The purity of nitrogen and oxygen directly affects industrial production costs and efficiency. Variations in the understanding of gas purity and quality across different global regions often lead to unnecessary cost increases. By deeply analyzing the impact of nitrogen and oxygen purity on industrial production costs, enterprises can better optimize gas supply strategies, reduce resource waste, and enhance overall production efficiency.
The purity of nitrogen and oxygen directly impacts industrial production costs. With purchased gases, the fixed purity often requires companies to pay additional premiums for high-purity gases, leading to resource waste and higher costs. For small-scale demands, purchasing may be more cost-effective, but for medium to large enterprises (such as in the chemical or electronics industries), investing in on-site gas production equipment results in lower long-term costs. On-site gas production allows for purity adjustments, optimizing equipment investment, reducing energy consumption, and lowering maintenance expenses. Using lower purity gases can further reduce electricity consumption and carbon emissions, thus further cutting costs.
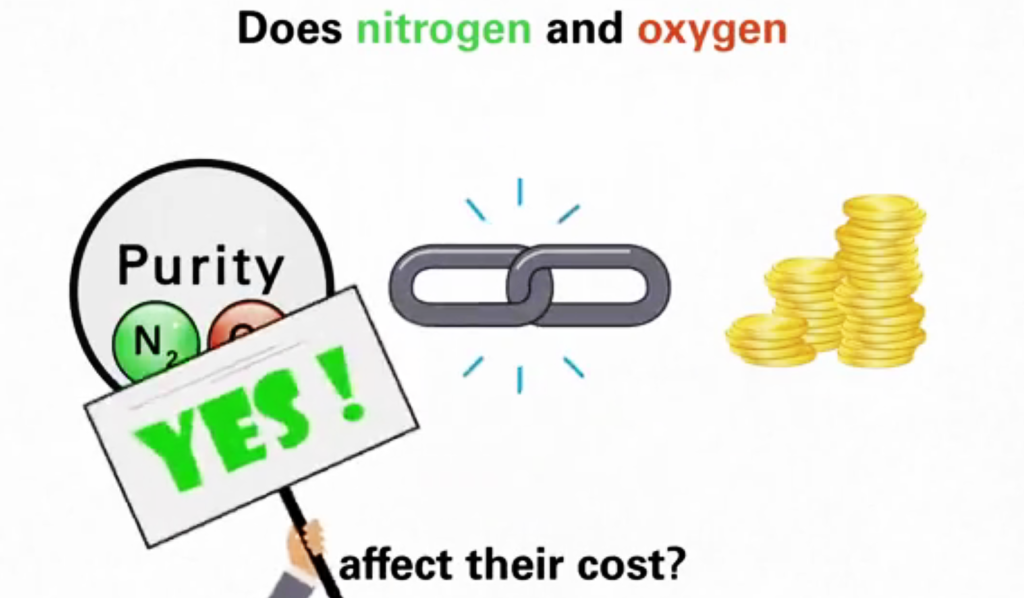
1. Background
In the global industrialization process, nitrogen and oxygen, as fundamental industrial gases, have purity levels that are core factors affecting industrial process efficiency and costs. However, in the international industrial gas market, practitioners in different countries and regions exhibit varying degrees of confusion between the concepts of “purity” and “quality.” According to international standards, purity refers to the volumetric fraction of the target gas in a mixture. For example, 99.9% nitrogen means that in every 100 volume units, 99.9 units are nitrogen, while the remaining 0.1 units are other gases. Quality, on the other hand, refers to the types and concentrations of non-target pollutants in the gas, such as moisture, hydrocarbons, and particulates. The control standards for these pollutants also differ internationally based on industries and application scenarios.
Currently, global industrial gas supply primarily relies on two approaches: external procurement and on-site generation. In developed regions such as Europe, the U.S., Japan, and some emerging economies, the fixed high-purity supply model for purchased gases offers logistical and storage conveniences but also leads to widespread cost redundancies. For example, similar issues exist in Southeast Asia’s electronics manufacturing clusters and Europe’s automotive component production bases.
2. Definitions of Gas Purity and Quality
2.1 Purity
According to the International Union of Pure and Applied Chemistry (IUPAC), purity is defined as the volumetric fraction of the target gas in a mixture. In practical industrial production, although industry standards vary across countries and regions, they generally adhere to this definition. For instance, in the semiconductor manufacturing sector, nitrogen purity must exceed 99.999% internationally to ensure no impurities are introduced during chip fabrication. In contrast, in general chemical production in some developing countries, nitrogen with 90%–95% purity suffices for certain processes.
