Laser welding technology has become an indispensable, high-precision, and high-efficiency joining method across various industries. Nitrogen, as a protective gas in laser welding, plays an essential role, and the advent of nitrogen generators has provided a stable and cost-effective nitrogen solution for laser welding. This article will explore the role of nitrogen generators in laser welding and analyze how they help companies improve welding quality, accelerate production processes, reduce costs, and optimize overall production efficiency.
Nitrogen generators provide a stable and economical nitrogen supply for laser welding, effectively preventing oxidation, improving welding quality, and enhancing efficiency. By generating nitrogen on-site, nitrogen generators reduce the cost of gas procurement, streamline production processes, and help companies boost production efficiency while reducing welding defects. As the demand for high-precision welding continues to grow, the application of nitrogen generators in laser welding shows broad prospects, making them a key piece of equipment for improving competitiveness.
Overview of Laser Welding Technology
Laser welding is an efficient technology that uses a focused laser beam as a heat source, delivering high energy to the material’s surface, causing it to melt locally and form a weld. This method is commonly used for joining thin-walled materials and is widely applied in industries such as automotive manufacturing, aerospace, and electronics. The advantages of laser welding include fast welding speed, high precision, and a small heat-affected zone. However, at high temperatures, metal surfaces are prone to react with oxygen in the air, leading to oxidation, decarburization, and other welding defects.
To address this issue, protective gases are used in laser welding to isolate oxygen and prevent oxidation of the molten pool, ensuring the quality of the weld. Common protective gases include argon and nitrogen, with nitrogen gaining widespread use due to its unique advantages in laser welding.
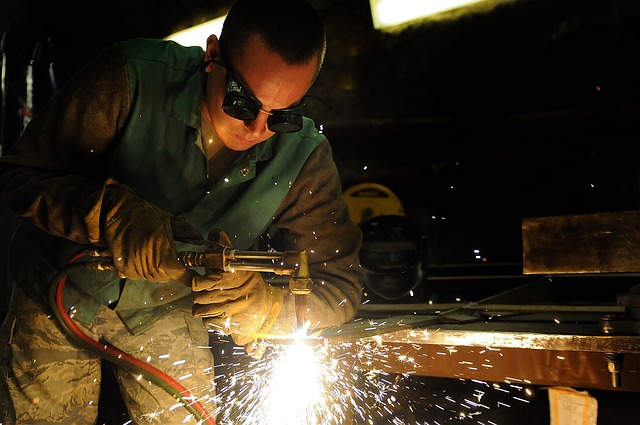
The Role of Nitrogen in Laser Welding
Nitrogen, as a protective gas, effectively prevents the molten pool from coming into contact with oxygen in the air, thus preventing oxidation reactions. By using nitrogen to protect the molten pool, it ensures the strength and appearance of the welded joints, avoiding defects such as porosity, cracks, and the formation of oxides. Additionally, nitrogen provides a cooling effect, helping to control the molten pool’s temperature and reducing damage to the material caused by overheating.
Compared to argon, nitrogen offers a stronger cooling effect, which helps increase welding speed and precision. Particularly when welding high-strength materials such as stainless steel, titanium alloys, and aluminum alloys, nitrogen effectively reduces embrittlement of the welded joints, improving welding quality.
Advantages of Nitrogen Generators in Laser Welding
A nitrogen generator is a device that extracts nitrogen on-site by separating nitrogen from oxygen and other components in the air, providing high-purity nitrogen for laser welding. Compared to traditional liquid nitrogen supply methods, nitrogen generators are not only more economical and efficient but also provide stable and continuous gas supply, ensuring smooth welding operations. Below are the specific advantages of nitrogen generators in laser welding:
Improving Welding Quality: Nitrogen’s Protective Role
The main role of nitrogen in laser welding is to protect the molten pool and prevent oxidation. Oxygen coming into contact with the molten pool leads to the formation of oxides, which affect the weld quality. The high-purity nitrogen provided by nitrogen generators effectively isolates oxygen, reducing the risk of oxidation and ensuring the strength and appearance of the weld joints.
