In modern industrial production systems, nitrogen generators play a crucial role as the key equipment for nitrogen supply, being widely applied in industries such as chemicals, electronics, and food. A decline in the nitrogen purity produced by nitrogen generators can cause varying degrees of disruption to the entire production process, potentially leading to product quality defects, production accidents, and other serious consequences. Therefore, a thorough and professional analysis of the causes and solutions for nitrogen purity decline is of great practical significance and industrial value.
The causes of nitrogen purity decline in nitrogen generators include equipment aging, improper operation, and raw material gas quality issues. Molecular sieve aging, poor valve sealing, improper flow and pressure control, and excessive oil mist and moisture in the raw material gas can all impact nitrogen purity. Solutions include regular replacement of molecular sieves and seals, proper flow and pressure control, and optimization of raw material gas treatment, such as oil removal and dehydration, to ensure nitrogen purity. Strengthening equipment management and operational procedures is key to ensuring stable system operation.
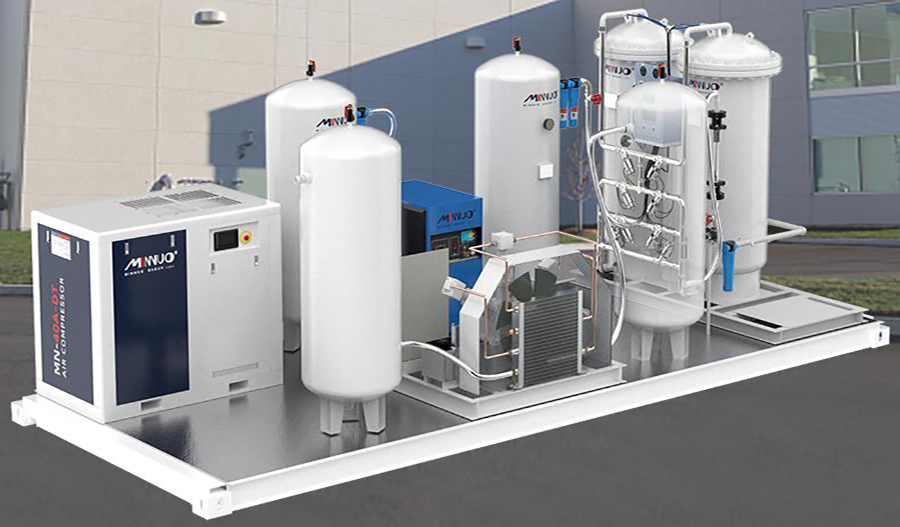
I. Analysis of the Causes of Nitrogen Purity Decline
(A) Equipment Aging and Wear
1.Molecular Sieve Aging
As the core adsorption and separation component in a nitrogen generator, the molecular sieve is primarily composed of aluminosilicate crystals, possessing an orderly and rich micropore structure, with pore sizes typically ranging from 0.3 to 1.0 nanometers. Over prolonged cycles of adsorption and desorption, the crystal structure of the molecular sieve gradually undergoes lattice distortion, leading to deviations in micropore size distribution and a reduction in specific surface area. These microscopic changes directly weaken the molecular sieve’s selective adsorption capacity for impurities such as oxygen, carbon dioxide, and water, resulting in an increase in impurity content in the nitrogen product and a subsequent decrease in purity.Generally, carbon molecular sieves have a lifespan of 5 to 8 years, while zeolite molecular sieves have a relatively longer lifespan but still age over time. As molecular sieves age, their ability to adsorb oxygen weakens, making it difficult to effectively separate oxygen from air, thereby reducing nitrogen purity.
- Molecular Sieve Pulverization
During the operation of a nitrogen generator, molecular sieves are subjected to factors such as airflow impact, pressure fluctuations, and mechanical vibrations. If these factors are too intense, the molecular sieve may undergo pulverization. Pulverized molecular sieve particles become smaller, increasing their specific surface area and making them more susceptible to being carried away by the airflow. This not only results in the loss of molecular sieve material but also leads to filter clogging, disrupting the normal operation of the nitrogen generator. Additionally, the adsorption performance of pulverized molecular sieves significantly declines, further reducing nitrogen purity.
