The oxygen-rich side-blown furnace copper smelting process is an emerging green metallurgical technology that is dedicated to improving the efficiency of copper smelting and reducing carbon emissions through the introduction of high-concentration oxygen. This technology not only meets the requirements of modern copper smelting for high efficiency and low pollution, but also brings significant benefits in environmental protection and comprehensive utilization of resources. This article will introduce in detail the working principle, production process, technical advantages and future development prospects of this process.
The high-concentration oxygen-rich low-carbon copper smelting process of oxygen-rich side-blown furnace introduces high-concentration oxygen to improve the oxidation reaction efficiency and reduce fuel demand in copper smelting, achieving significant carbon emission reduction effects. This process accelerates the oxidation of sulfides in copper ores and reduces external energy consumption through autothermal reactions. The by-product SO₂ gas can be recycled to make acid, improving resource utilization and environmental protection. This technology is in line with the trend of low-carbon and environmental protection and is expected to be more widely used and promoted in the global copper smelting industry in the future.
Process background and importance
Copper is one of the basic metals widely used in industry, and its demand in electrical, electronics, construction, machinery manufacturing and other industries is increasing year by year. However, traditional copper smelting methods rely on high temperatures generated by coal, coke and other fossil fuels to drive the smelting process, emitting large amounts of carbon dioxide (CO₂) and sulfur oxides (SOx), increasing environmental pollution and greenhouse gas emissions. In this context, how to achieve low-carbon copper smelting and reduce dependence on fossil energy has become an urgent issue in the global copper smelting field.
The high-concentration oxygen-rich low-carbon copper smelting process of oxygen-rich side-blown furnace has gradually become one of the core technologies of low-carbon copper smelting due to its remarkable results in reducing fuel usage and improving production efficiency. This process effectively reduces carbon emissions through autothermal oxidation in a high-concentration oxygen-rich environment, and converts sulfides and impurities in copper ores into recyclable by-products, providing a new way to achieve green metallurgy.
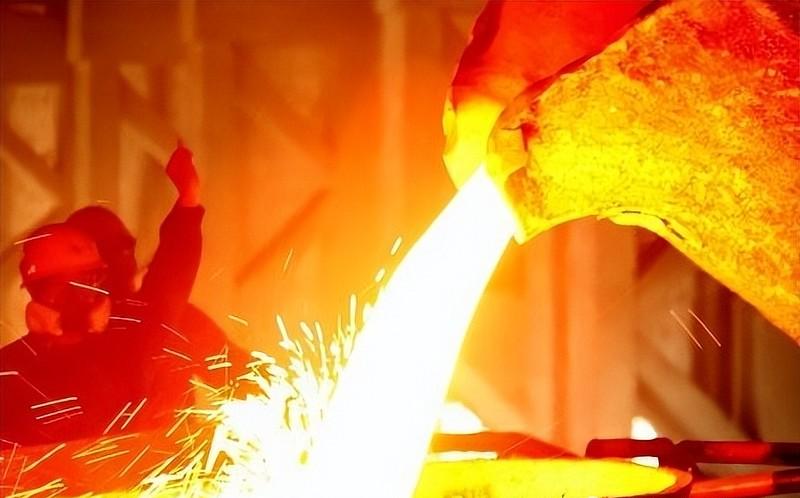
Process principle of oxygen-rich side-blown furnace
The core of the oxygen-rich side-blown furnace copper smelting technology is to use high-concentration oxygen to oxidize the sulfide in the copper concentrate. Different from the traditional copper smelting method, the oxygen content of the oxygen-rich side-blown furnace is as high as more than 80%, which greatly enhances the efficiency of the oxidation reaction. Its process principles include the following aspects:
Enhanced oxidation reaction
In an oxygen-rich environment, the oxidation reaction releases more heat, which helps maintain high temperatures and makes the chemical reactions in the entire smelting process more efficient. Impurities such as sulfur and iron in copper ores are rapidly oxidized under the action of high concentrations of oxygen to generate sulfuric acid gas and iron oxide slag, which facilitates the separation of copper metal.
Autothermal reaction reduces fuel requirements
Since the heat released by oxidation is sufficient to maintain the temperature in the side-blown furnace, the copper smelting process in the oxygen-rich side-blown furnace can reach the temperature conditions required for smelting without or only a small amount of external fuel, thus significantly reducing Reliance on fuel enables low-carbon production.
