The Nitrogen generator plays a pivotal role in many industries(such as oil and gas), particularly in providing a reliable and cost-effective source of nitrogen for various applications. The technology behind nitrogen generation includes methods like Pressure Swing Adsorption (PSA), membrane, and cryogenic systems, each offering unique benefits depending on the application. These systems ensure that nitrogen is supplied at the required purity and pressure, making it suitable for different industrial needs, especially in the oil and gas sector.
In the oil and gas industry, nitrogen is crucial for several processes, such as inerting pipelines, conducting pressure testing, and purging systems. Its inert properties make it the ideal choice to prevent explosions and fires, while its dry nature helps ensure the safety and integrity of critical equipment. Nitrogen is preferred over other gases due to its non-reactive characteristics, cost-effectiveness, and ability to provide a stable environment for operations.
This article will explore the key applications of nitrogen in the oil and gas industry, how nitrogen generators work, and the different types of systems available. We will also discuss the benefits of using nitrogen generators for these applications, highlighting their role in enhancing operational safety, efficiency, and sustainability in the oil and gas sector.
I. Applications of Nitrogen in the Oil and Gas Industry
1.1 Inerting of Oil and Gas Pipelines
Importance of Maintaining a Safe and Inert Environment to Prevent Explosions or Fires
In the oil and gas industry, pipeline safety is of paramount importance. Oil and gas pipelines are often exposed to volatile and flammable gases, which can cause catastrophic explosions or fires if not handled properly. Nitrogen, being an inert gas, is commonly used to displace oxygen and other reactive gases from pipelines, thereby reducing the risk of combustion. This is especially critical during maintenance, decommissioning, or when the pipeline is in standby mode.
How Nitrogen Generators Ensure the Proper Supply of Nitrogen for Inerting Processes
Nitrogen generators provide a reliable and cost-effective solution to generate nitrogen on-site, ensuring a continuous and stable supply for inerting purposes. Unlike traditional gas cylinders, on-site nitrogen generation eliminates the need for bulk nitrogen storage and transport, offering significant cost savings and reducing logistical challenges. The PSA (Pressure Swing Adsorption) technology or membrane technology used in nitrogen generators allows the oil and gas industry to generate nitrogen in real time with high purity, ensuring safety during pipeline operations.
1.2 Well Stimulation and Enhanced Oil Recovery (EOR)
The Use of Nitrogen in Well Stimulation to Improve Production
Well stimulation is a crucial process in the oil and gas industry aimed at increasing the productivity of wells. Nitrogen, used in techniques like hydraulic fracturing (fracking), helps increase the flow of oil and gas by pressurizing the well and breaking open rock formations. As an inert gas, nitrogen prevents undesirable reactions, ensuring the safety of the process while enhancing the overall efficiency of production.
How Nitrogen Is Injected into Wells to Increase Oil Recovery Rates
Enhanced Oil Recovery (EOR) is a process used to extract additional oil from wells after primary and secondary recovery methods have reached their limits. Nitrogen is injected into the well to increase pressure and push the remaining oil to the surface. The use of nitrogen for EOR has proven to be effective, especially in mature oil fields, as it can displace oil and enhance recovery rates significantly. Nitrogen generators ensure that the gas is available on-site, with adjustable purity levels and flow rates to meet specific EOR needs.
1.3 Purging and Pressure Testing
The Role of Nitrogen in Purging Pipelines and Systems
Purging is the process of cleaning or clearing a system, such as pipelines or storage tanks, of unwanted substances like air, oxygen, or contaminants. Nitrogen is ideal for purging due to its inert properties, ensuring that the system is thoroughly flushed without risking any chemical reactions. Nitrogen purging is commonly performed during system startup, shutdown, or maintenance to maintain system integrity and avoid contamination.
How Nitrogen Is Used for Pressure Testing Equipment in the Oil and Gas Industry to Ensure Safety and Integrity
Pressure testing is essential to ensure the safety and integrity of equipment used in oil and gas operations, such as pipelines, pressure vessels, and tanks. Nitrogen’s safety, stability, and controllability make it ideal for pressure testing. The non-reactive nature of nitrogen ensures that it will not cause any hazardous reactions under pressure. Nitrogen generators ensure a continuous, reliable supply of nitrogen for such testing, with the ability to adjust pressure and flow rates as needed.
