In the cable manufacturing industry, nitrogen generators have become an indispensable piece of equipment. As industrial development drives higher demands for cable quality, ensuring the conductivity, insulation, and durability of cables has become a pressing challenge for every cable manufacturer. This article will delve into the specific applications of nitrogen generators in cable production, analyzing their various advantages in helping manufacturers improve production efficiency and product quality.
During the cable production process, nitrogen generators are primarily used to provide an inert atmosphere for conductive cores, insulation materials, and other components to prevent oxidation and other chemical reactions that can affect material quality. Nitrogen generators offer an efficient and energy-saving way to produce high-purity nitrogen on-site, reducing reliance on bottled nitrogen and lowering transportation and storage costs. Moreover, nitrogen generators also play a crucial role in the storage and transportation of cables, providing an oxygen-free, dry environment that prevents oxidation and moisture. By flexibly controlling the purity and usage of nitrogen, nitrogen generators help companies enhance production efficiency and optimize product quality. Furthermore, the environmentally friendly features of nitrogen generators align with the sustainable development goals of modern manufacturing.
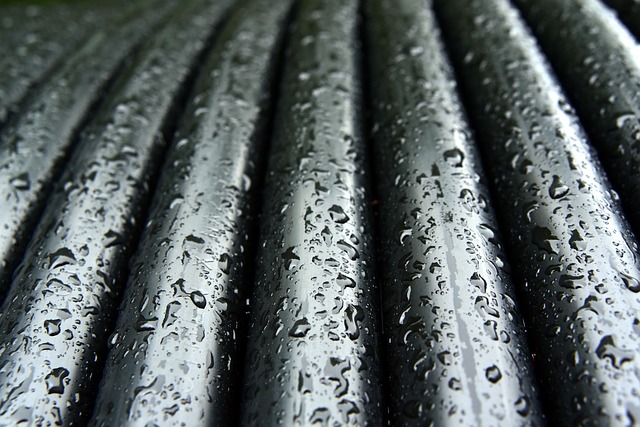
What is a Nitrogen Generator?
A nitrogen generator is a device that can separate nitrogen from the air, typically using Pressure Swing Adsorption (PSA) or membrane separation technology, to produce high-purity nitrogen that creates an oxygen-free environment for industrial production. In cable manufacturing, nitrogen generators can produce nitrogen directly at the production site, avoiding the high costs and logistics challenges of bottled nitrogen. As an inert gas, nitrogen is unlikely to react chemically, making it an ideal choice to prevent oxidation of cable materials during production.
The Importance of Nitrogen Generators in Cable Manufacturing
Cables are generally composed of conductive cores and insulation layers, with materials including metals like copper and aluminum and polymers such as polyethylene and PVC. During manufacturing, these materials, if exposed to air, are highly susceptible to oxidation caused by oxygen and moisture, which directly affects conductivity and insulation performance. Nitrogen generators provide a stable oxygen-free environment during the production process, effectively preventing oxidation and enhancing the durability and safety of cables.
Applications of Nitrogen Generators in Cable Manufacturing
Oxidation Prevention for Conductive Cores
In the production of cables, the copper or aluminum conductive cores need to undergo high-temperature annealing to improve their conductivity and flexibility. However, in high-temperature environments, oxygen in the air can quickly react with the metal, forming an oxide layer that reduces conductivity. Nitrogen generators provide an oxygen-free environment during the annealing process, keeping oxygen at bay and effectively preventing oxidation of the metal cores. This ensures that the conductivity remains intact and that the surface of the material stays smooth, thus extending the lifespan of the cables.
Oxygen-Free Protection for Insulation Materials
The insulation layer of cables is mainly made of polymers like polyethylene or PVC, which need to undergo processes such as heating and extrusion. In high-temperature environments, oxygen in the air can cause insulation materials to age or crack. Nitrogen produced by nitrogen generators creates a protective atmosphere around the insulation materials, preventing oxygen erosion, improving the quality and durability of the insulation layer, and ensuring better insulation performance for the cables.
Storage Protection for Finished Cables
Finished cables stored or transported in air are prone to oxidation or moisture damage. Using nitrogen supplied by nitrogen generators, companies can create a dry, oxygen-free environment in their storage facilities, effectively preventing oxidation and moisture damage to cables. This ensures that the finished cables remain in good condition after production, reducing quality issues caused by storage.
