In this paper, we will take an in-depth look at the problem of fluctuating oxygen concentration in PSA systems, especially the factors that affect their stability. We will analyze the working principle of the system and the main control process of oxygen concentration, focusing on how to improve the stability of the system in practical applications.
Oxygen concentration fluctuations can be caused by various factors, which may involve compressor performance, system pressure fluctuation, air source quality and other factors. The stability of oxygen concentration is crucial for medical and industrial applications, especially in medical oxygen supply, where any fluctuation may affect patients.
This article will analyze in-depth the specific causes of oxygen concentration fluctuations, discuss how different factors affect system stability, and provide a series of solutions to help enhance the stability of PSA systems to ensure continuous and stable oxygen output.
Ⅰ. Causes of fluctuations in oxygen concentration in PSA systems
PSA (Pressure Swing Adsorption) system is a gas separation device based on pressure swing adsorption technology, which is widely used in the production of oxygen, nitrogen, hydrogen and other gases. However, fluctuating oxygen concentration is a common problem encountered by many users during operation. In order to better understand and solve this problem, we can analyze its causes from the following aspects:
1. Molecular sieve performance problems
The molecular sieve is a key component in the PSA system, and its performance directly affects the stability of oxygen concentration. The adsorption capacity of the molecular sieve will gradually decrease with the prolongation of the use time, which leads to the decrease of its efficiency in separating the gases, and the concentration of oxygen can not be maintained in the predetermined range.
Aging of molecular sieve: With the prolonged use of molecular sieve, its internal micropores will be gradually blocked or damaged by water, oil and other impurities in the air, resulting in a decline in adsorption efficiency and a gradual loss of molecular sieve’s ability. This will lead to fluctuations in oxygen concentration, or even substandard conditions.
Molecular sieve type and quality: different types and brands of molecular sieves have different adsorption capacity and service life, and low-quality molecular sieves are more likely to be saturated too quickly, and the adsorption effect is not stable.
2. Inadequate compressor performance
The compressor is the core component in the PSA system, which is responsible for compressing air to a certain pressure and driving the gas into the molecular sieve tower for the adsorption process. Inadequate compressor performance may lead to the following problems:
Inadequate Compressor Output: If the compressor output gas flow is insufficient to reach the working pressure required by the adsorption tower, the molecular sieve will not be able to give full play to its adsorption effect, thus affecting the stability of oxygen concentration.
Compressor aging: As the compressor is used for a longer period of time, its seals and components may wear out, resulting in unstable gas output, which will exacerbate the fluctuation of oxygen concentration.
3. Air source quality problems
The air source in PSA system needs to be strictly filtered and treated to ensure stable gas quality. Water, oil, dust and other impurities in the air will have a serious impact on the operation of the system, especially in the following aspects:
Effect of water: If the air entering the system contains too much water, the molecular sieve will be easily contaminated by the water, which will lead to a decrease in its adsorption efficiency, and then affect the stability of the oxygen concentration.
Influence of oil: Oil in the air will cause the molecular sieve to be clogged, affecting the separation effect of the gas, leading to the instability of the oxygen concentration.
Dust and impurities: Particles and impurities in the air, if not effectively filtered, may cause mechanical damage to the molecular sieve, further affecting the stability of oxygen output.
