In modern industrial applications, Pressure Swing Adsorption (PSA) technology plays a vital role in the efficient separation of gases such as nitrogen and oxygen. The PSA process leverages adsorption materials to selectively separate these gases under varying pressure conditions, a critical process for applications ranging from medical oxygen generation to industrial gas production. This article delves into the fundamentals of PSA systems, highlighting the importance of molecular sieve maintenance and the optimization of gas flow processes to ensure consistent system performance.
A key factor in the efficiency and reliability of PSA systems is the molecular sieve used in gas separation. The relationship between the sieve’s longevity and system performance is crucial; proper maintenance and timely replacement of the molecular sieve are essential for ensuring high purity and continuous operation of the PSA system. Furthermore, optimizing the flow and adsorption processes helps mitigate potential downtime and extends the operational lifespan of the equipment.
This article aims to provide an in-depth guide on how to improve the efficiency and stability of PSA systems by optimizing molecular sieve management and system performance. We will explore practical strategies for maintaining the molecular sieve, adjusting operational parameters, and ensuring a consistent flow of high-purity gases. For engineers and industry professionals, this guide will serve as a valuable resource for enhancing the long-term performance and cost-efficiency of PSA oxygen and nitrogen generation systems.
Ⅰ.Molecular Sieve Lifetime Estimation
The lifetime of molecular sieves in PSA (Pressure Swing Adsorption) systems is a crucial factor in ensuring the long-term efficiency and cost-effectiveness of gas separation processes, particularly in oxygen and nitrogen production. Estimating the molecular sieve’s lifespan helps in optimizing system maintenance, scheduling replacements, and preventing unexpected downtimes. This section will explore the key factors that impact molecular sieve lifetime and propose practical approaches to estimating its lifespan based on operational conditions.
1. Factors Affecting Molecular Sieve Lifetime
Operating Parameters:
Pressure, Flow Rate, Temperature, and Humidity:
The molecular sieve’s longevity is directly affected by various operational parameters. High pressure, flow rate, temperature, and humidity can all shorten the sieve’s service life. For example, higher temperatures accelerate molecular sieve degradation by causing more rapid adsorption and desorption cycles, which can lead to cracking or increased wear.
Air Composition and Contaminants:
Air with higher levels of contaminants such as moisture, hydrocarbons, or CO₂ can also affect the molecular sieve. These impurities can clog the sieve pores, reducing its efficiency and lifespan. Therefore, monitoring and controlling air quality entering the system is essential to preserve the sieve.
Desiccant Saturation and Regeneration Cycles:
Frequency of Regeneration:
Frequent regeneration cycles (heating or pressure swing operations) are required to restore the sieve’s capacity, but each cycle slightly degrades the molecular sieve material. The higher the frequency of regeneration, the faster the sieve will wear out.
Regeneration Efficiency:
The efficiency of the regeneration process (whether heat or pressure swing) determines how well the molecular sieve can recover from its adsorption phase. Incomplete or inefficient regeneration can lead to premature aging of the sieve material.
2. Molecular Sieve Performance Degradation Mechanisms
Physical Factors:
Compaction and Cracking:
During prolonged use, molecular sieves can undergo physical changes such as compaction or cracking due to thermal or mechanical stress. The pressure swings and temperature variations cause expansion and contraction of the sieve’s surface, which may eventually lead to a loss of its adsorptive capacity.
Chemical Degradation:
The chemical environment within the adsorption tower can lead to the gradual degradation of molecular sieve materials. For example, exposure to high concentrations of CO₂, water, or other corrosive substances accelerates the chemical breakdown of the sieve, causing it to lose its adsorptive capabilities over time.
Performance Decline:
As the sieve’s adsorption capacity diminishes, the efficiency of the PSA system decreases. The molecular sieve may fail to effectively separate oxygen and nitrogen, which results in lower gas purity and increased energy consumption.
3. Lifetime Estimation Methods for Molecular Sieves
Predictive Models:
Empirical Formulas:
The lifespan of molecular sieves can be estimated using empirical formulas derived from field data. These formulas typically consider factors like operating pressure, temperature, humidity, and the type of adsorbed molecules. By applying these models, one can predict the number of operating hours before the sieve requires replacement.
Dynamic System Monitoring:
Incorporating sensors to monitor parameters like pressure drop, gas purity, and adsorption/desorption cycles in real time can provide early indicators of molecular sieve degradation. By regularly analyzing these parameters, operators can predict when the sieve is approaching the end of its effective life.