The Multiple Advantages of Nitrogen Generators
High Efficiency and Energy Saving
Compared to traditional bottled nitrogen, nitrogen generators can produce nitrogen on-site, eliminating transportation and storage costs associated with bottled nitrogen. This efficient, economical gas supply method allows cable manufacturers to obtain a stable supply of nitrogen at a lower operating cost, reducing nitrogen wastage and boosting overall production efficiency.
Flexible Nitrogen Purity Control
Different production processes require different nitrogen purity levels, and nitrogen generators can adjust the purity of nitrogen flexibly based on specific requirements. For example, the annealing of conductive cores requires high nitrogen purity, whereas oxygen-free protection for insulation layers can use slightly lower purity. This flexibility not only meets production needs but also effectively conserves nitrogen resources.
Simple Operation and Convenient Maintenance
Modern nitrogen generators are easy to operate, with a high degree of automation. Users can start and stop operations with the push of a button on a control panel. Additionally, nitrogen generators are designed with a rational structure, requiring low maintenance and having a long service life. Regular simple maintenance is sufficient to ensure efficient operation, significantly reducing operating costs for companies.
Improving Product Quality and Enhancing Market Competitiveness
High-quality cable products are more attractive in the market, and the application of nitrogen generators enhances the conductivity, insulation, and durability of cables, ensuring product consistency. Using nitrogen generators, cable manufacturers can produce higher-quality products, establish a strong brand image, and win customer favor and trust, further boosting market competitiveness.
Significant Environmental Benefits
Compared to the transportation and storage of bottled nitrogen, nitrogen generators significantly reduce carbon dioxide emissions. The efficient nitrogen generation technology of nitrogen generators meets environmental standards, reduces energy consumption, and lessens environmental pollution. The use of nitrogen generators not only improves production efficiency but also promotes the sustainable development of enterprises.
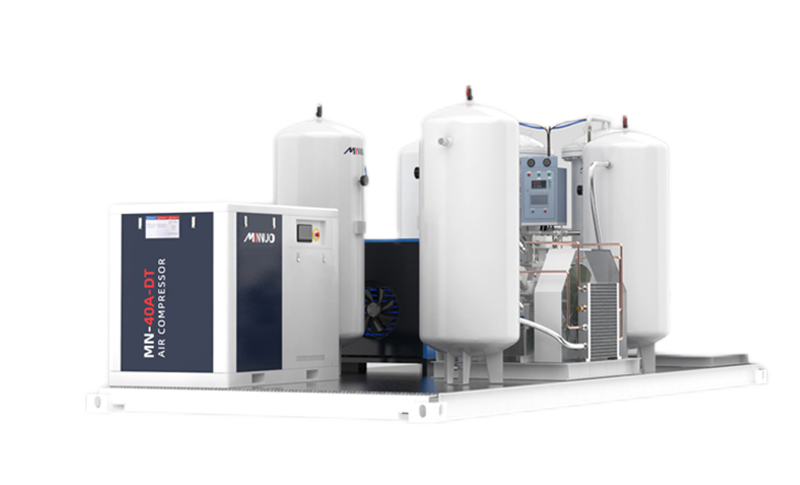
Future Trends in Nitrogen Generator Technology
With rapid technological advancements, nitrogen generator technology is also continuously being optimized and improved. Future nitrogen generators will be more intelligent, with more efficient nitrogen production capabilities and intelligent remote monitoring functions. Companies will be able to monitor nitrogen production, analyze data, and perform preventive maintenance through intelligent systems, effectively improving production efficiency and lowering maintenance costs. It is foreseeable that future nitrogen generators will play an even more critical role in cable production, helping enterprises achieve higher quality and more stable production.
Conclusion
With the growing demand for product quality in the cable market, the adoption of nitrogen generators has become an inevitable trend. MINNUO, with decades of experience in nitrogen generator production, is committed to developing more efficient and intelligent products. We provide comprehensive nitrogen protection solutions to countless cable manufacturers, continually contributing to the higher quality and greater efficiency of the cable production industry.