ial production, nitrogen generators, as key equipment for extracting high-purity nitrogen, directly impact production and product quality through their stable operation. Currently, mainstream nitrogen generation technologies include cryogenic air separation, Pressure Swing Adsorption (PSA), and membrane separation. In PSA nitrogen generation systems, solenoid valves are responsible for gas path switching, and their proper functioning is crucial to overall performance. Therefore, studying common solenoid valve faults and their solutions is essential for improving the reliability and stability of nitrogen generation equipment.
The stable operation of the solenoid valve directly affects the nitrogen production rate and purity. The main causes of solenoid valve failure fall into two categories: control failure and valve spool sticking. Control failure of the solenoid valve may be caused by reasons such as a burned-out solenoid coil or a short circuit in the control circuit; valve spool sticking may occur due to impurities in the gas entering the valve body or insufficient lubrication. If a solenoid valve fails and the airflow cannot switch properly, it will prevent the adsorption tower from operating according to the scheduled program, leading to a decrease in nitrogen production and purity. In severe cases, the nitrogen generator will fail to operate normally, affecting the entire production process.
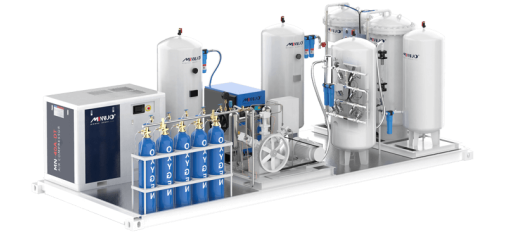
1. Analysis of Core Components in Nitrogen Generation Systems
A nitrogen generator is a device that uses physical separation technology to obtain high-purity nitrogen from air. In PSA nitrogen generation systems, air is compressed by a compressor and then enters a pre-treatment unit to remove oil, water, and impurities. It then flows into adsorption towers filled with molecular sieves. Molecular sieves have a strong adsorption capacity for oxygen, carbon dioxide, and other impurities in the air, allowing nitrogen to be separated and purified. In this process, solenoid valves play a critical role in controlling gas flow direction and switching adsorption towers.
For example, in a dual-tower PSA nitrogen generation system, while one adsorption tower is adsorbing and producing nitrogen, the other undergoes desorption and regeneration. Solenoid valves precisely control the gas flow to alternate the operation of the two towers, ensuring continuous and stable nitrogen production.
The stable operation of solenoid valves directly affects nitrogen output and purity. If a solenoid valve fails, the gas path cannot switch properly, causing the adsorption towers to deviate from their intended operation. This leads to reduced nitrogen output and purity, and in severe cases, the nitrogen generator may cease functioning, disrupting the entire production process.
2. Common Faults and Solutions
2.1 Solenoid Valve Control Failure
2.1.1 Fault Symptoms
During operation, it is common for the control panel to indicate that the solenoid valve has received an activation signal, but the gas path does not switch, resulting in abnormal nitrogen output. This fault severely impacts the nitrogen generator’s operation and may force production lines to halt due to insufficient nitrogen supply.
2.1.2 Diagnostic Process
- Circuit continuity test: Use a multimeter to check the 24V DC power supply for open or short circuits. Abnormal voltage may indicate power line faults or power module damage.
- PLC control module output signal check: Use professional equipment to read the PLC control module’s output signal to confirm if it matches the programmed output. Abnormal signals may indicate PLC program errors or hardware damage.
- Solenoid coil impedance test: Measure the solenoid coil’s impedance, which should be within 22Ω ±10%. Abnormal values suggest coil issues such as inter-turn short circuits or open circuits.
- Check for terminal oxidation: Inspect the solenoid valve terminals for oxidation caused by moisture or corrosion. If oxidation is found, gently sand the terminals to remove the oxidation layer and ensure proper contact.
2.1.3 Solutions
- Use a contact resistance tester to inspect circuit nodes: Ensure all connections are reliable and contact resistance is within normal range. Reconnect or replace components if high resistance is detected.
