With the rapid growth of on-site nitrogen production demand, membrane nitrogen generators have gradually become one of the important choices for nitrogen production solutions due to its high efficiency, simplicity and reliability. In this paper, we will analyze the working principle, differences in gas behavior and application advantages of membrane separation technology to help users understand the practical application value of membrane nitrogen generation system.
Compared with the traditional Pressure Swing Adsorption (PSA) or cryogenic separation technology, membrane separation has multiple advantages such as natural dehumidification, energy saving and consumption reduction, continuous and stable operation, lightweight structure, and adaptability to harsh environments, etc. Especially in the small and medium flow rate, high continuity of the operation of the scenarios with outstanding performance, and it has become one of the favored nitrogen production solutions in many industries.
If you are looking for an efficient, flexible and low-maintenance nitrogen production system, or want to understand the deeper scientific logic and practical application potential behind membrane technology, this article will provide you with a clear, systematic and professional interpretation with great reference value.
I. Introduction to the basic structure of membrane nitrogen generator
As a kind of high-efficiency, compact and low-maintenance gas separation equipment, the membrane nitrogen generator has a simple overall structure, but the core components and technical logic are very precise. Correct understanding of its basic structure will help users make scientific judgment in the selection, use and maintenance process.
Necessary supporting equipment: compressor (to provide raw gas pressure)
The role of the compressor: to provide continuous, stable and a certain pressure (usually 0.3 ~ 1.0MPa) of compressed air as the raw gas for membrane separation.
The compressed air needs to undergo pre-treatment, including filtration, oil removal, water removal, dust removal, etc., to ensure the long-term stable operation of the membrane module and to avoid contamination and blockage.
Core indicators: flow rate, stability, dryness, which directly affects the service life of the membrane and the effect of nitrogen production.
Key Component: Membrane Module (composed of thousands of hollow polymer fibers)
The core component of the membrane module consists of thousands of hollow fibrous polymer membranes neatly aligned to form a high-density bundle of membranes, which are encapsulated in a protective housing.
Advantage of fiber number: A large number of fine fibers can simultaneously provide a huge permeable area, improving the efficiency of gas treatment per unit volume.
Module expandability: According to the size of gas consumption, you can flexibly choose a single membrane bundle, a small membrane group or multiple parallel membrane systems, with high customization flexibility.
Microstructural properties of membrane fibers: molecular screening mechanism
Principle: Each membrane fiber wall is covered with very small pores, with selective permeability.
Screening mechanism: based on the molecular size of gas molecules and dissolution-diffusion rate differences, different gases pass through the membrane wall at different speeds:
water vapor (H₂O): the fastest, rapid penetration;
Oxygen (O₂): the second fastest, can be gradually penetrated;
Argon (Ar), nitrogen (N₂): penetration speed is very slow, mainly left inside the fiber.
End result: water vapor and oxygen are preferentially discharged, leaving high purity nitrogen.
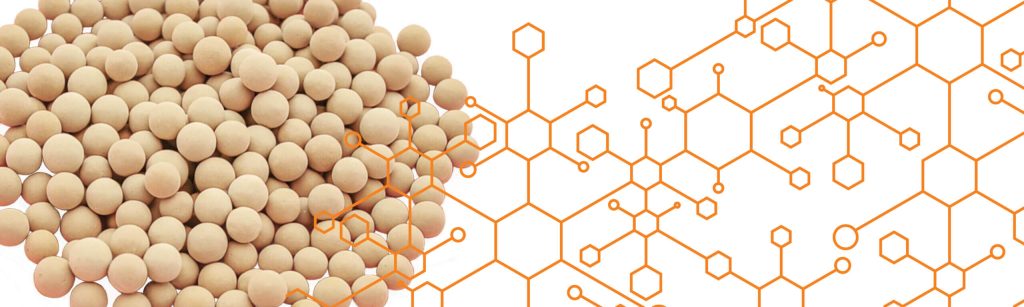
Components | Main Functions |
Compressor | Provides a constant supply of high-pressure air |
Pre-treatment | System Removes impurities and protects the membrane module |
Membrane Module (Hollow Fiber) | Performs the task of separating the gases and filtering the nitrogen |
Control System (optional) | Monitors the pressure, flow rate, and temperature to improve the stability of system operation |
Supplementary: Membrane Nitrogen Generator System Design Notes
Need to ensure that the compressed air inlet is clean and dry, to reduce the long-term damage of moisture on the membrane material;
The design should take into account the membrane module is easy to disassemble, easy to replace, and convenient for the optimization of the maintenance cycle;
Multi-modules in parallel need to be reasonably allocated to the intake volume, to avoid the uneven loading led to the decline in the efficiency of the membrane.
Ⅱ.The working principle of membrane separation in detail
Membrane nitrogen generator can efficiently separate nitrogen from air, the key lies in the unique physical separation mechanism of its internal membrane module. The overall process can be divided into three core links, each link closely linked to ensure continuous, stable, high-purity nitrogen output.
2.1 Air Supply and Entry into Membrane Module
Compressed Air Source:
Raw air must first be pressurized by a compressor, usually to 0.3-1.0MPa, to provide enough power to drive the gas through the membrane module.
