As a core component of cryogenic industrial equipment, liquid nitrogen generators play an irreplaceable role in medical, scientific research, electronics manufacturing, food freezing, and many other fields. However, during prolonged operation, failures may occur due to environmental factors, operation errors, or component aging. This article systematically outlines the common types of failures, diagnostic methods, and solutions for liquid nitrogen generators to help users quickly restore equipment performance and extend service life.
During extended operation, liquid nitrogen generators may encounter temperature instability, abnormal nitrogen consumption, pump malfunctions, and decreased nitrogen purity. These issues can be caused by sensor failures, seal degradation, valve aging, or electrical control system abnormalities. Effective solutions include calibrating or replacing parts, optimizing control parameters, enhancing sealing and insulation, regular cleaning and maintenance of key components, checking circuits, and timely replacement of adsorbent materials.
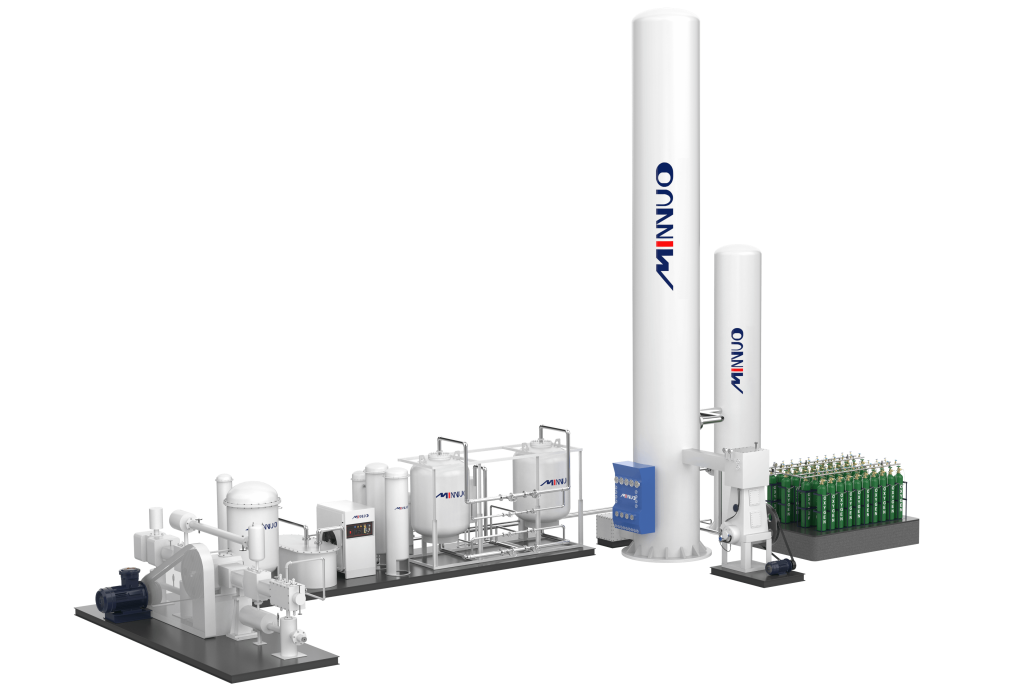
I. Temperature Control Failures
1. Abnormal or Fluctuating Temperature Display
Symptoms
Temperature sensor readings are unstable, and the device cannot maintain the preset low temperature. This may result in an uncontrollable environment for storing biological samples, affecting experimental accuracy or causing a decline in food quality during freezing.
Causes
- Temperature sensor misalignment or damage: During operation, vibrations or external forces may cause sensor displacement, leading to inaccurate temperature readings. Long-term exposure to low temperatures may also damage sensor components.
- Incorrect control system parameter settings: PID parameters are crucial for maintaining stable temperature. If set improperly, the system may fail to respond accurately and timely to changes, resulting in temperature fluctuations.
- Frost blockage on condenser or evaporator: Frost forming on the surfaces can create an insulation layer, impeding heat exchange and reducing cooling efficiency.
Solutions
- Calibrate or replace sensors: Use a multimeter to measure resistance values and compare with standard values. If the deviation exceeds 5%, replace the sensor. For example, in one laboratory, replacing a faulty sensor resolved abnormal temperature readings.
- Optimize control parameters: Fine-tune proportional, integral, and derivative parameters based on the manual. Gradually adjust and monitor temperature response for best performance. Contact technical support for professional advice if needed.
- Clean condenser/evaporator: Power off the unit, gently remove frost using a soft brush, and ensure ventilation is unobstructed. Increase defrost frequency if frost builds up frequently.
2. Abnormally High Liquid Nitrogen Consumption
Symptoms
The refill cycle shortens significantly, raising operating costs and possibly disrupting continuous production.
Causes
- Seal failure in storage tank or pipelines: Aging seals or loosened bolts can lead to nitrogen evaporation and leakage.
- Damaged insulation layer: A compromised insulation layer allows external heat to enter and accelerates evaporation.
- Valve not fully closed or internal leakage: Worn valve cores can prevent full closure, resulting in continuous leakage.
Solutions
- Leak detection: Apply soapy water to joints and welds and look for bubbles. Replace aged seals or tighten bolts (torque: 15–20 Nm). In one food plant, this method resolved fast nitrogen loss.
- Insulation repair: Check polyurethane or vacuum insulation for damage. Use dedicated materials to repair and ensure ≥5 mm thickness.
- Valve inspection: Disassemble and inspect valve cores. Replace worn springs or seals. If issues recur, upgrade to cryogenic-specific valves.
II. Mechanical Component Failures and Maintenance
1. Abnormal Liquid Nitrogen Pump Operation
Common Issues
- Failure to start: May be caused by poor electrical contact, worn motor brushes, or control circuit faults.