1.4 Cryogenic Applications
Use of Nitrogen in Cryogenic Systems to Support Low-Temperature Operations in the Oil and Gas Field
Cryogenic systems are used in the oil and gas industry to handle gases and fluids at extremely low temperatures, such as liquefied natural gas (LNG) and other cryogenic fluids. Nitrogen is used in these systems to maintain low temperatures or to assist in the liquefaction process. Nitrogen’s low boiling point allows it to be used as a cooling agent in cryogenic applications, making it ideal for transporting, storing, and processing liquefied gases.
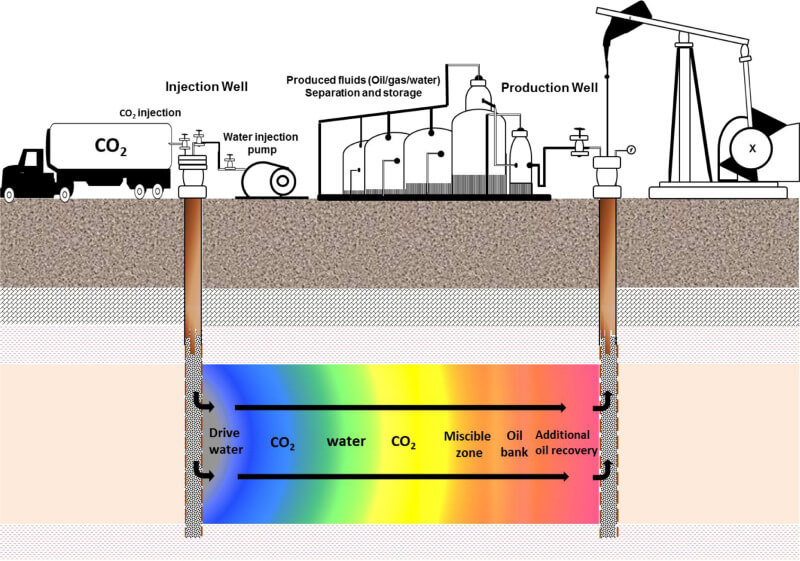
Ⅱ. Types of Nitrogen Generators for the Oil and Gas Industry
2.1 PSA (Pressure Swing Adsorption) Nitrogen Generators
Benefits of PSA nitrogen generators for Oil and Gas Applications
Continuous Supply: PSA systems can operate 24/7, providing a reliable, uninterrupted supply of nitrogen, which is crucial in industries requiring constant nitrogen for processes like pipeline inerting or pressure testing.
Recommended maintenance: Adsorbent replacement every 3-5 years, pressure valvechecks quarterly.”
Energy Efficiency: PSA nitrogen generators are energy-efficient as they work based on pressure cycles rather than the need for external cooling or refrigeration systems, making them cost-effective over time.
Cost-effectiveness: On-site nitrogen generation eliminates bottled nitrogen’s transport and storage costs.
Common Issues with PSA Systems and How They Are Addressed
Fluctuating Purity: One of the main issues with PSA systems is the fluctuation in nitrogen purity. To address this, regular maintenance and optimization of the PSA cycle are essential. Additionally, using high-quality adsorbent materials like CECA or UOP can improve stability.
High Maintenance: PSA systems require periodic maintenance, including checking the adsorbents and ensuring the system pressure is optimized. This can be mitigated by choosing systems that offer automated monitoring and easy-to-replace components.
System Aging: Over time, the adsorbents in the PSA system may degrade, leading to decreased performance. To counteract this, it is crucial to regularly monitor the adsorption capacity and replace the adsorbents as needed.
2.2 Membrane Nitrogen Generators
Benefits of Membrane Nitrogen Generators for Oil and Gas Applications
Smaller Footprint: Membrane generators are compact, requiring less space compared to PSA systems, making them ideal for environments where space is a constraint.
Ease of Use: Membrane systems are simple to operate and require less technical expertise for daily management, making them suitable for smaller operations or remote locations.
Low Maintenance: Since membrane systems don’t require pressure cycles or the replacement of adsorbent materials, they generally have lower maintenance requirements than PSA systems.
When Membrane Generators Are Preferred Over PSA
Smaller-scale applications: For operations requiring lower volumes of nitrogen (e.g., small pipelines or equipment testing), membrane generators provide a more economical option.
Low maintenance priority: When the operational environment demands minimal downtime and maintenance, membrane generators are more beneficial, as they are robust and don’t rely on pressure cycling.
