PSA (Pressure Swing Adsorption) oxygen generators play an indispensable role in industrial and medical applications due to their high efficiency and convenience in oxygen production. However, prolonged use can lead to overheating issues, causing performance degradation and even shutdowns. This not only affects production efficiency but can also pose a risk to patient safety in medical settings. This article provides an in-depth technical analysis of the causes of overheating in PSA oxygen generators and proposes systematic solutions to help users optimize equipment management.
Long-term operation of PSA oxygen generators can be affected by high temperatures, leading to performance deterioration or shutdowns. The primary causes include poor compressor heat dissipation, cooling system malfunctions, adsorption system anomalies, high-temperature environments, and the absence of temperature control mechanisms. Solutions involve optimizing heat dissipation design, installing intelligent temperature control devices, conducting regular maintenance of cooling and adsorption systems, adjusting operating parameters, and utilizing IoT-based monitoring for fault prevention.

Five Core Causes of Overheating in PSA Oxygen Generators
1. Compressor Overload and Poor Heat Dissipation
The compressor is the core component of a PSA oxygen generator and generates significant heat during operation. If the heat dissipation system is poorly designed or the equipment is placed in an inadequately ventilated environment, compressor temperatures can rise rapidly.
- Cooling fan failure: In dusty working environments, dust accumulation can obstruct fan blades, reducing cooling efficiency. If the fan motor fails, the cooling function ceases entirely.
- Insufficient ventilation space: When installed in confined spaces with blocked cooling vents, heat cannot dissipate effectively, causing internal temperatures to rise continuously.
- Continuous high-load operation: In some factories, PSA oxygen generators are operated 24/7 to meet production demands, leading to prolonged compressor operation beyond thermal limits, resulting in overheating.
2. Cooling System Malfunctions
The cooling system, consisting of the cooler and refrigerant, is essential for temperature control.
- Cooling fan stoppage: Fan failure can result from motor malfunctions or electrical issues such as short circuits or disconnections, preventing proper cooling and leading to temperature spikes.
- Refrigerant leakage: Poor system sealing or component aging can cause refrigerant leaks, significantly reducing cooling efficiency.
- Blocked cooling pipelines: Over time, impurities accumulate in the system, clogging pipelines and hindering refrigerant circulation, thereby impairing heat dissipation.
3. Adsorption System Anomalies
The molecular sieve adsorption tower is the core unit of PSA oxygen generation, and its malfunction can indirectly cause overheating.
- Molecular sieve contamination or failure: Oil or moisture infiltration can contaminate the adsorbent, reducing adsorption efficiency. To maintain oxygen output, the compressor must operate at higher pressure, exacerbating heat generation.
- Valve leakage or blockage: Pneumatic valve failures can cause leaks or blockages, leading to pressure imbalances in the adsorption tower, increasing compressor load, and raising temperatures.
4. Environmental and Operational Factors
- High-temperature environment: In summer or tropical regions, high ambient temperatures limit heat dissipation. For example, in hospitals, emergency rooms and wards demand a high oxygen supply during summer, causing prolonged oxygen generator operation under high ambient temperatures, increasing overheating risks.
- Incorrect parameter settings: Improper pressure threshold settings can lead to frequent compressor startups or overload conditions, intensifying heat generation.
5. Lack or Failure of Temperature Control Systems
Some low-end oxygen generators lack temperature control switches to reduce costs. Even if installed, prolonged use can lead to aging and failure of protective mechanisms, preventing timely shutdowns during overheating and ultimately damaging the equipment.
Systematic Solutions and Implementation Steps
1. Optimizing Heat Dissipation System Design
- Enhancing ventilation design: Ensure at least 30 cm of clearance around the equipment for effective heat dissipation and avoid obstructing cooling vents. During installation, companies should follow standard spacing guidelines to provide an optimal cooling environment.
- Upgrading cooling components: Implement a dual-fan redundancy design so that if one fan fails, the other continues functioning. High-efficiency heat sinks can increase surface area for better heat dissipation.
- Controlling ambient temperature: In high-temperature environments, industrial air conditioners or fans can be installed to reduce surrounding temperatures and improve cooling efficiency.
2. Installing Intelligent Temperature Control Protection
- Using high-precision temperature switches: Select suitable thresholds based on compressor power, such as 135°C shutdown protection and 60°C alarm activation. Industrial-grade temperature switches like the HCET-A model are recommended for precise power-cut protection.