Selective oxidation of high concentration of oxygen
High concentration of oxygen makes the oxidation reaction more selective, allowing the non-copper components in the copper ore to be oxidized preferentially, effectively improving the grade of the copper concentrate and improving the final product of copper smelting quality.
Comprehensive utilization of resources
The SO₂ tail gas generated during the oxidation process can be processed and prepared into sulfuric acid, achieving efficient recovery of resources and avoiding environmental pollution caused by direct emission of waste gas.
Detailed explanation of process flow
The process flow of high-concentration oxygen-enriched low-carbon copper smelting in oxygen-enriched side-blown furnace usually includes ore preparation, oxygen-enriched smelting in side-blown furnace, separation refining and tail gas treatment. The specific steps are as follows:
Ore preparation
The copper concentrate is first crushed and pre-treated to improve the uniformity and reaction efficiency of the concentrate. This step controls the purity and particle size of the mineral material to ensure full access to oxygen during the subsequent oxygen-rich side blowing process, thereby increasing the reaction rate.
Oxygen-enriched smelting in side-blown furnace
Oxygen-enriched side-blown furnace is the core of the entire process. After the copper concentrate enters the side-blown furnace, high-concentration oxygen is injected into the furnace from the side wall, so that the heat generated by the oxidation reaction is concentrated around the copper ore particles. Due to the rapid action of high-concentration oxygen, the sulfur in the ore is oxidized to generate SO₂ gas, while iron and other impurities are converted into oxide slag and separated from the liquid copper.
Separation and refining
Under the oxidation of the side-blown furnace, the molten copper liquid is separated from the slag to form relatively pure metallic copper. This process no longer requires a large amount of fuel heating, further reducing carbon emissions and costs. Subsequently, residual impurities in the copper are further removed through refining to obtain electrolytic copper that meets market standards.
Tail gas treatment
The SO₂ gas generated by oxidation in the oxygen-rich side-blown furnace enters the tail gas recovery system after cooling and purification. This gas can be converted into industrial sulfuric acid after treatment, realizing secondary utilization of resources and greatly reducing environmental pollution. The sulfuric acid generation device in the tail gas treatment system is also one of the components of the oxygen-rich side-blown furnace process, which improves the economy and environmental protection of production through resource recycling.
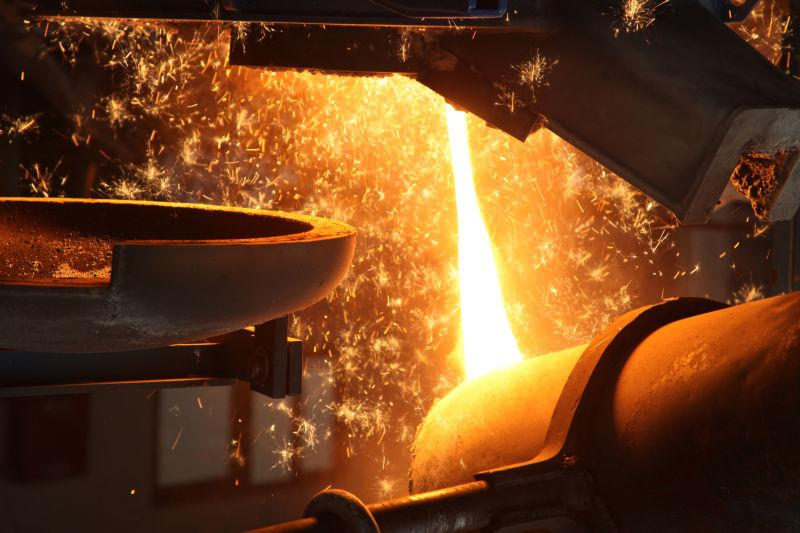
Advantages of high-concentration oxygen-rich low-carbon copper smelting process in oxygen-rich side-blown furnace
The advantages of high-concentration oxygen-rich low-carbon copper smelting in an oxygen-rich side-blown furnace are not only reflected in copper smelting efficiency and product quality, but also significantly reduce carbon emissions and environmental pollution in the traditional copper smelting process. The following are its core advantages:
The smelting efficiency is significantly improved
The injection of high-concentration oxygen accelerates the sulfide oxidation reaction in the copper ore, significantly increasing the copper recovery rate, shortening the entire smelting process, and improving efficiency. This makes the oxygen-rich side-blown furnace have higher production capacity than traditional processes and is suitable for large-scale continuous production.
