As we know, nitrogen generators are widely used in various industries such as chemicals, electronics, food, and pharmaceuticals. However, over time, these generators are inevitably subjected to various faults, which can seriously disrupt production. Therefore, understanding common faults in nitrogen generators and their effective troubleshooting methods is of significant practical importance.
Common faults in nitrogen generators include issues such as adsorption tower blockages, unstable air pressure, and nitrogen purity decline. Typical solutions to these problems include regular cleaning and replacement of adsorbents, checking and adjusting the pressure system, and ensuring the normal operation of membrane components. Additionally, regular equipment maintenance and servicing are key measures to prevent faults from occurring.
Overview of the Working Principles of Nitrogen Generators
Pressure Swing Adsorption (PSA) Principle
PSA nitrogen generators use adsorbents that have different adsorption capacities for various gases under different pressures to achieve nitrogen separation. Under high-pressure conditions, adsorbents strongly adsorb impurities such as oxygen and carbon dioxide, while nitrogen is relatively unaffected and flows out as product gas. Once the adsorbent becomes saturated, the pressure is reduced to desorb the impurities and restore the adsorbent’s ability, preparing it for the next cycle.
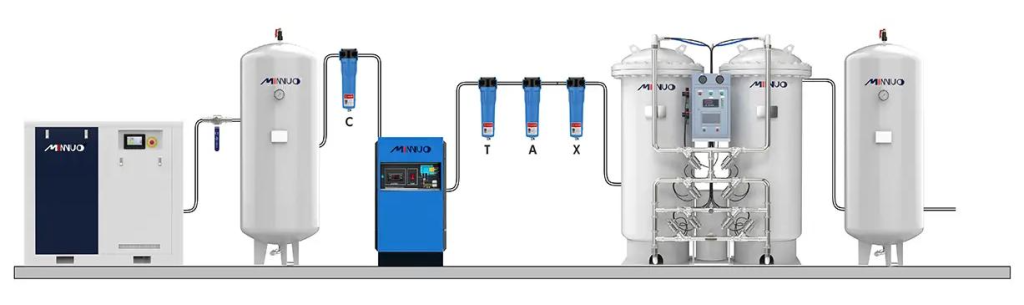
Membrane Separation Principle
Membrane separation nitrogen generators separate gases based on the different solubility and diffusion rates of gases through polymer membranes. Under a certain pressure, small molecules like oxygen and water vapor pass through the membrane more quickly, while nitrogen molecules are less likely to pass through, thereby obtaining nitrogen on the other side of the membrane. This technology is simple, easy to operate, and is typically used when nitrogen purity requirements are not very high.
Common Faults and Troubleshooting Methods
Power-Related Faults
The Power Switch Is Turned On, But The Main Power Board Does Not Light Up.
Possible Causes:
- Power cord not connected properly: This is a common cause of power failure. Frequent movement or vibration of the equipment may loosen the power cord.
- Power fuse is blown: Typically caused by circuit overloads or short circuits. The fuse will blow when the current exceeds the rated value to protect other components.
- Power switch failure: Long-term use or quality issues may damage internal contacts, preventing normal circuit connection.
Troubleshooting:
- Check the power cord connections and ensure it is securely plugged in. Use a multimeter to check the continuity of the power cord and replace it if damaged.
- Replace the blown fuse with one of the same specification and model, and always ensure the power is off before replacement to avoid electric shock.
- For a damaged power switch, first identify the type of fault. If it’s a contact issue, repair it; if it can’t be repaired, replace it with a new switch and test its operation after installation.
The Process Queue Indicator Does Not Light Up and The Process Runs Abnormally.
Possible Causes:
- Connection issues: Broken wires, short circuits, or poor contacts may disrupt signal transmission, causing abnormal process queue displays or failure in process execution.
- Faulty fast controller: The core control component of the nitrogen generator, a controller, may fail due to hardware damage, software errors, or incorrect parameter settings.
Troubleshooting:
- Perform a thorough inspection of the wiring, check the resistance of the wires using a multimeter, and find any breaks or short circuits. Reconnect loose contacts, and replace aged or damaged wires.
- Inspect the fast controller for hardware damage such as burned chips or bulging capacitors. If no hardware issue is found, reset the controller to restore default settings. If the problem persists, contact the manufacturer for remote diagnostics or onsite repair..
