In the field of modern metal processing, laser cutting is widely used in the processing of stainless steel, carbon steel, aluminum and other materials by virtue of its advantages of high precision, high efficiency and high degree of automation. However, the selection of nitrogen as an auxiliary gas is crucial to ensure that the cutting edges are smooth and free of oxidative discoloration. Compared with compressed air or oxygen, pure nitrogen in the cutting process can not only effectively isolate the oxidation reaction, but also protect the cutting edge organization, improve the quality of the finished product.
So why is laser cutting so dependent on the purity and pressure of nitrogen? The key is that different materials have different requirements for the cutting environment. For example, if stainless steel is cut in an oxygen environment, oxidization and yellowing are likely to occur, affecting the welding quality and appearance of the finished product. Nitrogen, as an inert gas, does not participate in combustion or oxidation reactions, and is an ideal protective gas source. In addition, high purity nitrogen can significantly reduce nozzle clogging and spattering problems, extending the life of laser equipment.
For factories considering the establishment of their own nitrogen supply system, this article will analyze the logic of matching the purity of nitrogen, output pressure and flow demand, help you assess the bottlenecks in the existing cutting process, and determine whether industrial nitrogen generators should be introduced to replace the traditional bottled or liquid nitrogen distribution, so as to achieve a safe, stable and economical long-term gas supply strategy.
I. Key Index 1: Nitrogen Purity
In the laser cutting process, nitrogen as an auxiliary gas not only plays the role of slag blowing, but more importantly prevents oxidation reactions, thus ensuring that the cutting edges are smooth and free of discoloration. The higher the purity of nitrogen, the better the cutting quality and the lower the rework rate, especially in the processing of high-end materials and export products, the purity has become an uncompromising core index.
1. Nitrogen purity requirements corresponding to common materials
Material type | Recommended Nitrogen Purity Range |
Stainless steel (sheet/plate) | ≥99.99% |
Aluminum alloy/titanium alloy | ≥99.995% |
Galvanized sheet/cold rolled sheet | ≥99.9 |
Description: Insufficient nitrogen purity may result in yellowing of the edge of the cutting seam, carbonization, and obvious burr, which will seriously affect the appearance of the quality and the subsequent welding and painting processes.
2. Common effects of insufficient purity
Yellowing and discoloration: metal surface will be oxidized if oxygen is entrained in nitrogen gas at high cutting temperature.
Blurring and slagging: The oxygen content in nitrogen gas exceeds the standard, and the plasma state formed at the nozzle outlet is unstable, resulting in unclean cutting surface.
Decrease in cutting efficiency: cutting parameters need to reduce power and speed in response to oxygen interference, wasting processing time.
Higher rework rate: especially in the processing of exported workpieces and appearance parts, it will seriously reduce the yield rate and affect the cost of the enterprise.
3. How to choose PSA module to meet the purity requirements
PSA (Pressure Swing Adsorption) nitrogen generator can realize high purity output by the following ways:
Dual Stage Purification Module: On the basis of one section of basic PSA nitrogen production, add a second stage of high purity purification device (up to 99.995%).
Tail gas recovery and injection system: Utilizing the unadsorbed tail gas for blowback recovery to improve nitrogen production efficiency and avoid purity fluctuations.
Filling of high quality carbon molecular sieve (CMS): through optimizing the filling density and gas flow uniformity, effectively improve the upper limit of nitrogen concentration output.
4. High-end equipment recommended configuration: online purity monitoring system
In ≥99.99% purity application scenarios, it is recommended to install online nitrogen purity analyzer:
Detection method: thermal conductivity, zirconia sensor, electrochemical type, etc.;
Data output: 24-hour real-time display and alarm linkage;
Linkage function: When the purity is lower than the set value, it will automatically shut down or switch to the backup gas source to ensure the quality of the cutting and the safety of personnel.
✅ Application Scenario: High power laser above 3kW, export grade precision machining, aluminum/titanium cutting factory, medical instrument manufacturing enterprises.