- Molecular Sieve Poisoning
If the air entering the nitrogen generator contains impurities such as oil, water, sulfur, or phosphorus, these substances can chemically react with the molecular sieve, damaging its active sites and causing it to lose its adsorption capacity. This phenomenon is known as molecular sieve poisoning. Molecular sieve poisoning is an irreversible form of damage. Once it occurs, it severely impacts nitrogen purity and can even render the nitrogen generator inoperable.
2.Poor Valve Sealing
Valves inside nitrogen generators, such as switching valves and throttling valves, often use sealing materials such as rubber and polytetrafluoroethylene (PTFE). Under frequent opening and closing actions and the effects of gas flow, these sealing materials may suffer from wear, aging, or deformation. For example, rubber seals, when in prolonged contact with compressed air, may degrade due to oxidation, swelling, and other chemical and physical changes. When valve seals are not tight, internal or external gas leakage can occur, disrupting the normal pressure distribution and flow path within the nitrogen generator, interfering with core nitrogen generation processes like pressure swing adsorption (PSA) or membrane separation, and ultimately leading to a decrease in nitrogen purity.
(B) Improper Operation
1.Unreasonable Flow Control
The intake flow of a nitrogen generator must match its designed processing capacity precisely. From a fluid mechanics and adsorption kinetics perspective, when the intake flow is too high, the gas spends insufficient time in the molecular sieve adsorption tower or membrane unit, preventing the adequate adsorption or separation of impurities such as oxygen and water, which leads to excessive impurity content in the nitrogen. For nitrogen generators based on the pressure swing adsorption principle, excessive intake flow will cause the adsorption front to quickly penetrate the adsorption bed, leading to incomplete adsorption. Conversely, if the intake flow is too low, it can result in a low superficial velocity, reducing production efficiency and potentially causing uneven gas distribution and local adsorption or desorption imbalances, which similarly affects nitrogen purity.
2.Unstable Pressure Control
During nitrogen generator operation, stable pressure is a key factor in ensuring the normal progress of the adsorption and desorption processes. For pressure swing adsorption nitrogen generation, the adsorption phase requires high pressure to increase the adsorption of impurities on the molecular sieve, while the desorption phase requires reduced pressure to release the adsorbed impurities. When the pressure is too high, although the molecular sieve’s adsorption capacity increases, excessive pressure may stress the molecular sieve’s crystal structure, causing irreversible structural damage and reducing its adsorption performance. If the pressure is too low, the desorption of impurities will be insufficient, leaving residual impurities on the molecular sieve and affecting the next adsorption cycle, ultimately decreasing nitrogen purity.
(C) Raw Material Gas Quality Issues
1.Excessive Oil Content
Oil mist in the raw material air mainly originates from lubricating oil leakage in air compressors. When oil mist enters the nitrogen generator, it forms an oil film on the surface of the molecular sieve. From an adsorption principle perspective, this oil film blocks the molecular sieve’s micropores, preventing gas molecules from contacting the active sites of the molecular sieve, significantly reducing its adsorption capacity. Additionally, oil can react chemically with the molecular sieve, destroying its crystal structure and causing permanent deactivation, severely impacting nitrogen purity.
2.Excessive Moisture Content
When the moisture content in the raw material air is too high, water may condense into liquid water or even freeze in low-temperature environments, such as in coolers and filters. This not only damages the metal components of the equipment, causing corrosion and cracking, but also “poisons” the molecular sieve by absorbing water. When the molecular sieve absorbs water, its internal active cations hydrolyze, destabilizing the crystal structure and reducing its selective adsorption capacity for impurity gases, thereby leading to a reduction in nitrogen purity.
