In the modern food industry, enterprises are faced with not only the basic requirements of product freshness, anticorrosion and explosion-proof, but also the need to meet strict quality standards and export specifications. Especially for leisure food, dairy products, fermented beverages and other high value-added products, packaging is no longer just a simple encapsulation, but is related to microbial control, shelf-life extension(Nitrogen filling) and consumer safety of the key nodes. Any loss of control of oxidation and gas instability may lead to product deterioration, recall or even brand damage.
Nitrogen is one of the most common and important protective gases used in food packaging. Through the formation of an “inert atmosphere”, it can effectively isolate oxygen, inhibit oxidation and microbial growth, and is suitable for many scenarios such as MAP, moisture-proof powder filling, and explosion-proof nitrogen filling for alcohol. Especially for those packaging lines that require less than 1% residual oxygen and continuous operation around the clock, the safety and continuity of the nitrogen system will directly determine the stability of the whole production chain and the quality of the finished products.
This article will focus on “industrial nitrogen generator”, combined with its working mechanism, safety advantages and typical application cases, to systematically analyze its practical value in the food packaging line. Whether you are a production supervisor, factory planner, or are looking for an upgrade program for export needs of the quality of the person in charge, this article will provide you with practical decision-making reference.
I. Nitrogen’s Core Safety Functions in Food Packaging
Industrial food packaging is not just about extending shelf life, it is about ensuring that food products are produced, transported and stored in a low-risk, non-polluting and highly stable environment. As an inert gas, nitrogen is widely used to enhance the system safety of food packaging due to its characteristics of not easily reacting with other components, colorless, tasteless and non-toxic, etc., which are reflected in the following five aspects:
1. Inhibit oxidation reaction, extend shelf life and prevent rancidity of fats and oils.
The oils and fats, vitamins and flavor molecules in most food products (e.g., nuts, mayonnaise, puffed snacks, etc.) are highly susceptible to oxidation in air, which can produce a “harrying” taste and a “harrying” smell. The oil, vitamins and flavor molecules in most foods (such as nuts, mayonnaise, puffed snacks, etc.) are highly susceptible to oxidation in the air, resulting in “halo flavor”, discoloration and even rancidity, affecting the taste and nutrition.
Nitrogen alternative packaging can effectively remove the oxygen inside the package, reducing the residual oxygen to less than 1% and significantly slowing down the oxidation rate of lipids. For example, the use of nitrogen-filled potato chips packaging, its shelf life can be increased from 6 months to 9 ~ 12 months.
2. Inhibit the growth of microorganisms (e.g. mold, bacteria) to form an antibacterial environment
Oxygen is necessary for the reproduction of aerobic microorganisms (e.g. Salmonella, E. coli, etc.). Nitrogen can build a low-oxygen or anaerobic environment, limiting bacterial growth from the source, especially suitable for use in food packaging with high microbial safety requirements such as fresh food, cooked food and dairy products.
If used with low temperature cold chain or CO₂ gas mixture, the antimicrobial effect is even better.
3. As filling inert gas in MAP (Modified Atmosphere Packaging)
MAP (Modified Atmosphere Packaging) is one of the main technological paths used by the modern food industry for prolonged freshness preservation. Nitrogen plays a key role in it:
Matching with CO₂ for delicatessen, cheese, instant lunch box, etc., to balance the internal air pressure and anti-bacteria
Matching with O₂ for fresh meat packaging, to prevent the color from darkening and to inhibit the oxidation
Individual nitrogen filling for cookies and cakes, to prevent the powder from flying and deformation
✅ Nitrogen’s role in MAP: to maintain the balance of the internal pressure of the package, to avoid collapsing the bag, condensation, and to guarantee the product’s integrity of the shape.
4. Prevent powdered food from caking, static adsorption and other pollution risks
For powdered products such as protein powder, coffee powder, seasonings, instant soups and other powdered products, the residual oxygen, water vapor and static electricity in the packaging environment will lead to:
caking, affecting the secondary solubility
dust adsorption on the inner wall of the package or equipment, resulting in cross-pollution
loss of aroma, lowering the organoleptic value of the goods
Nitrogen effectively improves this problem by lowering the relative humidity and reducing the static build-up, and it can be used as an alternative to nitrogen to prevent the caking of powdered food. Nitrogen can effectively improve this problem by reducing relative humidity and static buildup, and it can be used as an inert conveying gas for powder weighing, filling and other automated equipment. 5.
