Laser cutting technology has become an essential process in modern manufacturing, particularly in metalworking, where the use of nitrogen significantly enhances cutting quality and efficiency. However, selecting the right nitrogen generator for laser cutting to ensure high purity, stability, and cost-effectiveness is key to standing out in a competitive market. This article will explore the important considerations for choosing nitrogen generation equipment in the laser cutting industry, focusing on nitrogen requirements, selection criteria.
When selecting a nitrogen generator for the laser cutting industry, it is essential to consider key factors such as nitrogen purity, flow rate, and pressure. First, high-precision metals, such as 304 stainless steel and 6061 aluminum alloy, require nitrogen purity of 99.99% or higher. Second, the appropriate flow rate and pressure should be selected based on material thickness and cutting speed. Additionally, the reliability of the nitrogen generator and the supporting equipment (such as compressors, filters, and dryers) must be given priority to ensure stable gas supply.
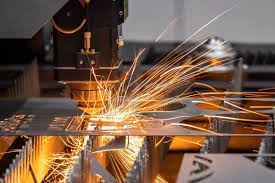
Nitrogen Requirements in Laser Cutting
The Core Role of Nitrogen
In laser cutting, nitrogen serves several critical purposes:
- Prevents Oxidation: As an inert gas, nitrogen displaces oxygen around the cutting area, preventing oxidation of the metal material and maintaining clean, rust-free cutting edges. This is especially crucial for high-end metal cutting, such as 304 stainless steel and 6061 aluminum alloys.
- Ensures Consistent Cutting: High-purity nitrogen provides a stable cutting environment, ensuring consistent quality, making it ideal for precision and repeatable manufacturing applications like aerospace and precision machinery.
- Increases Cutting Speed and Quality: Nitrogen does not react with the heated metal, increasing cutting speed and reducing the risk of material deformation or damage. The result is smoother, cleaner cutting edges.
Specific Nitrogen Requirements
Laser cutting has strict requirements for nitrogen:
- Purity: Nitrogen with a purity of 99.99% is required for cutting stainless steel (e.g., 304) or aluminum alloys (e.g., 6061), and for high-precision cutting, nitrogen purity may need to reach 99.999% (Grade 5.0).
- Flow Rate: The flow rate depends on material thickness. For example, cutting 6mm thick stainless steel typically requires a flow rate of 50-100 Nm³/h, while thicker materials, such as 12mm stainless steel, may require a flow rate of 150 Nm³/h to effectively blow away slag and maintain a clean cut.
- Pressure: Laser cutting typically requires nitrogen pressures of 15-25 bar to ensure stable cutting, especially when working with thicker materials or faster cutting speeds. Insufficient pressure can lead to incomplete cuts or rough edges.
Advantages of Nitrogen Generators
Using a nitrogen generator onsite offers several advantages compared to traditional liquid nitrogen supply:
- Cost-Effectiveness: Although nitrogen generators have a higher initial investment, their long-term operating costs are lower, reducing nitrogen usage costs by approximately 50%-70%.
- Environmental Benefits: Nitrogen generators separate nitrogen from the air without the need for transportation and storage of liquid nitrogen, reducing carbon emissions and aligning with sustainability goals.
- Continuous Gas Supply: Nitrogen generators provide continuous, automated gas supply, avoiding production interruptions due to liquid nitrogen shortages—particularly crucial for laser cutting applications that require uninterrupted nitrogen supply.
- Ease of Maintenance: The equipment is easy to maintain, requiring only periodic replacement of key components like filters and carbon molecular sieves to ensure stable operation. Additionally, nitrogen is generated onsite, reducing the maintenance and safety management work associated with liquid nitrogen storage.
How to Choose the Right Nitrogen Generator
Nitrogen Purity
- Matching Purity to Material: When cutting high-end materials like stainless steel (e.g., 304, 316L) or aluminum alloys (e.g., 6061), nitrogen with a purity of 99.99% or higher is necessary to avoid oxidation and surface defects. For cutting carbon steel, a slightly lower purity nitrogen may be suitable to lower costs.
- Stable Supply of High-Purity Nitrogen: High-end laser cutting requires stable, high-purity nitrogen. Choose nitrogen generation equipment with advanced gas separation technology to ensure a continuous, high-purity supply.
Nitrogen Flow Rate and Pressure
- Matching Flow Rate and Thickness: For cutting thicker materials like 12mm stainless steel, nitrogen flow rates of 150 Nm³/h and pressures of 25 bar are required to ensure cutting quality and speed. Insufficient pressure may result in incomplete cuts or rough edges.
- Reference Parameters: When selecting a nitrogen generator, refer to specifications for flow rate and pressure. For instance, the MINNUO MN-PG500 nitrogen generator provides 99.999% nitrogen purity and a flow rate of up to 500 Nm³/h, suitable for demanding laser cutting applications.
Importance of Auxiliary Equipment
- Compressor Performance: The compressor is a critical component of the nitrogen generation system, directly affecting nitrogen production efficiency. MINNUO uses Atlas compressors to ensure a stable, abundant gas supply for reliable operation.
- Filters: The Hankison high-efficiency filters used by MINNUO remove moisture and impurities from compressed air, ensuring high nitrogen purity. The filter’s performance directly impacts the adsorption efficiency of the carbon molecular sieve and overall nitrogen generation efficiency.
