PSA (Pressure Swing Adsorption) nitrogen generators are commonly used industrial gas separation equipment, widely applied in industries such as metallurgy, chemicals, electronics, food, and healthcare. However, to maintain high operational efficiency and extend their service life, regular maintenance is essential. This article will comprehensively discuss the maintenance key points of the PSA nitrogen generator, including maintenance of key components, troubleshooting common faults, and recommended maintenance cycles and techniques, ensuring your equipment remains in optimal working condition.
Maintaining a PSA nitrogen generator requires periodic inspection of key components such as the air compressor, molecular sieves, adsorption towers, valve systems, and control systems, to ensure efficient operation and prolong its lifespan. Monthly checks should be conducted on air filters, lubricants, and pipe systems. Every three months, molecular sieves and the control system should be inspected, while every six months, the adsorption towers should be cleaned and the cooling system checked. Molecular sieves should be replaced annually. Using high-quality lubricants and filters, regularly cleaning the equipment, and replacing worn parts in a timely manner will enhance efficiency and reduce failures, ensuring stable operation of the PSA nitrogen generator.
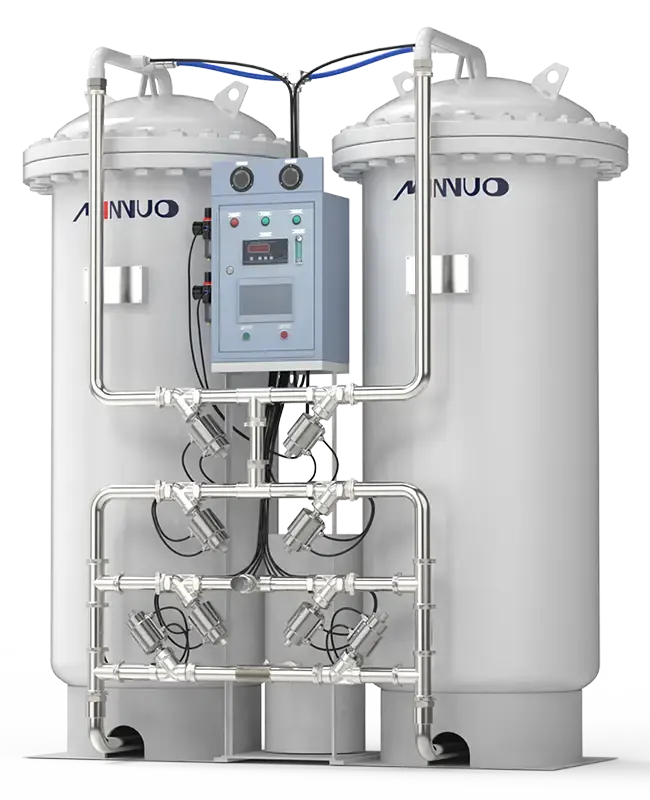
1. Basic Structure and Working Principle of PSA Nitrogen Generators
Before discussing how to maintain PSA nitrogen generators, let’s first understand their basic structure and working principle. The working principle of PSA nitrogen generators is based on pressure swing adsorption technology. Air enters the adsorption tower through a compressor, and oxygen and other gases are adsorbed by molecular sieves, while the remaining nitrogen is output as the product gas. PSA nitrogen generators generally consist of the following main components:
- Air Compressor: Responsible for compressing air to the required working pressure.
- Adsorption Tower: Contains molecular sieves that separate oxygen from nitrogen by adsorption.
- Molecular Sieves: Adsorb oxygen from the air, releasing nitrogen.
- Valve System: Controls the switching of different gas flows to ensure smooth nitrogen separation.
- Control System: Monitors and adjusts the operational parameters of the equipment, including temperature, pressure, and flow.
- Pipeline System: Connects all components, transferring air and nitrogen.
After understanding the basic structure of the equipment, we will now delve into the maintenance of these key components.
2. Key Component Maintenance of PSA Nitrogen Generators
2.1 Air Compressor Maintenance
As the “heart” of a PSA nitrogen generator, the air compressor is responsible for compressing air to the required pressure. To ensure efficient operation, it is essential to perform regular maintenance and checks. MINNUO recommends the following checks for the compressor:
- Lubricant Check and Replacement: The lubricant for the air compressor is crucial for its normal operation. Lubricant not only reduces friction between mechanical parts but also effectively cleans and cools the compressor. It is recommended to replace the lubricant every 500 to 1000 hours. The compressor accessories and lubricants provided by MINNUO ensure optimal performance.
- Air Filter Cleaning: The primary role of the air filter is to remove dust, moisture, and impurities from the air, preventing them from entering the compressor system. It is recommended to check and clean the filter every 6 months and replace the filter elements if necessary. Using MINNUO’s high-quality filters will extend the compressor’s service life.
- Compressor Pressure Check: The output pressure of the air compressor should be within the recommended range of the equipment. By installing a pressure gauge, the operating pressure of the compressor should be regularly checked to ensure it is normal.
- Cooling System Maintenance: The compressor generates a lot of heat during operation, and MINNUO’s advanced cooling system design ensures the equipment operates stably under different environmental conditions. Check the coolant level and replace the coolant regularly to prevent the compressor from overheating.
2.2 Molecular Sieves and Adsorption Tower Maintenance
Molecular sieves are one of the most important components in a PSA nitrogen generator, responsible for separating nitrogen from the air. Over time, the adsorption capacity of molecular sieves decreases, making regular checks and replacements essential.