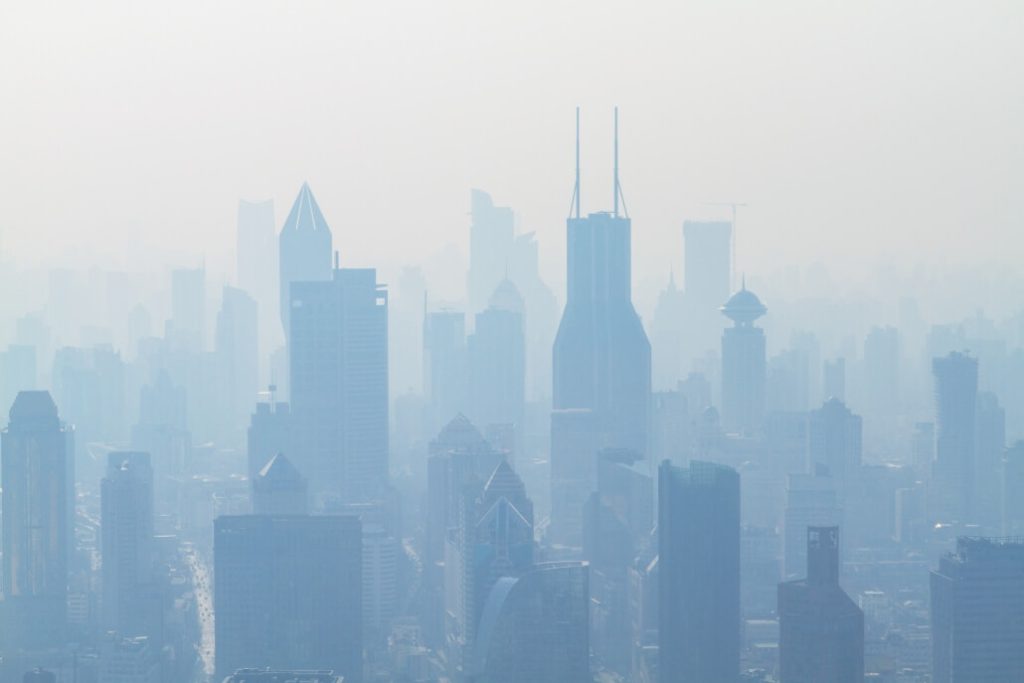
4. Pressure fluctuations in the system
Pressure fluctuations in PSA systems are a major cause of fluctuations in oxygen concentration. The pressure inside the system needs to be maintained within a certain range to ensure the proper functioning of the molecular sieve and the efficiency of the gas separation. Inaccurate pressure control can result in:
Pressure Instability: Pressure fluctuations within the system can cause the gas separation process to become unstable, resulting in fluctuations in oxygen concentration.
Insufficient compressor pressure: If the compressor fails to provide stable pressure, the adsorption efficiency of the molecular sieve will be reduced, which ultimately affects the oxygen concentration.
5. Changes in operating environment
The operating environment of PSA system also has a great influence on the stability of oxygen concentration. Environmental factors such as temperature, humidity and changes in air composition have a direct impact on system performance.
Temperature fluctuations: Fluctuations in ambient temperature may affect the efficiency of the compressor and molecular sieve, resulting in fluctuations in oxygen concentration.
Humidity changes: High humidity environment, the increase of moisture in the air will affect the molecular sieve adsorption effect, reducing the stability of oxygen concentration.
6. Improper system maintenance
The PSA system requires regular maintenance and inspection to ensure its stable operation. The following are some common maintenance problems:
Inadequate periodic inspection: If the molecular sieve, compressor, or filters in the system are not regularly inspected and replaced, or if the filters in the system are not cleaned, the performance of the equipment may deteriorate, resulting in unstable oxygen concentration.
Damaged components: Failure of system components (e.g. valves, pressure sensors, etc.) may also result in unstable system pressure and gas flow, which in turn affects the oxygen concentration output.
II. Solutions to Improve the Stability of Oxygen Concentration in PSA System
In order to ensure that the PSA system can provide high purity oxygen continuously and stably, it is crucial to take suitable measures to improve the stability of oxygen concentration. The following are some optimization measures and solutions that can effectively improve the performance and stability of the PSA system.
1. Optimization and selection of molecular sieve
Optimization of molecular sieve:
Select highly efficient and stable molecular sieve brands, such as CECA, Tosoh, UOP and other famous brands, which have high adsorption capacity and long service life.
Regularly check the status of molecular sieves: Regularly check the status of molecular sieves to ensure that they have not aged and failed.