Note: Membrane systems are sensitive to inlet air humidity, pre-filtration is required foroptimal performance in humid environments
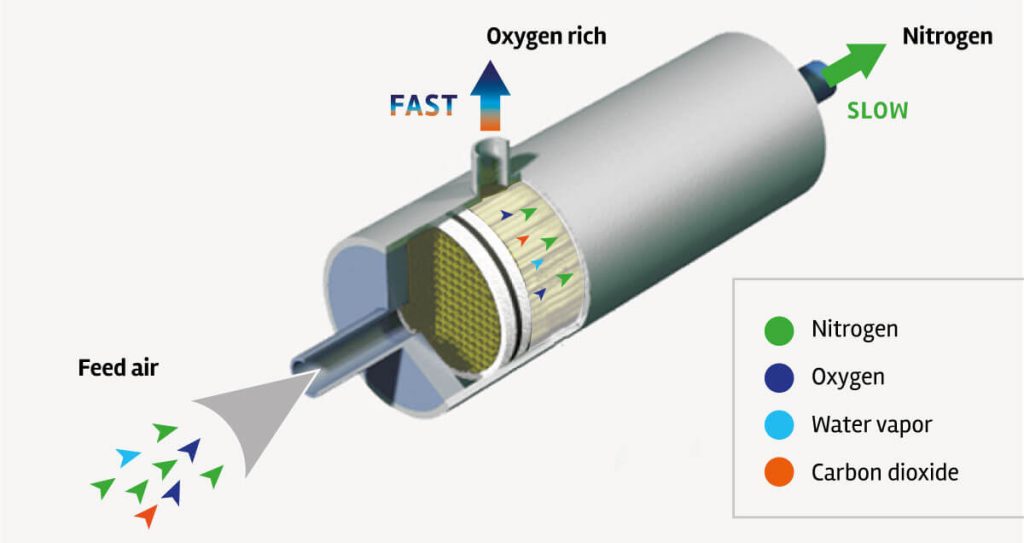
2.3 Cryogenic Nitrogen Generators
Application Areas in the Oil and Gas Industry Where High-Purity Nitrogen Is Required
LNG Processing: In liquefied natural gas (LNG) plants, cryogenic nitrogen generators are used to provide ultra-pure nitrogen for inerting and purging of LNG tanks.
Cryogenic Pipeline Operations: For the transport and storage of gases at extremely low temperatures, cryogenic nitrogen is required to maintain the safety and integrity of the systems.
Oil Refining: Cryogenic nitrogen is used in the refining processes, where high-purity nitrogen is needed to prevent contamination or oxidation of products.
The Pros and Cons of Cryogenic Generators
Pros:
High-purity nitrogen: Cryogenic systems are capable of producing nitrogen with very high purity levels, which is essential for critical applications in the oil and gas industry.
Large-scale capacity: Cryogenic nitrogen generators can supply large volumes of nitrogen, making them ideal for industries with high nitrogen consumption.
Cons:
High energy consumption: Cryogenic systems are energy-intensive due to the cooling process required, leading to higher operational costs compared to PSA or membrane systems.
Complexity and maintenance: Cryogenic systems require regular maintenance and have more complex operations, making them less convenient for smaller-scale applications.
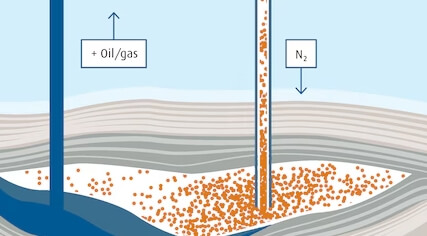
Ⅲ.Advantages of Using Nitrogen Generators in the Oil and Gas Industry
3.1 Cost Efficiency
Using On-Site Nitrogen Generation vs. Purchasing Nitrogen
One of the most significant advantages of using nitrogen generators in the oil and gas industry is the reduction in operational costs. Traditional methods of nitrogen supply often involve purchasing bottled or bulk nitrogen from external suppliers. This incurs substantial costs for transportation, storage, and handling. By adopting nitrogen generators, companies can produce their own nitrogen on-site, eliminating these additional costs.
