Removing hydrogen sulfide (H₂S) is a crucial step in biogas treatment and biomethane production. Hydrogen sulfide is highly corrosive, damaging equipment and disrupting downstream processes, which raises maintenance costs and operational risks. This article explores the use of oxygen generators in biogas treatment, focusing on their working principle, specifications, and technical benefits.
The oxygen generator used for biogas treatment generates high-purity oxygen on-site through Pressure Swing Adsorption (PSA) technology to efficiently remove hydrogen sulfide, ensuring the quality of biomethane and equipment safety. Compared to traditional methods like iron salts or activated carbon, oxygen-based hydrogen sulfide removal is economical, eco-friendly, and highly efficient. The oxygen generator employs an advanced automated control system and modular design, providing a flexible and stable oxygen supply, with a purity of 90%-95%, optimizing the removal process and enhancing the efficiency of biomethane production.
What Are Biogas and Biomethane?
Biogas is a renewable energy source produced by the anaerobic digestion of organic matter, such as agricultural waste, urban organic waste, and sewage sludge. Its main components are methane (CH₄, about 50-70%) and carbon dioxide (CO₂, about 30-50%), along with trace amounts of hydrogen sulfide (H₂S), ammonia (NH₃), and water vapor. Methane, being a high-energy fuel, makes biogas a valuable energy source for power generation and heating.
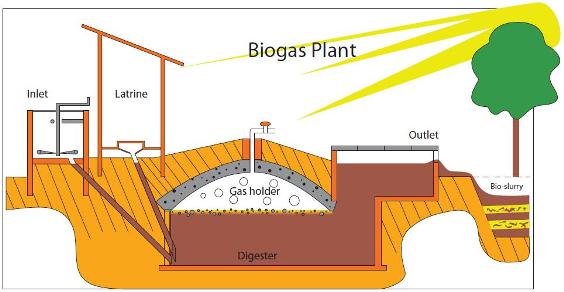
Biomethane is a highly purified form of methane obtained from biogas, with a methane content typically above 95%. By removing impurities such as carbon dioxide, hydrogen sulfide, and water from biogas, biomethane meets natural gas quality standards, often termed “green natural gas.” Biomethane can be injected into natural gas networks, used as a vehicle fuel, or applied in industrial processes, making it a clean and renewable energy option.
Why Use Oxygen to Remove Hydrogen Sulfide?
Hydrogen sulfide removal is key to ensuring the safety of equipment and the quality of biomethane during biogas treatment. Using oxygen to remove hydrogen sulfide offers several distinct advantages compared to traditional methods like iron salts or activated carbon—it is more efficient and cost-effective.
Principle and Advantages of Oxygen Treatment
Oxygen reacts with hydrogen sulfide to form elemental sulfur and water, a simple reaction without secondary pollution. The aerobic reaction oxidizes hydrogen sulfide, with non-toxic by-products that are easy to handle, reducing environmental impact.
Comparison with Other Methods
Traditional hydrogen sulfide removal methods include iron salt precipitation and activated carbon adsorption. These approaches consume large amounts of chemicals or adsorbents, which need frequent replacement, raising operating costs. Activated carbon, in particular, loses its adsorption capacity over time, requiring regular replacement. Oxygen-based hydrogen sulfide removal is more economical, environmentally friendly, and minimizes maintenance and operational complexity.
Cost and Maintenance
On-site oxygen generation provides a stable supply without transport, eliminating uncertainties related to external oxygen supply. The oxygen removal process can integrate seamlessly with biogas production, reducing extra equipment burden and achieving low-cost, high-efficiency operations.
How an Oxygen Generator Works
The core technology of an oxygen generator is based on Pressure Swing Adsorption (PSA). PSA utilizes physical adsorbents (usually zeolite molecular sieves) that selectively adsorb gases under varying pressures, separating oxygen from nitrogen in compressed air.
The PSA process is a cyclic pressure swing. First, dry compressed air, consisting of approximately 78% nitrogen and 21% oxygen, is fed into the system. The zeolite adsorbs nitrogen preferentially at high pressure, allowing oxygen to be enriched and separated. When the pressure is reduced, the nitrogen is released, regenerating the adsorbent.
This adsorption and desorption cycle continues, ensuring a continuous supply of high-purity oxygen. Our oxygen generators also feature advanced Variable Cycle Saver (VCS) technology, which adjusts production parameters automatically under low load or variable oxygen demand, significantly reducing energy consumption. Compared to traditional oxygen systems, VCS can reduce energy consumption by up to 70% under low-load conditions.
Steps to Convert Biogas into Biomethane Using an Oxygen Generator
Compressed Air Preparation
The first step is to compress and dry ambient air to remove moisture and impurities, ensuring the stability of the subsequent adsorption process.