Practical Calculation of Lifetime:
To estimate the molecular sieve’s lifetime, use the following general approach:
Calculate Total Cycles: Using operational data, estimate the number of cycles (adsorption and desorption) the molecular sieve undergoes.
Determine Wear Rate: Calculate the wear rate based on temperature, pressure, and cycle frequency. A higher cycle count accelerates the degradation process.
Model Lifespan Based on Degradation: Incorporate known degradation rates for the specific type of sieve used to estimate the remaining service life.
4. Improving Molecular Sieve Longevity
Optimal System Design:
To maximize sieve life, the PSA system should be designed to operate within optimal temperature, pressure, and humidity ranges. Proper control of the adsorption and desorption cycles, including minimizing excess heating and pressure swing, can significantly extend the sieve’s useful life.
Maintenance Practices:
Regular maintenance practices, such as periodic cleaning and proper air filtration, can reduce the exposure of the molecular sieve to contaminants, helping to extend its lifespan. Replacing pre-filters regularly and keeping the system free of moisture and oil can also reduce the stress placed on the sieve.
Advanced Molecular Sieve Materials:
Incorporating newer, more durable materials with improved resistance to thermal and chemical degradation can significantly increase the life of the sieve. Some advanced molecular sieves are engineered to withstand harsher operating conditions, resulting in longer service intervals.
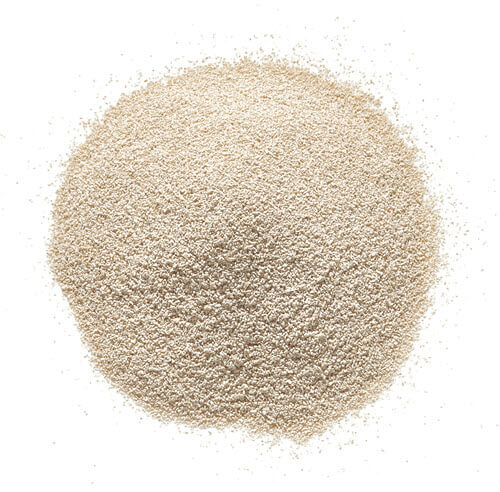
II. PSA System Maintenance Cost Calculation
1.Definition of PSA System Maintenance Cost
The maintenance cost for PSA (Pressure Swing Adsorption) systems is an essential factor in determining the overall operational expenses of such systems. The cost can be broadly categorized into two types:
Preventive Maintenance Costs: These are proactive efforts designed to avoid system failures, like regular inspections, cleaning, lubrication, and part replacements as recommended by the manufacturer.
Corrective Maintenance Costs: These arise when the system experiences unplanned breakdowns, leading to unscheduled repairs, parts replacements, and the associated downtime.
Effective PSA system management requires a balance between both types of maintenance, ensuring that the system operates reliably while minimizing the total maintenance expenditure over its operational life.
2.Maintenance Cost Calculation
a. Breakdown of Maintenance Costs
To calculate PSA system maintenance costs, we need to consider both the direct costs and indirect costs associated with maintaining the system.
Parts Replacement Cost: This includes the cost of consumables such as molecular sieves, valves, gaskets, seals, filters, and other wear parts that need to be periodically replaced. The frequency of replacements depends on factors like the system’s operating hours, pressure levels, and temperature fluctuations. For example, molecular sieve replacement costs can vary significantly based on the operational conditions (e.g., cycle time and the quality of air entering the system).
Labor and Service Costs: The costs associated with labor for routine maintenance tasks, troubleshooting, and system calibration also need to be factored in. Labor costs depend on the level of expertise required (e.g., standard technicians vs. specialized engineers) and the frequency of maintenance activities. Additionally, external service providers for specialized parts or advanced troubleshooting may contribute to the cost.
System Downtime Costs: Maintenance efforts, especially unplanned ones, cause downtime, which could lead to reduced production efficiency or loss of output. Estimating the cost of downtime (including missed opportunities and operational inefficiencies) is crucial for a comprehensive maintenance cost analysis.
b. Factors Affecting Maintenance Cost
System Age and Wear: Older PSA systems or those with high operating hours will generally incur higher maintenance costs due to the increased likelihood of part failures and the need for frequent replacements.
Operating Conditions: PSA systems operating under extreme conditions (e.g., higher temperatures, more frequent cycle times, or harsh environments with high moisture levels) will naturally have a higher maintenance cost, as these conditions accelerate wear on components.
Preventive Maintenance Strategies: Proactive maintenance strategies, like scheduled cleaning, monitoring, and performance checks, can reduce the frequency of major repairs, thereby lowering long-term maintenance costs. Regular inspections help in identifying potential issues before they become critical, allowing for cost-effective fixes.