- Excessive noise: Damaged bearings, loose impellers, or foreign matter in the pump may cause unusual sounds.
- Reduced vacuum efficiency: Aging seals, blocked exhaust valves, or expired adsorbents can reduce vacuum performance.
Solutions
- Circuit check: Use a multimeter to verify voltage is within ±10%. Check fuses (e.g., 5A/3A) and terminals for oxidation. A research institute once resolved a startup issue by replacing a blown fuse.
- Mechanical maintenance: Every 500 hours, clean the pump, remove impurities, replace lubricant, and tighten impeller screws (torque: 8–12 Nm).
- Replace adsorbents: If nitrogen purity drops below 99.5%, replace molecular sieves or activated carbon. Ensure compressed air oil content is <0.01 ppm during replacement.
2. Blocked Pipelines and Valves
Symptoms
Reduced or interrupted liquid nitrogen flow and abnormal pressure may halt operation.
Causes
- Condensed water or debris blocking pipelines: Water, oil, and particles can accumulate and clog lines.
- Valve freezing: Moisture inside valves can freeze in low temperatures, jamming movement.
Solutions
- Pipe cleaning: Disassemble, rinse with anhydrous ethanol, then purge with dry nitrogen. Test for leaks afterward.
- Valve defrosting: Shut down power and allow natural defrosting. Apply cryogenic lubricant afterward. Avoid forced heating to prevent deformation.
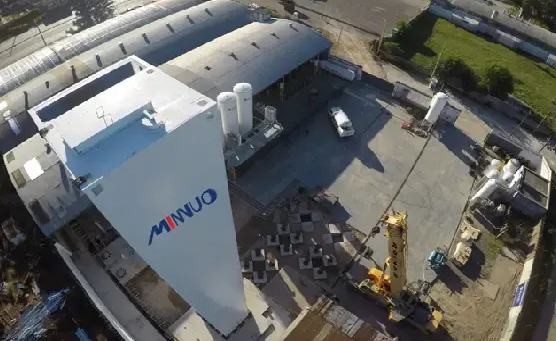
III. Nitrogen Purity and Output Issues
1. Substandard Nitrogen Purity
Causes
- Degraded adsorbents: Aging or contamination lowers adsorption performance.
- High compressed air humidity: Moisture entering the separation tower affects nitrogen purity.
- Blocked air filters: Letting impurities pass through reduces purity.
Solutions
- Replace adsorbents: Replace molecular sieves every 2–3 years. Wear a dust mask during replacement. One electronics plant restored purity by doing so.
- Control air moisture: Use a refrigerated dryer to lower dew point below –40°C.
- Filter replacement: Pre-filters every 3 months; high-efficiency filters every 6 months.
2. Insufficient Nitrogen Output
Symptoms
Flow rate falls below rated output, affecting production schedules.
Causes
- Insufficient compressor pressure: Standard pressure is 0.7–1.0 MPa; low pressure reduces output.
- Membrane fouling or damage: Reduces nitrogen separation efficiency.
- Solenoid valve malfunction: Disrupts gas distribution and output.
Solutions
- Compressor maintenance: Check oil level, clean radiator, and ensure stable exhaust pressure.
- Membrane cleaning/replacement: Clean with special solution. Replace if >10% of fibers are damaged.
- Solenoid valve testing: Measure coil resistance (normal: 50–200Ω). Replace if abnormal.
IV. Electrical and Control System Faults
1. Failure to Start or Sudden Shutdown
Troubleshooting
- Check power input: Voltage should be 380V ±5%, 50Hz.
- Inspect fuses: Replace blown 5A fuses with same type.
- Restart PLC: Check error codes (e.g., E01 = pressure sensor fault) and troubleshoot accordingly.
Preventive Measures
Install voltage stabilizers to guard against power fluctuations. Back up control parameters monthly for quick recovery.
2. Display Malfunction or No Signal
Solutions
- Check ribbon cable: Reconnect to ensure firm contact.
- Replace power module: If indicator lights are off, replace with the same switch power supply (input: 220V, output: 24V DC).
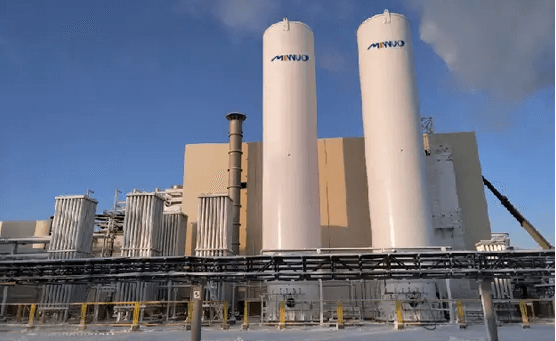
V. Preventive Maintenance and Safety Guidelines
1. Scheduled Maintenance
- Daily: Record liquid level, pressure, and temperature. Drain condensate to avoid pipe blockage.
- Quarterly: Lubricate moving parts, calibrate sensors, and replace filters.
- Annually: Inspect seals and electrical insulation, identify safety risks, and upgrade software for performance and stability.
2. Safety Protocols
- Personal Protection: Wear cryogenic gloves and goggles to avoid frostbite from contact.
- Emergency Response: In case of leaks, ventilate immediately, avoid flames, and reduce nitrogen concentration. For frostbite, soak the area in warm water (40–45°C) without rubbing.
VI. Conclusion
The efficient operation of liquid nitrogen generators depends on accurate fault diagnosis and scientific maintenance strategies. By conducting regular inspections, replacing vulnerable components (such as seals and filters) in time, and optimizing operation procedures, failure rates can be significantly reduced. MINNUO has specialized in gas equipment for over 30 years and boasts a team of expert engineers. If you have any questions, feel free to consult us!