As industrialization progresses, industrial oxygen generators have become vital in many industries, such as chemical, metallurgy, and pharmaceuticals. They are an essential part of daily operations in enterprises. However, like any equipment, industrial oxygen generators, especially their core component—the molecular sieve—require regular maintenance and care to ensure efficient operation over time. This article will delve into the specific maintenance and care methods for molecular sieves in industrial oxygen generators, helping businesses reduce equipment failures, lower repair costs, and extend the service life of their oxygen generators.
A molecular sieve is a critical component of industrial oxygen generators. Its main function is to adsorb nitrogen and other impurities from the air, increasing the oxygen concentration to the required level. Since molecular sieves are sensitive to environmental factors such as humidity and temperature, their performance can degrade over time. To ensure the long-term stability and production efficiency of oxygen generators, maintenance and care of the molecular sieve cover aspects such as cleaning, drying, replacement, and storage. These practices help businesses extend the service life of their oxygen generators and ensure safe production.
What Is a Molecular Sieve in an Industrial Oxygen Generator?
Before exploring the maintenance methods for molecular sieves, it’s important to understand their basic functions and working principles. A molecular sieve is a highly adsorbent material used to separate oxygen from nitrogen in the air. It is usually made from silica-alumina or other metal oxide materials, and its porous structure allows it to effectively separate gas molecules in the air. During operation, the molecular sieve adsorbs nitrogen and water vapor, ultimately separating pure oxygen through adsorption and desorption cycles.
The quality of the molecular sieve directly impacts the performance of the oxygen generator. If the sieve’s performance declines, it can lead to reduced oxygen output and even unstable oxygen concentrations. Therefore, proper maintenance of the molecular sieve is essential for ensuring the oxygen generator operates at peak efficiency.
Why Is Maintenance of Molecular Sieves Important?
Molecular sieves act as the “heart” of industrial oxygen generators, and their maintenance directly affects the equipment’s production efficiency and safety. Over time, molecular sieves may face common issues such as decreased adsorption capacity, clogging, aging, and the accumulation of impurities, all of which can result in lower oxygen output, equipment failure, and disruptions in production. Regularly inspecting, cleaning, drying, and replacing the molecular sieve can extend its service life, improve operational efficiency, prevent production line downtime, and reduce high repair costs.
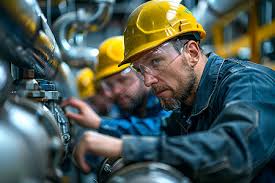
Maintenance Methods for Molecular Sieves in Industrial Oxygen Generators
Regular Inspections
Regular inspections form the foundation of effective molecular sieve maintenance. Enterprises should establish a comprehensive inspection system to ensure any potential issues are identified early during operation. Inspection items include:
- Physical condition of the molecular sieve: Look for visible cracks or damage to the sieve’s surface.
- Performance of the molecular sieve: Test parameters such as oxygen concentration and flow rate to determine if the sieve is functioning properly.
- Temperature changes: Excessive temperatures can reduce adsorption efficiency, so it’s crucial to monitor the working temperature of the molecular sieve.
- Pressure variations: The operating pressure of the oxygen generator should stay within the designed range. Both excessively high and low pressures can affect the sieve’s performance.
Cleaning and Drying
The operating environment of molecular sieves often contains dust, oil, and water vapor, which can accumulate in the sieve’s pores and block its adsorption ability. Regular cleaning and drying are essential maintenance steps.
- Cleaning: Use specialized cleaning tools to remove dust and oil from the sieve’s surface. Avoid using corrosive cleaning agents during this process.
- Drying: The adsorption performance of molecular sieves is closely related to their moisture content. Excess moisture can decrease adsorption efficiency and even cause mold growth. After cleaning, the sieve should be dried. This can be done using hot air or drying equipment, but temperature control is critical to prevent damage to the sieve.
Replacing the Molecular Sieve
Over time, the adsorption capacity of molecular sieves decreases, making replacement necessary. The frequency of replacement depends on several factors, including the frequency of operation, environmental humidity, and temperature. Typically, molecular sieves have a service life of 2 to 5 years. If significant drops in adsorption capacity, clogging, or other issues occur, it’s time to replace the sieve.
When replacing the molecular sieve, follow the manufacturer’s manual to ensure the replacement process does not affect the generator’s normal operation. Select the appropriate molecular sieve based on the model of the oxygen generator and the required gas output.
Storage and Transportation
When molecular sieves are not in use, they should be stored in a dry, well-ventilated area to prevent contamination from moisture or oil. Sealing the sieves in airtight containers can help prevent moisture absorption. During transportation, protect the sieves from excessive vibration, which may damage their structure.
Preventing Contaminant Pollution
To avoid contaminating the molecular sieve during operation, it’s advisable to install appropriate filtration devices at the air intake. This is especially important in environments with high levels of oil or particulate matter in the air. High-efficiency filters can significantly extend the service life of the molecular sieve.
Common Problems and Solutions
Decreased Adsorption Capacity
If the molecular sieve’s adsorption capacity decreases, check for moisture accumulation or contaminant buildup. Cleaning and drying can resolve most of these issues. If the problem persists, it may be necessary to replace the sieve.
Clogging
Clogging is often caused by the accumulation of impurities or too small a pore size in the sieve. This can be addressed by cleaning the sieve professionally or replacing it with a more suitable model.
Excessive Temperature
If the molecular sieve operates at too high a temperature, its performance will deteriorate. In this case, check the cooling system to ensure it is functioning properly and keeping the temperature within the optimal range.
Conclusion
Maintaining and caring for molecular sieves in industrial oxygen generators is essential to ensure long-term, efficient operation of the equipment. Regular inspections, cleaning, drying, timely replacement, and proper storage can significantly extend the service life of the molecular sieve, enhance the generator’s efficiency, reduce maintenance costs, and prevent production disruptions. Whether for routine maintenance or emergency repairs, MINNUO’s after-sales service is reliable. We assist businesses in developing scientific maintenance plans based on actual usage conditions to ensure oxygen generators perform at their best and guarantee safe production.