5. Forming an explosion-proof gas barrier in alcohol or combustible dust products
Products such as alcohol-containing jellies, alcohol-centered chocolates, flavored beverages, etc., or highly dusty foodstuffs such as whey powder and flour are prone to form explosive atmospheres under conditions of high temperatures, sparks, and electric shocks if they are exposed to the air.
The use of nitrogen as a packaging gas can isolate oxygen from contact with ignition sources, reducing the probability of combustion and explosion. At the same time with positive pressure control system and pressure relief valve, can build explosion-proof level workshop.
Risk type | Nitrogen protection effect |
Oxidative rancidity | Significantly reduce, extend the freshness cycle |
Microbial colonization | Reduce residual oxygen, build a low-oxygen / anaerobic environment |
Dust contamination | Reduce static electricity, inhibit the diffusion of particles |
Bag collapse/deformation | Maintain the internal air pressure, to avoid the collapse of the form |
Flammable explosion risk | Nitrogen inert dilution, isolation of the oxygen source and ignition sources |
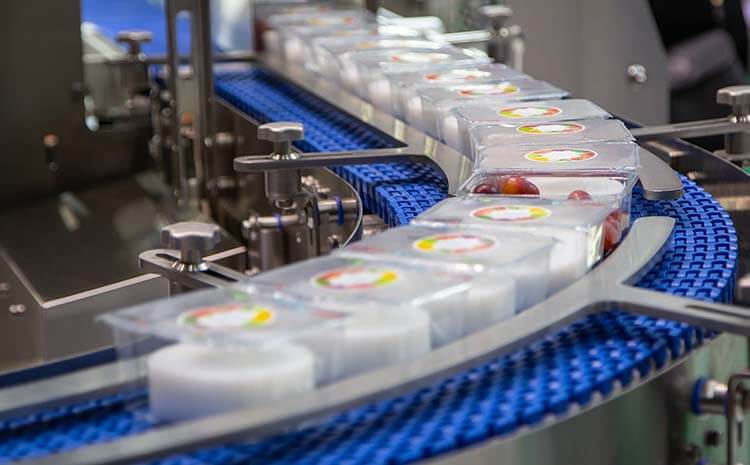
Ⅱ.The working mechanism and advantages of industrial nitrogen generator
In the food industry, nitrogen is no longer a simple packaging gas, but a key component of the production line to guarantee quality, improve efficiency and control safety risks. In order to realize this goal, industrial nitrogen generator, as the core technology to replace the traditional bottled or liquid nitrogen supply, has been adopted by more and more medium and large-scale food processing enterprises in recent years, especially with PSA (Pressure Swing Adsorption) technology as the mainstream.
1. Brief description of the working principle: Introduction to Pressure Swing Adsorption (PSA) and Membrane Separation Technology
PSA (Pressure Swing Adsorption) Principle of Pressure Swing Adsorption:
Carbon molecular sieve through the different adsorption capacity of oxygen and nitrogen molecules in the high and low pressures of the alternating switch to separation. Nitrogen is output through the adsorption tower and oxygen is released under low pressure, thus realizing continuous gas supply.
Membrane Separation Technology (Membrane Separation):
Utilizing the difference in permeation rates of polymer membranes to different gas molecules, it is commonly used for on-site nitrogen supply with medium purity demand (e.g. 90~99%), with simple structure and suitable for small and medium-sized application scenarios.
✅ Note: If the food packaging industry needs to control the residual oxygen ≤1%, most of the scenarios recommend the use of PSA system to get higher purity and output stability.
2. Wide range of controlling nitrogen purity, adapting to the diversified needs of food packaging
The requirements for nitrogen purity in food packaging lines vary depending on the type of product, for example:
Product Type | Recommended Nitrogen Purity | Purpose of use |
Inflated food/nuts/bakery | ≥99% | Resistance to oxidation, moisture, maintenance of structure |
Liquor-centered chocolate/flavored powders | ≥99.5% | Antioxidant, electrostatic protection, resistance to explosion risk |
High-end export canned/frozen foods | ≥99.9%~99.999 | Control of residual oxygen, meeting export standards |
PSA system can realize high precision output from 95% to 99.999% by adjusting the adsorption tower pressure, cycle and carbon molecular sieve loading method, and support online oxygen content monitoring and alarm linkage.
