Pressure Swing Adsorption (PSA) technology is a widely used method for oxygen production in both industrial and medical fields. By utilizing the adsorption properties of oxygen and nitrogen in the air, combined with pressure fluctuations, PSA technology can effectively separate nitrogen from oxygen, producing high-purity oxygen. In this process, the adsorbent plays a crucial role as the core material for gas separation. The selection of adsorbents directly impacts the efficiency, purity, and longevity of the system.
When selecting an adsorbent for PSA oxygen generation equipment, several factors should be considered: adsorption capacity, desorption capacity, mechanical strength, chemical stability, and service life. An ideal adsorbent should exhibit high selectivity for nitrogen adsorption, ensuring oxygen enrichment, and should be able to perform stably under pressure fluctuations. The choice should also take into account factors such as gas composition, operating pressure, temperature, and cost-effectiveness. Common adsorbents include LiLSX lithium-based molecular sieves, which perform excellently in high-purity oxygen production with long service life and sulfur resistance; and 5A molecular sieves, which are suitable for medium-purity oxygen production and offer good cost performance. Activated carbon and silica gel are used for dehydration and gas purification.
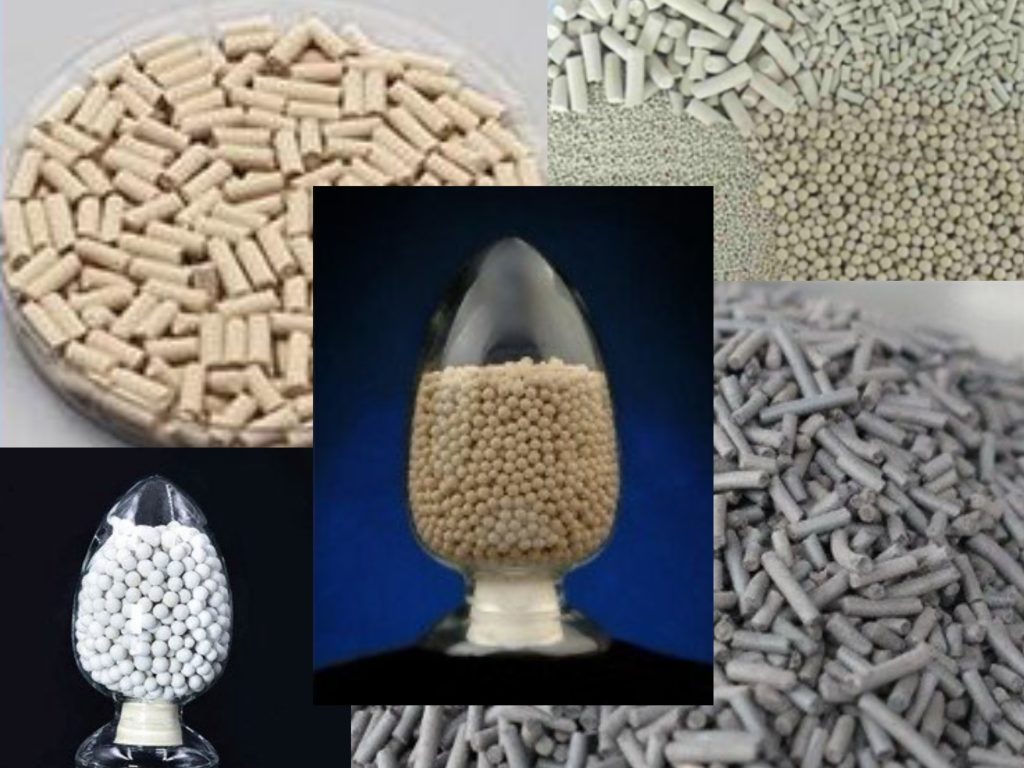
Principles of Pressure Swing Adsorption and the Role of Adsorbents
PSA oxygen generation systems primarily rely on the selective adsorption of gas components by adsorbents under varying pressure. By adjusting pressure, nitrogen in the air is adsorbed, while oxygen is enriched in the gas phase and separated. The principle is that compressed air enters the adsorption bed, where, under high pressure, nitrogen, with its larger molecular size and stronger polarity, is adsorbed by the adsorbent. Oxygen, due to its smaller polarity, is less adsorbed, remaining in the gas phase and collected.