Optimize the filling of molecular sieve: Precisely calculate the filling amount and arrangement of molecular sieve to ensure the best adsorption effect, so as to stabilize the oxygen concentration.
Choose the right type of molecular sieve:
Choose the right type of molecular sieve according to different needs, for example, the molecular sieve with stronger adsorption performance can improve the stability of oxygen concentration and the durability of the system.
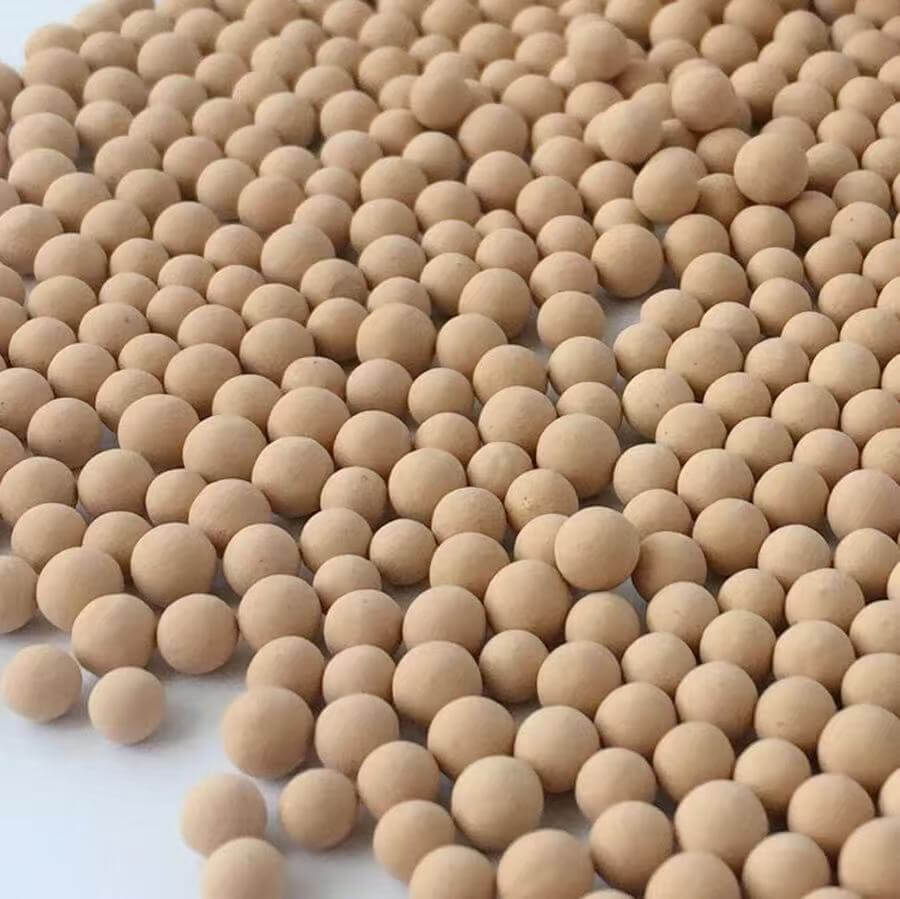
2. Optimization of the compression system
Improvement of compressor quality:
Use of a high-quality compressor ensures stable output flow and pressure.
Choosing a high quality compressor ensures the stability of the system and reduces the load on the compressor, thus avoiding fluctuations in oxygen concentration due to inadequate compressor performance.
Reasonable selection of compressors:
Select the right type of compressor (e.g., single-stage or two-stage compressor) according to the gas flow demand, to ensure that it can supply compressed air efficiently and consistently, and to avoid system instability caused by mismatch of compressor performance.
