In industrial production, nitrogen generators are core equipment that continuously supply high-purity nitrogen to ensure product quality, extend food shelf life, and create anaerobic environments. Their stable operation directly impacts production efficiency and cost control. However, neglecting equipment maintenance often leads to premature aging, performance degradation, increased downtime, and higher production costs. With our rich experience and technical expertise, we can provide effective methods to help extend the lifespan of nitrogen generators, reduce downtime risks, and improve return on investment.
The key to extending the lifespan of nitrogen generators lies in ensuring the stable operation of auxiliary equipment, closely monitoring performance indicators, conducting regular deep maintenance, and addressing faults in a timely manner. Regularly checking and maintaining auxiliary equipment such as cooling fans and dryers ensures their proper function; through data-driven preventive maintenance, key performance indicators of nitrogen generators can be continuously monitored; regularly replacing filters and activated carbon in the filtration system prevents pollutants from damaging the equipment; when adsorbent faults occur, immediate shutdown and replacement with specialized adsorbents should be performed to avoid secondary damage.
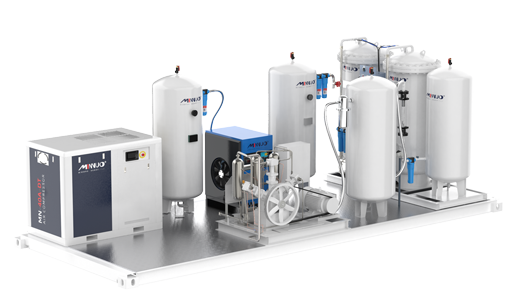
1. Ensuring Stable Operation of Auxiliary Equipment: Safeguarding Efficiency from the Source
A nitrogen generation system operates like a tightly coordinated orchestra, where the overall performance is not determined solely by the main nitrogen generator but also by the auxiliary equipment, which plays an irreplaceable role. Cooling fans, dryers, and other supporting devices, like key instruments in the orchestra, contribute to a stable and efficient performance. If the air-drying equipment malfunctions, moisture or impurities can infiltrate the system like dissonant notes, speeding up the aging of the molecular sieve, a critical component, and severely affecting the overall performance and lifespan of the nitrogen generator.
1.1 Regular Inspection of Cooling Fans and Dryers
Cooling fans and dryers are essential equipment responsible for heat dissipation and dehumidification within the nitrogen generation system. Users should strictly follow the equipment manual and conduct comprehensive checks of the cooling fans and dryers, ensuring their heat dissipation and dehumidification functions are operating correctly. During inspections, it is important to check for any visible damage and to calibrate parameters to keep them in optimal operating condition. For example, check if the cooling fan’s heat dissipation fins are overly dusty, affecting heat dissipation efficiency, and whether the desiccant in the dryer is saturated and needs replacing. Only by doing so can the auxiliary equipment provide a stable and suitable operating environment for the nitrogen generator.
1.2 Monitoring Drying Equipment’s Operating Status
The operation of drying equipment is crucial for the nitrogen generator’s performance. Users should closely monitor key indicators such as exhaust dew point and energy consumption. If the exhaust dew point rises or energy consumption becomes abnormal, it is akin to hearing an alarm from the equipment, signaling the need for a comprehensive inspection and prompt repairs. For instance, a higher dew point may be caused by ineffective desiccants or damaged seals; abnormal energy consumption may indicate internal blockages or electrical faults. Timely troubleshooting and resolution of these issues can effectively prevent damage to the nitrogen generator caused by drying equipment failure.
1.3 Operator Training on Standard Procedures
The professional skills and adherence to operating procedures of operators directly influence the stability of the nitrogen generation system. Regular training should be conducted to familiarize operators with the working principles, operational procedures, and precautions of the nitrogen generation system, enabling them to master proper operational techniques. For example, when starting up and shutting down the equipment, operators must follow the prescribed sequence to avoid chain reactions caused by mistakes, such as starting the nitrogen generator without first activating the cooling fan and dryer, which may cause abnormal internal pressure and damage the equipment. Additionally, operators should have troubleshooting and emergency handling skills to quickly address abnormal situations, minimizing losses.
MINNUO particularly reminds users that faults in auxiliary equipment act like “invisible killers” hidden within the nitrogen generation system. They are hard to detect but can severely threaten the nitrogen generator’s lifespan. To promptly detect and resolve potential issues in auxiliary equipment, it is recommended that users conduct systematic interlinked inspections of the nitrogen generation system every quarter to ensure stable system operation.
2. Strict Monitoring of Performance Indicators: Data-Driven Preventive Maintenance
The purity and output of a nitrogen generator are the core indicators of its performance, similar to a car’s speed and fuel consumption, directly reflecting the operational state of the equipment. To ensure the nitrogen generator always operates at its best, it is necessary to continuously monitor these indicators using professional instruments, implementing data-driven preventive maintenance.
2.1 Calibration of Oxygen Analyzers
Oxygen analyzers are essential tools for monitoring the purity of the nitrogen generator, and their accuracy directly affects the output quality. Monthly calibration of the oxygen analyzer with standard gases is crucial for maintaining accuracy. If the electrode sensitivity decreases during calibration, such as slow response or fluctuating readings, similar to a car’s malfunctioning dashboard, the electrodes need to be replaced to ensure the analyzer can accurately monitor the nitrogen generator’s purity.
2.2 Record Key Data
Establishing an operational log to record key data of the nitrogen generator, such as purity, output, pressure, and temperature, is the foundation for preventive maintenance. By comparing historical data, users can quickly identify trends in performance changes. For example, if the purity of the nitrogen generator drops below 99.5% or output decreases by 10%, it is like a warning light on the equipment, signaling the need for deep maintenance, a comprehensive inspection, and repair to identify and address performance issues.