2.2 Quality
Gas quality primarily concerns the types and concentrations of non-target pollutants. International standards clearly define gas quality requirements for different industries. For example, in the food packaging industry, the Codex Alimentarius Commission (CAC) imposes strict limits on moisture and hydrocarbon content in gases to ensure food safety. In aerospace, the International Air Transport Association (IATA) sets stringent standards for oxygen and nitrogen quality in aviation fuel production to prevent gas quality issues from compromising flight safety.
It is important to note that purity and quality are not directly correlated. High-purity gases may fail to meet quality standards due to excess contaminants, while low-purity gases may still meet quality requirements in specific applications. For example, the International Organization for Standardization (ISO) in ISO 13473-1 specifies the laser scattering method for detecting particulate concentration in industrial gases, requiring that particles with a diameter greater than 0.3μm be less than 1000 particles/m³. The ASTM D3652 standard uses gas chromatography-mass spectrometry to measure oil content, with a limit of ≤0.1mg/m³ and a dew point for moisture of ≤-40°C. Therefore, global companies must establish gas purity and quality standards based on their respective industry’s international standards and the specific requirements of their processes.
3. Cost Structure Analysis of Purchased Gases
3.1 Investment Costs
- Logistics Facilities: Globally, different countries and regions have varying safety regulations for purchased gas cylinder storage and liquefied storage tanks, but all have strict standards. In Europe, cylinder storage must comply with EU safety directives, and liquefied storage tanks must be equipped with advanced leakage monitoring and safety protection systems. In North America, regulations from the National Fire Protection Association (NFPA) and the Canadian Standards Association (CSA) must be followed, including the construction of concrete bases and enclosures. The construction, maintenance, and upgrading of these logistics facilities, as well as gas losses during transportation (e.g., residual gas in cylinders) and safety incident risks, require significant financial investment from companies. Additionally, cross-border transportation must account for tariffs, insurance, and currency fluctuations.
- Leasing Fees: In the international gas leasing market, fees for cylinders or tanks are influenced by factors such as raw material price fluctuations, exchange rate variations, and regional supply-demand dynamics. For instance, leasing costs are higher in resource-scarce regions but lower in areas with concentrated gas production. Accumulated long-term leasing fees significantly impact corporate finances.
3.2 Unit Gas Pricing
- High-Purity Gas Premiums: Globally, cryogenic distillation is a mainstream method for producing high-purity gases (typically ≥99.995%). However, most industrial applications in different regions require far lower purity levels. For example, India’s textile dyeing industry only needs 99% pure nitrogen for process protection but must purchase higher-purity gas due to market constraints, incurring unnecessary premiums. This mismatch-induced cost escalation is common in international gas markets.
3.3 Operational Costs
- Transportation Costs: International gas transportation involves cross-border logistics, with costs covering fuel consumption, vehicle maintenance, driver wages, and impacts from oil price fluctuations, transportation regulations, and tariff policies. For example, along the “Belt and Road” countries, transportation costs vary widely due to geography, infrastructure, and customs policies.
- Environmental Taxes: With growing global attention to climate change, more regions are implementing environmental taxes. The EU regulates industrial gas emissions via its Emissions Trading System (EU ETS), requiring companies to purchase carbon allowances. Australia once levied a carbon tax on high-emission gas users. These policies further increase operational costs for enterprises purchasing gases.
3.4 Key Issues
The inability to adjust gas purity is a global challenge. In Africa’s food processing and Latin America’s beverage packaging industries, companies often procure higher-purity gases than needed, leading to resource waste and cost escalation. This issue persists not only in developing nations but also in specific sectors of developed countries.
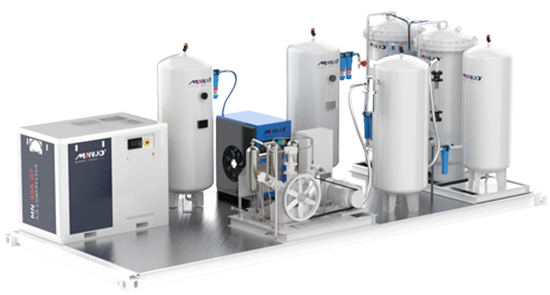
4. Economic Optimization Mechanisms for On-Site Gas Generation
4.1 Technical Pathways
- Pressure Swing Adsorption (PSA): PSA technology is widely applied globally. It works by utilizing the selective adsorption characteristics of molecular sieves for different gas molecules, achieving gas separation by periodically changing pressure. In industries like electronics in South Korea and high-end manufacturing in Germany, PSA technology is used to produce high-purity nitrogen (up to 99.999%) and oxygen (up to 95%), meeting the strict purity requirements of these sectors.