Long-Term Savings and Impact
While initial setup costs for nitrogen generators may be higher, the long-term savings are significant. Generating nitrogen on-site allows for a steady, reliable supply, with the cost of operation primarily related to the electricity consumed by the generators. This can lead to substantial savings, especially in remote areas or offshore operations where nitrogen supply logistics are challenging and costly. For example, the cost-effectiveness is most notable in offshore oil rigs, where the need for continuous nitrogen supply is crucial, and shipping nitrogen bottles would be inefficient and expensive.
3.2 Enhanced Safety
Ensuring Safe Transportation and Handling of Gases
In the oil and gas industry, safety is paramount, particularly when dealing with hazardous gases like oxygen, methane, and hydrogen. Operators extensively use nitrogen to displace these gases and create an inert environment, particularly in pipeline maintenance, tank inerting, and rig operations.
Reducing Risks
Using nitrogen generators directly at the work site helps reduce the risks associated with transporting and handling large amounts of compressed gases. Nitrogen generators ensure the availability of nitrogen in a controlled manner, reducing the risk of accidents that can occur when dealing with bulk nitrogen storage and transportation.
Inerting and Purging Applications
Inerting oil and gas pipelines with nitrogen prevents the risk of explosions due to the presence of flammable gases. Additionally, nitrogen purges systems and pipelines before maintenance to ensure they are free of hazardous gases, improving safety during operations.
3.3 Control and Flexibility
Better Control of Gas Purity and Supply
Using on-site nitrogen generators allows oil and gas companies to have better control over the purity and flow rate of the nitrogen being produced. Nitrogen generators can be adjusted based on the specific purity requirements of different applications, such as well stimulation, pipeline inerting, and pressure testing.
Customization to Meet Specific Needs
One of the major advantages is the ability to customize the nitrogen production process to meet specific operational needs. The flexibility to adjust purity and flow rates ensures that nitrogen is produced in the right quantities and with the right specifications for each application. This can be particularly beneficial when operations in different areas of the oil and gas sector have varying requirements for nitrogen purity, such as in high-pressure environments where high-purity nitrogen is needed for specific processes.
3.4 Environmental Impact
Reducing Carbon Footprint
Nitrogen generators are an environmentally friendly solution compared to traditional nitrogen supply methods. By using on-site nitrogen production, the need for transport trucks and the associated emissions from the transportation process are eliminated. This contributes to the reduction of the carbon footprint of operations, making nitrogen generation a more sustainable option for the oil and gas industry.
Energy Efficiency
Modern nitrogen generators are designed with energy efficiency in mind. Advances in PSA and membrane technologies have significantly reduced the energy consumption of nitrogen generation, ensuring that the environmental impact is minimized. These systems are particularly valuable in remote oil and gas operations, where energy efficiency is crucial due to high energy costs or limited energy resources.
IV. Key Considerations When Choosing Nitrogen Generators for the Oil and Gas Industry
4.1 Purity and Nitrogen Requirements
How to Ensure Adequate Nitrogen Purity
In the oil and gas industry, nitrogen purity is a critical factor. Specific applications, such as pipeline inerting or well stimulation, require varying levels of purity, typically between 95% and 99%,For pipeline inerting: 299.5% purity, for pressure testing: 95-99%. Ensuring the nitrogen generated meets the necessary purity standards is crucial for the safety and efficiency of operations.
Customized Nitrogen Purity for Different Tasks
Different operations demand different nitrogen purity levels. For example, the nitrogen used for inerting pipelines must meet higher purity standards, while for other applications like pressure testing, lower purity nitrogen might suffice. When selecting a nitrogen generator, it is essential to assess the purity requirements of each task to ensure that the equipment can be appropriately tuned to meet those needs.
4.2 Installation and Footprint
Considerations for Site Location
The location of installation is another key factor in choosing a nitrogen generator. Both offshore and onshore oil and gas operations have unique spatial constraints. Onshore installations may need to factor in the space for infrastructure, such as storage tanks and pipelines, while offshore installations require compact systems due to the limited space on oil rigs.
4.3 System Maintenance and Reliability
Long-Term Operational Requirements
Reliability and ease of maintenance are paramount in selecting a nitrogen generator for oil and gas operations. The generator must operate continuously and efficiently without frequent interruptions. For remote oil fields or offshore platforms, where access to service may be limited, choosing a system with minimal downtime and a design that supports easy maintenance is critical.
