PSA (Pressure Swing Adsorption) technology is one of the core technologies widely used in the field of gas separation.PSA technology plays a vital role in many industries by separating gases such as oxygen and nitrogen through adsorption and desorption processes. It is widely used in gas separation and nitrogen production, and has great advantages in ensuring gas purity and energy efficiency.
In this paper, we will take an in-depth look at the effects of gas flow distribution within a PSA nitrogen generator, focusing on how to improve the overall performance of a PSA system by optimizing gas flow distribution. We will examine the critical role of gas flow and pressure distribution on the efficiency of PSA systems, and present calculations to achieve the ideal gas flow distribution to maximize nitrogen production efficiency and minimize waste.
Through this article, you will gain a practical approach on how to optimize airflow distribution in PSA nitrogen generators. Whether you are an engineer, technician or industry practitioner, the calculations and optimization suggestions provided in this article will help you achieve more efficient gas separation, improve system stability and energy saving in actual operation.
Ⅰ.Gas Flow Distribution in PSA Nitrogen Generators
The Role of Gas Flow in PSA Systems
At the heart of a PSA nitrogen generator is the separation of gases through a series of pressure swing adsorption processes. The distribution of gas flow is critical to achieving efficient operation of the nitrogen generator. Proper flow distribution not only helps to improve nitrogen yield and purity, but also reduces energy consumption and minimizes waste. In a PSA system, the gas flow is distributed along the path of the adsorption column, usually starting from the gas inlet and flowing uniformly along the molecular sieve bed in the adsorption column to ultimately achieve the goal of gas separation.
Factors Affecting Gas Flow Distribution
Pressure and Temperature Differences:
Pressure and temperature differences in a PSA nitrogen generator can directly affect the uniformity of gas flow distribution. Pressure difference and temperature gradient lead to uneven distribution of gas flow inside the generator, which in turn affects the adsorption efficiency of the gas and the utilization efficiency of the molecular sieve.
Equipment design and structure:
The design of the adsorption tower and the arrangement of the piping play a crucial role in the gas flow distribution. The column design of the adsorption tower, the configuration of the gas flow inlet and outlet, and the layout of the piping determine the way the gas flows through the entire system. Improper design may result in over-concentration of gas flow in some areas and short-circuiting of gas flow in other areas.
Condition and structure of the adsorbent:
The pore structure of the adsorbent, the size of the particles, and their arrangement have a significant effect on the airflow distribution. Areas with too tightly packed particles may lead to increased airflow resistance, while areas with too loose particles may lead to uneven gas flow, resulting in reduced gas separation efficiency.
Efficiency of airflow control systems:
Precise airflow control devices, such as manual or automatic regulating valves, are effective in optimizing airflow distribution, ensuring balanced and uniform gas flow, and thus improving the overall efficiency of the system.
The Challenge of Achieving Uniform Gas Flow
In PSA nitrogen generators, it’s not just the magnitude of the flow rate, but also the uniform distribution of the gas flow that is a major challenge in system design. Uneven gas flow distribution can lead to excessive wear of the molecular sieve, insufficient gas handling in certain areas of the adsorption tower, and thus affect the separation and overall efficiency. Factors such as pressure fluctuations, frictional resistance of piping, and equipment design flaws can affect gas flow distribution to varying degrees. The design must take these factors into account and optimize the gas flow path to ensure a more uniform gas flow.
Solutions and Optimization Strategies
Optimize System Design:
To ensure uniform distribution of gas flow, the design should reasonably configure the gas inlet and outlet locations, and ensure that the internal structure of the adsorption tower is designed to effectively guide the gas flow to avoid uneven distribution.
Use of precise gas flow control system:
is equipped with precise gas flow monitoring and regulating devices, such as flow sensors, regulating valves and pressure control devices, which can dynamically adjust the gas flow and ensure more uniform gas distribution in the system during operation.
Regular Maintenance and Inspection:
Regular system inspection and maintenance ensures that the equipment and airflow control system are in optimal working condition, and that airflow irregularities are detected and resolved in a timely manner. For example, clean the inner wall of the adsorption tower and the pipeline to avoid the accumulation of dust or other pollutants affecting the airflow.