2.3 Pressure and Temperature Monitoring
Pressure and temperature are critical parameters in the operation of nitrogen generators. Abnormal fluctuations in pressure and temperature often indicate equipment faults. For instance, abnormal pressure fluctuations may be caused by valve failures, such as poor sealing or damage to the valve core, resulting in unstable system pressure; excessive temperature can accelerate the failure of adsorbents, shortening their lifespan. Users should closely monitor the pressure and temperature of the nitrogen generator, install pressure and temperature monitoring devices, collect data in real time, and set alarm thresholds to alert operators if parameters exceed normal ranges, prompting timely action.
One client once faced a 20% error in their oxygen analyzer’s measurements due to failure to replace the oxygen electrodes, resulting in nitrogen purity falling far below standard. Running with inaccurate monitoring led to the molecular sieve failing three months earlier than expected, incurring increased repair costs and production losses due to downtime.
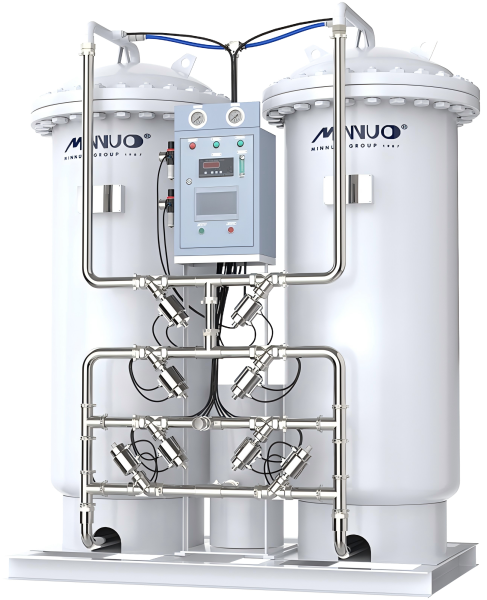
3. Deep Maintenance of Filtration System: Blocking Pollutant Sources
The air contains large amounts of particles, oil mist, and moisture, which act like tiny enemies that can severely damage the internal structure of the nitrogen generator, blocking channels and affecting gas flow and separation efficiency. Regularly replacing filter elements is one of the most cost-effective and efficient measures to protect the nitrogen generator and extend its lifespan.
3.1 Pipeline Filter Elements
Pipeline filter elements are the first line of defense in the nitrogen generator’s filtration system, designed to filter particles in the air. The replacement cycle varies depending on the operating environment. In normal conditions, the filter should be replaced every 2,000 to 4,000 hours of operation. In dusty environments, the replacement cycle should be shortened to 1,500 hours. When removing the filter, carefully inspect its color and condition. If the filter has turned black or clumped, it indicates that it has absorbed a large amount of contaminants and should be replaced immediately.
3.2 Activated Carbon Filters
Activated carbon filters are primarily used to adsorb oil mist and odors in the air. As their adsorption capacity decreases over time, the activated carbon must be completely replaced every 7,000 hours to ensure the filter functions properly. If the activated carbon is not replaced when saturated, it will not effectively adsorb pollutants and may even release previously absorbed contaminants, causing secondary pollution and damaging the nitrogen generator.
3.3 Gas Tank Drainage
Gas tanks store nitrogen, and moisture in the air can condense at the bottom of the tank. Draining the condensate daily from the gas tank is a necessary measure to prevent liquid accumulation from corroding the tank and returning to the system. If condensate builds up in the gas tank for extended periods, it can cause corrosion of the tank, reduce its lifespan, and potentially affect the nitrogen generation system’s performance.
MINNUO’s statistics show that using original factory filters can improve filtration efficiency by 30%, effectively reducing the damage caused by pollutants to the nitrogen generator and extending the molecular sieve’s lifespan by over 20%. Therefore, it is recommended that users prioritize using original factory filters to ensure optimal filtration system performance and prolong the nitrogen generator’s lifespan.
4. Emergency Handling of Adsorbent Faults: Preventing Secondary Damage
If black powder appears at the nitrogen generator’s outlet, it is a critical warning that indicates the molecular sieve or activated alumina adsorbent has powdered. Immediate emergency action must be taken to prevent further damage.
4.1 Immediate Shutdown
If black powder is detected at the nitrogen generator’s outlet, the equipment should be shut down immediately to prevent the powder from entering downstream devices such as gas tanks and pipelines. Powder entering downstream equipment can cause severe blockage and wear, increasing repair costs.
4.2 Full Inspection of Adsorbent Layers
After shutting down, depressurize and open the adsorption tower to inspect the adsorbent layer for damage. Carefully check for caking, powdering, and the evenness and compactness of the adsorbent layer. Through this inspection, identify the causes of powdering, such as uneven airflow distribution or internal structural damage in the adsorption tower.
4.3 Replace with Specialized Adsorbents
When replacing adsorbents, use MINNUO’s high-density molecular sieves to ensure the quality and performance of the adsorbents. During the filling process, ensure the adsorbent is packed tightly to avoid short-circuiting of airflow. For instance, use layer-by-layer filling and compression to ensure uniformity and compactness.
Delaying treatment of adsorbent faults may lead to valve blockages, purity drops, and even require replacement of the entire adsorption tower, resulting in significant economic losses.
5. Conclusion
To ensure the lifespan of nitrogen generators, MINNUO recommends developing an annual maintenance plan with clear tasks, timelines, and responsibilities, using original factory parts for maintenance to ensure compatibility, reliability, and optimal operation for sustainable industrial production.