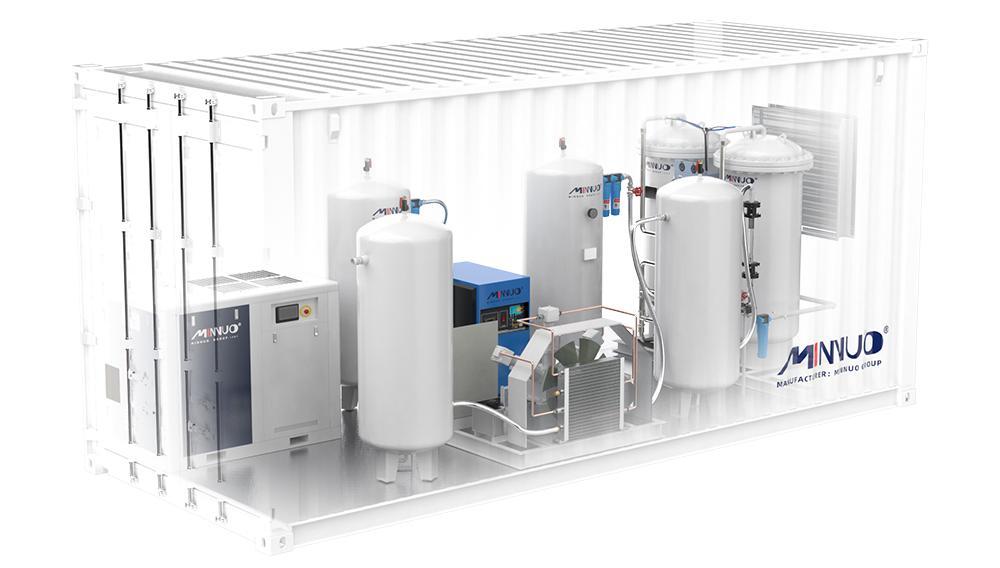
Pressure-Related Faults
Left Absorption Tank Pressure Does Not Reach Normal Value During The Left Adsorption Process
Cause of Fault:
- The pilot air pressure is not set. Pilot air plays an essential role during the adsorption process of the nitrogen generator. It helps drive the adsorbent to capture impurities in the gas. Without setting the pilot air pressure, the adsorption process cannot proceed correctly, resulting in the left absorption tank pressure not rising.
- The control valve of the left suction is damaged. The solenoid valve controls the flow of gas and can fail due to issues such as a stuck valve core or burned coil. If the control valve of the left suction is damaged, it cannot open or close properly, affecting the left absorption tank’s pressure.
- The left suction valve is not open. This could be due to a fault with the valve itself, such as poor sealing or a rusted valve stem, or due to failure of the control signal to the valve, preventing its operation.
Troubleshooting:
- Set the pilot air pressure to half the air pressure as required in the equipment manual. Use specialized pressure measuring instruments to ensure the setting is accurate.
- For damaged solenoid valves, first check if the valve core is stuck, and clean and lubricate it if necessary. If the valve core is not the issue, check the coil for burn-out using a multimeter. If the resistance is infinite, the coil is burned out and needs to be replaced with a matching solenoid valve.
- Inspect the left suction valve for visible damage. If the valve seal is not tight, replace the sealing gasket; if the valve stem is rusted, perform rust removal and lubrication. Also, check if the control signal is being transmitted correctly to the valve; if the signal transmission is faulty, inspect the related control circuits and output ports.
Uneven Pressure Between Left and Right Absorption Tanks During Equalization
Cause of Fault:
- The solenoid valve controlling equalization is damaged. As with other solenoid valve faults, issues such as a stuck valve core or burned coil could prevent the equalization solenoid valve from functioning, affecting the pressure equalization between the two absorption tanks.
- The upper and lower equalization valves are not open. These valves balance the pressures of the left and right absorption tanks during the switching process of the adsorption tower. If the equalization valves are not open, pressure cannot be balanced, resulting in uneven pressures between the two tanks.
Troubleshooting:
- Repair or replace the solenoid valve controlling equalization. During maintenance, disassemble the solenoid valve to check for any damage to the valve core, spring, etc., and replace or repair any damaged parts. If the valve cannot be repaired, replace it with a new one and adjust it to ensure normal operation.
- Inspect the upper and lower equalization valves for obstructions. If there are foreign objects, clear them away. Also, check if the valve’s actuating device is functioning correctly, such as verifying that there is no air leakage from the cylinder or damage to the electric actuator. Replace or repair any faulty actuating devices. After checking and repairing the equalization valves, perform an equalization test to ensure the pressure between the two absorption tanks is balanced.