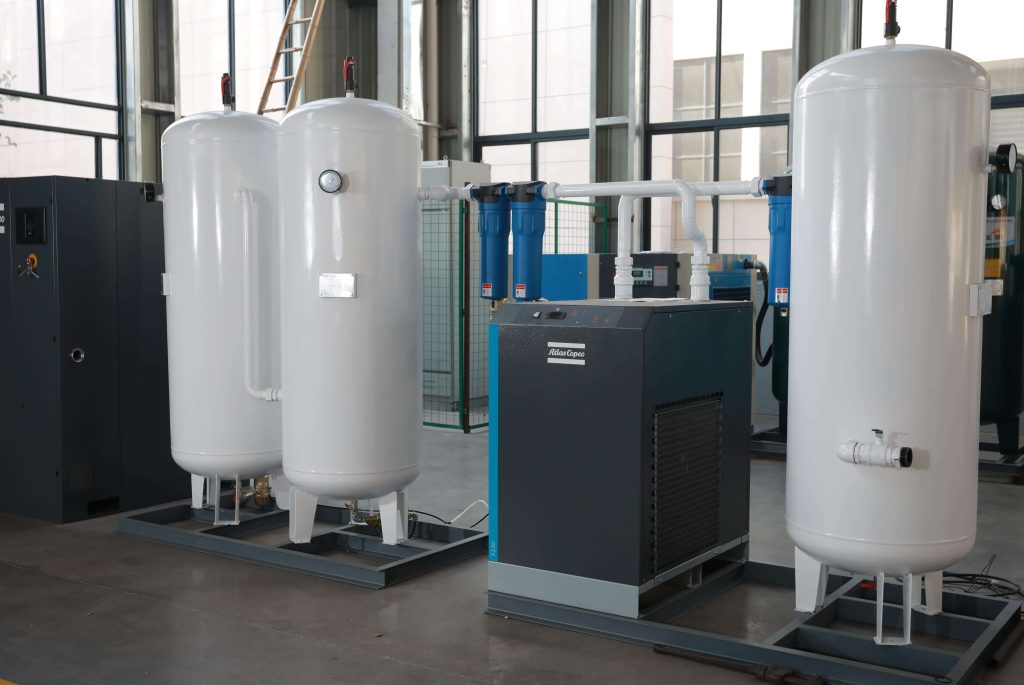
3. Improvement of air pre-treatment system
Optimization of air treatment system:
Increase the air source pre-treatment system, using advanced filters and dryers to remove moisture, oil and particles from the air.
Moisture Removal: Add high-efficiency drying equipment at the system inlet to ensure that the incoming air is dry and free of impurities, to minimize the effects of moisture on the molecular sieve, and to improve the stability of the oxygen concentration.
Reduce impurities in the system:
Use high efficiency filters and oil removal equipment to reduce oil and impurities in the air, prevent molecular sieves from being contaminated, and ensure gas separation efficiency and oxygen concentration.
4. Enhanced Pressure Control System
Precise Control System Pressure:
Ensure that the working pressure of the PSA system is always maintained in a stable range through the precise pressure control system.
Using high-quality pressure sensors to detect and adjust the system pressure in time to ensure the working efficiency of the adsorption tower and the stability of oxygen concentration.
Optimized Pressure Fluctuation Control:
The automatic adjustment function is incorporated in the system design to automatically compensate for pressure changes caused by load fluctuations, thus reducing the impact of pressure fluctuations on oxygen concentration.
5. Intelligent system automatic control
Intelligent monitoring:
By installing an intelligent monitoring system, real-time monitoring of the system’s operating parameters, such as pressure, flow, temperature, etc., and automatic adjustment of the operating state.
Remote monitoring and data analysis: using IOT technology and data analysis tools, real-time monitoring of the system’s operating status, timely detection and resolution of potential problems to ensure the stability of oxygen concentration.
Automatic Adjustment Function:
Combined with the intelligent control system, it realizes the automatic adjustment of the system to ensure that the oxygen concentration is in the preset range at every moment.
