Oxygen plays a vital role in modern metal smelting. It not only significantly improves smelting efficiency, but also plays a key role in energy conservation, emission reduction, and improvement of metal quality. As the global demand for environmentally friendly and efficient production continues to increase, the application of oxygen is driving the metallurgical industry to develop in a more intelligent and sustainable direction. This article will delve into the application of oxygen in metal smelting and reveal why it is called a “good helper” in metal smelting.
Oxygen plays a vital role in modern metal smelting, greatly improving the smelting efficiency and quality of steel and non-ferrous metals. By participating in the oxidation reaction, oxygen effectively removes impurities, increases the smelting temperature, and accelerates metal extraction. In addition, the use of oxygen also significantly reduces energy consumption and pollutant emissions, promoting the green development of the metallurgical industry. Oxygen generator technology provides a stable supply of oxygen for the metallurgical industry, and combined with intelligent systems, further optimizes the efficiency of oxygen use. In the future, oxygen will continue to assist the smelting process and promote the industry towards intelligent and sustainable development.
Basic principles of oxygen smelting
The core goal of metal smelting is to extract pure metals from ores. Oxygen significantly boosts efficiency by driving oxidation reactions. It reacts with impurities like carbon, silicon, sulfur, and phosphorus, turning them into gaseous or solid oxides, which are then removed. This reaction not only makes the metal purer, but also increases the smelting temperature and accelerates the metal’s melting process.
Oxygen burns with fuel, like coke or natural gas, to generate high temperatures, speeding up the smelting process. Traditional air combustion can’t achieve such heat levels, so oxygen creates a more intense and efficient furnace flame. This extremely high temperature helps extract metal quickly, shortening smelting time and reducing energy consumption.
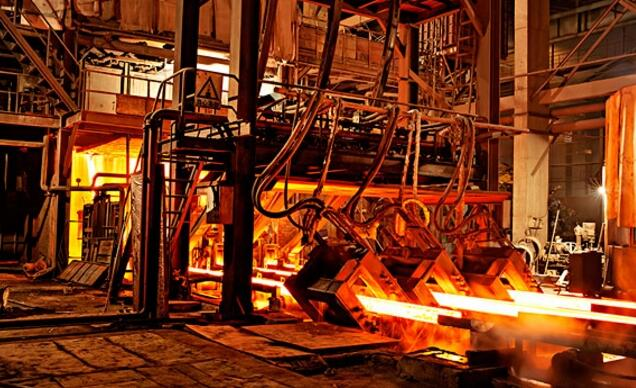
Application of oxygen in steel smelting
The steel industry is one of the most widely used fields for oxygen, especially in oxygen top-blown converter steelmaking and electric arc furnace steelmaking. The use of oxygen has greatly improved the efficiency and quality of steel production.
Oxygen top-blown converter steelmaking
Oxygen top-blown converter steelmaking is one of the most commonly used steelmaking methods in the world. In this process, oxygen is injected into the converter through a high-pressure spray gun. It reacts with impurities like carbon, silicon, and phosphorus in the molten iron, removing them. Oxygen accelerates the chemical reactions and adds heat, raising the furnace temperature to keep the iron molten, which speeds up the smelting process.
The advantages of top-blown converters include:
- Higher efficiency: The use of oxygen significantly shortens the smelting time of each furnace of steel and improves production efficiency.
- Improving the quality of steel: The oxygen reaction helps remove impurities, making the steel purer and more stable in quality.
- Reduced energy consumption: Due to the high temperature generated by oxygen combustion, the need for traditional fuel is reduced, reducing overall energy consumption.
Oxygen application in electric arc furnace steelmaking
Electric arc furnace steelmaking is mainly used to recycle scrap steel. Electric arc furnaces use the high heat from the arc to melt scrap steel. Oxygen aids in removing impurities like silicon and phosphorus by speeding up the melting process. This significantly boosts furnace efficiency, enabling faster and more efficient recycling of scrap steel.
Advantages of oxygen in electric arc furnaces include:
- Fast melting: Oxygen injection increases the temperature inside the electric arc furnace, speeding up the melting of scrap.
- Reduced power consumption: Oxygen provides additional heat, reducing the electric arc furnace’s need for electricity.
- Removal of impurities: Oxygen helps remove unnecessary elements from scrap steel and improves the purity of recycled steel.
Application of oxygen in non-ferrous metal smelting
Oxygen not only plays an important role in steel smelting, but is also widely used in the smelting of non-ferrous metals. It helps improve the purification efficiency and quality of metals such as copper, aluminum, and zinc.
Oxygen application in copper smelting
In copper smelting, oxygen is used in a flash smelting process to remove impurities such as sulfur and iron by reacting with sulfides in the ore. Oxygen not only improves smelting efficiency, but also reduces fuel consumption, thereby lowering production costs. In addition, the use of oxygen increases the purity of the copper, making the final electrolytic copper of higher quality.
Oxygen application in aluminum smelting
During the aluminum smelting process, oxygen is used to increase the reaction temperature and accelerate the decomposition of alumina. This not only increases production speed, but also optimizes the energy usage efficiency of the electrolysis process and reduces energy consumption in aluminum production.
Oxygen helps energy conservation and environmental protection
With the global focus on environmental protection, oxygen use in smelting offers significant environmental and energy-saving benefits. Replacing traditional air combustion with oxygen cuts fuel consumption and lowers emissions of harmful gases like nitrogen oxides. Nitrogen oxides are major contributors to air pollution, and pure oxygen combustion effectively reduces their production.
In addition, oxygen combustion reduces the amount of slag generated and reduces waste disposal costs. Oxygen makes combustion more complete, allowing the smelting process to produce less waste, helping the metallurgical industry improve production efficiency while reducing environmental impact.