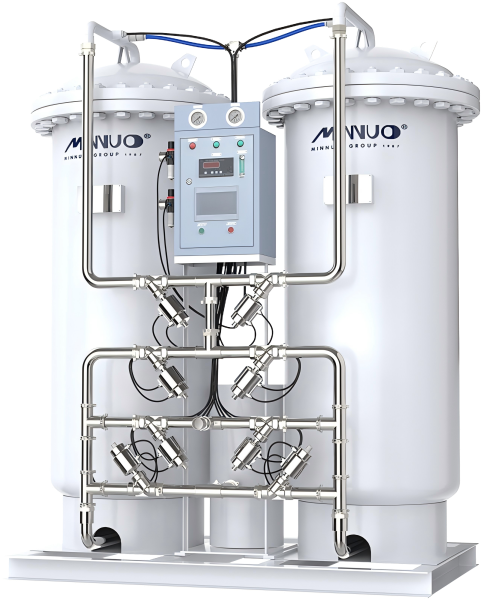
II.Calculations for Analyzing Gas Flow Distributions
Fundamentals of Flow Analysis
In PSA systems, accurate calculations of gas flow distributions are essential to optimize system efficiency and to ensure high nitrogen or oxygen production and purity. Fluid dynamics principles (e.g., mass balance, continuity equations, Bernoulli’s law, etc.) are widely used for such calculations. The flow characteristics of gases – such as viscosity, density, temperature, etc. – directly affect the flow distribution, so a thorough understanding of these fundamentals is necessary to properly calculate and regulate the flow of gases in a system.
Gas Flow Characteristics:
The operating principle of a PSA system involves the adsorption and desorption of gases under different pressure and temperature conditions. The flow of gases in a pipeline is affected by friction, turbulence, flow and pressure variations. Flow analysis relies on the fundamental properties of the gas, including viscosity, density, flow rate and temperature. These factors determine the flow pattern of the gas in the pipeline, which in turn affects the adsorption efficiency of the molecular sieve and the gas separation process.
Construction of Flow Calculation Models:
The gas flow calculation models for PSA systems usually use CFD (Computational Fluid Dynamics) models for gas flow and pressure analysis. These calculation models can simulate the gas flow path and distribution in the system according to specific fluid physical properties and operating conditions, which can help optimize the design and improve the separation effect.
Gas Flow Modeling in PSA Systems
Gas flow in PSA systems can be simulated by computational fluid dynamics (CFD) modeling. The model is mainly used to analyze the flow pattern of gases in the system, especially the flow path and distribution of gases in the adsorption tower. Fluid flow modeling not only helps to understand the direction and velocity of the flow, but also provides information about the flow efficiency, such as pressure drop, adsorption rate and desorption efficiency.
Application of CFD models:
The application of CFD models to PSA systems allows the simulation of the fluid behavior of pipelines, adsorption towers and their associated system components. By calculating gas velocity distribution, pressure changes and turbulence intensity, CFD models help engineers optimize system design, improve flow distribution and maximize gas separation.
Fluid Dynamics Calculation Process:
In CFD calculations, key physical quantities include the gas flow rate, temperature, density, pressure, and the effects of turbulence. With these parameters, a three-dimensional gas flow model can be built to simulate the gas flow path and its distribution in different adsorption tower regions. Optimizing the gas flow distribution can reduce energy consumption and increase the lifetime of the molecular sieves.
Optimization of gas flow distribution analysis using CFD
The application of CFD technology plays a vital role in PSA systems. It can not only reveal the actual situation of airflow distribution, but also provide theoretical support for optimized design. By adjusting the piping design, adsorption tower size and internal configuration, CFD analysis can identify potential problems at the design stage, thus avoiding unnecessary waste and loss of efficiency during later commissioning.
Advantages of CFD simulation:
CFD simulation can provide detailed airflow information under different operating conditions. For example, at lower pressures, the flow efficiency of a system may be limited. With CFD modeling, engineers can analyze and adjust the system design to find the airflow path and pressure distribution that is best suited for specific operating conditions.
Application of analysis results from CFD models:
The results of CFD analysis will have a direct impact on the optimization of the airflow path. By adjusting the piping layout, changing the adsorption tower design and installing additional airflow control equipment, the resistance of the airflow can be reduced and the gas flow can be optimized, thus improving the separation efficiency and reducing energy consumption.
CFD-based gas flow optimization design:
The key steps to optimize the gas flow distribution design using CFD model include:
Piping layout optimization: reduce the gas flow loss by reasonably designing the diameter and length of the pipeline and the location of the gas flow inlet.
Adsorption tower design adjustment: According to the CFD analysis results, optimize the distribution of airflow in the adsorption tower to avoid short-circuit flow and dead zone.
Airflow monitoring and dynamic adjustment: through real-time monitoring of system airflow and pressure data, dynamic adjustment is carried out to ensure that efficient airflow distribution is always maintained.