- Replace the solenoid coil with the same model: If the solenoid coil is damaged, replace it with a compatible model, such as the FESTO 073611 series, known for its stability and reliability.
- Upgrade the control cabinet to IP54 protection: Enhance the control cabinet’s protection level to prevent dust and moisture from affecting the control circuit, reducing the likelihood of control failure.
2.2 Hydraulic Actuator Leakage
2.2.1 Fault Symptoms
During operation, if the pneumatic actuator moves sluggishly, the exhaust port continuously leaks gas, and the cylinder stroke fails to meet standards, it is likely due to hydraulic actuator leakage. This fault causes inaccurate solenoid valve operation, affecting gas path switching and reducing the nitrogen generator’s efficiency.
2.2.2 Technical Parameter Checks
- Operating pressure range: The normal operating pressure range for the solenoid valve in a nitrogen generator is generally between 0.4 and 0.7 MPa. Using professional pressure testing equipment to monitor the system pressure, if the pressure exceeds the normal range, it could cause damage to the valve body pneumatic actuator, leading to leakage.
- Allowable leakage rate: According to standards, the solenoid valve’s leakage rate should be less than 3% of the rated flow. Use flow testing equipment to measure leakage and determine if it exceeds the limit.
2.2.3 Solutions
- Use helium mass spectrometry to locate leaks: This high-precision method quickly identifies leakage points. Inject helium into the system and use the detector to pinpoint leaks.
- Replace with imported polyurethane seals: Once leaks are located, replace the seals with high-quality components like the Parker Hannifin P2U series, known for excellent sealing and wear resistance.
- Calibrate cylinder stroke: After replacing seals, calibrate the cylinder stroke to ensure it is within ±0.5 mm tolerance, restoring accurate actuator operation.
2.2.4 Maintenance Recommendations
To extend the hydraulic actuator’s lifespan, replenish lubricant (Molykote EM-30L) every 2,000 operating hours. Lubrication reduces friction, minimizes wear, and enhances reliability.
2.3 Valve Spool Sticking
2.3.1 Fault Symptoms
When the solenoid valve is energized, the normal switching response time is usually between 50ms and 100ms. If it exceeds 200ms and abnormal vibration or noise occurs, it typically indicates a sticking fault of the valve spool. Valve spool sticking can prevent the solenoid valve from switching the airflow promptly and accurately, affecting the normal operation of the nitrogen generator and potentially causing safety accidents.
2.3.2 Root Cause Analysis
- Excessive oil and moisture in compressed air: Nitrogen generators require high-quality compressed air with a dew point of -40°C and oil content below 0.01 ppm. Excessive oil and moisture can cause oil and water buildup inside the valve, increasing friction and leading to spool sticking.
- Internal particle contamination: According to ISO 8573-1 Class 2 standards, the valve interior must remain clean. Airborne particles and dust can accumulate between the spool and seat, obstructing movement and causing sticking.
2.3.3 Solutions
- Disassemble and ultrasonically clean the valve body: Remove the valve spool from the valve body and place it into an ultrasonic cleaning machine for cleaning. Set the cleaning frequency to 40kHz, and prepare the cleaning solution by mixing it with water in a 1:9 ratio. The high-frequency vibrations from the ultrasound effectively remove oil, impurities, and other contaminants from the valve spool and valve seat.
- Replace with a 0.01 μm precision filter: Install a high-efficiency filter to prevent particles from re-entering the valve.
- Apply PTFE coating to the spool: For worn spools, use PTFE coating to restore surface smoothness, reduce friction, and improve movement.
2.3.4 Preventive Measures
To prevent spool sticking, install a two-stage refrigerated dryer and an activated carbon oil filter. The dryer reduces the compressed air’s dew point, while the oil filter removes oil, ensuring air quality meets operational requirements.