The key role of oxygen generator in metallurgy
The widespread application of oxygen is inseparable from the support of oxygen generators. Modern industrial oxygen generators provide high-purity oxygen through cryogenic separation and pressure swing adsorption (PSA), ensuring that smelters maintain stable oxygen supply while producing efficiently. The oxygen concentrators produced by MINNUO are always at the top of the industry. Many metallurgical manufacturers recognize our products and our customers are all over the world.
Oxygen production by cryogenic separation method
Cryogenic separation separates oxygen from other components by liquefying air. This method can produce high-purity oxygen and is widely used in large smelters, especially steel smelters.
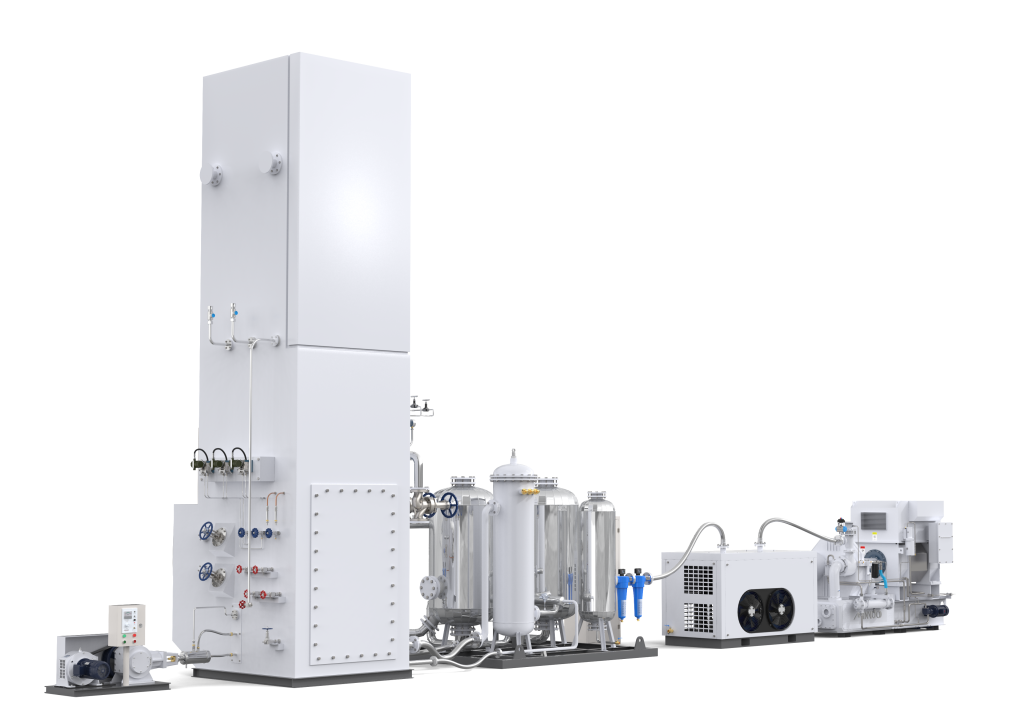
PSA oxygen concentrator
PSA oxygen generator is suitable for small and medium-sized smelters. It separates oxygen from the air through an adsorbent and can flexibly provide oxygen and adjust production volume according to demand. The PSA oxygen concentrator is easy to operate and has low maintenance costs, making it an ideal choice for many small and medium-sized enterprises.
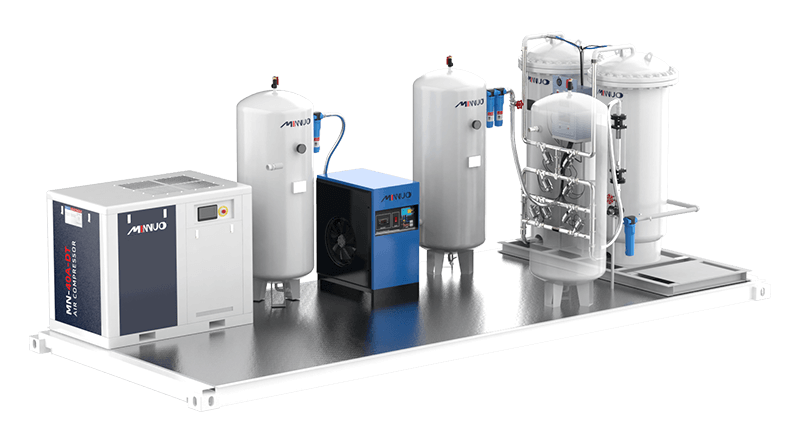
Oxygen and the future of intelligent smelting
As smelters gradually become smarter, the use of oxygen is also more precisely controlled. Through intelligent systems, smelters can monitor and adjust the flow, pressure and purity of oxygen in real time to ensure that the smelting process of each furnace of metal achieves the best results. Big data analysis can also optimize oxygen usage strategies, reduce unnecessary waste, and improve production efficiency.
In the future, oxygen will combine with new energy sources to drive the metallurgical industry toward green and sustainable development. With intelligent technology, oxygen not only boosts smelting efficiency but also plays a vital role in environmental protection and energy conservation.
Conclusion
Oxygen has become a core element in the field of metal smelting. From steel to non-ferrous metals, oxygen has greatly improved smelting efficiency and reduced production costs. It has also helped the metallurgical industry achieve remarkable results in environmental protection and energy conservation. Through the efficient supply of oxygen generators, the application prospects of oxygen will be broader in the future. It is not only an indispensable “good helper” in the current smelting process, but will also continue to promote the intelligent and green development of the metallurgical industry. If you want to know more about oxygen metallurgy, please come for consultation. We at MINNUO will provide you with personalized customized services to promote your metallurgical career to the top.