In the modern industrial system, oxygen, as a crucial industrial gas, is widely used in numerous fields such as steel smelting, chemical production, and medical care. With the continuous growth in the demand for oxygen across various industries and the increasing requirements for the economy and environmental protection of the oxygen production process, the Vacuum Pressure Swing Adsorption (VPSA) oxygen production process has attracted significant attention due to its unique technical advantages. The VPSA process can achieve efficient oxygen production with relatively low energy consumption and features flexible operation and simple equipment maintenance. In-depth research on its process flow is of great significance for improving the level of oxygen production technology and promoting the development of related industries.
The VPSA oxygen production process includes four steps:Air compression: Air, filtered in two stages, is pressurized by the fan. An end cooler may be added and air can be vented.Vacuum pumping: The rotary blower, with sealing water, creates vacuum. Exhaust gas and vapor are separated, then vented and drained.VPSA process: Two beds alternate. Pressurized air in adsorption bed separates oxygen. After saturation, vacuum pumping regenerates. Product oxygen is stored and flow balanced.Product delivery: Compressor pressurization depends on pipeline pressure. It has a cooler and controls flow for stable operation.
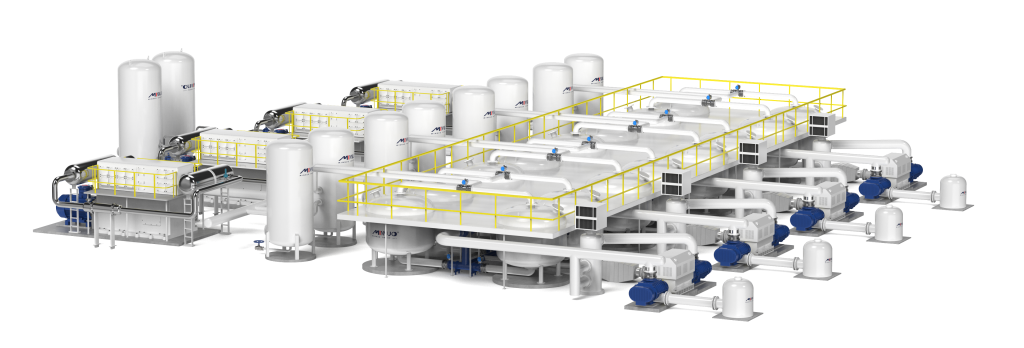
VPSA oxygen production process
Air Compression
Filtration technology principle and equipment selection
The air enters two-stage raw material air filters before entering the raw material fan, using filtering media with different precisions. The primary filter usually adopts a coarse filter screen, which can effectively intercept larger particle-sized pollutants in the air, such as dust and sand grains, preventing them from entering the fan and causing mechanical wear. The secondary filter uses finer filtering materials, such as fiber filter paper or microporous membranes, to further remove tiny particles and some gaseous pollutants, ensuring that the air entering the adsorption bed has a relatively high cleanliness. The selection of filters needs to comprehensively consider factors such as local air quality, inlet air flow, filtration efficiency requirements, and maintenance costs.
The design of the inlet silencer is based on acoustic principles, using sound-absorbing materials and special structures, such as porous sound-absorbing panels and resonance cavities, to effectively reduce the airflow noise generated when the air enters the fan. This can not only improve the working environment but also avoid the interference of noise on the operation stability of the fan and surrounding equipment.
Performance and control strategy of the raw material fan
As the core equipment for air compression, the performance parameters of the raw material fan are crucial to the entire oxygen production system. The air volume and air pressure characteristic curves of the fan determine its operating efficiency and conveying capacity under different working conditions. In the VPSA process, the fan needs to pressurize the air to 63 kPa (gauge pressure). This pressure value is set based on the requirements of the subsequent VPSA process for the inlet air pressure to ensure that the adsorption bed can carry out oxygen separation operations within an appropriate pressure range.
To ensure the stable operation of the fan, an advanced control system is usually equipped. This system monitors parameters such as the inlet and outlet pressures, temperature, and rotational speed of the fan in real-time and automatically adjusts the rotational speed of the fan through technical means such as variable frequency speed regulation according to changes in the system load, thereby precisely controlling the output air volume and pressure. When the outlet pressure exceeds the set value, the control system responds promptly and opens the vent valve to vent the excess air to maintain the stability of the system pressure and prevent damage to the equipment caused by excessive pressure.
Optimization of the venting and cooling system
The design of the venting system aims to cope with fluctuations in the outlet pressure of the fan and changes in the air demand of the adsorption bed. The selection and installation position of the vent valve are carefully designed to ensure smooth airflow during the venting process and reduce the impact of pressure shocks on the system. Meanwhile, the diameter and length of the vent pipe need to be reasonably calculated according to the venting flow to reduce the venting resistance and improve the venting efficiency.