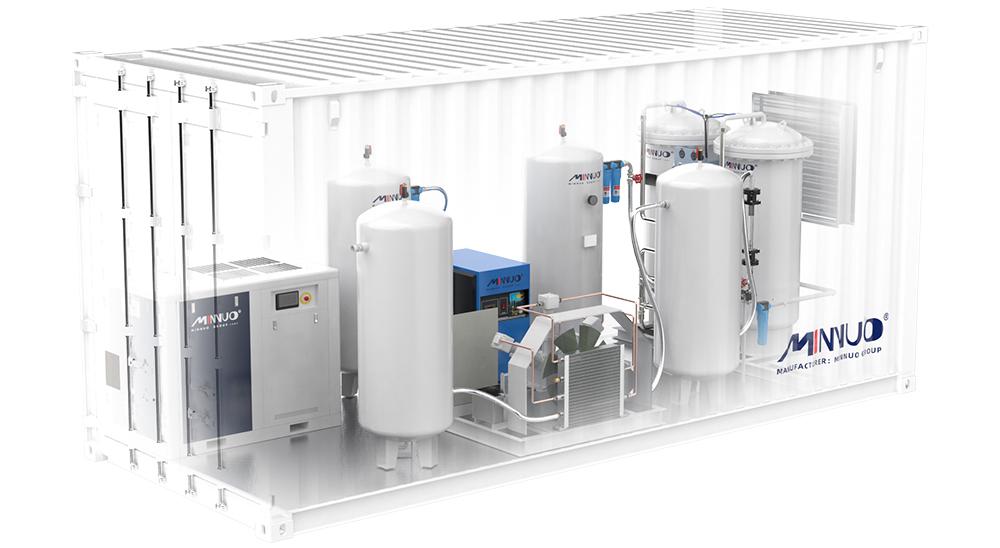
II. Solutions for Nitrogen Purity Decline
(A) Equipment Maintenance and Upgrades
1.Regular Replacement of Molecular Sieves
The replacement cycle of molecular sieves should be determined based on the actual operating conditions, raw material gas quality, and technical parameters provided by the manufacturer. Generally, for nitrogen generators operating in harsh environments or with high impurity levels in the raw material gas, it is recommended to shorten the replacement cycle. During the replacement, molecular sieves should be selected that match the original equipment and comply with industry standards (such as GB/T 10504-2008). Care should also be taken to ensure the even filling of molecular sieves to avoid gaps or uneven piling, thus ensuring the full performance of the adsorption capacity.
2.Inspection and Replacement of Valve Seals
A regular valve seal inspection system should be established, utilizing leak detection instruments such as ultrasonic leak detectors and helium mass spectrometers. If wear or degradation of the seal is detected, it should be promptly replaced. When selecting seal materials, factors such as gas medium, operating pressure, and temperature should be considered. For high-temperature and high-pressure gas environments, materials like polyetheretherketone (PEEK) should be chosen, while for corrosive gases, materials such as fluororubber should be used to ensure long-term reliable sealing.
(B) Standardized Operation Procedures
1.Reasonable Flow Control
Operators should be familiar with the nitrogen generator’s design flow range and accurately control the intake flow based on actual production needs using flow control valves, frequency converters, and other equipment. Flow monitoring instruments such as vortex flow meters and mass flow meters should be installed to monitor the intake flow and nitrogen output flow in real-time. During equipment startup, shutdown, and load changes, the flow should be adjusted gradually to avoid shock to the equipment caused by sudden flow changes. Additionally, a flow and nitrogen purity correlation model can be established to dynamically adjust the intake flow based on real-time nitrogen purity, achieving optimal operating conditions.
2.Stable Pressure Control
A high-precision pressure control system should be installed, consisting of a programmable logic controller (PLC), pressure sensors, and regulating valves in a closed-loop control system. The PLC should analyze and process data from the pressure sensors in real time and automatically adjust the valve opening to ensure that the nitrogen generator maintains stable pressure within the set range. Operators should strictly follow operational procedures for pressure setting and adjustments, and not arbitrarily change pressure parameters. Regular calibration and maintenance of the pressure control system should also be performed to ensure measurement accuracy and reliable control.
(C) Optimization of Raw Material Gas Treatment
1.Installation of Oil Removal Equipment
Before the raw material gas enters the nitrogen generator, multi-stage oil removal equipment should be installed to create a comprehensive oil removal system. For example, a coarse-effect inertial separator can first remove larger oil droplets in the air, followed by a high-efficiency oil mist filter, which can reduce the oil mist content in the air to below 0.01mg/m³. Additionally, regular cleaning and maintenance of oil removal equipment should be conducted, and filtering elements should be replaced to ensure stable and effective oil removal performance.
2.Enhanced Dehydration Treatment
A combined dehydration process using refrigerated dryers and adsorption dryers can be employed. The refrigerated dryer utilizes refrigeration principles to cool the raw material air below the dew point temperature, causing water to condense into liquid water, which is then drained. The adsorption dryer further removes remaining moisture using adsorbents like activated alumina or molecular sieves, which can lower the dew point of the raw material gas to below -40°C. Furthermore, regular regeneration of adsorbents should be carried out to ensure their adsorption capacity and effectively reduce the moisture content in the raw material gas, ensuring stable operation and nitrogen purity.