Oxygen-Nitrogen Separation
Through PSA technology, compressed air is separated into oxygen and nitrogen. The zeolite adsorbent captures nitrogen at high pressure, resulting in high-purity oxygen (90%-95%).
Hydrogen Sulfide Removal
The purified oxygen is injected into the biogas, where it reacts with hydrogen sulfide to produce elemental sulfur and water, effectively reducing hydrogen sulfide levels. This method is straightforward, without secondary pollution, significantly cutting subsequent treatment costs.
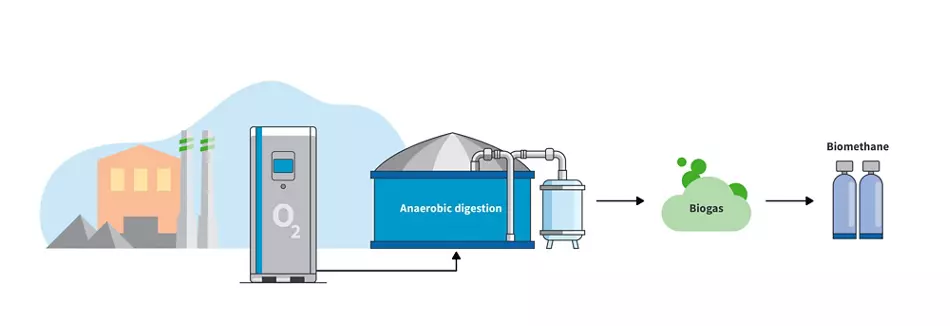
How to Select an Appropriate Oxygen Generator Specification
Choosing the right oxygen generator specification for a biogas plant involves several considerations to ensure tight integration with the production process. Key factors include:
- Biogas Flow Rate and Hydrogen Sulfide Concentration: Determine the total flow rate of the biogas and the initial concentration of hydrogen sulfide to establish the required oxygen flow rate and reaction capacity.
- Oxygen Purity Requirements: In hydrogen sulfide removal, the oxygen purity should be between 90%-95%. This range ensures effective oxidation while avoiding unnecessary costs. Low purity may reduce efficiency, whereas overly high purity could increase safety risks, particularly in large-scale biogas plants where higher purity oxygen might increase explosion risks.
- Number of Digesters and Concurrent Oxygen Demand: If multiple digesters are used simultaneously, the oxygen generator must support concurrent operation.
- Modular Plug-and-Play Equipment: For users with limited space or without a dedicated plant, a modular plug-and-play solution might be the best choice, saving on installation costs and allowing for quick deployment.
- Precision of Oxygen Control: Precise control of oxygen input is essential in biomethane production. An advanced oxygen generator should include an intelligent flow control system to adjust oxygen supply based on real-time conditions.
Advantages of MINNUO Oxygen Generators
Our oxygen generators use industry-leading PSA technology and high-efficiency zeolite adsorbents to ensure efficient and stable oxygen supply. We offer customized solutions tailored to biogas plant needs. Key advantages include:
- High Efficiency and Energy Savings: With VCS technology, our oxygen systems reduce energy consumption effectively during low oxygen demand, helping customers lower operational costs. Compared to traditional equipment, our generators reduce energy costs by 70% under low-load conditions.
- Intelligent Control: Our systems feature advanced automation to monitor oxygen purity, flow, and pressure in real-time, ensuring process stability and safety. They utilize Siemens PLC control systems, providing precise and stable control for complex processes.
- Modular Design: The modular configuration of our oxygen generators supports quick assembly for various applications, from small to large-scale biogas plants. All components are sourced from leading brands like Schneider Electric, ensuring equipment reliability.
- High-Quality Components: High-quality zeolite adsorbents ensure oxygen separation efficiency meets international standards. The core compressors use Atlas Copco units, known for excellent energy efficiency and durability.
- Compliance with International Standards: Our oxygen generators meet ISO 9001 and ISO 14001 certifications for quality and environmental management, ensuring high standards in production. Oxygen purity is precisely controlled between 90%-95% to meet various industrial needs.
Our oxygen systems not only provide stable, efficient oxygen but also optimize the hydrogen sulfide removal process, ensuring efficient and environmentally friendly biogas treatment. We work closely with clients to deliver custom design and installation services, ensuring optimal system integration.
By partnering with us, clients not only receive high-quality oxygen equipment but also benefit from professional technical support and maintenance services, ensuring optimal operation throughout the system’s lifecycle.
Conclusion
Oxygen generators play an irreplaceable role in biogas treatment and biomethane production. By efficiently removing hydrogen sulfide, they significantly enhance biogas utilization while reducing operating costs and environmental risks. With advanced technology and exceptional service, MINNUO is committed to providing the highest quality oxygen solutions for the biogas treatment industry.
If you have questions about selecting an appropriate oxygen system or process optimization, MINNUO‘s team is here to offer technical support and consultation. Please reach out to us, and let’s advance the efficient and sustainable use of biogas resources together.