Adsorbents play a vital role throughout the PSA oxygen generation process. Their selection not only affects the oxygen purity but also impacts the system’s operational efficiency and stability. Typically, the choice of adsorbent is based on its ability to selectively adsorb specific gas molecules. By choosing the right type of adsorbent, oxygen production can be optimized.
Basic Performance of Adsorbents
When selecting an adsorbent, its basic performance, including the following aspects, should be considered:
- Adsorption Capacity: The ability of the adsorbent to adsorb nitrogen is the most critical factor in the PSA oxygen generation process. The adsorbent needs to selectively adsorb nitrogen while minimizing oxygen adsorption to improve oxygen purity.
- Desorption Capacity: The adsorbent must have good desorption performance, rapidly releasing nitrogen when pressure is reduced. Desorption efficiency directly affects the system’s cycle time and gas production efficiency. In high-speed applications, improved desorption can significantly shorten cycle times and increase output.
- Mechanical Strength and Durability: Adsorbents must withstand multiple pressure fluctuations and avoid breaking or wear during long-term use. In large-scale production, mechanical strength and stability are key factors in evaluating the adsorbent’s performance.
- Chemical Stability: In some special environments, adsorbents need to have strong resistance to contamination and poisoning. Harmful components in the gas, such as sulfur, carbon dioxide, and moisture, may negatively affect the adsorbent, so selecting adsorbents with enhanced chemical stability can extend their lifespan.
- Regeneration Capability: The ability to regenerate adsorbents directly affects their cost-effectiveness and the long-term operating costs of the system. Efficient regeneration can save energy and reduce the frequency of adsorbent replacement, thus lowering maintenance costs.
Adsorbent Performance Evaluation and Selection Criteria
The performance of adsorbents is typically evaluated through static isothermal adsorption experiments and dynamic breakthrough tests. Static experiments help assess the adsorption capacity at different pressures, while dynamic experiments more closely simulate real working conditions, providing more accurate performance data.
- Adsorption Isotherms: Adsorption isotherms reflect the adsorbent’s capacity to adsorb gas under different pressures. By measuring the adsorption curve, the adsorbent’s ability and equilibrium characteristics can be understood. This curve is essential for selecting adsorbents, as performance differences at low and high-pressure conditions can significantly impact the oxygen generation process.
- Separation Factor: The separation factor refers to the ratio of adsorption amounts for strongly adsorbed components (such as nitrogen) to weakly adsorbed components (such as oxygen). An ideal adsorbent should have a high separation factor, meaning that oxygen can be separated at a high purity. Typically, a separation factor greater than 2 for nitrogen and oxygen ensures effective separation.
- Dynamic Breakthrough Curve: The dynamic breakthrough curve helps assess the adsorbent’s efficiency under real operational conditions. It reflects parameters such as adsorption rate, capacity, and desorption speed, which are critical for system design optimization.
- Mechanical Strength and Durability: The mechanical strength and durability of adsorbents are evaluated through tests such as particle size distribution and compressive strength. Since adsorbents are subject to repeated pressure fluctuations and gas flow, their physical stability directly influences the long-term stability of the system.
Adsorbent Selection Guidelines
In practical applications, adsorbent selection is based on several factors:
- Air Composition: Air is primarily composed of nitrogen and oxygen, so the adsorbent’s ability to selectively adsorb nitrogen is crucial. Molecular sieves (e.g., LiLSX, 5A) are commonly used for oxygen separation because they exhibit strong nitrogen adsorption while minimizing oxygen adsorption, ensuring effective nitrogen removal and oxygen enrichment.
- Operating Conditions: Adsorbent selection also depends on temperature, pressure, and other environmental conditions. Different adsorbents may perform differently under varying temperatures and pressures, so the adsorbent must be chosen according to process requirements.
