Oxygen plays a crucial role in numerous industrial, medical, and scientific applications, with its purity level being a key factor in determining its suitability. From medical treatments to manufacturing processes, understanding the different oxygen purity levels and their applications is essential for selecting the appropriate type of oxygen, ensuring optimal performance, safety, and cost-effectiveness.
Oxygen purity grades vary from industrial-grade (90%-95%) for smelting, to medical (≥99.5%) and food-grade (≥99%) for healthcare and preservation. High-purity (99.9%-99.99%) is used in semiconductors, while ultra-high-purity (99.99%-99.999%) is critical in aerospace and research. Specialty gases are tailored for specific industries.
What is Oxygen Purity?
Oxygen purity refers to the concentration of oxygen (O₂) in a sample, expressed as a percentage. The higher the percentage, the purer the oxygen. Pure oxygen is typically defined as having a purity of 99.5% or higher, with the remaining portion consisting of trace gases like nitrogen (N₂), argon (Ar), and carbon dioxide (CO₂). The purity of oxygen is critical for its safety and effectiveness across various fields, as even trace impurities can affect the outcome of certain applications.
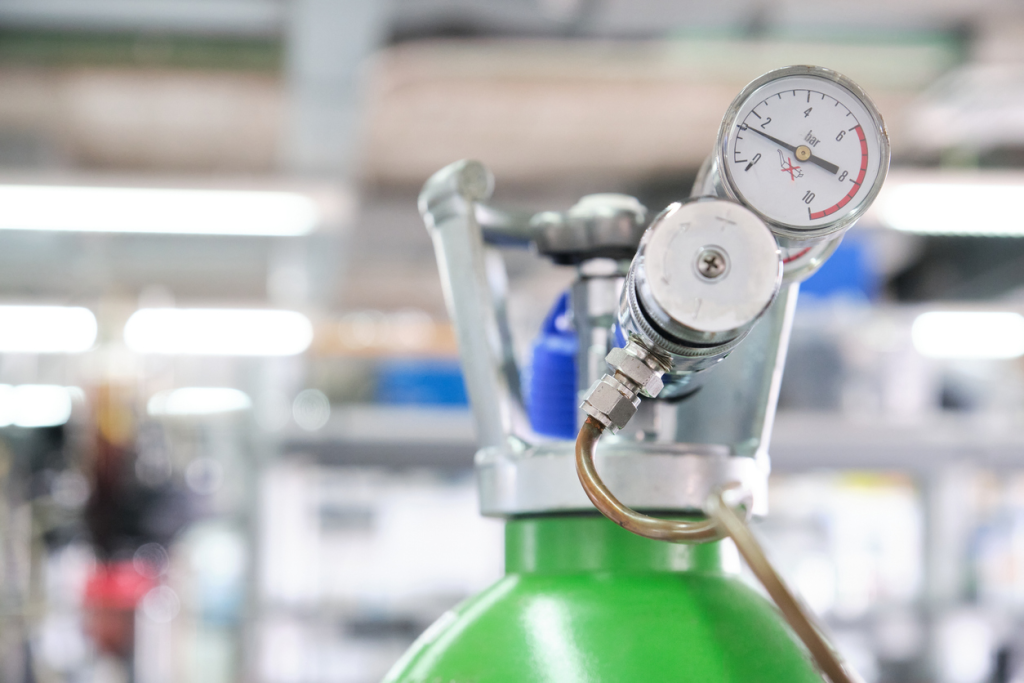
Oxygen Purity Levels and Their Applications
Oxygen purity levels are determined not only by the concentration of oxygen molecules (O₂) but also by the presence of impurities such as nitrogen, argon, and carbon dioxide. These factors directly influence its applicability in different fields. Oxygen purity is classified based on international gas standards, industry requirements, and gas analysis techniques. The purity requirements vary greatly across sectors, with each industry having strict gas quality standards and certification processes.
Industrial-Grade Oxygen (90%-95%)
Applications
Industrial-grade oxygen is primarily used in combustion processes, metal smelting, petrochemical industries, and many other high-temperature chemical processes.