- Membrane Separation Technology: Membrane separation technology, based on the selective permeation principle of semi-permeable membranes, has unique advantages in producing medium and low purity gases internationally. It is widely adopted in industries such as rubber processing in Southeast Asia and petrochemical industries in the Middle East. The nitrogen produced typically has a purity range of 95%–99.5%, with simple equipment and low costs, saving companies significant amounts of money.
- Cryogenic Air Separation Technology: This method uses low-temperature distillation (-196°C) to separate air, producing nitrogen and oxygen with purity ≥99.999%, suitable for large-scale continuous production (≥5000Nm³/h). Although the equipment investment is 3-5 times higher than PSA (with a 1000Nm³/h investment around $2 million), the energy consumption per unit is 30%-40% lower than PSA. This technology is widely adopted in large-scale operations such as LNG plants in Qatar and steel enterprises in China, due to its significant economies of scale.
In summary, PSA is suited for small to medium-scale high-purity applications, membrane separation is ideal for low-purity, large-flow production, and cryogenic air separation is best for large-scale operations.
4.2 Cost Components
- Investment Costs: On-site gas generation equipment costs vary globally. In developed countries like the U.S. and Japan, higher labor and manufacturing costs elevate expenses for generators, compressors, and pretreatment systems. In developing nations like China and India, lower production costs reduce equipment expenses. Nonetheless, investment costs remain a critical factor.
- Operational Costs: Globally, electricity consumption accounts for 60%–70% of on-site generation operational costs. Regional electricity price differences are significant: Nordic countries with abundant hydropower have lower rates, while energy-scarce regions face higher prices. Maintenance and carbon emission costs also vary based on local environmental policies and market rates.
4.3 Purity’s Leverage Effect on Costs
- Equipment Downsizing: Lower purity requirements allow global enterprises to use smaller, lower-power equipment. For example, Brazil’s agricultural preservation industry reduced nitrogen purity needs, adopting smaller compressors that cut procurement costs by ~30% and improved space efficiency.
- Energy Consumption Reduction: International studies show that a 1% purity reduction decreases compressed air consumption by 2%–5%. In Russia’s metallurgical sector, optimizing gas purity saves millions of rubles annually in electricity costs.
- Lower Maintenance Costs: Globally, low-load equipment operation extends lifespan and reduces failure rates. In South Africa’s mining industry, adopting low-purity gas solutions decreased maintenance frequency by ~25%, boosting productivity.
5. Case Study: Cost Impact of Purity Requirement Differences
Two global scenarios—wave soldering and coffee packaging—are analyzed. In wave soldering (e.g., a Californian electronics manufacturer), 99.999% pure nitrogen is required for high welding quality. In coffee packaging (e.g., an Italian processor), 99.9% purity suffices. Assuming both use 50 Nm³/h flow rates, a 7-year total cost analysis (in USD 10,000) yields:
Application | Investment | Electricity | Maintenance | Total Cost |
Wave Soldering (99.999%) | 30 | 50 | 20 | 100 |
Coffee Packaging (99.9%) | 18 | 30 | 15 | 63 |
This shows a 37% global cost reduction by matching purity requirements. Lower purity enables smaller equipment, reduced investment, and lower energy and maintenance costs.
6. Discussion
6.1 Technology Selection
Globally, gas application technologies vary by industry and region. In advanced manufacturing and R&D (e.g., Europe and the U.S.), PSA dominates for ultra-high-purity gases. In Asia and Africa’s labor-intensive sectors, membrane separation’s cost efficiency prevails. For instance, Vietnam’s textiles and Kenya’s agro-processing industries use membrane separation to balance cost and demand.
6.2 Environmental Benefits
Lowering gas purity offers global environmental benefits. Reducing compressor power cuts energy use and emissions, aligning with climate goals. In the EU, optimizing purity helps meet carbon policies and qualify for subsidies. In China, companies support the “Dual Carbon” goals by improving gas supply methods.