- Dryers: Cold and adsorption dryers are used to remove moisture from compressed air, ensuring the gas is dry and preventing damage to the molecular sieve. In high-humidity environments, an adsorption dryer can further improve dehumidification.
- Air Pre-treatment: If the nitrogen generation equipment is installed in environments with poor air quality or corrosive gases, pre-treatment equipment such as corrosion-resistant coatings or stainless steel casings should be used to protect the system and extend its lifespan.
Reliability and Stability
- Gas Supply Guarantee: The nitrogen generator must have high reliability and automated protection features to ensure stable gas supply. MINNUO’s nitrogen generators are equipped with advanced PLC control systems that monitor nitrogen purity, flow, and pressure in real-time, ensuring efficient and stable operation.
- Alarm Systems: The system should include comprehensive alarm and protection functions, such as nitrogen purity monitoring alarms and high-temperature overload protection. In the event of an anomaly, the system will alert operators and automatically switch to backup gas sources, ensuring no interruption in production.
- Ease of Maintenance: Key components such as filters and carbon molecular sieves should be easy to maintain and replace. The supplier should offer comprehensive technical support and training to ensure the equipment remains reliable and easy to maintain.
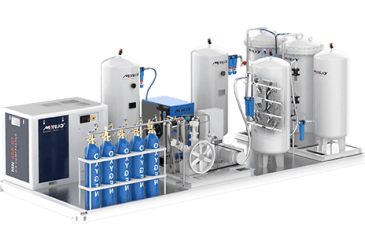
Nitrogen Generation Methods
Pressure Swing Adsorption (PSA) Nitrogen Generation
PSA nitrogen generators operate on the principle of pressure swing adsorption, using carbon molecular sieves to selectively adsorb oxygen and impurities from the air to produce high-purity nitrogen:
- High Purity: PSA generators can produce nitrogen with purities up to 99.999%, ideal for laser cutting applications requiring high nitrogen quality.
- Wide Flow Range: PSA systems can provide various flow rates, making them suitable for laser cutting applications of all sizes, especially those requiring large, stable nitrogen flows.
- Suitable for Precision Applications: PSA generators offer high purity and flow characteristics, making them ideal for high-precision, high-quality laser cutting environments.
Membrane Separation Nitrogen Generation
Membrane separation systems separate nitrogen and oxygen based on their different permeation rates through a membrane:
- Simple Design and Small Size: Membrane nitrogen generators are simple and compact, making them ideal for factories with limited space.
- Lower Energy Consumption: Membrane separation systems consume less energy, making them suitable for applications that do not require extremely high nitrogen purity, such as small to medium-sized enterprises.
- Suitability: Membrane separation is ideal for applications with lower purity and volume requirements, but it is not suitable for large-scale production requiring high-purity nitrogen.
Advantages of MINNUO Nitrogen Generators
High Efficiency and Stability
- High-Precision Carbon Molecular Sieves: MINNUO nitrogen generators use advanced, high-precision carbon molecular sieves to effectively separate oxygen and impurities, ensuring nitrogen purity up to 99.999%—meeting the high standards required by laser cutting.
- Variable Frequency Compressor: Equipped with an Atlas variable frequency compressor, MINNUO generators offer a 20%-30% improvement in energy efficiency compared to traditional fixed-speed compressors.
- Advanced PLC Control System: MINNUO nitrogen generators use Siemens PLC systems to monitor nitrogen purity, flow, pressure, and other parameters in real-time, ensuring optimal performance and system stability.
- Multiple Protection Mechanisms: MINNUO generators include alarms and automatic protection functions for high temperatures, low pressure, and excess impurities, with automatic switching to backup gas sources to ensure uninterrupted operation.
Customized Solutions
- Tailored to Customer Needs: MINNUO can customize nitrogen purity (e.g., 99.9%, 99.99%, 99.999%), flow rate (from 100 Nm³/h to 1000 Nm³/h), and pressure (up to 30 bar) to meet specific production requirements.
- Specialized Environment Adaptations: For challenging environments like high altitudes or corrosive conditions, MINNUO offers enhanced durability designs, such as corrosion-resistant stainless steel casings, special coatings, and efficient air pre-treatment systems.
- Modular Design: MINNUO generators use a modular design for easy expansion and maintenance, allowing customers to adjust the system based on production needs.
Cost-Effectiveness and Service
- Performance and Price: MINNUO nitrogen generators offer high performance at competitive prices. Compared to other brands, MINNUO excels in nitrogen purity, energy efficiency, and reliability, offering a more economical overall cost of ownership.
- Comprehensive After-Sales Service: MINNUO provides 24/7 technical support and rapid response after-sales services, including equipment installation, operation training, and regular maintenance to ensure smooth operation.
- Long-Term Spare Parts Supply: MINNUO commits to providing long-term
spare parts and upgrades, reducing the risk of downtime and ensuring continued optimal performance over the lifetime of the equipment.
Conclusion
Selecting the right nitrogen generator for laser cutting is crucial for ensuring high-quality cuts, consistent production, and cost-efficiency. The nitrogen generator should meet specific purity, flow, and pressure requirements for the materials being cut. MINNUO’s nitrogen generators offer high purity, energy efficiency, and reliability, providing tailored solutions for a variety of applications in the laser cutting industry. With a focus on performance, service, and customization, MINNUO nitrogen generators are the ideal choice for manufacturers seeking stable, high-quality cutting performance.