3. Safety Advantage: Avoiding the hidden danger of liquid nitrogen or high-pressure gas cylinders
Compared with the traditional liquid nitrogen tank/cylinder system, the industrial nitrogen generator has significant on-site safety advantages:
Safety Dimensions | Cylinders/liquid nitrogen | PSA system |
Gas Storage Risks | High pressure/low temperature, there is a potential risk of bursting | Atmospheric or medium pressure (0.3~0.6MPa), stable |
Operational Requirements | Frequent replacement, easy to misconnect | Automatic operation, remote control |
Transportation and Handling | Occupies a large area, often in and out of the plant | Local nitrogen production, no need for external transportation |
System Monitoring | Relies on manual inspection | Support PLC system + gas sensing linkage |
✅ It has been proved that the accident rate of equipment in workshops using PSA nitrogen system can be reduced by more than 60%, and the labor intensity of operators and the working environment can be improved effectively.
4. Realize continuous and stable gas supply and improve the operation efficiency of production line
Food packaging production beat is fast, and the requirement for gas supply continuity is extremely high, especially for MAP air-conditioning packaging line, automatic filling equipment, rotary weighing system, etc., which are extremely sensitive to fluctuations in gas supply. PSA nitrogen generator has the following system advantages:
Dual towers run alternately to ensure uninterrupted gas supply all day and all night;
buffer tank + nitrogen flow automatic adjustment module to meet peak load switching; optional remote monitoring/abnormal warning system, which can be used for monitoring and monitoring of nitrogen supply; buffer tank + nitrogen flow automatic adjustment module. The buffer storage tank + nitrogen flow automatic adjustment module can meet the peak load switching;
can be equipped with optional remote monitoring/abnormal warning system to reduce the risk of production shutdown;
supports the night-time pressure preservation mode/low-power operation strategy, which saves energy and reduces carbon emissions.
Application suggestions: for packaging workshops with daily nitrogen output ≥1000Nm³, it is recommended to configure dual tower + online purity control + flow regulation system to achieve the best balance between energy and operation.
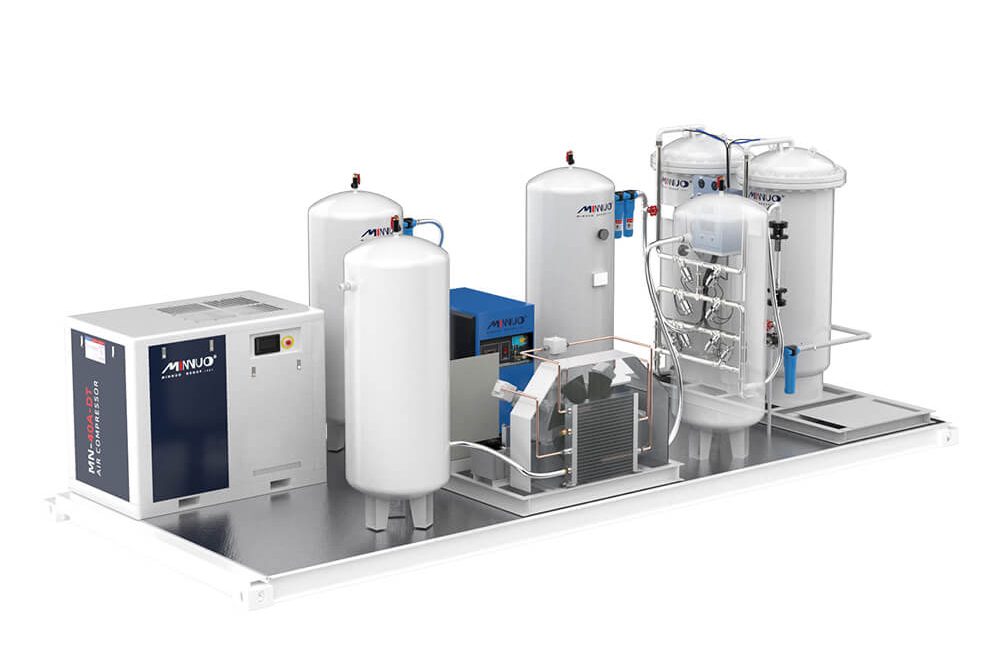
Ⅲ.How to specifically enhance the safety of food packaging lines
How Industrial Nitrogen Systems Enhance Safety on Food Packaging Lines
In the food industry, the safety of the packaging line does not only refer to the stable operation of the equipment itself, but also includes the control of the gas supply, the prevention of potential explosion risks, and the health protection of the operators. In the food industry, safety on packaging lines is not only about the stable operation of the equipment itself, but also about the control of the gas supply, the prevention of potential explosion risks, and the health of the operators. The introduction of industrial nitrogen generators, especially the localized nitrogen supply system based on PSA technology, can eliminate the many hidden dangers of external gas supply from the root, and at the same time build an intelligent and standardized food safety defense line.