- Gas Impurity Levels: Air may contain impurities such as moisture, carbon dioxide, or sulfur, which can poison or contaminate the adsorbent. Therefore, adsorbents should be selected based on their resistance to contamination, depending on the impurity levels in the gas.
- Economic Considerations: Different adsorbents have varying performance characteristics and costs. Highly efficient adsorbents tend to be more expensive, but their regeneration capabilities and longer service life can reduce long-term operational costs. Adsorbent selection should balance performance and cost-effectiveness.
Application and Selection of MINNUO’s High-Quality Adsorbents
Through years of technical accumulation and practical experience, we have carefully selected a range of high-quality adsorbents and offer customized solutions based on different customer needs. Below are some commonly used adsorbents and their application scenarios.
Lithium-Based Molecular Sieve (LiLSX)
LiLSX lithium-based molecular sieves are widely used in our oxygen production systems. They exhibit excellent nitrogen adsorption capabilities and are commonly applied in hospital oxygen supply, industrial oxygen production, and high-purity oxygen generation. Benefits include:
- High Selectivity: LiLSX exhibits extremely high selectivity for nitrogen adsorption, effectively separating oxygen and nitrogen, thereby improving oxygen yield and purity.
- Long Service Life: Compared to other molecular sieves, LiLSX has a longer lifespan, significantly reducing maintenance costs and adsorbent replacement frequency.
- Sulfur Resistance: LiLSX has strong sulfur resistance, making it suitable for environments with sulfur-containing gases, thus extending the adsorbent’s service life.
5A Molecular Sieve
5A molecular sieves are cost-effective adsorbents suitable for oxygen generation systems that do not require extremely high purity. They are commonly used for medium-purity oxygen production in applications such as welding and glass manufacturing. Benefits include:
- Efficient Nitrogen Removal: 5A molecular sieves effectively adsorb nitrogen, improving oxygen production efficiency.
- Cost-Effectiveness: Compared to lithium-based molecular sieves, 5A molecular sieves are more affordable, making them suitable for budget-conscious projects.
- Strong Adaptability: 5A molecular sieves can operate stably under various working conditions, making them versatile for different gas processing environments.
Activated Carbon
Activated carbon is commonly used for removing moisture, carbon dioxide, or other harmful gases, and is suitable for low-temperature environments and high-purity gas purification. Benefits include:
- Strong Moisture Adsorption: Activated carbon effectively adsorbs moisture from gases, ensuring the system runs in a dry state.
- Gas Purification: Activated carbon also adsorbs harmful gases like carbon dioxide or volatile organic compounds, providing cleaner gas sources for customers.
- Good Regeneration Capability: Activated carbon can be regenerated by heating or vacuum recovery, making it suitable for equipment that requires long-term operation and periodic maintenance.
Silica Gel
Silica gel adsorbents are primarily used to remove moisture from gases, particularly important in environments with high humidity. Benefits include:
- Efficient Dehumidification: Silica gel effectively adsorbs moisture from gases, ensuring that the system is not affected by humidity.
- Strong Adaptability: Silica gel performs well under various gas conditions, particularly in applications requiring dry gases.
- Good Regeneration Capability: Silica gel can be easily regenerated through heating, making it suitable for applications requiring periodic maintenance.
For specialized oxygen generation projects, we provide customized adsorbent combinations based on customer requirements, including gas composition, pressure, and temperature, ensuring optimal separation efficiency. By precisely matching adsorbents, we help customers achieve efficient system operation while reducing operational costs.
Conclusion
In PSA oxygen generation systems, the choice of adsorbent is at the heart of system design and operation. Whether it’s efficient nitrogen adsorption or resistance to contamination in complex gas environments, selecting the right adsorbent can greatly enhance oxygen purity and production efficiency. MINNUO provides diverse and efficient oxygen generation solutions to ensure each unit performs optimally under various working conditions.
In the future, we will continue to innovate and enhance the performance of PSA oxygen systems through the optimization and application of adsorbents, creating more value for our customers.