Pre-treatment of front-end air source:
Before the compressed air enters the membrane module, it must go through a strict pre-filtration system, including oil removal, dust removal, water removal and other steps.
Purpose: to protect the membrane fiber, to avoid oil, water, particles clogging or damage to the microporous, to extend the service life of the membrane.
Entering the Membrane Module:
Purified high-pressure air is uniformly fed into the membrane module containing thousands of hollow polymer fibers to start the separation process.
✅ Core Understanding: The cleanliness of the air source directly determines the stability and final quality of the membrane separation system.
2.2 Permeation Mechanism
The nature of membrane separation relies on the difference in permeation rates of different gases through the membrane fiber walls, which is mainly related to the size, solubility and diffusion rate of the gas molecules.
Water vapor (H₂O):
small molecule size and very fast diffusion;
preferentially passes through the membrane wall and is quickly excluded from the membrane module.
Oxygen (O₂):
medium molecular size, fast diffusion rate;
can penetrate faster and be expelled with water vapor, but slightly slower than water vapor.
Argon (Ar) and Nitrogen (N₂):
large molecular size, slow diffusion;
most of the nitrogen and part of the argon is retained inside the membrane fiber, not easy to pass through the membrane wall.
✅ Core understanding: Different gases “escape” at different rates, and membrane modules actually utilize this natural diffusion difference to achieve selective separation.
2.3 Gas Flow Separation
Outlet Channel (Penetrating Gas):
Permeated water vapor and oxygen are guided out of the membrane housing and safely released or disposed of in a centralized manner;
This portion is usually discharged through a separate pipeline to avoid contamination of the produced gas.
Gas production channel (retained gas):
Nitrogen (N₂) that remains inside the membrane fibers and is not permeated out is collected internally to form the final output product gas;
According to the application requirements, the number of membranes and the speed of air flow can be adjusted to achieve the output of nitrogen with different purities (generally 90%~99%).
✅ Core understanding: two independent gas flow directions are actually formed inside the membrane module to collect different components, thus realizing efficient gas separation.
Step | Process Description | Critical Control Points |
Air Supply | High-pressure clean air is fed into the membrane module | Compressor output is stable, clean and dry air source |
Permeation Screening | Differential diffusion rates of gas molecules are utilized to give priority to water vapor and oxygen to penetrate the membrane wall | Membrane fiber quality, smooth discharge channels |
Airflow Separation and Collection | Permeate the permeate gas to discharge and collect the nitrogen gas to be collected as product gas | Nitrogen Gas Collecting System Sealability and Flow Control |
Ⅲ.The membrane separation process of the differences in the behavior of each gas analysis
In the membrane nitrogen generator, different gases due to the molecular size, solubility and diffusion rate is different, the speed of its penetration of the membrane fibers and the treatment of significant differences:
Water vapor (H₂O)
Penetration rate is very fast, almost instantaneous through the membrane wall, so it is quickly discharged from the system, and play a natural dehumidification effect.
Oxygen (O₂)
Penetrates faster and is partially expelled, with a small amount remaining. The purity of nitrogen production can be further enhanced by precise control of the flow rate.
Argon (Ar)
The permeation rate is slower, most of it is retained in the membrane, but some of it is exported together with nitrogen, which slightly affects the purity of nitrogen.
Nitrogen (N₂)
Has the slowest penetration rate and is mainly retained within the hollow fibers, and is ultimately collected and exported as product gas.
Gases | Penetration rate | Treatment |
Water vapor (H₂O) | Very fast | Fast exhaust |
Oxygen (O₂) | Faster | Exhaust or slight residual |
Argon (Ar) | Slow | Retained, partially exported with N₂ |
Nitrogen (N₂) | Slowest | Mainly retained, captured as a product gas |
Ⅳ.The main advantages of membrane technology is summarized
Membrane separation technology as an advanced means of gas separation, in the actual application shows a variety of advantages:
Drying nitrogen output
Due to the priority of water vapor molecules rapid penetration and discharge, membrane technology in the separation process naturally completed air drying, without additional dehumidification equipment, especially suitable for the gas dryness of the high requirements of the industry.
Energy Saving and Consumption Reduction
Users can choose different purity outputs according to the actual demand.The compressed gas volume can be significantly reduced for low purity applications, which reduces energy consumption and optimizes operating costs.
No need for complex cycle switching system
Unlike the traditional PSA variable pressure adsorption, the membrane system realizes continuous flow separation without valve switching action, which makes the system simple, stable in operation and low in maintenance requirement.
Compact structure, small footprint, simple maintenance
The overall modular design of the membrane nitrogen generator makes the equipment small in size and light in weight, flexible in installation, suitable for space-constrained or mobile deployment scenarios, and easy for routine maintenance.
Adaptable to harsh environments
Whether in coastal operation areas with high humidity and high temperature, or in field environments with huge temperature differences, membrane technology can maintain efficient operation and is highly adaptable.
✅ Summary: Membrane technology is the preferred solution for today’s high-efficiency nitrogen production in many industries due to its high efficiency, energy savings, reliability and flexibility.