Significantly reduces carbon emissions
By utilizing the heat generated by the oxidation reaction to maintain the temperature of the side-blown furnace, the need for external fuel is reduced, thereby significantly reducing CO₂ emissions. This process complies with the environmental protection requirements of low-carbon smelting and has a positive effect on reducing greenhouse gas emissions.
Energy saving and consumption reduction
Under the action of high concentration of oxygen, the sulfur element in the copper ore can quickly oxidize and release heat, eliminating the need for additional fuel heating, saving energy consumption. In addition, the heat generated by smelting can be fully utilized, reducing energy waste and lowering production costs.
Reduced environmental pollution
The SO₂ gas generated by the oxygen-rich side-blown furnace process is converted into industrial raw materials such as sulfuric acid through the tail gas treatment system, realizing waste gas resource utilization, avoiding direct emission of sulfur oxides from polluting the environment, and enhancing the environmental protection effect.
Improved copper product quality
A high-concentration oxygen-rich environment makes impurities in copper ores easier to oxidize and separate, improving the purity of copper concentrate and improving the quality of final copper products, making the products more competitive in the market.
Application and Development Prospects
The high-concentration oxygen-rich low-carbon copper smelting process of oxygen-rich side-blown furnace has been applied in pilot trials in many copper smelters at home and abroad and has achieved good results. With the development of low-carbon smelting technology and increasingly stringent environmental protection requirements, this technology has broad prospects for application in copper smelting. The following are future development trends:
Technological innovation and optimization
With the introduction of high-efficiency, low-energy consumption equipment, the oxygen-rich side-blown furnace process is expected to further reduce energy consumption and improve smelting efficiency. Future research directions will focus on optimizing the oxygen injection device and improving the fire resistance of the furnace body to ensure the sustainability and economy of the process.
Comprehensive utilization of resources
The optimization of the exhaust gas treatment system will promote the efficient recovery of SO₂, provide high-quality raw materials for sulfuric acid production, form a circular economy model, and maximize the utilization of resources.
Global promotion potential
Driven by the low-carbon requirements of various countries around the world for the metallurgical industry, the oxygen-rich side-blown furnace copper smelting process is expected to be promoted and applied in more countries, helping the green transformation of the global metallurgical industry.
Integration with carbon emission reduction policies
The low-carbon characteristics of the oxygen-rich side-blown furnace copper smelting process make it adaptable to policies such as carbon emission limits and carbon trading. In the future, this technology is expected to become one of the metallurgical process options to achieve carbon emission reduction goals.
Conclusion
The high-concentration oxygen-rich low-carbon copper smelting process of the oxygen-rich side-blown furnace achieves rapid oxidation of copper ore sulfides through the injection of high-concentration oxygen, significantly improving copper smelting efficiency and reducing energy consumption and carbon emissions. With the development of low-carbon economy, the oxygen-rich side-blown furnace technology has broad application prospects in the global copper smelting field.
Pressure swing adsorption oxygen production device is very suitable for oxygen-rich copper smelting. MONNUO VPSA oxygen concentrator can produce low-cost oxygen on a large scale and has many advantages: convenient start-up and parking, flexible load adjustment, and high online rate. So far, dozens of copper smelting companies at home and abroad have chosen to use MINNUO oxygen generators. Among them, the highest continuous purchase record by a single user is 7 sets, which is enough to prove that the majority of copper smelting users have full trust in MINNUO VPSA oxygen generators.
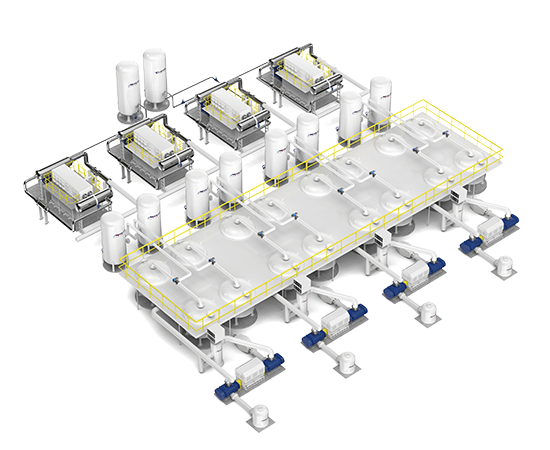