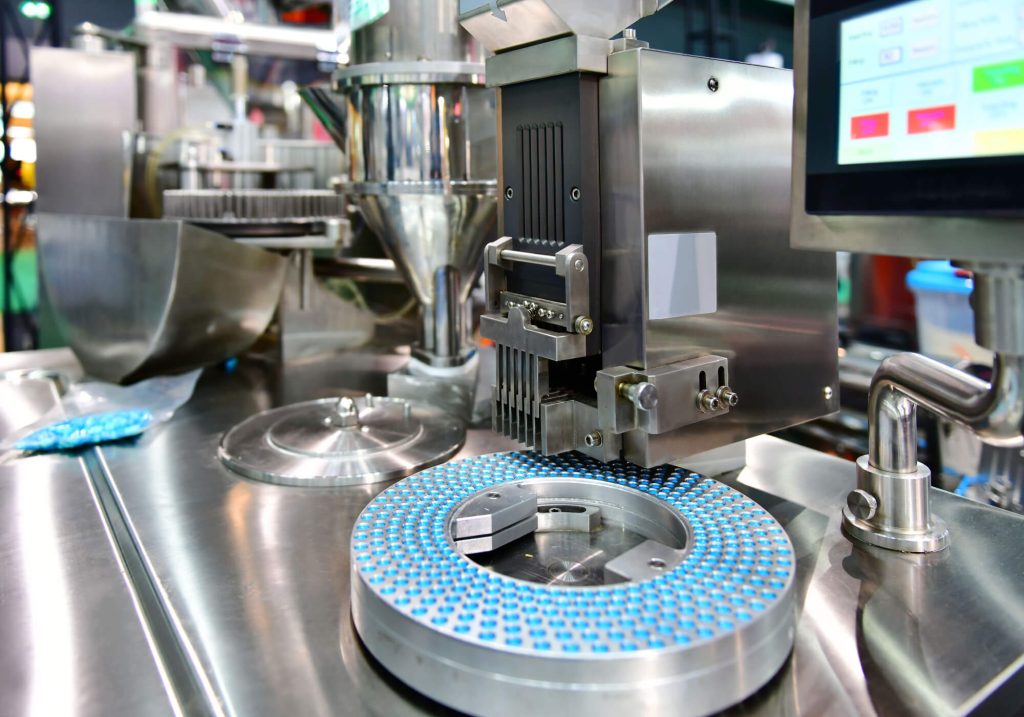
Ⅱ.The key indicators 2: output pressure (Pressure)
laser cutting of nitrogen “purity” to determine the quality of cutting, while the “pressure” has a direct impact on the speed of airflow, slag blowing efficiency and kerf section finish. Especially in the processing of thick plate or high anti-material, nitrogen pressure is often more important than the flow rate. Neglecting to match the pressure when selecting a model will easily lead to process instability and capacity constraints.
1. Basic pressure requirements for laser equipment
Materials & Processing Types | Recommended output pressure range | Explanation of the purpose of cutting |
Thin Plate (≤3mm) | 8~12 bar | Mainly for slag blowing and preventing oxidation reaction |
Medium Thick Plate (4~12mm) | 12~16 bar | Ensure clean cutting section and reduce slag hanging |
Thick Plate or Highly Reflective Material (Aluminum, Copper) | 15~20 bar | Prevent slag rebound from nozzle and guarantee cutting penetration |
Description: The smaller the cutting head nozzle and the higher the power, the more demanding the air pressure requirements. Especially in high-precision cutting scenarios, air pressure fluctuations will directly affect the focus clarity and edge fusion.
2. Why ordinary nitrogen cylinders can’t provide high pressure stably for a long time?
Common problems with traditional cylinders or liquid nitrogen dispensing stations:
Rapid drop of bottle pressure: with the use of time, the pressure inside the cylinder is gradually insufficient, affecting the blowing speed at the nozzle end.
Intermittent gas supply: Downtime is required during cylinder replacement, resulting in unstable production line beats.
High safety risk: High-pressure cylinders are frequently operated and are subject to risks such as tipping and bursting.
Unable to control remotely: the air pressure is not visible, which is not conducive to accurate management and linkage.
❌ Practical consequences: air pressure fluctuation → nozzle clogging/tempering → rough cutting surface, or even rework.
3. How do PSA nitrogen systems meet laser cutting pressure requirements?
Modern PSA nitrogen generators can be supplied at high pressure through a combination of “main unit air supply + high pressure nitrogen booster”:
Primary air supply pressure: usually 0.610 bar, suitable for direct use on thin and medium plates.
Matching booster system: oil-lubricated/oil-free piston booster to raise the nitrogen pressure to 1.520 bar for thick plates.