Right Absorption Tank Pressure Does Not Reach Normal Value During The Right Suction Process
Cause of Fault:
- The solenoid valve controlling right suction is damaged, similar to the left suction solenoid valve failure.
- The right suction valve is not open, which could be due to faults in the valve itself or issues with the control signal transmission.
Troubleshooting:
- Repair or replace the solenoid valve controlling right suction, following the same steps as for the left suction valve.
- Check the associated valve in the piping to ensure it opens freely and seals well. If there is an issue with the valve, repair or replace it promptly. Also, inspect the connections to ensure there are no loose fittings or air leaks.
Silencer Does Not Stop Discharging While Suction Is Active, and Absorption Tank Pressure Does Not Rise
Cause of Fault:
- The return air valve is too open. The position of the return air valve affects the pressure balance in the adsorption tank. If the valve is too open, it may cause excessive gas backflow, preventing pressure buildup in the adsorption tank and resulting in continuous exhaust from the silencer.
- The solenoid valve is leaking. A leaking solenoid valve may cause gas to flow through unintended paths, disrupting the pressure buildup in the adsorption tank.
- The pressure equalization valve is leaking. The pressure equalization valve plays a crucial role during equalization, and a leak here may prevent stable pressure, affecting the pressure buildup in the adsorption tank.
- Air leak from a disassembled valve. After maintenance or disassembly, if the valve is not tightly closed, air leakage can occur, impacting the normal operation of the adsorption tank.
Troubleshooting:
- Adjust the return air valve opening. Gradually adjust the valve’s opening while observing the pressure in the adsorption tank and the silencer’s exhaust. Find the optimal opening where the pressure rises correctly and the silencer stops discharging abnormally.
- Repair or replace any leaking solenoid valves. Ensure their seals are intact, and replace any faulty seals or the entire solenoid valve if necessary.
- Repair or replace piping valves, especially the pressure equalization and disassembly valves. Use pressure testing to verify their sealing, and replace or repair any leaking valves. For disassembly valves, ensure they close tightly, using sealant if necessary to enhance their sealing.
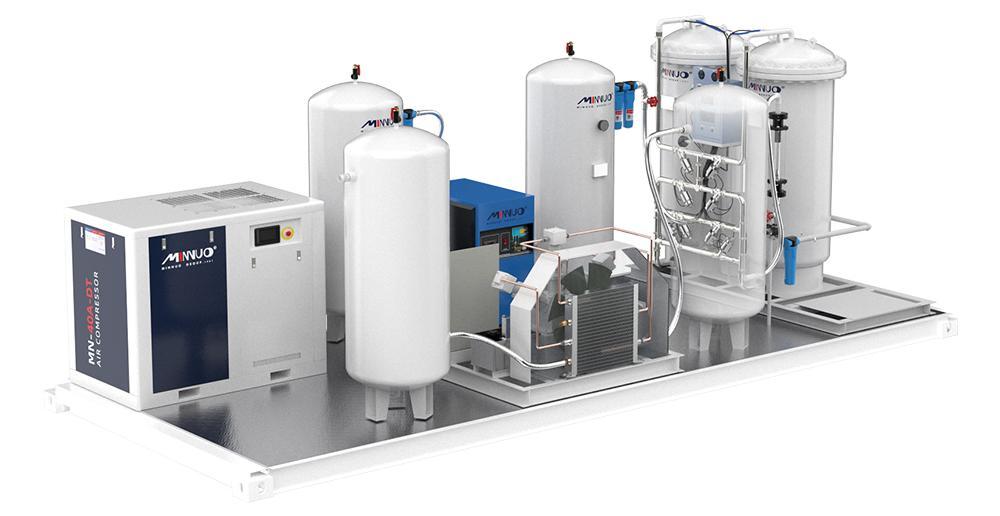
Other Faults
Inaccurate Display of Nitrogen Measurement Instrument
Cause of Fault:
- Air contamination. Leaks in the pipe connections or equipment may allow air to mix with nitrogen, resulting in inaccurate readings from the nitrogen measurement instrument.
- Oxygen sensor damage. The oxygen sensor is a critical component of the nitrogen measurement instrument. Prolonged use or environmental factors may cause sensor degradation, affecting measurement accuracy.
Troubleshooting:
- Inspect the oxygen electrode and the measurement system. Ensure pipe connections are properly sealed, and repair any leaks. Calibrate the system if necessary to maintain accurate readings.