Furthermore, nitrogen helps lower the temperature of the heat-affected zone, reducing material deformation and strength loss due to overheating, thereby improving welding quality and ensuring the structural stability of the welded joints.
Increasing Welding Efficiency: Accelerating Production Processes
Nitrogen generators provide a stable nitrogen supply for laser welding, avoiding the issues associated with external gas supply instability. Especially in large-scale production, nitrogen generators can provide a continuous supply of nitrogen, ensuring that the production line is not halted due to insufficient gas supply. This not only increases welding speed but also shortens production cycles, significantly boosting production efficiency.
Additionally, the cooling effect of nitrogen helps control the welding temperature, preventing welding defects caused by overheating and further improving welding efficiency.
Cost Savings: Reducing Gas Procurement Expenses
Traditional nitrogen supply methods typically rely on purchasing and transporting liquid nitrogen, which is costly. In contrast, nitrogen generators produce nitrogen on-site by separating it from the air, reducing the costs associated with gas procurement, transportation, and storage. For manufacturers requiring large amounts of nitrogen over the long term, using a nitrogen generator can significantly reduce operating costs.
Moreover, the efficient gas utilization of nitrogen generators minimizes gas waste, ensuring that every unit of nitrogen is fully utilized, thus improving economic efficiency.
Enhancing Safety and Environmental Friendliness
Nitrogen is a non-toxic, non-hazardous, and non-combustible gas, and using a nitrogen generator eliminates the need to store and transport hazardous gases, reducing safety risks. Furthermore, nitrogen generators do not produce waste gases, aligning with green manufacturing and environmental protection standards. On-site nitrogen generation reduces the risk of leakage during transportation, providing a safer and more environmentally friendly gas solution for the production process.
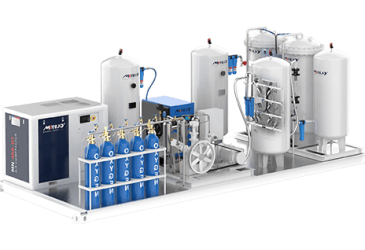
How to Choose the Right Nitrogen Generator
Selecting the right nitrogen generator is crucial for ensuring smooth laser welding operations. When choosing a nitrogen generator, companies should consider the following factors:
Nitrogen Purity Requirements
Different welding processes have different nitrogen purity requirements. High-precision and high-strength material welding may require nitrogen with a purity of 99.99% or higher. It is important to choose a nitrogen generator that meets the required purity levels to ensure welding quality.
Gas Demand and Production Scale
Larger-scale enterprises will need nitrogen generators with a higher production capacity to meet continuous gas demand. Smaller companies may opt for generators with lower capacities to reduce initial investment costs.
Equipment Stability and Maintenance Costs
The stability of the nitrogen generator directly affects production efficiency, so it is essential to choose high-performance, reliable equipment. Additionally, the maintenance costs of the equipment should also be considered.
The Future of Nitrogen Generators in Laser Welding
As the demand for improved production efficiency and quality in manufacturing continues to grow, the application of nitrogen generators in laser welding will expand further. By enhancing welding quality, speeding up production processes, reducing costs, and promoting green manufacturing, nitrogen generators are becoming an indispensable part of modern laser welding.
With continuous advancements in nitrogen generation technology, nitrogen generators will play a more prominent role in various industrial sectors, driving smart manufacturing and efficient production.
Conclusion
The role of nitrogen generators in laser welding goes beyond simply providing nitrogen. By offering stable and economical nitrogen supply, they help businesses improve welding quality, reduce costs, and boost production efficiency, making them a vital part of modern laser welding operations. For companies seeking to improve welding quality and optimize production processes, selecting the right nitrogen generator is a crucial step in enhancing competitiveness.
If you want to make your business more competitive, choose MINNUO nitrogen generators and experience the unexpected benefits they can bring.