1. Eliminate the transportation and operation risks of handling high-pressure cylinders
Traditional liquid nitrogen tanks or high-pressure nitrogen cylinders have the following safety risks:
poisoning, fire or explosion risks caused by dumping, misconnection, leakage of cylinders, etc.;
cold burns or equipment damage caused by the extremely low temperature of liquid nitrogen (-196 ℃);
a large number of manual labor is occupied by multiple handling, and there are human errors in operation.
✅ The introduction of nitrogen generator can realize “in-situ nitrogen production, no need to carry”, and through the fixed installation system to realize the sealing of the gas flow path, effectively avoiding misoperation and leakage or impact accidents during transportation. 2.
2. Reduce residual oxygen and gas, reduce the risk of oxidation and contamination
Food deterioration is often associated with oxygen residue, high oxygen environment not only promotes the oxidation of fats and oils, but also prone to microbial growth and poor taste of the product.
Advantages of PSA nitrogen system:
Online nitrogen purity monitoring and residual oxygen alarm (residual oxygen <1%);
Continuous output of nitrogen with stable concentration, avoiding oxygen seepage caused by “high and low switching”;
Linkage with automatic packaging machine, avoiding contamination caused by lag of gas switching.
Typical applications: cooked food, snack food, nuts, milk powder packaging line. 3.
3. Reduce the risk of flammable and explosive, and improve the explosion protection level
Certain food additives (such as flavors), wine heart food, seasoning powder, etc. contain flammable volatiles or dust particles, and have the possibility of explosion in the environment where oxygen and static electricity exist at the same time.
Advantages of nitrogen protective layer:
Use nitrogen dilution to form an inert atmosphere, preventing the spread of open flame;
Form a continuous gas barrier in the process of canning, mixing and sealing;
Prevent “dust cloud” and detonation due to pressure difference in the powder filling line.
✅ Recommended configuration: Nitrogen flow rate regulator + dust collection device + high-purity nitrogen capping protection module. 4.
4. Enhance automation control and alarm linkage capability
Modern food factory emphasizes on “unmanned” and “intelligent linkage”, and the nitrogen system needs to be equipped with corresponding intelligent identification and emergency disposal capability.
Configuration suggestions:
PLC intelligent linkage control, realizing the whole chain feedback of flow, pressure, purity and abnormal working conditions;
online nitrogen concentration monitoring > real-time adjustment of the output or trigger alarms;
can be docked with the production line MES system, which can record the gas parameters to meet the traceability requirements.
Suggestion: Integrate the online monitoring module with the nitrogen generator to avoid additional interface interference.
5. Ensure workers’ operation safety and health environment
In the past, production lines using high-pressure cylinders required workers to frequently change, lift and load, and release pressure, which had high labor intensity and occupational health hazards:
Gas cylinders falling and injuring people, mistakenly connecting to pure oxygen during operation → high risk;
Nitrogen leakage concentration in the working area is too high, and the risk of hypoxia is increased.
✅ PSA system solution:
Remote monitoring + automatic drainage + unattended, greatly reducing manual intervention;
can be configured with oxygen concentration alarm, forming a secondary safety barrier in the crowded area.