- Integrating multi-level alarm systems: Temperature sensors should continuously monitor compressor, adsorption tower, and cooler temperatures. Upon reaching set thresholds, the system can trigger stage-based alarms, such as visual/audible alerts, automatic frequency reduction, or forced shutdowns, prompting timely intervention.
3. Regular Maintenance and Troubleshooting
- Cooling system checks: Clean cooling fans and cooler filters monthly to prevent dust accumulation. Inspect refrigerant pressure and leakage quarterly to ensure proper cooling system operation.
- Adsorption tower maintenance: Inspect molecular sieve conditions every six months and replace contaminated adsorbents promptly. Test pneumatic valve seals and repair leaks to maintain adsorption system stability.
- Compressor maintenance: Replace lubricant and clean internal carbon deposits annually to minimize frictional heat generation.
4. Optimizing Operational Procedures and Parameter Settings
- Load balancing management: For continuous 24-hour operation, alternating between multiple oxygen generators is recommended to distribute the load and reduce strain on individual units.
- Adjusting pressure parameters: Dynamically set adsorption cycles and pressure thresholds based on ambient temperature to prevent frequent overload operation.
5. Emergency Handling and User Training
- High-temperature alarm response: When a high-temperature alarm is triggered, the equipment should be shut down immediately, and the cooling system inspected. Restart the system only after the temperature drops below a safe level, such as 55°C.
- User training: Operators should be instructed to regularly clean cooling vents, recognize abnormal heat signals, and maintain a log of operational status and maintenance activities.
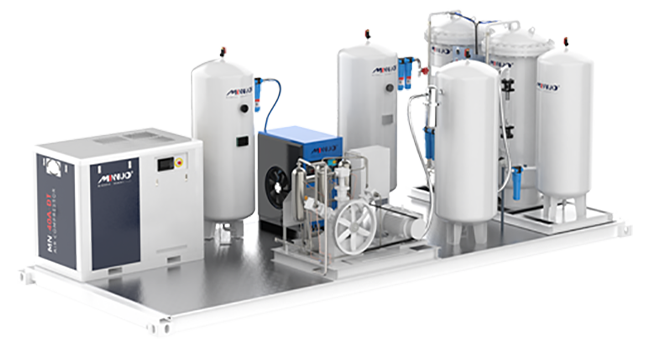
Case Studies
Case 1: Compressor Overheating Protection in an Industrial Oxygen Generator
A chemical plant’s PSA oxygen generator frequently shut down in summer due to high ambient temperatures.
MINNUO implemented several measures, including installing HCET-A temperature switches with a 130°C shutdown threshold. The company also recommended installing industrial air conditioning in the equipment room to maintain ambient temperatures below 30°C. Additionally, adsorption cycle optimization reduced compressor startup frequency.
After implementing these measures, failure rates dropped significantly, and equipment lifespan was extended.
Case 2: Molecular Sieve Contamination Leading to Overheating
A hospital’s oxygen generator experienced persistent high temperatures due to molecular sieve oil contamination, which reduced adsorption efficiency and forced the compressor into sustained high-pressure operation.
MINNUO resolved the issue by replacing the molecular sieve and installing an oil removal filter. This successfully restored normal operating temperatures, ensuring a stable medical oxygen supply.
Preventive Maintenance and Long-term Management Recommendations
1. Establishing a Maintenance Schedule
Divide inspection tasks into weekly, monthly, and quarterly checks, covering key components such as the cooling system, temperature control devices, and adsorption towers. Weekly checks should focus on equipment appearance and cooling vents, monthly tasks on cooling system cleaning, and quarterly inspections on adsorption towers and compressors.
2. Implementing IoT-Based Monitoring
Remote sensors can transmit real-time temperature and pressure data for predictive maintenance. Companies can leverage big data analysis to detect potential issues early and schedule timely maintenance to prevent failures.
3. Using High-Compatibility Components
Prioritize ISO-certified temperature control switches and cooling components to ensure compatibility, improving equipment stability and reliability.
Conclusion
Overheating in PSA oxygen generators must be addressed through design improvements, operational optimizations, and maintenance strategies. MINNUO recommends customized solutions, integrating intelligent temperature control, enhancing heat dissipation, and establishing long-term maintenance to improve stability and ensure efficient, safe operation for industrial and medical applications.