In industrial production, nitrogen generators are widely used in many fields such as chemical industry, food packaging, and electronic manufacturing. As an efficient and practical gas separation equipment, nitrogen generators can provide high-purity nitrogen. However, many users will encounter a common problem when using nitrogen generators – insufficient pressure. Nitrogen generator pressure issues not only affect nitrogen purity and output but can also lead to production delays. This article will analyze in detail the common reasons for insufficient pressure in the nitrogen generator and provide corresponding solutions to help you solve the pressure problem of the nitrogen generator.
Insufficient pressure in a nitrogen generator is a common issue that many industrial users encounter, impacting nitrogen purity and production efficiency. Reasons for pressure problems can include insufficient air supply from the compressor, aging or clogged adsorbent, malfunctioning solenoid valves, system leaks, and clogged output lines.
Causes and Solutions for Low Nitrogen Generator Pressure
To troubleshoot pressure problems, it’s essential to understand how a nitrogen generator operates. Typically, the nitrogen generator relies on an air compressor to supply pressure, and it uses adsorption towers to separate oxygen from nitrogen. When the generator can’t reach the set pressure, the issue could lie in insufficient air supply, issues with the adsorption towers, system leaks, or other factors. Here’s a closer look at each potential cause and solution.
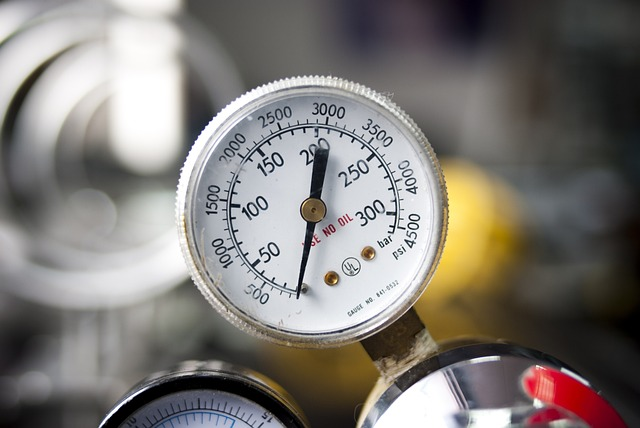
Insufficient Air Supply from the Compressor
The air compressor is the power source for the nitrogen generator. If the compressor can’t supply enough air, the generator won’t be able to reach the desired pressure. Common reasons for insufficient air supply include:
- Insufficient Output from the Compressor: Worn or aging compressor parts can cause unstable airflow.
- Compressor Malfunction: Issues with the motor or leaks in the system can lower the compressor’s efficiency.
- Blocked Filters: Clogged intake filters prevent proper airflow, reducing the compressor’s output.
Solution: Regularly inspect the compressor to ensure it’s in good working condition, clean or replace intake filters, and ensure air can flow freely. If you notice the compressor’s output is consistently low, repair or replace it as needed.
Aging or Clogged Adsorbent
Nitrogen generators often use Pressure Swing Adsorption (PSA) technology, relying on adsorbent material within adsorption towers to separate oxygen from nitrogen. The condition of the adsorbent is crucial for effective nitrogen production, and aging or clogged adsorbent can result in low nitrogen output pressure. Common issues include:
- Aging Adsorbent: Over time, the adsorbent’s efficiency declines, leading to less effective nitrogen separation.
- Clogged Adsorption Towers: Contaminants accumulate in the adsorbent, restricting airflow and reducing separation efficiency.
- Insufficient Amount of Adsorbent: An inadequate amount of adsorbent reduces the generator’s ability to separate oxygen effectively.
Solution: Regularly replace the adsorbent and ensure the adsorption towers are clean. Also, verify that there’s an adequate amount of adsorbent to maintain proper nitrogen output pressure.