The application of the end cooler is based on the thermodynamic principle in the air compression process. The temperature of the air will increase significantly after being compressed by the fan, which will not only reduce the adsorption performance of the adsorbent but also may affect the service life of the equipment. The end cooler adopts efficient heat exchange technologies, such as shell-and-tube or plate heat exchangers, and exchanges heat with the cooling medium (such as water or air) to cool the compressed air to an appropriate temperature range. The flow and temperature control of the cooling medium are the key factors for optimizing the cooling effect and need to be precisely adjusted according to parameters such as the inlet air temperature, flow, and the required cooling temperature.
Vacuum Pumping
Technical characteristics of the vacuum blower and the sealing water system
The rotary blower exhibits unique technical advantages in the vacuum pumping process. It has a compact structure, a large pumping capacity, and a high vacuum degree, which can meet the vacuum degree requirements (about 56 kPa) for the desorption of the adsorption bed in the VPSA process. Inside the blower, the sealing performance between the rotor and the casing is crucial for maintaining the vacuum degree. The sealing water system set at each stage inlet forms a liquid seal, effectively preventing gas leakage and improving the vacuum efficiency of the blower.
The sealing water not only plays a sealing role but also participates in heat exchange as a cold source. During the operation of the blower, water vapor and exhaust gas will exchange heat with the sealing water when passing through the blower, causing partial condensation of the water vapor and reducing the water content in the exhaust gas, which is beneficial to the subsequent separation and treatment of the exhaust gas. The water quality and temperature control of the sealing water have a significant impact on the performance and service life of the blower and need to be regularly monitored and maintained to ensure that they meet the equipment operation requirements.
Innovation in exhaust gas separation and venting technology
The separation silencer adopts the design principle combining acoustics and fluid mechanics. The internal structure design enables the exhaust gas flow to reduce noise through acoustic reflection and absorption materials when passing through the silencer, and on the other hand, realizes the efficient separation of exhaust gas and water vapor through a special flow channel design. The exhaust gas is vented from the top of the silencer, and the position and shape of its vent port are optimized to ensure smooth exhaust gas emission and reduce the impact on the surrounding environment.
The bottom drainage system adopts an automatic drain valve or a liquid level control system, which can timely drain the separated water to prevent the accumulation of water from affecting the separation effect and equipment operation. The material selection of the drainage system needs to consider the corrosiveness of the wastewater to ensure long-term stable operation. In addition, the discharged wastewater can be further treated and recycled according to environmental protection requirements.
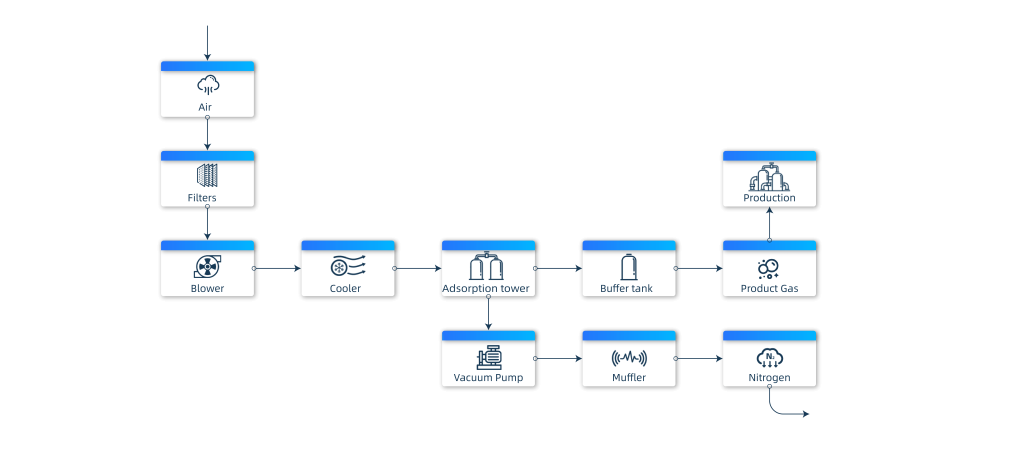
VPSA Process
Oxygen separation mechanism and adsorbent characteristics
The oxygen separation in the VPSA process is based on the principle of selective adsorption of different gas molecules by the adsorbent. Commonly used adsorbents, such as molecular sieves, have specific microporous structures, and the pore size matches the diameter of the adsorbed molecules. During the adsorption stage, when the air passes through the adsorption bed under a certain pressure, molecules such as nitrogen, water, carbon dioxide, and hydrocarbons can be adsorbed in the micropores of the adsorbent because their molecular diameters are close to or slightly smaller than the micropore size of the molecular sieve, while oxygen molecules and argon molecules have relatively smaller diameters and are not easily adsorbed, thus realizing the separation of oxygen and other impurity gases.
