In today’s industry, energy conservation and environmental protection have become the focus of attention in various industries, and the glass industry is no exception. The wide application of PSA oxygen production process (Pressure Swing Adsorption) in full oxygen combustion in glass furnaces provides an efficient and environmentally friendly combustion solution for the industry. This article will deeply explore the principles of PSA oxygen production process, the advantages of full oxygen combustion in glass furnaces, typical cases and future development trends, and reveal the application value of it in glass production.
The application of PSA oxygen production process in full oxygen combustion in glass furnaces provides an efficient, energy-saving and environmentally friendly combustion solution for the glass industry. Compared with traditional air combustion, the PSA oxygen production process uses molecular sieve separation technology to provide high-purity oxygen to the glass kiln, achieving full oxygen combustion, greatly increasing combustion temperature and efficiency, reducing fuel consumption, and significantly reducing NOx and other pollutant emissions.
What is the PSA oxygen production process? ——Basic principles of oxygen production process
The PSA oxygen production process is an oxygen production method based on physical adsorption separation technology. It separates oxygen from the air through pressure changes and provides high-purity oxygen. The core equipment is the adsorption tower, which is filled with adsorbents such as molecular sieves. The specific process is as follows:
- Adsorption process:The air enters the adsorption tower after being compressed. Molecular sieves preferentially adsorb nitrogen in the air, while oxygen is separated and further purified to form high-purity oxygen.
- Desorption process:When the molecular sieve is saturated, reduce the pressure, release the adsorbed nitrogen, and regenerate the molecular sieve.
- Alternate working of adsorption towers:PSA systems usually use two adsorption towers to work alternately to ensure continuous oxygen supply.
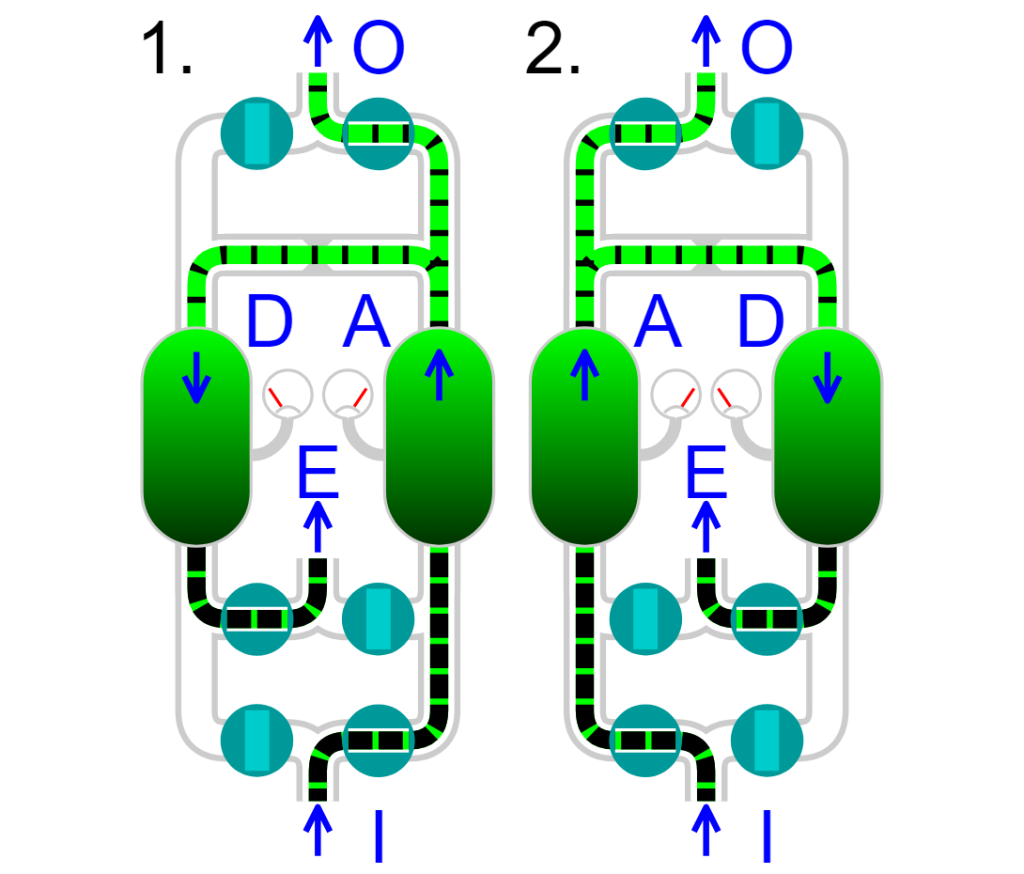
- I:compressed air input
- A:absorption
- O:oxygen output
- D:desorption
- E:exhaust
Compared with the traditional cryogenic oxygen concentrator, PSA oxygen concentrator has a simple structure, fast startup, and low operating costs. It is very suitable for full oxygen combustion in glass furnaces that require long-term oxygen supply.