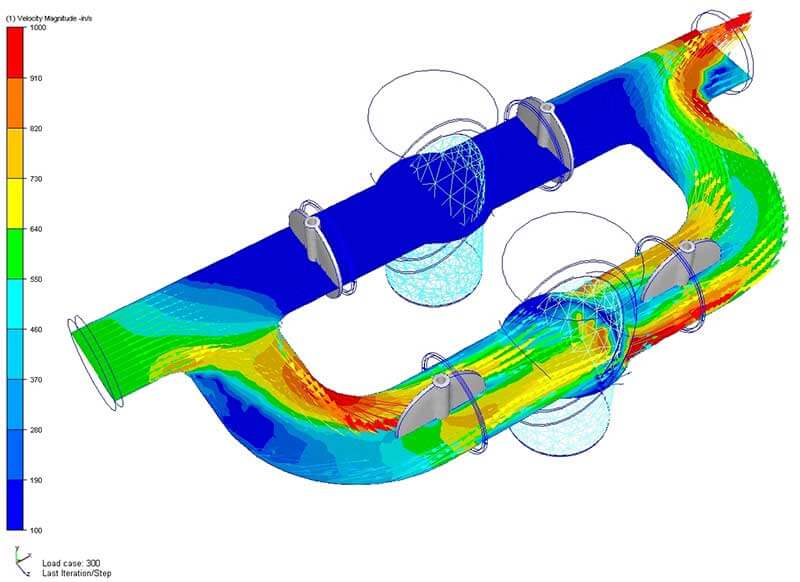
III. Impact of flow and pressure distribution on PSA system performance
Impact on nitrogen purity
Uneven flow distribution may lead to incomplete separation of nitrogen and oxygen, thus reducing the purity of the produced nitrogen. The relationship between pressure and gas distribution efficiency is critical, especially in PSA systems, where pressure fluctuations directly affect the distribution of gas flow in the adsorption tower and the effectiveness of gas separation.
Uneven Flow Distribution: When the flow distribution is uneven, certain areas may be subjected to higher flow rates, resulting in lower efficiency of the adsorption and desorption processes. Especially in low flow rate regions, the gas contact time is not sufficient, resulting in oxygen not being completely separated from nitrogen. Conversely, high flow areas may have too much gas flow to fully adsorb the gas, wasting energy and reducing purity.
Optimize pressure and flow: To improve nitrogen purity, the flow and pressure distribution of the PSA system needs to be adjusted to ensure a more uniform flow of gas through the system. Through flow control and intelligent pressure regulation, the system can reduce imbalances in the gas separation process and achieve higher separation efficiencies.
Impact on energy consumption
Uneven flow distribution also increases the energy consumption of the system. As the gas flow rate and pressure change, the power required by the system increases, which can lead to higher operating costs.
Wasted energy: When the flow distribution in a system is unbalanced, certain areas of the flow rate are too high, resulting in unnecessary energy consumption. For example, areas of high pressure require more compression energy to keep the gas flowing, while areas with lower flow rates waste energy due to poor gas separation efficiency. This uneven distribution of energy directly affects the overall energy efficiency of the PSA system, resulting in higher operating costs.
Optimize Energy Efficiency: By optimizing the distribution of flow and pressure, the energy consumption of the system can be minimized while maintaining stable operation. Adopting intelligent control strategies to adjust airflow paths and pressure settings can effectively reduce unnecessary energy waste and ensure maximum efficiency in energy use.
System Stability and Equipment Wear
Uneven flow distribution can increase equipment loading in certain areas, especially areas of higher pressure, which can lead to premature equipment wear and shorten its service life.
Excessive Equipment Load: In a PSA system with uneven flow distribution, certain areas of the equipment will be subjected to higher loads, resulting in excessive wear. For example, certain valves and compressors may be subjected to higher operating pressures and flow rates, which can accelerate their wear and aging.
Optimize equipment protection: With precise control of flow and pressure distribution, the load on the equipment can be reduced and overworking of the system avoided, thus extending the life of the equipment. Regular maintenance and intelligent monitoring systems will help identify and resolve possible equipment problems in a timely manner, reducing unnecessary repair and replacement costs.
Potential Hazards of Uneven Flow to PSA Systems
Uneven flow distribution not only affects gas separation efficiency, but can also lead to overall system performance degradation, increasing operational complexity and instability.
System performance degradation: Uneven flow distribution may cause some areas of the system to operate inefficiently for long periods of time, thus affecting overall gas production and gas purity. Due to uneven flow and pressure distribution, there may be sharp fluctuations between high and low pressure areas within the system, leading to unstable operation.