Optional Constant Pressure Output Module: Combined with an automatic pressure regulator, the air pressure at the front of the cutting nozzle is stabilized within ±0.5 bar.
Suggestion: When cutting thick plates, aluminum plates, titanium alloys, etc., the PSA unit should be equipped with air storage tank and two-stage booster unit to ensure stable output of high pressure for a long period of time.
4. Configuration suggestion and process matching reference
Cutting material type | Recommended Equipment Configuration | Key Tips |
General thin plate (carbon steel, stainless steel ≤3mm) | PSA mainframe (no booster) + online purity monitoring | ≥99.99% Nitrogen, 8~10bar stable output |
Medium-thick plate (stainless steel, aluminum alloy 4~10mm) | PSA mainframe + single-stage nitrogen booster + storage tank | ≥15bar, ensure airflow through the slit area |
High-power laser + high-reflective material | PSA dual-stage high-purity module + booster + precision regulator | Oxygen residue ≤1%, pressure stability < ±0.3bar |
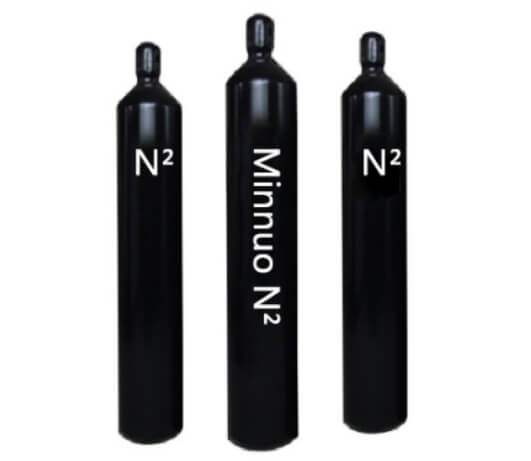
Ⅲ.The key indicators 3: flow (Flow Rate)
Nitrogen flow is one of the key variables to ensure the efficiency of laser cutting and the quality of the kerf. Different power laser equipment, different cutting materials and thickness, there are significant differences in the requirements for flow rate. Ensuring stable and sufficient flow rate supply is the basis for avoiding quality problems such as gas breakage, over-burning and slagging.
1. Correspondence between different laser power and flow rate
The laser power is directly proportional to the instantaneous flow rate of nitrogen, and the common estimation references are as follows:
Laser power | Recommended Nitrogen Flow Range | Unit Description |
1kW | 200-300 L/min | Conventional cutting of thin plates (<3mm) |
3kW | 600-900 L/min | Medium-thick plates (3-8mm) |
6kW | ≥1500 L/min | Thick plates/high-strength alloy materials |
≥10kW | ≥2000 L/min (redundant design required) | Precision cutting, high-speed piercing |
Unit conversion tips: 1 Nm³/h = 16.67 L/min, some manufacturers use Nm³/h to express the flow rate.
2. Dynamic cutting vs. continuous cutting: flow rate stability is more critical
Dynamic cutting scenarios (high-speed contour speed, small holes, high-frequency piercing): instantaneous gas fluctuations, the system needs to have the ability to quickly adjust.
Continuous cutting scenarios (large format, automatic loading and unloading): the flow rate needs to be kept constant for a long time to avoid the gas pressure falling back and leading to poor processing.
If you use cylinders to supply gas, due to uneven flow and bottle pressure decay, it is very easy to lead to unstable gas, it is recommended to use PSA system + buffer tank combination program to improve the response speed of the gas source and capacity buffer capacity.
3. Analysis of the consequences of insufficient flow
❌ Cutting failure: incomplete or interrupted perforation, scrapping of the workpiece;
❌ Overcooking and yellowing: charring of the section, expansion of the heat-affected zone;
❌ Frequent shutdowns: system alarms, laser protection mechanism is activated.
Recommendation: When selecting the model according to the laser power, reserve ≥ 20% flow redundancy and configure a centralized gas supply network or a large-volume buffer tank in the case of multiple workstations/multi-machine linkage.
Ⅳ.How to choose the right nitrogen generator according to the equipment and materials?
In laser cutting applications, the selection of the appropriate nitrogen generator is not only related to whether “can be used”, but also affect the cutting quality, equipment matching and production efficiency. Comprehensive consideration should be given to the power of the laser equipment, cutting material type, process beat, running frequency and other factors, choose the most suitable gas supply program.
