With the continuous growth of nitrogen demand in industrial fields, nitrogen injection pipeline pressure testing has become an increasingly critical procedure for ensuring the safety of nitrogen delivery systems. This is particularly important in high-risk environments such as mining and chemical industries, where the stability and safety of nitrogen pipelines are crucial. This article will provide a detailed analysis of the importance of nitrogen injection pipeline pressure testing and the safety measures involved, helping industry personnel to better understand and implement pressure testing operations to ensure the safe and stable delivery of nitrogen.
The nitrogen injection pipeline pressure testing process ensures that the nitrogen delivery system can withstand the operating pressure and prevent leaks. The key factors include strict control over pressure testing pressure, nitrogen concentration, and safety monitoring. With parallel design of dual adsorbers, PLC intelligent control systems, precise gas flow control, leakage alarms, and remote monitoring technology, the stability and safety of the pressure testing process are guaranteed. Additionally, measures such as gas monitoring, equipment pipeline management, personnel allocation, and emergency evacuation routes further ensure the safe execution of operations.
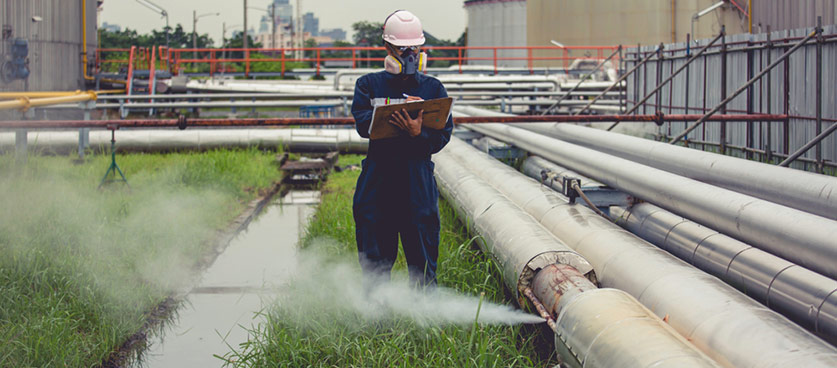
1. Importance of Nitrogen Injection Pipeline Pressure Testing
Nitrogen injection pipeline pressure testing is an indispensable step in the commissioning process of a nitrogen delivery system, aimed at ensuring that the pipeline system can withstand working pressure and prevent nitrogen leaks. Nitrogen injection pipelines are generally used in mining, chemical plants, and other facilities requiring high-concentration nitrogen, and the success or failure of pressure testing directly affects the safety and stability of the entire system. To ensure the safety of both equipment and personnel, the technical parameters during the pressure testing process must strictly comply with relevant standards.
In environments such as underground operations, nitrogen injection pipeline pressure testing becomes even more critical. During pressure testing, the nitrogen concentration typically needs to be maintained at ≥97% high purity, with pressure strictly controlled below ≤0.8 MPa, ensuring the safe operation of the nitrogen delivery system in extreme environments. Additionally, pressure testing work must strictly adhere to relevant safety regulations and technical measures to eliminate potential risks at the source.
2. MINNUO Nitrogen Generator Pressure Testing Technical Advantages
As a leading domestic nitrogen generator manufacturer, MINNUO continuously enhances its technological capabilities to ensure the efficiency and safety of every nitrogen injection operation. MINNUO’s nitrogen generators feature a dual adsorber parallel design and a PLC-controlled intelligent control system. This design ensures continuous nitrogen supply through alternating pressure adsorption and depressurization regeneration technology, guaranteeing stability and safety during the pressure testing process.
Specifically, MINNUO’s nitrogen generators ensure stable nitrogen output during the pressure testing process through precise gas flow control, pressure sensors, and leak detection systems. Furthermore, MINNUO’s equipment can be remotely monitored for data collection and real-time monitoring, ensuring that every aspect of the process complies with safety standards and minimizing the likelihood of accidents.
The pressure testing paths cover multiple routes from the nitrogen injection pump room to various work points, such as: nitrogen injection pump room → auxiliary shaft → 730 track transport street → first mining area track uphill → 850 vehicle yard → 1110 track tunnel → 1111 coal mining work face transportation route. Through systematic design, MINNUO ensures that each pipeline can operate smoothly under strict pressure testing standards.
3. Safety Technical Measures for Nitrogen Injection Pressure Testing
3.1 Gas Monitoring and Personnel Protection
During the nitrogen injection pipeline pressure testing process, gas monitoring is critical. Personnel must continuously monitor changes in nitrogen concentration and other harmful gases to prevent poisoning or asphyxiation accidents due to low oxygen levels or the accumulation of toxic gases. Every shift must be equipped with multifunctional gas measuring instruments to monitor CH4, CO, and O₂ concentrations in the environment. The specific alarm thresholds are as follows: if the oxygen concentration drops below 18.5%, personnel must immediately evacuate the work area; if CO concentration exceeds 0.0024%, emergency measures must be taken.
Emergency Evacuation: If symptoms such as hypoxia or difficulty breathing occur, personnel must immediately evacuate to an area with fresh air to avoid unnecessary health problems from exposure to low-oxygen environments.