Choosing Robust and Low-Maintenance Systems
Oil and gas operations are demanding environments, and the nitrogen generators used in such settings need to be robust. Look for equipment that uses high-quality components and systems that require less maintenance. This reduces the risk of failure and ensures that operations remain uninterrupted, especially in critical processes like pipeline inerting, where continuous nitrogen flow is essential.
4.4 System Integration and Automation
How Automation Improves Operational Efficiency
Automation plays a key role in enhancing the efficiency of nitrogen generators. Automation ensures that nitrogen purity and flow rates are precisely controlled without manual intervention, which is especially beneficial in high-risk or complex operations like offshore drilling or high-pressure systems.
Intelligent Control Systems for Better Performance
Advanced control systems allow for real-time monitoring of nitrogen output and quality. With automated systems, operators can adjust settings remotely, ensuring optimal performance and minimizing human error. Additionally, these systems can offer predictive maintenance capabilities, alerting operators about potential issues before they become problems, which is especially important in remote or hazardous environments.
4.5 System Scalability
Flexibility for Future Expansion
As oil and gas operations evolve, the need for scalable solutions becomes increasingly important. A nitrogen generation system must be able to meet current demands and adapt to future needs. Choosing a scalable system ensures that nitrogen generation capacity can be expanded without major modifications to the infrastructure.
Adapting to Changing Operational Needs
In the oil and gas sector, operational conditions can change rapidly. Whether the demand for nitrogen increases or decreases based on exploration and production activities, having a flexible nitrogen generation system allows companies to easily adjust to these shifts. Scalable systems also support increased flow rates or purity adjustments when necessary, ensuring that the equipment can grow with the operation.
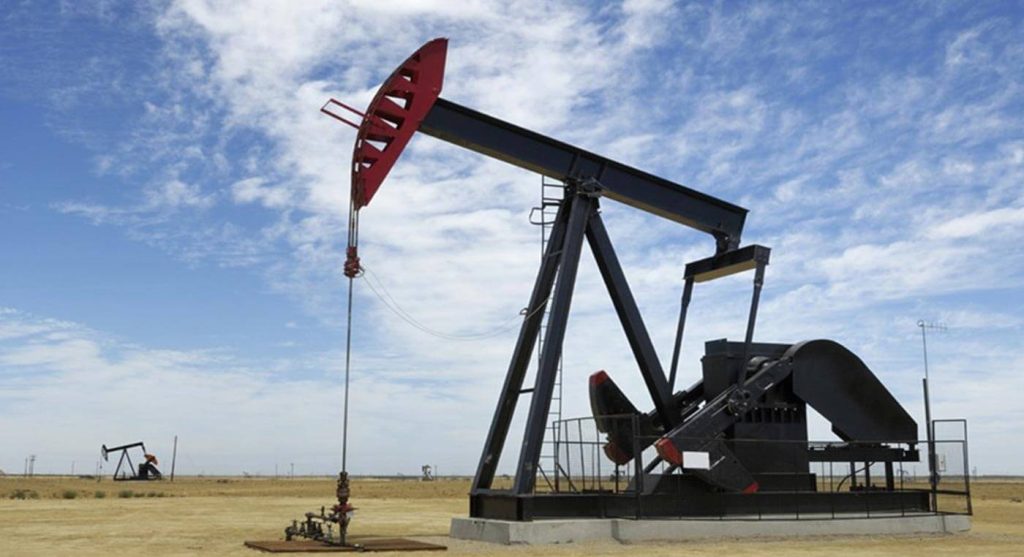
Conclusion
The future of nitrogen generation in the oil and gas industry is focused on increasing efficiency, reducing environmental impact, and lowering operational costs. Innovations in nitrogen generation technologies, such as energy-efficient PSA, membrane, and cryogenic systems, are helping the industry meet stricter environmental regulations while enhancing operational safety and sustainability. These advancements ensure a continuous, stable nitrogen supply with reduced energy consumption, making nitrogen generation more cost-effective and environmentally friendly.
MINNUO offers specialized nitrogen generation solutions designed to meet the unique demands of the oil and gas industry. Our high-performance PSA, membrane, and cryogenic nitrogen generators provide reliable, energy-efficient, and low-maintenance systems tailored for applications such as pipeline inerting, well stimulation, and pressure testing. MINNUO’s solutions ensure safe, efficient nitrogen production to support your operations, backed by expert technical support and industry-leading service. For more information, contact MINNUO today to discuss your nitrogen generation needs.