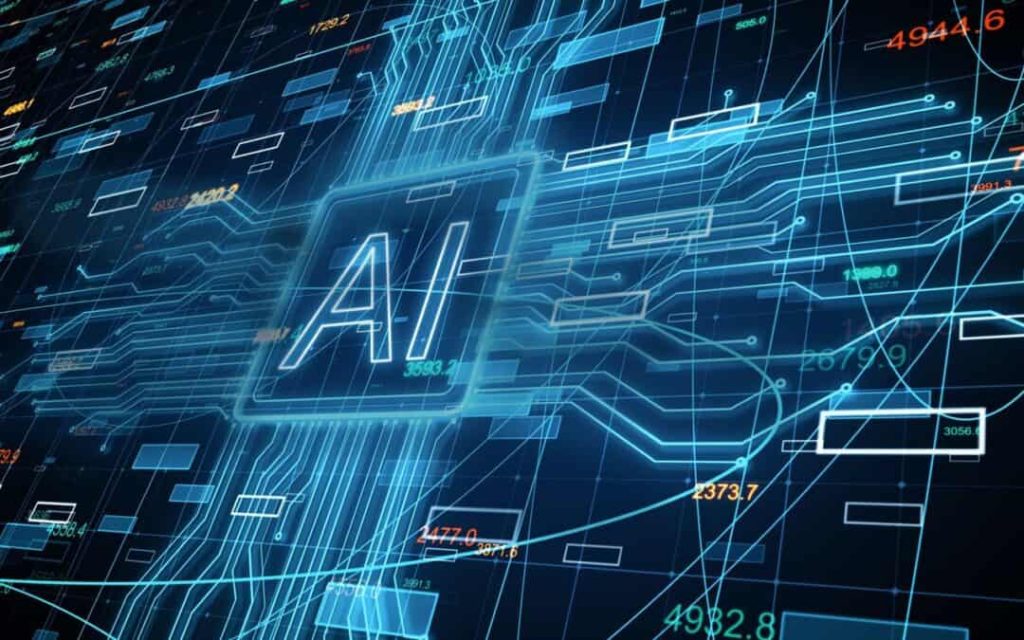
6. System Maintenance and Upkeep
Regular Maintenance:
Regularly maintain the PSA system by checking the key components of the system, such as molecular sieve, compressor, pressure sensor, etc., to ensure that they are in the best working condition.
Replacement of molecular sieve: Replace the molecular sieve periodically, especially after a certain number of hours of operation, to restore the stability of oxygen concentration.
Regular testing of oxygen concentration:
Use the concentration testing instrument to regularly test the output oxygen concentration, and make necessary adjustments according to the results to ensure that the oxygen concentration is always within the stable range.
III. Professional Recommendations and Best Practices: Ensuring Stable and Efficient Operation of PSA System
In order to ensure that the PSA system works stably and efficiently for a long time, the following professional recommendations and best practices are crucial. Through regular maintenance, selection of a professional system integrator and systematic optimization measures, equipment life can be extended, operational efficiency can be improved and malfunctions can be reduced.
1. Regular Maintenance and Overhaul
Regular Inspection and Repair:
Whole System Inspection: Conduct a comprehensive inspection of the PSA system to ensure that the system maintains its optimal working condition after a long period of operation. Especially check the compressor, molecular sieve, valves and pressure control system and other key components.
Replacement of molecular sieves: After a certain period of operation, the molecular sieves are replaced periodically to ensure the stability of their adsorption capacity and oxygen concentration. In this way to avoid molecular sieve saturation, to ensure long-term stability of system performance.
Cleaning and Maintenance:
Clean the system equipment: Clean all kinds of equipment of the system regularly, including compressor, filter and valve, etc., to ensure that there is no oil, moisture or other impurities contamination.
Check gas flow: Check gas flow and pressure periodically to ensure they meet system design requirements. Timely adjustments should be made to prevent unstable flow rate from affecting the stability of oxygen concentration.