1. According to the recommended configuration of laser power (2kW / 4kW / 6kW / 10kW)
Different power lasers correspond to different flow rate and purity requirements, refer to the following:
Laser power | Recommended flow configurations | Suggested Nitrogen Purity | Recommended Models | Remarks |
2kW | ≥200 L/min | ≥99.99% | Single Tower PSA Standard | Suitable for stainless steel thin plate cutting |
4kW | ≥400-600 L/min | ≥99.995% | Twin Tower High Purity PSA | Suitable for carbon steel, stainless steel mixed working conditions |
6kW | ≥900-1200 L/min | ≥99.995% | Two Stage Refined PSA + Buffer Tank | Meet the high-frequency continuous cutting |
10kW+ | ≥1500 L/min | ≥99.999% | High Order Integrated PSA System | Recommended to configure multiple gas sources in parallel or centralized gas supply station |
✅ Recommendation: ≥6kW laser equipment should use high-end nitrogen generator supporting online purity monitoring + PLC control, to ensure quality consistency.
2. Single station vs multi-station gas deployment strategy
Stand-alone: suitable for single laser machine, flexible configuration, easy to control;
Multi-station unified gas supply: suitable for centralized operation of multiple laser equipment, recommended the use of the mother + branch gas supply station program, unified control of the pressure and purity, more convenient for automation management.
Multi-station machine is recommended to cooperate with the ring gas circuit + gas equalization module to avoid pressure drop or inconsistent purity at the remote end.
3. Suggestions on selection for mixed cutting scenarios of multiple materials
If it involves mixed cutting of carbon steel, stainless steel, aluminum alloy, etc., the nitrogen generator needs to meet the following conditions:
Nitrogen purity is dynamically adjustable (99.99%~99.999%)
Rapid boosting and pressure return capability (≥15 bar)
Automatic recording of cutting tasks and gas usage curve (adapted to MES system)
Configuration suggestions: high purity PSA module + nitrogen buffer tank + online oxygen analyzer. Buffer tank + online oxygen analyzer.
4. Suggestions for intelligent linkage control of laser machine
When selecting the model, give priority to nitrogen equipment that supports linkage with the laser system, so as to realize the following:
automatic gas supply at start-up, automatic gas shutdown at shutdown;
automatic adjustment of gas flow/purity according to the switching of tasks;
automatic alarm for system failure (low pressure/deviation of purity).
Suggested Support: PLC control system + touch HMI interface + oxygen content online monitoring module.
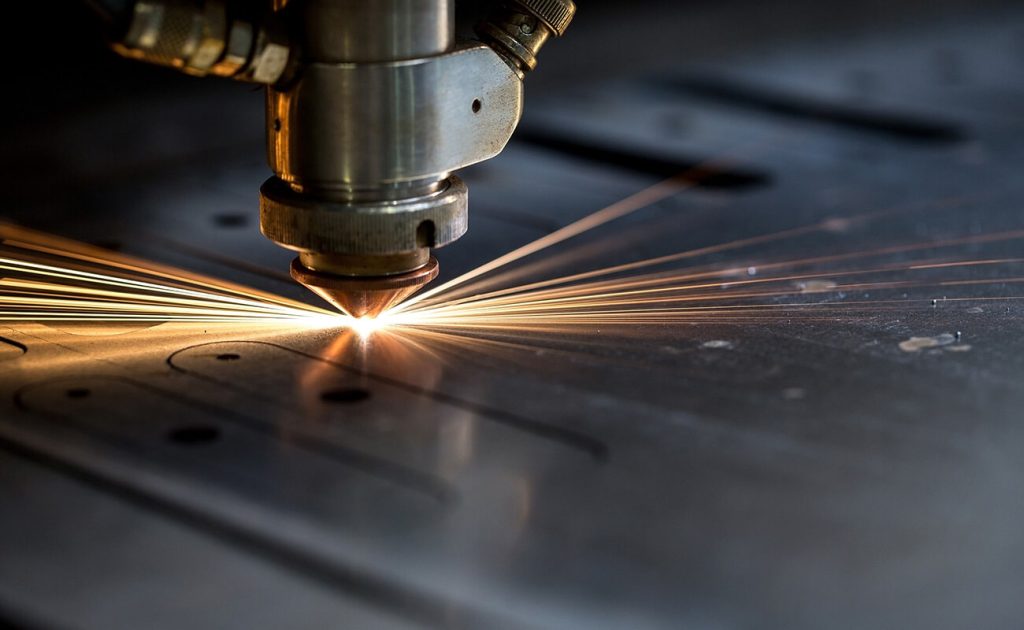
Ⅴ.Case Study: Real-World Deployments
The actual application scenarios can visualize the advantages of nitrogen generator in laser cutting, including cutting efficiency, gas cost, system stability and certification compliance. The following three real-world cases demonstrate the specific benefits of upgrading nitrogen systems for different types of companies.