3.Maintenance Cost Calculation Methods
a. Calculation Formula
There are several key formulas to help calculate maintenance costs effectively:
Total Maintenance Cost Formula:
Total Maintenance Cost=(Labor Cost+Parts Replacement Cost+Downtime Cost)×Maintenance Frequency
Annual Maintenance Cost Per Unit:
This formula can be used to calculate the cost of maintenance per PSA unit on an annual basis:

This breakdown will help determine the cost efficiency of the PSA system and how well it aligns with production goals.
b. Cost Allocation
In large operations, it is useful to allocate maintenance costs per system, per unit of product produced, or per operating cycle. This helps in determining the maintenance cost per unit of oxygen or nitrogen produced, allowing for a more granular understanding of system performance.
For example, by dividing the annual maintenance costs by the total amount of gas produced, businesses can evaluate the cost-effectiveness of their PSA system.
4. Optimizing PSA System Maintenance Costs
a. Preventive Maintenance to Reduce Costs
A proactive maintenance approach is critical for minimizing the need for emergency repairs and extending the lifespan of components. Key strategies include:
Routine Inspection and Monitoring: Regular checks of the molecular sieve, pressure regulators, and valves will ensure optimal performance and avoid unnecessary replacements.
Air Quality Management: Ensuring that the incoming air meets the necessary quality standards can prevent contaminants from damaging the sieve and other critical components.
b. Optimized Cycle and Pressure Settings
Adjusting cycle times and pressure settings can reduce the stress placed on key components like the molecular sieve. This not only prolongs the sieve’s lifespan but also minimizes maintenance needs.
Cycle Optimization: Shortening cycle times without sacrificing the purity of the oxygen/nitrogen produced can reduce wear and tear on the system.
Pressure Control: Maintaining the right pressure levels prevents overloading the system and decreases wear on components.
c. Smart Monitoring and Data Analytics
Implementing smart monitoring tools and using data analytics can reduce long-term maintenance costs by predicting system failures before they occur. Technologies like IoT-based sensors can monitor key parameters, providing real-time data to help operators make informed decisions about when maintenance is required. This predictive approach avoids unnecessary maintenance and prevents costly unplanned downtimes.
5. Example Case: MINNUO PSA System Maintenance
MINNUO specializes in high-efficiency PSA systems, ensuring both reliable operation and minimal maintenance costs. The company’s design philosophy focuses on optimizing the lifespan of key components such as molecular sieves by reducing cycle frequencies, using advanced materials that extend component life, and improving system cooling capabilities to reduce wear and tear.
For instance, in a high-output industrial setting, MINNUO installed a custom PSA system that reduces wear on molecular sieves by optimizing the cycle time, improving system cooling, and incorporating sensors for predictive maintenance. As a result, the system’s maintenance costs were reduced by 15% over a year, and the lifespan of critical components increased by 20%.
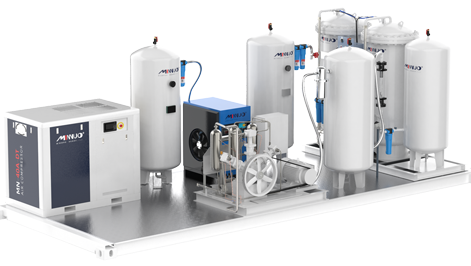
IV. Optimization of Molecular Sieve Lifespan and Maintenance Costs
1. Techniques for Extending Molecular Sieve Life
a. Proper System Design
To maximize the lifespan of molecular sieves in PSA systems, it is crucial to design the system for optimal pressure and flow management. The design should focus on:
Maintaining Optimal Pressure Levels: Ensure that the PSA system operates within an optimal pressure range, as excessive pressure may lead to premature degradation of the molecular sieve. By designing the system to handle pressure efficiently, you can reduce unnecessary wear and tear on the sieve material.
Flow Optimization: Adjusting the system’s flow rates ensures that the molecular sieve does not experience unnecessary stress. Ensuring a balanced flow, especially during regeneration and adsorption phases, will help preserve the sieve’s integrity over time.
Pressure Swing Time: Proper adjustment of the cycle times is vital. A longer cycle time may improve the separation process, but it also increases the wear on molecular sieves. Shorter cycles, while increasing throughput, could reduce efficiency and reduce the sieve’s lifespan. The system should be designed to balance these factors.
b. Effective Operation Conditions
Optimizing the operating conditions is crucial for extending the life of molecular sieves:
Temperature Control: High temperatures accelerate the aging process of molecular sieves. A well-maintained cooling system to regulate operating temperature is crucial to preserve the sieve material.