6.3 Policy Drivers
Global policies significantly influence gas supply modes and purity optimization. Beyond carbon taxes and trading, nations incentivize eco-friendly technologies. Singapore offers tax breaks for advanced gas systems; India subsidizes clean energy-based gas production. Such policies encourage purity optimization and cost control.
- The Non-linear Impact of Gas Purity on Global Industrial Costs and Optimization Strategies
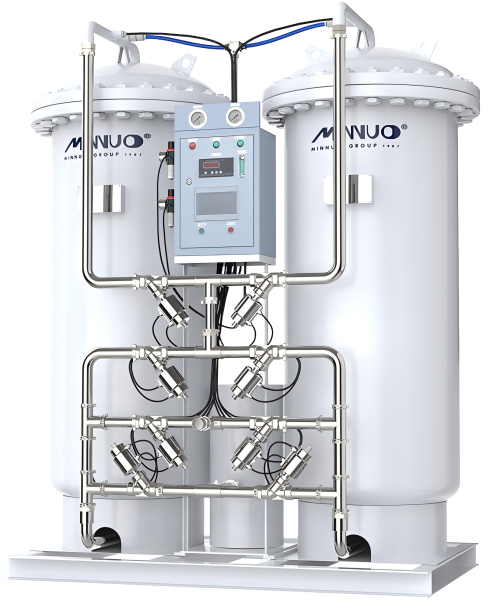
7.1 Non-linear Relationship Between Cost and Purity
- High-end Manufacturing Scenarios: The semiconductor industry requires nitrogen with a purity of 99.999% or higher. Although the equipment investment is high (e.g., in the wave soldering case, the total cost over 7 years is $1 million), it can prevent impurities from causing chip defects, reducing the defect rate by 1% and saving millions of dollars.
- Basic Industrial Scenarios: For food packaging, 99.9% nitrogen can lower total costs by 37% through reduced energy consumption (with a 2%-5% reduction in electricity consumption for every 1% reduction in purity) and smaller equipment sizes (reducing investment costs by 40%). For example, in the coffee packaging case, the total cost over 7 years is $630,000.
7.2 Hidden Cost Chain of Purchased Gases
- Premiums and Logistics: Due to market supply restrictions, India’s textile industry is forced to purchase 99.99% nitrogen, paying an additional premium (purity premiums reach 20%-30%), compounded by cross-border transport costs (which account for over 30% of operational costs) and EU carbon trading costs (increasing by 15%-20%).
- Storage Risks: In Europe and North America, gas cylinder storage must meet NFPA/CSA standards, with construction and maintenance costs accounting for 15%-20% of the investment. Additionally, transportation losses reach 2%-5%.
7.3 On-site Gas Production Dynamic Optimization Path
- Technological Adaptability: PSA technology meets the high purity requirements of the electronics industry (purity ≥99.999%), while membrane separation technology is suitable for rubber processing (purity 95%-99.5%), with equipment costs 30%-50% lower than PSA systems.
- Cost Leverage Effect: In Brazil, reducing purity for agricultural product preservation reduces equipment investment by 30% and energy consumption by 20%. In Russia’s metallurgy industry, annual electricity costs are reduced by over 1 million rubles, while maintenance costs in South African mining drop by 25%.
7.4 Key Decision-Making Considerations
- Compliance with Quality Standards: Food packaging must comply with CAC moisture (dew point ≤ -40°C) and hydrocarbon (≤0.1ppm) restrictions. Aerospace follows IATA standards, as non-compliant gas quality can lead to safety accidents or loss of certification.
- Regional Policy Differences: Singapore offers a 15% tax incentive for energy-saving technologies, India provides a 20% subsidy for clean energy gas production, and EU carbon tariffs will force companies to opt for low-purity gas supply solutions.
7.5 Future Trends and Recommendations
- Emerging Sector Drivers: Hydrogen storage and transportation require 99.999% high-purity hydrogen, while quantum computing demands ultra-high-purity helium (purity ≥99.9999%), driving advancements in cryogenic air separation and adsorption technologies.
- Smart Direction: AI algorithms will optimize purity adjustments (e.g., dynamically matching low load demand at night), potentially reducing energy consumption by 10%-15%.
8. Conclusion
When selecting gas supply strategies, companies should comprehensively consider factors such as process requirements, equipment costs, market fluctuations, and environmental policies. MINNUO Gas — a global leader in industrial gas solutions — empowers high-purity gas production through smart technology, providing customized full-process gas supply solutions to help you achieve energy efficiency upgrades and sustainable development goals.