- Molecular Sieve Inspection and Replacement: The adsorption capacity of molecular sieves directly affects the nitrogen output and purity. MINNUO recommends inspecting the molecular sieves annually, and if clumping, damage, or reduced adsorption capacity is detected, they should be replaced promptly. Depending on the usage environment, the lifespan of molecular sieves is generally 2 to 5 years.
- Adsorption Tower Cleaning: Dust, impurities, and moisture accumulate inside the adsorption tower, which affects the adsorption efficiency of the molecular sieves. The adsorption tower should be cleaned regularly, with a thorough cleaning recommended every two years to ensure normal operation.
- Adsorption Tower Sealing Check: The sealing of the adsorption tower is critical; poor sealing can cause air leakage, which affects nitrogen yield and purity. MINNUO recommends regularly checking the seals, joints, and valves of the adsorption tower to ensure there are no leaks.
2.3 Valve and Pipeline System Maintenance
The valve system in a PSA nitrogen generator controls the switching of gas flows, ensuring the smooth separation process. Maintenance of the valve system primarily includes the following:
- Valve Lubrication: The sealing and flexibility of the valves are crucial for the normal operation of the equipment. Regularly check if the valves operate smoothly and apply appropriate lubrication to prevent the valves from becoming stuck.
- Pipeline Inspection: The pipeline system needs to remain clean and leak-free. Regularly check the seals at pipeline connections to prevent gas leakage. Also, inspect the pipes for water, oil, or impurities inside, and clean the pipelines regularly to prevent contamination.
- Pipeline Insulation: In cold environments, gas inside the pipes may freeze, affecting the efficiency of the equipment. External insulation materials should be used to wrap the pipes to ensure unobstructed airflow.
2.4 Control System Maintenance
The control system of a PSA nitrogen generator is the “brain” of the equipment, responsible for monitoring and adjusting the operational parameters. To ensure the precision and stability of the control system, MINNUO recommends regular maintenance:
- Sensor Calibration: PSA nitrogen generators contain sensors for temperature, pressure, flow, etc. Regular checks and calibrations of these sensors will ensure the accuracy of the equipment’s operation. MINNUO’s intelligent control system supports remote monitoring and automatic calibration, helping you track the device’s status in real-time.
- Electrical Contact Point Inspection: The electrical contact points and cable connections in the control system must remain clean and secure. Check for corrosion, looseness, or wear at the contact points, and clean or replace them as needed.
- Software Updates: Regularly check the software version of the control system to ensure it is up to date, fixing any known bugs and improving the operating efficiency of the equipment.
3. Common Faults and Solutions for PSA Nitrogen Generators
Although PSA nitrogen generators are generally stable during operation, various factors can lead to common faults. Below are analyses of some typical faults and solutions:
Fault Phenomenon | Possible Causes | Solution |
Insufficient Nitrogen Yield | Molecular sieve failure, pipeline leakage, compressor malfunction | Check if molecular sieves need replacing; inspect for pipeline leaks; repair the compressor. |
Low Nitrogen Purity | Adsorption tower seal failure, molecular sieve contamination, equipment aging | Check the sealing of the adsorption tower; clean the molecular sieves; replace aging components. |
Equipment Overheating or Freezing | Temperature control system failure, large temperature fluctuations | Calibrate the temperature control system; install auxiliary heating/cooling devices. |
Abnormal Equipment Vibration | Compressor malfunction, loose pipelines, valve failure | Repair the compressor; tighten pipeline connections; check valve status. |
4. Maintenance Cycle and Tips for PSA Nitrogen Generators
4.1 Maintenance Cycle
The maintenance cycle for PSA nitrogen generators should be determined based on the equipment’s usage frequency, environmental conditions, and workload. The following periodic maintenance is recommended:
- Monthly: Inspect air filters, compressor lubricants, valves, and pipeline systems.
- Every 3 Months: Check molecular sieve adsorption capacity, control systems, sensors, and electrical contact points.
- Every 6 Months: Clean the adsorption tower, check the cooling system, and inspect pipeline insulation.
- Annually: Replace molecular sieves and inspect the overall operational status of the equipment.
4.2 Maintenance Tips
- Use high-quality lubricants and filters to reduce wear and contamination, improving operational efficiency.
- Regularly clean the equipment, especially in environments with a lot of dust and impurities.
- Replace worn parts (such as molecular sieves, filter elements) in a timely manner to maintain good equipment performance.
- Record each maintenance and inspection to help detect potential problems and take preventive measures in advance.
5. Frequently Asked Questions (FAQ)
Q1: How often should the molecular sieves of a PSA nitrogen generator be replaced?A1: The lifespan of molecular sieves is typically 2 to 5 years, depending on usage frequency and environmental conditions. It is recommended to inspect them annually and replace them when adsorption capacity decreases.
Q2: How can I extend the service life of a PSA nitrogen generator?A2: Regular maintenance and inspections, especially of the compressor, molecular sieves, valves, and pipeline systems, can effectively extend the equipment’s service life.
Q3: What should I do if the equipment malfunctions?A3: Start by checking common fault causes (such as molecular sieve failure or pipeline leakage). If the issue cannot be resolved independently, contact professional maintenance personnel or MINNUO’s technical support team.
6. Conclusion
Through regular checks and maintenance, the stability of PSA nitrogen generators can be ensured, reducing unexpected downtimes and enhancing equipment longevity. MINNUO’s professional maintenance services and spare parts can further ensure your equipment’s optimal performance. If you are interested in purchasing high-quality PSA nitrogen generators or need more maintenance advice, feel free to contact us. We are committed to providing top-notch solutions and services to meet your industrial gas generation needs.