Regeneration Techniques: Proper and efficient regeneration techniques prevent overuse of the sieves, ensuring they retain their adsorption capacity. Under- or over-regeneration can lead to reduced efficiency or damage to the sieves, leading to higher replacement costs.
c. Monitoring and Real-Time Adjustments
Using sensors to monitor key parameters like pressure, temperature, and flow rates helps maintain optimal conditions for the molecular sieve. By implementing smart monitoring systems, you can make real-time adjustments that reduce unnecessary wear and optimize operational efficiency. This approach allows for early detection of any abnormal conditions that may affect the sieve’s lifespan, allowing for preemptive maintenance rather than costly replacements.
d.Use of High-Quality Materials
Selecting higher-quality molecular sieve materials designed for extended operation in harsh conditions (e.g., high temperature, fluctuating pressures) can significantly increase the sieve’s lifespan. High-performance materials also offer enhanced stability, which reduces the frequency of replacements and lowers long-term operational costs.
2. Maintenance Cost Optimization Strategies
a. Regular Maintenance Scheduling
Implementing a regular and predictable maintenance schedule for PSA systems helps avoid unexpected failures and maintenance costs. Preventive maintenance can help address minor issues before they evolve into more significant problems. By routinely checking and replacing worn-out parts like seals, valves, and molecular sieves, you can prevent downtime and maintain optimal system performance.
b. Energy-Efficient Design
Optimizing the design of the PSA system not only helps extend the molecular sieve’s lifespan but also reduces overall energy consumption, which is a key factor in maintenance cost. Integrating energy-efficient compressors, cooling systems, and pressure management tools reduces the load on the molecular sieve, extending its life and reducing maintenance needs.
c. Data-Driven Maintenance
Using advanced data analytics tools to predict maintenance needs based on real-time data can minimize the risk of unexpected system failures. By incorporating IoT-based monitoring systems, engineers can analyze wear trends, detect performance anomalies, and predict the end-of-life of critical components such as the molecular sieve. Predictive maintenance minimizes both the costs associated with unplanned shutdowns and the frequency of costly repairs.
3. Balancing Maintenance Cost and Performance
a. Cost-Effective Performance Adjustments
While optimizing maintenance costs, it’s essential to ensure that the PSA system maintains high levels of performance. This involves careful balancing of operational parameters such as cycle time, pressure, and temperature. For example, optimizing the cycle time to reduce the frequency of sieve regeneration may lower energy consumption but may impact gas purity. Thus, achieving the right balance between operational efficiency and system longevity is key.
b. Minimizing Downtime and Maximizing Output
One of the most significant costs in PSA system maintenance is downtime, which directly impacts productivity. To minimize this, systems should be designed with redundancy in mind, allowing for partial operation during maintenance. Additionally, designing PSA systems for ease of repair and part replacement ensures that maintenance can be done quickly and efficiently.
c. Cost Recovery through Optimization
The cost-saving benefits of optimization extend beyond just the molecular sieve and include reducing the need for expensive repairs or early replacements. By using high-quality components and implementing real-time monitoring, the lifespan of the entire PSA system can be extended, leading to a reduced total cost of ownership.
4. Practical Example: MINNUO’s Molecular Sieve Optimization
MINNUO’s PSA systems are designed with advanced temperature and pressure regulation mechanisms, ensuring that the molecular sieve operates within the optimal range for maximum efficiency. By using high-quality sieve materials, precise cycle time adjustments, and advanced cooling technologies, MINNUO has successfully extended the lifespan of its systems, reducing the need for frequent maintenance or early sieve replacements.
Case Study: In a large-scale industrial facility, MINNUO’s PSA system, designed with optimized operating conditions, resulted in a 20% reduction in maintenance costs over a year. This was achieved through careful pressure and temperature control, as well as the use of more durable molecular sieves.
Energy Efficiency: The system’s energy consumption was also reduced by 10%, thanks to the advanced design features that minimized unnecessary load on the sieve, while maximizing the efficiency of nitrogen and oxygen production.
V. Practical Case Studies and Examples
Case Study 1: Industrial PSA Oxygen Generator
Overview:
This case focuses on a large-scale industrial PSA (Pressure Swing Adsorption) oxygen generator designed to meet the rigorous demands of a high-output manufacturing environment. The system’s optimization, including both the operational efficiency and maintenance cost calculation, is pivotal in this scenario.