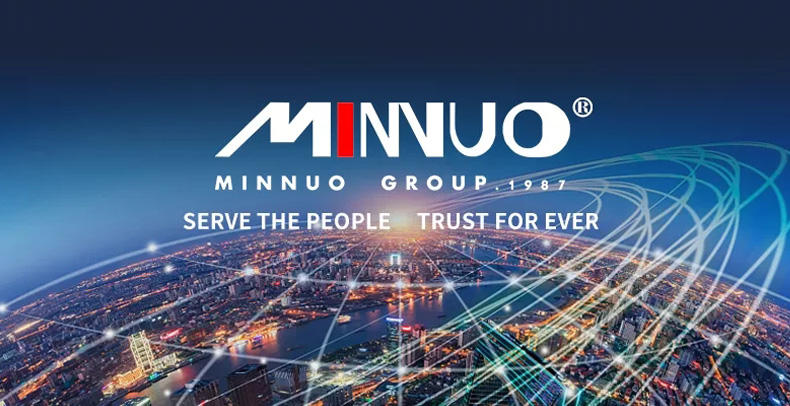
III. MINNUO’s Quality Assurance Measures
As a long-established manufacturer in the nitrogen generator industry, MINNUO has always placed product quality and stability as its top priorities, striving to provide customers with high-quality, high-performance nitrogen generation solutions. To effectively prevent various issues that could lead to a decrease in nitrogen purity, MINNUO has implemented a series of rigorous and professional measures:
(A) Use of Imported High-End Components and Materials
During the manufacturing process, MINNUO adheres to the principle of selecting high-end components and raw materials from internationally renowned brands. From key components like molecular sieves and valves to various seals, filters, and other parts, all undergo stringent selection and quality control. For instance, the molecular sieves are sourced from leading international brands, offering superior adsorption performance and a longer service life, effectively reducing the risk of nitrogen purity degradation caused by the deterioration of sieve performance. Valves are made of high-quality alloy materials paired with high-performance sealing materials, ensuring excellent sealing performance even under frequent opening and closing and exposure to gas flow, thus minimizing the interference of gas leakage with the nitrogen generation process.
(B) Optimized Compressor Configuration
As the core component of the nitrogen generator’s air supply system, the compressor’s performance directly affects the nitrogen quality. MINNUO’s nitrogen generators use advanced variable frequency compressors, paired with other high-end components. Through precise variable frequency control technology, the compressor’s output power and speed are adjusted in real-time according to actual gas demand, ensuring stable air supply with precise and controllable flow. A stable air supply effectively prevents adsorption and desorption process abnormalities caused by fluctuations in flow and pressure, ensuring the nitrogen generator consistently produces high-purity nitrogen under various operating conditions.
(C) Upgraded Purification System
To ensure the high quality of the raw air, MINNUO has deeply optimized the purification system, utilizing advanced 5-stage filtration equipment. From coarse filtration to remove large particle impurities, to fine filtration to eliminate tiny oil mist, moisture, and other harmful impurities, each stage is designed to precisely intercept pollutants of different sizes and properties. Additionally, a high-precision concentration alarm system is integrated to monitor impurity levels in both the raw air and nitrogen. If the impurity concentration approaches the preset threshold, the system immediately triggers an alarm to notify operators, allowing timely intervention to prevent nitrogen purity from being compromised due to raw air quality issues. This ensures early warning and effective prevention of potential problems.
With the comprehensive quality assurance measures mentioned above, MINNUO nitrogen generators have earned a strong reputation in the market and gained the trust of numerous customers.
IV. Conclusion
In summary, the decline in nitrogen purity from nitrogen generators is caused by a combination of various complex factors, involving aspects such as molecular sieve performance, intake systems, equipment sealing, operating parameters, and post-treatment systems.In actual production, companies should also strengthen equipment management, personnel training, and quality monitoring, and establish comprehensive equipment operation and maintenance records to promptly identify and resolve potential issues (such as nitrogen purity decline), ensuring the safe and stable operation of the entire production system.
MINNUO, as an experienced nitrogen generator manufacturer, can tailor solutions to your specific working conditions and provide professional technical support at any time. Feel free to reach out for consultation!