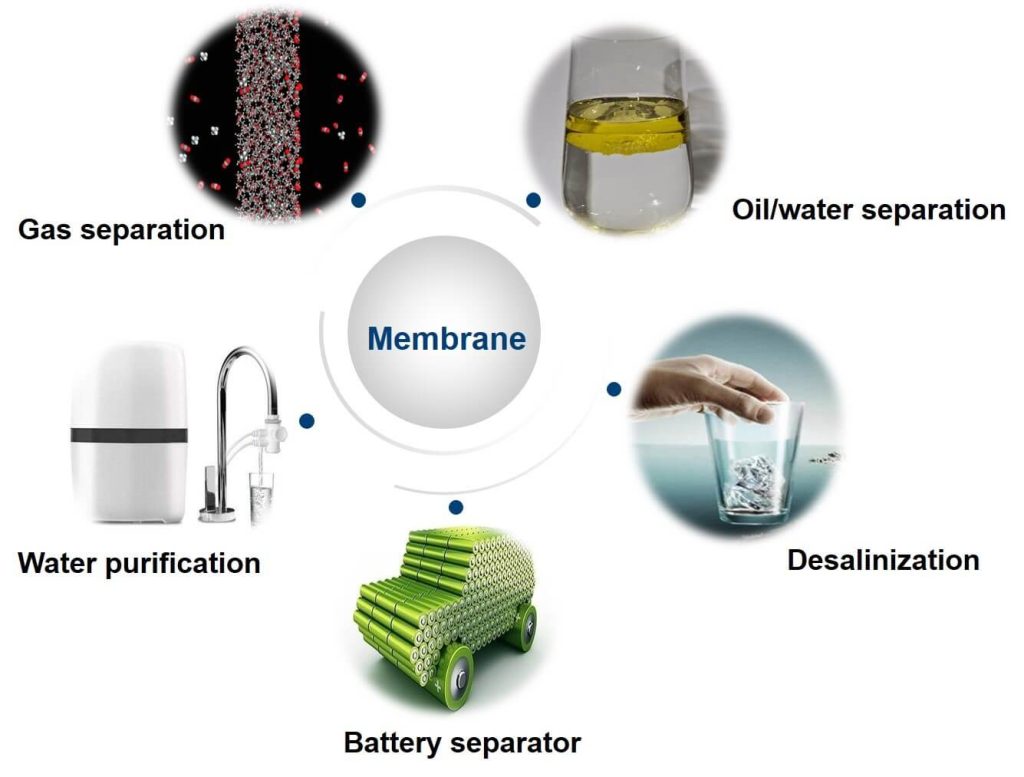
Membrane Technology Application Scenario Recommendation Chart
Application Scenarios | Major demand | Membrane Technology Advantages |
Offshore Oil Platforms | Explosion-proof inert gas supply, corrosion-resistant, continuous and stable | Compact and corrosion-resistant module, no need for cycle switching, stable and reliable |
Food Packaging Lines | Nitrogen replacement for preservation of freshness, requiring dry high-purity nitrogen | Natural dehumidification, high dryness nitrogen output |
Pharmaceutical & Bioengineering | Nitrogen protection, preventing oxidative contamination of pharmaceuticals | Continuous gas supply, flexible and adjustable purity |
Electronics & Semiconductor Manufacturing | Nitrogen environmental protection, avoiding moisture and oxygen erosion | High dryness nitrogen output, continuous operation without interruption |
High Plateau Field Operations | Portable nitrogen supply to cope with harsh environments | Light structure, small footprint, adaptable to high humidity/high-temperature environments |
Mobile Emergency Gas Supply System | Rapid deployment, mobility | Flexible installation, no need for complex infrastructure support |
Internal Factory Gas Station Retrofit | Reducing costs and increasing efficiency, energy conservation and reduction of consumption | Adjustment of purity according to the needs of low-energy operation |
Conclusion
Through the systematic analysis in this paper, we can see that the membrane separation technology, utilizing the natural physical mechanism based on the difference in molecular diffusion rates, achieves continuous, stable, and highly efficient nitrogen production without the need for a complex switching system.
Membrane nitrogen generators are compact, easy to maintain, and have excellent energy efficiency, especially suitable for on-site nitrogen production applications with small to medium flow rates, high continuity of operation, and high environmental adaptability.
With the continuous upgrading of membrane materials and manufacturing processes, membrane separation technology will continue to play an increasingly important role in high-end manufacturing, food and pharmaceutical industry, electronics industry, field operations and other fields. Membrane nitrogen generators are undoubtedly the preferred solution for users who want to realize lightweight, intelligent and flexible deployment of equipment.
As a professional gas equipment manufacturer, MINNUO has long been focusing on the R&D and export of portable nitrogen generation, membrane nitrogen generation, and industrial centralized gas supply systems, providing a complete set of optimized design from compressor, air pretreatment to membrane module to ensure the equipment to achieve high efficiency, reliability, and low energy consumption operation in different application scenarios.
If you are looking for an efficient, flexible and stable nitrogen generation system, MINNUO will be your reliable partner!