Key Details:
Energy Efficiency: The industrial PSA oxygen system was designed with a focus on energy optimization. Through precise cycle time control and pressure regulation, the system achieved a reduction in energy consumption by 12%.
Maintenance Plan: A proactive maintenance plan was implemented, which included periodic checks of the molecular sieve and compressors. This approach reduced the frequency of unexpected downtimes and extended the lifespan of the system’s key components.
System Design: The system was designed with redundant compressors to ensure constant oxygen supply in case of system failure. The PSA process was optimized to maintain stable operation with low pressure fluctuation, thereby increasing overall productivity.
Results:
Reduction in Operating Costs: By integrating advanced control systems, the company reduced maintenance costs by 20%, which was primarily driven by extending the lifespan of the molecular sieve and ensuring optimal system performance.
Improved Output: Oxygen purity was consistently maintained at 99.9%, while gas output met the higher production demands without compromising energy consumption.
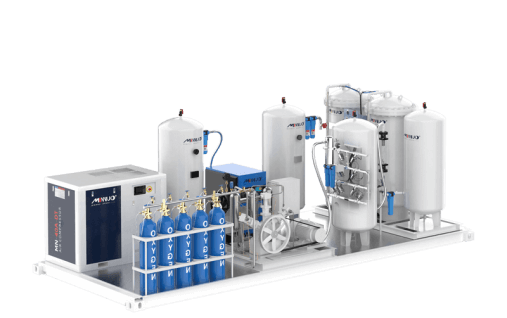
Case Study 2: Food Industry PSA Oxygen System
Overview:
This case examines a PSA oxygen generation system used in the food packaging industry. In food preservation, maintaining high levels of oxygen purity is crucial for keeping packaged products fresh. The system needed to operate efficiently under varying environmental conditions while keeping operational costs low.
Key Details:
Environmental Influence: The system had to be capable of adjusting to fluctuations in temperature and pressure within the facility. These fluctuations were common in high-altitude locations or temperature-sensitive environments.
Design Adjustments: The PSA system incorporated high-performance filters and pressure regulators to optimize gas flow, especially when the external temperature fluctuated, affecting oxygen density.
Cost Optimization: The maintenance cost was minimized by selecting advanced molecular sieves that required less frequent replacement. A detailed cost-benefit analysis was conducted to ensure that energy consumption was kept within reasonable levels, allowing for long-term savings.
Results:
Increased Efficiency: The system’s design allowed for continuous operation with minimal interruptions. This led to a significant increase in product shelf-life and reduced spoilage during packaging.
Operational Savings: By carefully monitoring system pressure and temperature, the food packaging facility reduced the overall operating costs by 15% through a combination of energy savings and optimized system maintenance schedules.
Key Insights from the Case Studies:
Energy Optimization: Both cases emphasize the importance of energy-efficient designs in PSA systems. By fine-tuning the operating parameters (such as cycle time, pressure, and temperature), companies can achieve significant reductions in energy consumption.
Maintenance Planning: Effective maintenance scheduling, coupled with the use of high-quality materials, helps prolong the life of critical components, such as the molecular sieve and compressors, while reducing unexpected repair costs.
Design Flexibility: The ability to adapt PSA systems to varying environmental conditions is crucial for maintaining consistent performance, especially in industries with fluctuating operational environments like food packaging and high-output manufacturing.
Cost-Benefit Balance: Optimizing PSA system design based on operational demands ensures not only the efficiency of the system but also its cost-effectiveness. Regular monitoring and adjustment of system settings can help businesses strike the right balance between maintaining high purity and minimizing energy usage and maintenance costs.
Conclusion
In conclusion, the effective performance and reliability of PSA (Pressure Swing Adsorption) systems are significantly influenced by the proper understanding of molecular sieve management and flow optimization. This article has explored the fundamental importance of molecular sieve functionality, maintenance strategies, and the critical interplay between these components to enhance system efficiency and longevity.
Through the optimization of adsorption processes and system design, as highlighted in the discussion, businesses can achieve not only higher purity and yield but also more cost-efficient and sustainable operations. Moreover, the systematic approach to selecting and maintaining molecular sieves is crucial in ensuring long-term performance stability.
MINNUO, with its advanced PSA technology, offers specialized oxygen and nitrogen solutions that incorporate these best practices for maintenance and system optimization. By integrating MINNUO’s tailored solutions, industries can ensure that their PSA systems perform at peak efficiency, delivering consistent, high-purity gas production while minimizing operational costs and maintenance downtime. This alignment of expertise and innovation in MINNUO‘s PSA technology continues to drive performance excellence across various industries.