Optimizing flow distribution: To avoid degradation of system performance, PSA systems must precisely control the distribution of gas flow and pressure. Through advanced design and flow optimization techniques, it is possible to achieve a balanced gas flow, ensuring that all zones work efficiently and improving the overall performance and stability of the system.
IV. Optimizing Gas Flow Distribution for Maximum Efficiency
Ideal Gas Flow Distribution in PSA Systems
Ideal distribution of gas flow in a PSA system is critical because it directly affects the effectiveness of gas separation and the overall efficiency of the system. Ideal gas distribution requires uniform gas flow with minimal pressure drop to ensure that gases are effectively separated throughout the PSA system. Uneven gas distribution may result in insufficient adsorption capacity in certain areas, resulting in lower gas purity or reduced separation efficiency.
Ideal Flow and Minimized Pressure Drop: By ensuring that the gas flow is uniformly distributed throughout the PSA system, the efficiency of the adsorber tower can be maximized, energy consumption can be reduced, and the separation of oxygen and nitrogen can be ensured. When designing, special attention needs to be paid to minimizing pressure drop while optimizing the gas path to achieve the desired gas flow.
Uniform distribution is critical: Uneven gas flow can lead to too much or too little gas flow in certain parts of the system, which not only affects the stability of the separation process, but also increases energy consumption. Therefore, an ideal gas flow distribution needs to be precisely designed to avoid this.
Optimizing adsorption bed design
When designing an adsorption bed, how to effectively direct the gas flow and maintain a uniform gas flow distribution is critical to optimizing the performance of the PSA system. A proper design ensures that the gas flow is in full contact with the molecular sieves in the bed, thus improving separation efficiency and gas purity.
Bed Structure Design: During the bed design process, it is critical to ensure that the path of the gas flow through the bed is optimized to ensure uniformity of the gas flow. This includes aspects such as the size and shape of the bed and the choice of molecular sieves. Proper bed design reduces flow dead zones and avoids blockage or uneven flow as the gas flows between the molecular sieves.
Objective of bed optimization: By improving the design of the adsorption bed, the efficiency of the molecular sieve can be improved, the service life of the equipment can be extended, and the maintenance cost can be reduced. In order to achieve the best separation effect, the structure of the bed, flow rate control and air intake method need to be considered comprehensively.
Improvement of air intake control mechanism
Flow control is another key factor to ensure the efficient operation of PSA system. Improvements to the inlet control mechanism to ensure a balanced flow rate and pressure distribution of the gas into the PSA system can improve separation efficiency and optimize the use of the gas stream.
Precise flow regulation: The intake air flow must be precisely regulated to ensure even distribution and minimize unwanted flow fluctuations. The use of an automatic control system allows for dynamic adjustment of the intake air flow, thus improving system responsiveness and stability.
The importance of pressure regulation: the matching of flow and pressure has a direct impact on system efficiency. Under different operating conditions, the pressure drop of the airflow may vary. A reasonable pressure control system ensures that the airflow passes evenly through the entire PSA system and reduces the negative effects of uneven flow distribution.
System Pressure Drop and Airflow Mechanics
The ultimate goal of optimizing airflow distribution is to achieve the lowest possible pressure drop in the system while ensuring that the airflow is utilized efficiently in each section. Efficient airflow design reduces the pressure drop, thereby improving system performance and reducing energy consumption.
Impact of pressure drop: Excessive pressure drop not only leads to uneven airflow, but also increases the energy consumption of the system. Therefore, the optimal airflow distribution should make the airflow evenly distributed in all gas separation areas, and keep the pressure drop at the lowest level to avoid energy waste.
Design Principles for Reducing Pressure Drop: Energy losses due to pressure drop can be reduced through the use of better piping design, fine flow control and flow optimization strategies. An effective airflow optimization program can improve the overall energy efficiency of a PSA system.
Conclusion
Exploring the importance of optimal flow distribution in PSA nitrogen generators to achieve maximum efficiency was the centerpiece of this paper. An in-depth analysis of flow distribution, pressure variations, and system design can be used to effectively improve PSA system performance, reduce energy consumption, and increase gas purity. Understanding the role of flow and pressure distribution in PSA system design, especially in optimizing gas distribution, is critical to improving overall efficiency and reducing waste.
MINNUO provides advanced PSA nitrogen generator solutions with optimized gas distribution technology to help customers improve gas distribution efficiency and system performance. By combining efficient gas distribution design with state-of-the-art control technology, MINNUO’s systems provide a stable and cost-effective gas supply solution for a wide range of industries, further advancing customers’ productivity and energy saving goals.