Advantages of full oxygen combustion supported by PSA oxygen production process to the glass industry
In glass production, the kiln is the core equipment, and the choice of combustion gas directly affects production efficiency and product quality. Traditional kilns use air for combustion. However, 78% of the nitrogen in the air does not participate in combustion. Instead, it consumes a lot of heat, thereby reducing the combustion efficiency and producing a large amount of nitrogen oxides (NOx) and other pollutants. Oxygen combustion uses high-purity oxygen as a combustion-supporting gas, which improves combustion efficiency and significantly reduces pollution emissions.
The advantages of oxygen combustion primarily include the following aspects:
- Higher flame temperature: Oxygen combustion significantly increases the flame temperature, which helps to melt the glass raw materials quickly and evenly, thus improving production efficiency.
- Reduce pollution emissions: Air combustion produces a large amount of nitrogen oxides, while full oxygen combustion greatly reduces the generation of NOx, complying with increasingly stringent environmental regulations.
- Save fuel: Oxygen has a better combustion-supporting effect and improves combustion efficiency, thereby reducing fuel consumption and helping companies control costs.
Five advantages of PSA oxygen production process in full oxygen combustion in glass furnaces
Improve combustion efficiency and production speed
The PSA oxygen production process can stably provide high-purity oxygen, making the kiln combustion more efficient. Compared with air combustion, the flame temperature is higher and the combustion is more stable, thus shortening the glass melting time and improving production efficiency. According to statistics, oxygen combustion can improve production efficiency by 20%-30% in glass production and significantly increase output.
Significant savings on fuel costs
PSA oxygen generation equipment generates oxygen on-site, avoiding the high cost of oxygen transportation and storage. Through efficient combustion, fuel consumption can be reduced by 15%-25%. The low energy consumption of the PSA oxygen generation system further reduces the cost of oxygen generation, helping the glass factory to significantly save operating expenses.
Remarkable effect on environmental protection and emission reduction
After using PSA oxygen generation equipment, full oxygen combustion avoids the participation of nitrogen in combustion, greatly reduces NOx emissions, improves air quality, and has significant environmental benefits. NOx emissions are reduced by more than 50%, which not only meets the requirements of environmental protection policies, but also reduces the company’s emission costs.
Improve glass quality
The PSA oxygen production process provides high-purity oxygen to ensure uniform and stable oxygen combustion flames, which is conducive to the uniform melting of glass raw materials, avoids local high temperature problems, improves the uniformity and heat resistance of glass products, and enhances the market competition of glass products. force.
The system is highly intelligent, stable and reliable
The PSA oxygen generation system has a high level of automation, has functions such as one-button start and fault alarm, and is easy to operate. At the same time, the system’s twin-tower structural design ensures continuous oxygen supply, improves the continuity and stability of production, and greatly reduces the operational risks of the glass factory.
Practical application cases of PSA oxygen production process in glass industry
In order to more intuitively demonstrate the practical application effect of PSA oxygen generation technology in full oxygen combustion in glass furnaces, we provide you with feedback from customers who purchased MINNUO PSA oxygen generators two years ago.
Case 1: A customer in China
The company introduced the PSA oxygen production process in the furnace renovation to support full oxygen combustion. Through modification, the combustion temperature is increased by 200°C, fuel costs are reduced by 23%, and NOx emissions are reduced by 55%. In addition, the PSA oxygen production system realizes real-time monitoring and intelligent adjustment of oxygen concentration, reducing manual operation costs and improving production efficiency.
Case 2: A customer in the United States
In order to meet environmental regulations, the company uses the PSA oxygen production process to transform full-oxygen combustion, saving an average of 20% of fuel annually, reducing NOx emissions by 60%, and significantly improving product quality. The stable oxygen supply of the PSA oxygen generation system prevents enterprises from being subject to fluctuations in external oxygen supply, ensuring the continuity of production.

Future trends and technological innovation of PSA oxygen production process
With the continuous tightening of environmental protection regulations and the increase in energy-saving needs of enterprises, the PSA oxygen production process has broad application prospects in full oxygen combustion in glass furnaces. In the future, this technology will develop in the following directions:
Improve oxygen purity
In the future, the PSA oxygen production process will use new molecular sieve materials and advanced adsorption processes to further improve oxygen purity to meet higher-precision combustion needs.
Intelligent and automated control
In the future, the PSA oxygen production system will combine the Internet of Things and artificial intelligence technology to dynamically adjust the oxygen supply, further optimize equipment operation, and improve system efficiency.
Reduce running costs
New adsorbents and optimized designs will further reduce the power consumption and maintenance costs of the PSA oxygen production system, making the oxygen production process more economical.
Development in line with environmental protection
PSA oxygen generation technology not only reduces pollutant emissions during the combustion process, but also conforms to modern green production concepts and will continue to play an important role in environmentally friendly production in the glass industry in the future.
Conclusion
The application of PSA oxygen production process in full oxygen combustion in glass furnaces not only significantly improves combustion efficiency, reduces production costs, but also reduces pollutant emissions, providing an efficient and environmentally friendly solution for the glass industry. The PSA oxygen production process demonstrates significant advantages in energy saving, environmental protection, and product quality, making it an ideal choice for glass factories aiming to improve production levels and achieve green development. MINNUO oxygen concentrators have always been among the first in the industry, providing personalized high-quality services to many customers in the glass industry and receiving good feedback. We will continue to promote the popularization of oxy-combustion technology and provide solid support for the sustainable development of the glass industry.