Purity Requirements
Typically, industrial-grade oxygen has a purity of 90%-95%, with the main components being oxygen (O₂) and nitrogen (N₂). The impurity concentration does not significantly impact most industrial applications, as oxygen is mainly used as an oxidizing agent or combustion support in these processes.
Technical Standards
ISO 8573-1 (compressed air quality), ISO 9001 (quality management standards), etc., apply to industrial gas production and supply.
Typical Applications
- Gas combustion: Used in metallurgy for combustion support, oxy-fuel cutting, and welding.
- Oxidation processes: Chemical reactions, petroleum refining, waste gas treatment, etc.
- Glass and ceramics industries: Boosting production temperatures, accelerating glass melting, etc.
Medical Oxygen (≥99.5%)
Applications
Medical oxygen is used in clinical oxygen therapy, anesthetic gas mixtures, and emergency respiratory support, particularly in the treatment of hypoxia, respiratory failure, and chronic lung diseases.
Purity Requirements
Medical oxygen must have a purity of at least 99.5%, with strict control over impurities like moisture, carbon dioxide, and nitrogen to ensure patient safety. Certain special therapies may require higher purity levels.
Technical Standards
Medical oxygen must comply with pharmacopoeias (e.g., European Pharmacopoeia (EP), United States Pharmacopeia (USP)) and GxP (Good Manufacturing Practice) certifications to meet rigorous medical safety standards.
Certifications
Must be certified by FDA, EMA, etc., and comply with ISO 13485 (medical device quality management) and ISO 9001 standards.
Typical Applications
- Long-term oxygen therapy: For respiratory support in patients with chronic diseases such as COPD.
- Emergency and intensive care: Emergency oxygen, anesthetic gases, and respiratory support in ICU patients.
- Surgical support: Providing pure oxygen environments for patients during anesthesia.
Food-Grade Oxygen (≥99%)
Applications
Food-grade oxygen is widely used in food packaging, refrigeration, cold chain logistics, and certain fermentation processes. It helps regulate the atmosphere in food packaging, slow oxidation, and extend shelf life.
Purity Requirements
Food-grade oxygen typically requires a purity of 99% or higher, with very low levels of moisture and impurities (e.g., nitrogen, carbon dioxide) to prevent any negative impact on food quality and safety.
Technical Standards
Food-grade oxygen complies with ISO 22000 (food safety management), FSSC 22000, and other standards to ensure its purity does not contaminate food.
Certifications
Must meet GMP (Good Manufacturing Practices) and HACCP (Hazard Analysis and Critical Control Points) certifications for the food industry.
Typical Applications
- Modified Atmosphere Packaging (MAP): One of the typical applications is Modified Atmosphere Packaging (MAP), which adjusts gas composition in food packaging to extend shelf life.
- Food refrigeration and freezing: Maintaining oxidative stability in low-temperature environments.
- Brewing and fermentation: Used in processes such as beer brewing, alcohol production, and bread fermentation.
High-Purity Oxygen (99.9%-99.99%)
Applications
High-purity oxygen is used in industries that demand stringent precision, such as semiconductor manufacturing, aerospace, fine chemical synthesis, and certain laboratory applications.
Purity Requirements
This oxygen has a purity range of 99.9% to 99.99%, with very low levels of impurities, typically requiring control at the ppb (parts per billion) level, as even trace impurities can affect the quality of end products.
Technical Standards
Meets ISO 14644 (cleanroom standards), ISO 9001, and other quality management system certifications, along with specialized standards for semiconductors, electronics, and precision chemical processes.
Typical Applications
- Semiconductor manufacturing: Used in integrated circuit and other electronic component manufacturing, where impurity control is critical.
- Laboratory gases: For applications such as gas chromatography, mass spectrometry, and environmental monitoring.
- Precision welding and cutting: For processes such as laser cutting, brazing, and fiber optic manufacturing.
Ultra-High-Purity Oxygen (99.99%-99.999%)
Applications
Ultra-high-purity oxygen is used in extremely precise research, aerospace, nanotechnology, and high-end materials manufacturing, because where oxygen purity requirements are highly demanding.