The setting that the adsorption pressure generally does not exceed 55 kPa is determined on the basis of comprehensively considering factors such as the adsorption performance of the adsorbent, the oxygen recovery rate, and energy consumption. Within this pressure range, the adsorbent can achieve a good oxygen separation effect while ensuring a relatively high adsorption capacity, and the energy consumption is relatively low. Different types of adsorbents have different adsorption kinetics and thermodynamic characteristics. In practical applications, appropriate adsorbents need to be selected according to requirements such as oxygen purity and the composition of the raw material gas, and the structure and operation parameters of the adsorption bed need to be optimized.
Adsorption bed regeneration technology and cyclic operation
The regeneration process of the adsorption bed is a key link in the VPSA process. By pumping gas from the adsorption bed with a vacuum pump, the pressure inside the bed is reduced to about -50 kPa, creating a negative pressure environment and prompting the adsorbed molecules to desorb from the micropores of the adsorbent. The desorption process is accompanied by changes in the surface energy of the adsorbent and needs to overcome the adsorption force between the adsorbed molecules and the adsorbent. The pumping rate and ultimate vacuum degree of the vacuum pump directly affect the regeneration effect and regeneration time.
The alternate operation of the two adsorption beds realizes the continuous production of oxygen. While one adsorption bed is performing adsorption and gas production, the other adsorption bed is undergoing regeneration operations. Through precise time control and valve switching, the stable operation of the system is ensured. The setting of the adsorption bed cycle period needs to comprehensively consider factors such as oxygen production, purity requirements, and the service life of the adsorbent. By optimizing the cycle period, the oxygen production efficiency can be improved and the energy consumption can be reduced.
Function and pressure control of the buffer tank
The product oxygen buffer tank plays an important buffering and pressure stabilizing role in the VPSA process. Since the oxygen production process of the adsorption bed is intermittent and fluctuating, the buffer tank can store a certain amount of oxygen, balance the flow difference between gas production and gas consumption, and ensure the continuous and stable supply of oxygen to users. The volume of the buffer tank is calculated and determined according to factors such as oxygen production, fluctuations in user gas consumption, and the allowable pressure fluctuation range of the system.
The pressure in the buffer tank is controlled between 14 – 49 kPa through pressure sensors and regulating valves. When the pressure in the tank is lower than the lower limit value, the gas production time of the adsorption bed is increased or the gas delivery pressure of the compressor is increased; when the pressure is higher than the upper limit value, the oxygen is appropriately vented through the vent valve to maintain pressure stability.
Product Delivery
Compressor selection and performance optimization
Reciprocating compressors and centrifugal compressors have their own characteristics in product delivery. Reciprocating compressors have a relatively high pressure ratio and are suitable for increasing the pressure of oxygen from a lower pressure range to a higher pressure range, but their structures are relatively complex and the maintenance workload is relatively large. Centrifugal compressors have the advantages of large flow, stable operation, and simple maintenance and are suitable for large-scale oxygen delivery occasions. When selecting, comprehensive evaluations need to be made according to specific pressure and flow requirements of users, site conditions, and operating costs.
The performance optimization of the compressor involves multiple aspects, such as the adjustment of the inlet air flow, the improvement of the cooling system, and the enhancement of the sealing performance. Adopting advanced inlet air adjustment technologies, such as inlet vane adjustment or variable frequency speed regulation, can precisely adjust the inlet air volume of the compressor according to changes in user gas consumption and improve the operating efficiency. The optimization of the cooling system includes improving the structure of the cooler, increasing the flow of the cooling medium and the heat exchange efficiency to ensure that the temperature of the compressor is stable during the working process and extend the service life of the equipment.
Integration of the cooling and flow control systems
The aftercooler is indispensable in the product delivery process. It adopts efficient heat exchange technology to cool the high-temperature oxygen at the outlet of the compressor to an appropriate temperature range, meeting the temperature requirements of users for oxygen and also helping to reduce the safety risks in the oxygen delivery process. The design of the cooler needs to consider factors such as oxygen flow, inlet and outlet temperatures, and pressure drop, and select an appropriate heat exchange area and cooling medium flow.