2. Select professional system integrator
Experienced integrator:
Select reliable integrator: In order to ensure the stability and efficient operation of the PSA system, it is recommended to select a professional system integrator with rich experience, such as MINNUO. This can guarantee the reliability of the system design and implementation, and minimize the problems of maintenance in the later stage.
Technical support and service: Choose a system integrator that can provide continuous technical support and maintenance to ensure that any problems in the operation of the system can be quickly resolved.
Customized service:
Customized solutions according to needs: Professional integrators can customize the PSA system according to different application scenarios and needs, including gas purity, flow rate and pressure, etc., to ensure that the performance of the equipment is maximized.
3. System Optimization and Automation
Introduction of Intelligent Control and Automation:
Intelligent Monitoring System: In order to improve the efficiency and accuracy of the PSA system, it is recommended to install an intelligent control system, which is capable of real-time monitoring of key parameters, such as gas concentration, temperature, pressure, etc., and provide early warning functions to prevent system abnormalities.
Automatic adjustment function: The system should be equipped with automatic adjustment function, which can automatically adjust the operation state according to different load conditions to ensure stable gas output and avoid waste.
Regular update and optimization:
Continuous optimization: Adopt new technology for PSA system optimization, and constantly upgrade the gas separation and compression technology. The system is regularly updated to ensure that it always meets current industry requirements and maximizes operating efficiency.
4. Regular technical training and operation training
Technical training:
System operation training: Provide regular system operation and maintenance training for operators to ensure that they are familiar with the operating principles of the equipment and common troubleshooting methods. Improve operators’ understanding of the system and their ability to cope with it, which will help to extend the service life of the equipment.
Regular learning of new technologies: As technology advances, regular training of operators to master the latest equipment operation techniques and maintenance knowledge helps to improve work efficiency and safety.
5. Perfect spare parts management and supply chain
Spare parts reserve:
Ensure spare parts supply: In order to ensure the long-term and stable operation of the PSA system, set up a perfect spare parts reserve management system, especially the supply of spare parts for key components such as molecular sieve, filter element, pressure sensor, etc., so as to avoid affecting the normal operation of the system due to the delay in the supply of spare parts.
Select good quality spare parts:
High quality parts: In the process of system maintenance, it is recommended to use high-quality original spare parts and avoid the use of poor quality parts, which will help to improve the stability of the equipment and reduce the failure rate.
6. Comprehensive consideration of environmental factors
Adaptation to environmental conditions:
Environmental adaptability: When selecting a PSA system, the operating environment of the system must be considered. For example, when operating in high humidity, high temperature or high altitude environments, the system design should take into account these special environmental conditions and select the appropriate equipment configuration to ensure stable system operation.
Environmental Monitoring:
Operating Environment Monitoring: Establish a monitoring mechanism to track the operating environment temperature, humidity and other factors of the equipment in real time, and adjust the system parameters in time to cope with the impact of environmental changes on the performance of the equipment.
Conclusion
In the PSA system, the stability of oxygen concentration is a key factor to ensure the long-term and efficient operation of the equipment. Oxygen concentration fluctuations may be affected by several factors, including the performance of the molecular sieve, the stability of the compressor, system pressure fluctuations, and the operating environment. The stability of the PSA system and the continuous output of oxygen concentration can be significantly improved by optimizing the molecular sieve selection, improving the compressor performance, enhancing the air source treatment, and the application of intelligent monitoring system.
Through regular maintenance, monitoring of system parameters, improvement of equipment configuration and selection of high-quality core components, the problem of fluctuating oxygen concentration can be effectively solved to ensure that the PSA system provides continuous and stable oxygen output while operating efficiently and stably. In order to better adapt to different application scenarios, it is crucial to choose high-quality gas equipment, MINNUO gas equipment focuses on gas production, providing innovative and reliable PSA oxygen and nitrogen solutions, with high stability of oxygen output and strong adaptability.