Purity Requirements
The oxygen purity must reach 99.99% or higher, with impurities (e.g., nitrogen, argon, carbon dioxide) controlled to ultra-low ppb or ppt levels (parts per trillion).
Technical Standards
Meets ISO 99.99% purity standards, ISO 14644 cleanroom standards, and typically adopts industry-specific purity standards for aerospace, optics, and other high-tech fields.
Certifications
Complies with international and regional gas quality certification standards, especially for ultra-high-purity gases.
Typical Applications
- Aerospace: Used in spacecraft propulsion systems, life support systems, etc., where oxygen purity and quality are critical for operational safety.
- Advanced research: In fields such as particle accelerators, nuclear physics experiments, etc., where purity is crucial.
- Nanotechnology and materials science: In the manufacturing process, where even the smallest impurity can affect material properties and performance.
Specialty Gas Oxygen (Customized for Specific Needs)
Applications
Specialty gas oxygen is tailored for specific industries with unique needs, where purity, composition, and impurity levels may differ from standard oxygen.
Purity Requirements
The purity and composition of specialty gas oxygen are adjusted according to specific requirements. For example, some applications may require trace amounts of argon (Ar) or carbon dioxide (CO₂) to meet particular reaction needs.
Technical Standards
Customized according to the specific industry and application, with lower standardization and typically controlled based on the industry’s unique requirements.
Typical Applications
- Specialty chemical synthesis: Certain chemical processes require oxygen with specific components to facilitate reactions.
- High-end manufacturing: In processes such as specialty metal smelting, where precise control of oxygen composition is critical.
- Environmental monitoring: Oxygen configured for specific gas monitoring systems.
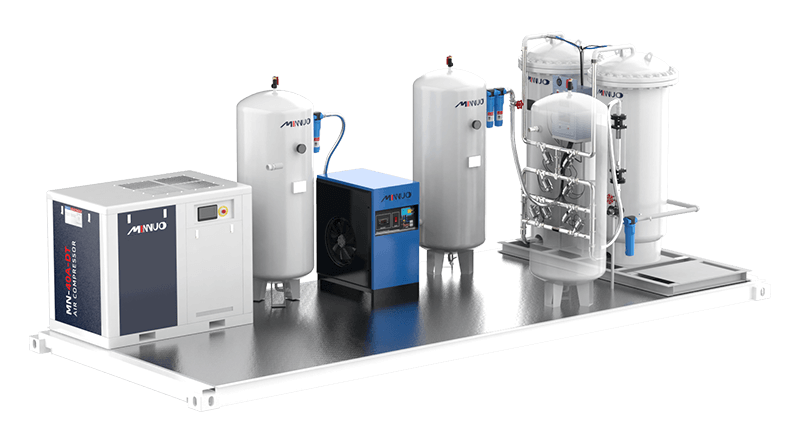
Oxygen Purity Testing and Certification
Testing the purity of oxygen is a crucial step in ensuring it meets the required standards for various applications. Common methods for testing oxygen purity include gas chromatography (GC), thermal conductivity detection (TCD), and paramagnetic analysis. These methods offer high precision and reliability in detecting oxygen concentration in gas samples.
Gas chromatography can precisely separate and quantify oxygen and other gas components, while thermal conductivity measures changes in the sample’s thermal properties to estimate oxygen content, suitable for rapid testing. Paramagnetic analysis relies on the paramagnetic properties of oxygen molecules, measuring concentration through changes induced by an external magnetic field.
Oxygen purity certification is typically conducted by qualified testing organizations.The test report clearly outlines oxygen purity, impurity composition, testing methods, and equipment, and complies with relevant standards. For high-demand applications such as medical oxygen, the certification process is rigorous, adhering to ISO 9001 quality management, ISO 13485 medical device quality management, and FDA and EMA regulatory requirements.
Factors Affecting Oxygen Purity Requirements
Cost and Benefit Analysis
In industrial applications, the choice of oxygen purity directly affects production costs. For applications with higher tolerance for purity (e.g., metal cutting, welding), industrial-grade oxygen (90%-95%) can reduce costs effectively. However, sectors requiring stricter purity (e.g., semiconductor manufacturing, medical use) must select oxygen with at least 99.5% purity. The balance between cost and purity should consider the application’s sensitivity and the quality requirements of the final product.
