUO can provide the optimal solution. For customized solutions, feel free to contact our engineering team.