✅ Case 1: Stainless steel processing plant upgraded to 15bar high-pressure dual-stage PSA, cutting efficiency increased by 30%
Background: A sheet metal manufacturing company originally used ordinary bottled nitrogen, and the bottle pressure was unable to provide ≥12bar gas source stably for a long period of time, which led to frequent interruptions of the cutting process.
Solution: Upgrade to a two-stage refined PSA nitrogen system + high-pressure storage tank, with a stable output of 15 bar, as well as an automatic pressure regulator and purity monitoring module.
Results:
Stainless steel thick plate cutting section more polished, burrs significantly reduced
Laser light continuity improved, cutting efficiency increased by 30% +
Eliminate the need for frequent replacement of gas bottles, improve operator safety
Applicable Suggestions: 4 ~ 10kW laser, stainless steel / aluminum alloy thick plate cutting scenarios
✅ Case 2: Three laser machines share the same centralized gas supply system, saving ¥ 10,000 + in gas cylinder costs per month!
Background: A machine shop with three laser machines originally used multiple nitrogen gas cylinders in parallel, not only the wiring is complex, switching frequently, there are also uneven pressure resulting in fluctuations in the purity of the bottle.
Solution:
Adopting mother station + pipeline zoned centralized gas supply
The main station is equipped with 45Nm³/h PSA system + oxygen content online analyzer
Each laser is equipped with pressure regulator to realize independent gas supply control
Economic benefits:
Reduce the frequency of replacement of bottled nitrogen by about 70 times per month
Directly save the cost of nitrogen ¥ 10,000 +, while reducing the number of manpower
Realize the “one machine, multiple workstations” shared type of gas supply Achieve “one machine, multi-station” shared gas deployment
Application suggestions: medium-sized enterprises, laser machine centralized arrangement of multi-station processing workshop
✅ Case 3: export customers to introduce high-purity nitrogen system to meet the requirements of the European Union welding certification
Background: a company engaged in automotive parts welding export enterprises, the need to pass the ISO 3834, EN 15085, and other European welding certification before export, the requirements of welding shielding gas purity ≥ 99%. Welding shielding gas purity ≥99.999%.
Solution:
Adopt high-precision double-tower PSA module + multi-stage refining system
Support high-precision oxygen analyzer in export pipeline (on-line + off-line)
The gas system automatically records the purity report of each batch, which facilitates the traceability of deliveries
Results:
All the exported products have successfully passed the gas compliance test of the EU customers
The company scored 20+ points in the tender with the “independent gas supply + whole-process monitoring”. The company scored 20+ points in the tender for “independent gas supply + full process monitoring”.
The gas system becomes the core hardware of the certification process.
Recommended for: export-oriented enterprises, high-end manufacturing industry, precision welding factories.
Conclusion
Choosing the right nitrogen generator for laser cutting depends on three key parameters: purity, pressure and flow rate. Materials as diverse as stainless steel and aluminum alloys require nitrogen with a purity of ≥99.99%, while cutting thicker or denser substrates requires a consistent delivery pressure between 15-20 bar. In addition, as laser power increases (e.g. 6 kW, 10 kW), nitrogen flow requirements can exceed 1000 liters/minute, making a stable and dynamic supply critical for edge quality, productivity and equipment safety.
To meet these stringent requirements, MINNUO has customized a high-performance PSA nitrogen generation system for industrial cutting environments. Featuring a two-stage purification module, PLC-linked purity monitoring, automatic drainage and a high-pressure booster, the solution ensures a reliable gas supply even during peak laser workloads. Whether configuring a single workstation or sharing a multi-unit pipeline, MINNUO helps you optimize nitrogen output to match your cutting process – efficiently, safely and with room for expansion.