Environmental and Safety Standards
Industries such as healthcare, pharmaceuticals, and food processing have stringent oxygen purity requirements, mainly due to safety concerns. Standards like the United States Pharmacopeia (USP) and European Pharmacopeia (EP) specify that medical oxygen must have a purity of at least 99.5%. Impurities in oxygen can pose health risks, so that used for medical and food applications must be thoroughly tested and meet specific safety standards.
Impact of Impurities
While industrial applications may tolerate impurities, any impurity in medical oxygen can pose serious health risks. Therefore, medical and food-grade oxygen must be processed and purified to meet strict quality criteria. Some industries, such as the aerospace sector, require near-zero impurity levels, as even the smallest amount of contamination can affect mission success or product quality.
Industry-Specific Requirements
Oxygen application requirements vary across different industries due to differences in process demands and safety standards.
Cost Efficiency
In high-consumption industries such as steelmaking and chemicals, oxygen purity requirements are lower, with industrial-grade oxygen (90%-95%) typically chosen. In these sectors, oxygen is primarily used to improve combustion efficiency or promote chemical reactions, with a higher tolerance for lower purity. This allows for a significant reduction in production costs.
Environmental and Safety Regulations
In industries like healthcare, food processing, and pharmaceuticals, oxygen purity standards are strict, especially in applications where patient or product safety is critical. Any impurities in the oxygen can cause severe health issues or contamination of products. These industries generally require oxygen purity levels of 99.5% or higher, with rigorous testing and certification in accordance with relevant standards to ensure safety and hygiene compliance.
Precision Requirements
High-precision applications, such as semiconductor manufacturing and aerospace, demand extremely high oxygen purity. Even trace impurities can significantly affect chemical reactions, material properties, or experimental results during production. As a result, these sectors typically use oxygen with a purity level of 99.99% or higher, with strict quality control through high-precision detection equipment.
Choosing the Right Oxygen Purity
The choice of oxygen purity should be based on several factors: the technical requirements of the application, cost constraints, safety standards, and product quality. For medical, pharmaceutical, and high-precision research applications, oxygen with at least 99.5% purity is essential to ensure safety and effectiveness. For industrial applications, especially those with lower purity requirements, oxygen with 90%-95% purity is sufficient, helping to reduce overall operational costs.
Future Trends in Oxygen Purity
With the continuous development of high-tech industries, the demand for oxygen with higher purity levels is becoming increasingly extreme, particularly in sectors such as semiconductors, aerospace, and nanotechnology, where the need for ultra-high purity will continue to grow. At the same time, stricter environmental regulations are driving the need for more sustainable practices in oxygen production. Balancing these rising purity requirements with environmental considerations and cost control will be a key challenge in the future of oxygen production technology.
Moreover, the adoption of smart manufacturing and digital technologies may enable more precise, automated monitoring and control of oxygen quality, improving both the precision and safety of its applications.
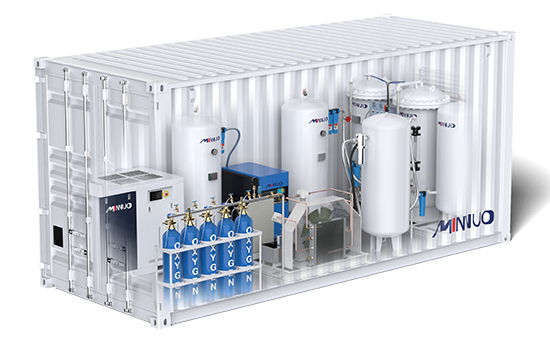
Conclusion
Oxygen purity plays a critical role in ensuring its effectiveness across various applications. The appropriate purity level should be chosen based on factors such as the specific needs of the application, cost considerations, environmental safety standards, and the sensitivity of the use case. As technology progresses and industry demands evolve, the standards for oxygen quality are expected to increase, further influencing the development of oxygen production technologies and their applications.
As a manufacturer specializing in oxygen solutions, MINNUO has accumulated extensive technical expertise over the past 20 years. For more information, feel free to reach out to us!