The flow control system realizes precise control through flow meters, regulating valves, and reflux valves installed on the pipeline. When the user’s consumption is less than the output of the compressor, the opening degree of the reflux valve is automatically adjusted to make the excess oxygen flow back to the inlet of the compressor, forming a circulation loop and realizing the automatic adjustment of the oxygen flow. Meanwhile, the system is equipped with a safety vent valve. When the oxygen pressure or flow exceeds the safe range, the excess oxygen is promptly vented to ensure the safe and stable operation of the system.
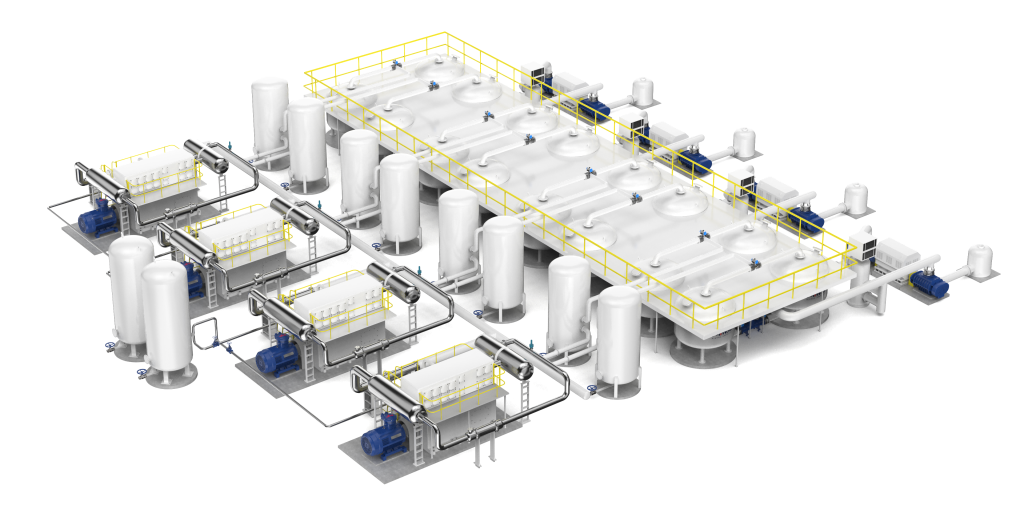
Optimization Strategies of the VPSA Process in Practical Applications
Optimizing process parameters according to the conditions of the raw material gas
The air composition and environmental conditions in different regions may vary. For example, altitude affects air pressure and oxygen content, and the pollutant content in the air in industrial areas is relatively high. In practical applications, the VPSA process parameters need to be optimized and adjusted according to the specific conditions of the raw material gas, such as temperature, pressure, humidity, and impurity content. For example, in high-altitude areas, the adsorption pressure can be appropriately increased to compensate for the reduction in air oxygen content; for areas with high humidity, strengthening the air pre-drying treatment or optimizing the regeneration parameters of the adsorption bed can prevent the adsorbent from being affected by excessive water absorption and affecting its adsorption performance.
Equipment maintenance and operation management strategies
Regular maintenance of equipment is the key to ensuring the long-term stable operation of the VPSA oxygen production system. For filters, regularly replace the filtering media and clean the filter screens to ensure the filtering effect; for rotating equipment such as fans and vacuum pumps, carry out regular lubrication, check the bearing wear, monitor the vibration and noise levels, and promptly detect and handle potential faults. In terms of operation management, establish a complete set of operating procedures and monitoring systems, monitor key parameters of the system in real-time, such as pressure, temperature, flow, and oxygen purity, and adjust the process parameters in a timely manner through data analysis to optimize the system operation state.
Energy-saving, consumption reduction and sustainable development measures
With the increase in energy costs and the improvement of environmental protection requirements, energy-saving, consumption reduction and sustainable development of the VPSA oxygen production process have become important research directions. For equipment selection, preference is accorded to choosing energy-efficient fans, compressors and other apparatuses and optimizing their operational control strategies to cut down energy consumption. During the process, investigate waste heat recovery and utilization technologies, like employing the waste heat of the compressor to warm the air for the adsorption bed’s regeneration to enhance energy utilization efficiency. Moreover, handle and recycle the adsorbent’s regeneration exhaust gas to diminish greenhouse gas emissions and fulfill the sustainable development of the oxygen production process.
Conclusion
The Vacuum Pressure Swing Adsorption (VPSA) oxygen production process flow is a complex system involving multidisciplinary knowledge and technologies. In practical applications, reasonably optimizing process parameters, selecting appropriate equipment and strengthening operation management according to different working conditions and user requirements are the keys to improving the performance of the VPSA oxygen production system, reducing costs and achieving sustainable development.
Our continuous technological innovation and optimization make MINNUO highly competitive and valuable in the field of oxygen production. If you want to know more, welcome to consult the MINNUO official website.