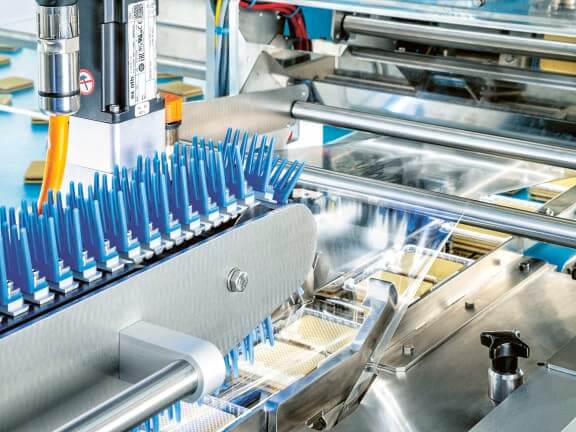
Ⅳ.Case Study: Real-World Safety and Efficiency Gains
Deploying industrial nitrogen generator system in food packaging production line can not only optimize the cost of gas usage, but also significantly improve the effect of product freshness and the level of intrinsic safety of the workshop. The following are three typical application case studies from actual factories:
✅ Case 1: Puffed food factory introduced PSA nitrogen system, oxidation rate dropped by 30%, monthly cost savings of 20%
Background Problems: A puffed food factory has long relied on bottled nitrogen, and there were problems such as high residual oxygen and incomplete packaging every time it was filled, resulting in a high rate of return of finished products, and increased oxidation of fats and oils.
Solution:
adopt 10Nm³/h PSA nitrogen generator;
set the purity at ≥99.5%, and linkage nitrogen filling and sealing equipment;
equipped with online residual oxygen monitor to realize residual oxygen <1%.
Improvement effect:
Oxidation reaction is obviously slowed down, and the shelf life of the product is extended to 1.5 times of the original one;
The average monthly return rate is reduced by about 30%, and the cost of nitrogen purchasing and artificial bottling is saved by about 20%;
meets the standard of oxygen content of exported prepackaged food.
Promotion Suggestion: Applicable to leisure food, puffed food, seasoning powder, custard and other oxygen-sensitive packaging categories.
✅ Case 2: Kiwifruit air-conditioned preservation warehouse uses nitrogen to seal and condition the air, extending the shelf life by 3 weeks.
Scenario Description: A fruit cold chain logistics park adopts the ordinary air conditioning system, but there are still problems such as softening and taste degradation right out of the warehouse, making it difficult to enter the high-end fruit market.
Deployment plan:
install 15Nm³/h PSA nitrogen system for dynamic nitrogen replenishment in cold storage;
equip with low-oxygen environment system, with oxygen concentration controlled at 2%~3%;
automatically link CO₂ and humidity controllers to optimize the overall storage atmosphere.
Effectiveness evaluation:
Extend the shelf life of kiwifruit by more than 3 weeks from picking to terminal sales;
Reduce the rate of transportation pressure loss by nearly 60%;
Enter the supply chain system of super-exporters of high-quality fruits.
Promotion suggestions: Applicable to kiwifruit, blueberries, avocado, cherries and other high value-added fruits warehousing scenarios.
✅ Case 3: Upgrading Nitrogen System in Alcoholic Juice Packaging Workshop to Improve Safety Level by 1 Grade
Background: A beverage factory produces fruit-flavored alcoholic beverages, with static electricity and gas evaporation from packaging materials and can sealing stations, which need to be rectified in accordance with the requirements of the new version of the safety regulations.
Retrofit program:
Deploy high-purity PSA nitrogen containment systems in the mixing, storage and filling areas;
Linkage of explosion-proof sensors to form an “inert isolation air curtain”;
Interconnect data with the existing fire alarm system.
Effect of the modification:
Alcohol residual gas concentration is <10% for a long period of time, which is far below the lower explosion limit;
The overall safety level of the plant has been upgraded from Zone 2 to Zone 1, and the plant has successfully passed the annual fire safety audits and the EHS risk assessment;
The visualization of alarms and linkages at the management end has significantly reduced the frequency of manual inspections.
Suggestions for promotion: Applicable to the workshop of wine mixing, confectionery, flavors and fragrances, and concentrated sauces.
Conclusion
Under the background of food packaging increasingly pursuing “shelf-life extension, safety protection and production intelligence”, industrial nitrogen generator has become one of the key equipments for modern food enterprises to improve product safety and operation stability by virtue of its advantages of high purity, low residual oxygen and automatic joint control. Through continuous nitrogen supply, residual oxygen control and explosion protection, nitrogen systems not only improve product freshness, but also significantly reduce rework and risks associated with gas fluctuations.
MINNUO, as a dedicated manufacturer of gas solutions, offers high-purity PSA nitrogen generator systems for the food industry that support modular deployment, online monitoring of oxygen concentration, and intelligent linkage with packaging line PLCs. Whether it is leisure food, alcoholic beverages, or cold chain fruit and vegetable packaging plant, MINNUO can customize safe, energy-saving and easy-to-maintain nitrogen solutions according to the scenarios, helping customers build a standardized and intelligent food production system.