- Replace the oxygen electrode if it is damaged. After replacement, recalibrate the nitrogen measurement instrument to ensure its readings are accurate.
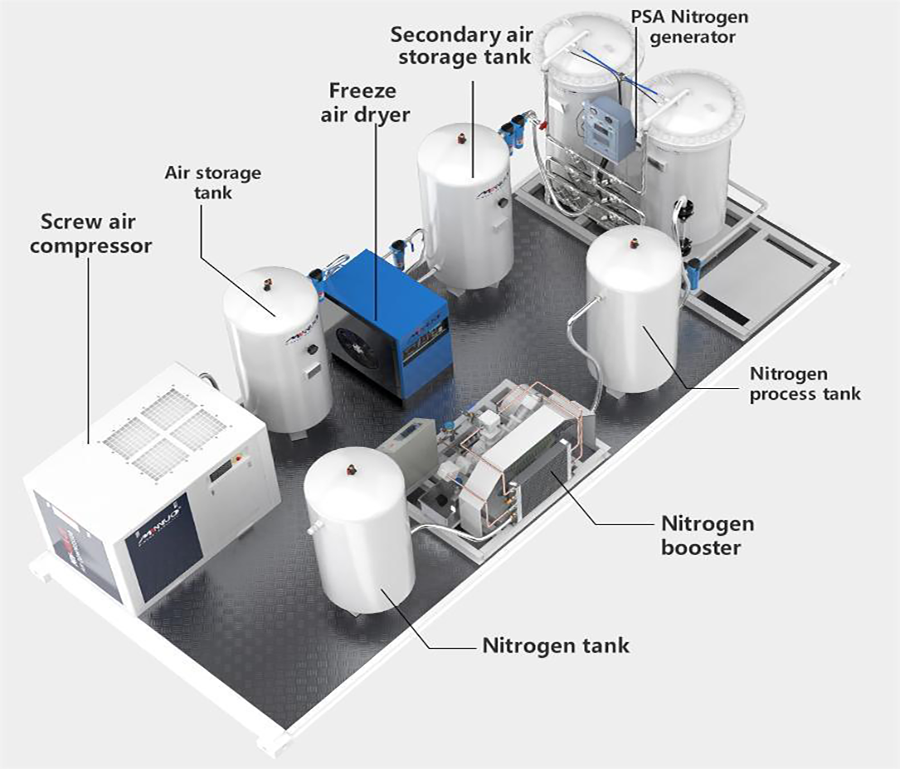
Operating Notes for Nitrogen Generators
Flow and Pressure Adjustment
Adjust the regulator in front of the flow meter and the nitrogen output valve behind the flow meter according to the air pressure and consumption. Once nitrogen reaches the standard, do not adjust the flow or pressure arbitrarily, as it can lead to issues like reduced adsorption effectiveness and valve damage, affecting the generator’s normal operation.
Valve Management
Do not adjust any other valves arbitrarily. These valves are calibrated at the factory to ensure the coordinated operation of the system. Arbitrary adjustments may disrupt the system’s pressure balance and gas flow distribution, causing faults or reduced nitrogen purity.
Electrical and Piping Component Handling
Do not move electrical components inside the control cabinet or disassemble/install air piping valves without professional guidance. Moving electrical components may cause wiring issues, while improper handling of valves may result in air leakage.
Pressure Gauge Inspection and Record-Keeping
Regularly inspect the nitrogen generator’s pressure gauges and maintain a record of pressure changes. Sudden increases or decreases in pressure could indicate blockages or leaks, helping in the early identification of faults.
Monitoring Equipment Operating Parameters
Regularly monitor outlet pressure, flow meter readings, and equipment status displays. Abnormalities in these parameters may indicate a fault in the system.
Equipment Maintenance
Perform regular maintenance according to the technical requirements for the compressor, cooler, and filter. This ensures the stable operation of key components like the compressor and cooler, which are essential for the nitrogen generator’s performance.
Daily Record Keeping
Maintain accurate daily logs detailing equipment operation, including start/stop times, pressure, flow, temperature, and maintenance records. This helps identify potential issues early and provides useful data for troubleshooting and preventive maintenance.
Conclusion
Nitrogen generators are crucial in industrial production, and their stable operation directly impacts efficiency. By understanding common faults and troubleshooting methods, operators can reduce failure rates, extend equipment life, and improve output and quality.
MINNUO, as a professional gas equipment manufacturer, has always been committed to providing high-quality nitrogen generators and other gas-related products. If you encounter any issues, please contact our technical support team for detailed assistance.