3.2 Equipment and Pipeline Management
During nitrogen injection pressure testing, managing equipment and ensuring the seal integrity of pipelines are equally crucial. All valves must be clearly marked and sealed, especially the three-way valves, which should be clearly labeled with warning signs such as “Nitrogen Injection Hazard, Do Not Open,” to prevent safety hazards due to operational errors. Additionally, warning lines and “No Entry” signs should be placed along the nitrogen injection pipeline route to prevent unauthorized personnel from entering the operation area.
Leakage Prevention and Control: Leakage detection devices must be installed in the system. If leakage occurs, personnel must immediately take emergency measures to ensure pipeline safety. The mechanical and electrical department should arrange dedicated personnel to inspect pipelines and promptly identify and repair potential leakage risks.
3.3 Personnel Allocation and Responsibility Division
Personnel allocation and responsibility division are essential during the nitrogen injection pipeline pressure testing process. The duties of each position must be clearly defined to avoid operational errors due to unclear responsibilities. Nitrogen injection operators should record gas flow and pressure data in the pipeline every hour and make adjustments based on actual conditions. Each shift should also assign a dedicated person for on-site handover to ensure smooth work transitions.
Additionally, the ground bundle pipe monitoring system must simultaneously monitor gas composition and verify the pressure testing effectiveness through data comparison, ensuring safety and accuracy at each stage.
3.4 Disaster Evacuation Route Planning
The operation area must have clearly defined emergency evacuation routes, especially for cases of unexpected accidents, allowing for the swift and safe evacuation of personnel to safe areas. For example, the emergency evacuation route for the 1111 coal mining work face is as follows: 1111 coal mining work face → 1110 belt tunnel → 111 ventilation pedestrian uphill → 730 conveyor street → auxiliary shaft → ground. All personnel should be familiar with the evacuation routes to ensure efficient and rapid evacuation in emergencies.
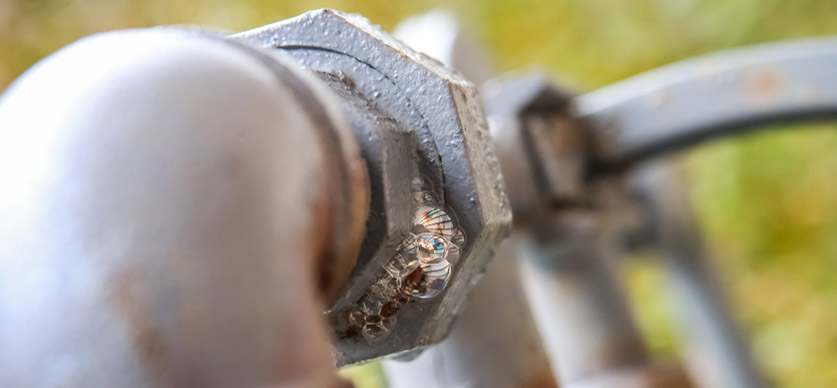
4. Industry Standards and MINNUO Solutions
During nitrogen injection pipeline pressure testing, all operations must comply with industry safety standards and regulations. According to relevant provisions, personnel must be strictly prohibited from entering vortex wind areas during the pressure testing process. Oxygen detectors should be installed around the operation site and monitored by a supervisor to ensure that oxygen concentration remains within a safe range.
MINNUO’s Technical Support: To ensure the safety and efficiency of the operation process, MINNUO’s nitrogen generators are equipped with PLC intelligent control systems, which monitor pipeline pressure, gas concentration, and other parameters in real time and automatically adjust the system’s operation status to reduce the risks associated with human intervention. Additionally, MINNUO uses modular designs, allowing nitrogen generators to be flexibly configured based on different scenarios, making them especially suitable for nitrogen injection needs in complex environments such as coal mines and chemical industries.
5. Frequently Asked Questions (FAQ)
Q1: Why must the pressure be controlled to ≤0.8 MPa during nitrogen injection pressure testing?
A: High pressure may cause pipeline rupture or joint leakage, increasing safety risks. MINNUO’s nitrogen generators are equipped with pressure sensors that monitor pipeline pressure in real time, issuing warnings if any abnormalities are detected, thus preventing accidents.
Q2: How can we quickly respond to unexpected leaks during pressure testing?
A: MINNUO recommends a “warning line + gas monitoring” dual safeguard system, combined with the ground bundle pipe system’s remote monitoring function, to respond to leaks immediately and take corresponding emergency measures.
6. Conclusion
In high-risk industries such as mining and chemicals, nitrogen injection pipeline pressure testing is undoubtedly fundamental to ensuring the safety of nitrogen delivery systems. By strictly implementing safety measures, using efficient equipment and technology, and providing personnel training and emergency plans, safety risks can be minimized.
As an industry leader, MINNUO is committed to providing customized nitrogen injection solutions, ensuring that every operation is completed efficiently and safely. If you require more detailed technical support or training services, please contact MINNUO. We will provide you with the most professional services and solutions.