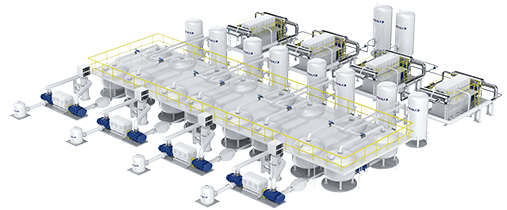
3. System Optimization and Intelligent Maintenance
3.1 Implementing Preventive Maintenance
- Establish a 500-hour inspection cycle: Conduct comprehensive inspections every 500 hours, covering the solenoid valve’s appearance, connections, operation, and electrical performance.
- Use vibration analyzers to monitor solenoid valve operation: Analyze vibration signals to detect abnormalities and provide early warnings.
- Inspect valve cavities with industrial endoscopes: Regularly check internal components for wear and damage.
3.2 Intelligent Upgrade Solutions
- Install IoT sensors for real-time monitoring: Monitor coil temperature, actuation count, and pressure fluctuations, transmitting data to a remote center for real-time oversight.
- Build a predictive maintenance platform: Use BP neural networks to analyze historical data and predict potential faults, enabling proactive maintenance.
- Configure redundant control systems: Use dual solenoid valves in parallel to ensure uninterrupted gas path switching if one valve fails.
4. Professional Technical Support System
As a leader in gas separation, MINNUO offers a comprehensive four-level technical support system:
4.1Rapid response
Eight service centers nationwide provide technical responses within four hours.
4.2Spare parts network
Over 2,000 solenoid valve components are stocked, ensuring delivery within 48 hours.
4.3Customized upgrades
Based on the customer’s specific requirements, we offer valve body material upgrade services, such as upgrading from 316L stainless steel to Hastelloy C276. This upgrade is particularly necessary in the following special scenarios:
- Highly corrosive environments: When nitrogen generators are used in industries like chemicals and pharmaceuticals, where the gases being processed contain large amounts of corrosive substances such as chlorine, hydrochloric acid, sulfuric acid, etc., ordinary 316L stainless steel cannot resist the corrosion of these strong corrosive substances. This can lead to valve body corrosion and damage, affecting normal equipment operation. Hastelloy C276, with its excellent corrosion resistance, can maintain stable performance in such harsh environments, ensuring the long-term stable operation of the nitrogen generator.
- High temperature and high pressure conditions: In certain special industrial processes, such as petroleum refining and high-pressure synthesis, nitrogen generators need to operate under high temperature and high-pressure conditions. High temperatures can degrade the performance of metal materials, and the strength and corrosion resistance of 316L stainless steel weaken at high temperatures, potentially failing to meet long-term stable operation requirements. Hastelloy C276 not only has excellent high-temperature resistance but also maintains superior strength and corrosion resistance under high temperature and high-pressure conditions, ensuring the solenoid valve operates normally in these extreme conditions.
4.4Full lifecycle management:
Use the Equipment Health Management System (EHM V3.0) to monitor and maintain solenoid valves throughout their lifecycle.
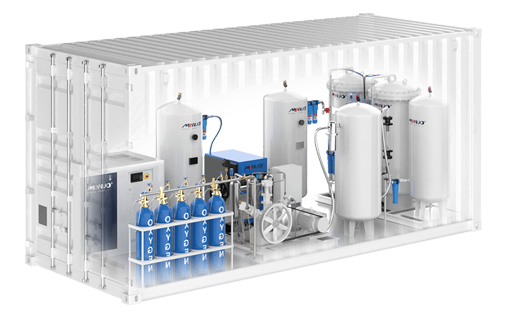
5. Conclusion
By thoroughly analyzing common faults, particularly those related to solenoid valves in nitrogen generators, we have proposed systematic fault-handling solutions and preventive maintenance strategies. Implementing these measures, which focus on optimizing the performance and longevity of solenoid valves, can significantly enhance the reliability of nitrogen generation equipment.
For reliable products, consult MINNUO today!