Solenoid Valve Malfunction
Solenoid valves control the flow of gas into the adsorption towers, making them essential to the nitrogen generator’s performance. If a solenoid valve malfunctions, it can disrupt airflow, preventing the generator from reaching the set pressure. Signs of solenoid valve issues include:
- Valve Sticking: Over time, solenoid valves can stick due to dust or oil buildup, impeding airflow.
- Damaged Solenoid Valve: Worn coils or seals can result in improper gas flow, affecting pressure levels.
Solution: Clean the solenoid valves regularly to ensure smooth operation. If a solenoid valve shows signs of damage, replace it promptly to restore normal airflow.
System Leaks
Leaks in the system’s piping, joints, or valves can prevent the nitrogen generator from maintaining proper pressure. These leaks not only waste nitrogen but also make it difficult to achieve the required pressure. Common causes of leaks include:
- Aging Pipes: Pipes can deteriorate over time, leading to small cracks or leaks.
- Worn Seals: Seals in pipes and connectors may wear out, compromising the system’s airtightness.
Solution: Regularly inspect the system for leaks, especially in high-pressure areas. Replace any worn or aged seals or pipes to maintain the system’s integrity and ensure stable pressure.
Clogged Output Line
If the nitrogen generator’s output line is clogged, nitrogen can’t flow out smoothly, resulting in low pressure. This clogging often occurs due to accumulated contaminants or moisture in the air. In humid environments, moisture buildup can lead to blockages in the output line.
Solution: Periodically clean the output line and air filters to ensure uninterrupted airflow. In environments with high humidity, consider using a dryer or dehumidifier to prevent moisture buildup.
Incorrect Adsorption Tower Switching
In PSA nitrogen generators, the adsorption towers need to switch periodically to maintain consistent nitrogen output. If there is an issue with the tower switching, nitrogen separation may be affected, resulting in unstable pressure. Causes of incorrect switching may include:
- Solenoid Valve Malfunction: A solenoid valve that fails to operate properly can delay tower switching.
- Incorrect Switching Settings: The control system’s timing may not be set correctly, causing delays in the tower switching process.
Solution: Check the control system settings to ensure proper tower switching. Also, inspect the solenoid valves and switching components to verify they are functioning correctly.
Extreme Ambient Temperature
Environmental temperature can affect the efficiency of the nitrogen generator. Extremely high or low temperatures impact the adsorbent’s ability to function, reducing the effectiveness of nitrogen separation. For instance, during cold winter months, the adsorbent may lose activity, leading to low pressure.
Solution: Maintain a stable working temperature for the nitrogen generator to avoid extreme fluctuations. If possible, install temperature control equipment to keep the generator within the optimal temperature range.
Improper Pressure Regulator Settings
The pressure regulator controls the nitrogen output pressure. If the regulator settings are incorrect, or if the regulator is malfunctioning, the generator may not reach the desired pressure. Common problems include:
- Settings Too Low: The regulator is not set to meet production requirements.
- Malfunctioning Regulator: Sticking valves or incorrect calibration can result in unstable output pressure.
Solution: Check the pressure regulator settings to ensure they meet production requirements. If the regulator is faulty, have it repaired or replaced promptly.
Poor Air Quality
Air quality is crucial for the efficient operation of a nitrogen generator. Contaminants like dust, oil, and other particles can clog filters and adsorbents, reducing separation efficiency and lowering nitrogen output pressure. This is especially an issue in dusty environments where particles can quickly accumulate.
Solution: Use high-quality air filters to ensure clean air enters the generator, and replace filters regularly to maintain efficiency. Regular filter maintenance is essential in areas with high dust levels.
Conclusion
To maintain efficient nitrogen generator performance, it’s essential to conduct regular maintenance, checking components such as the air compressor, adsorption towers, solenoid valves, and piping systems. Additionally, controlling the working environment’s temperature and air quality will help keep the generator in optimal working condition.
If you have more questions about the pressure of the nitrogen generator, or want to get professional maintenance advice, please contact MINNUO‘s service team, we will help you achieve a stable and reliable nitrogen supply.