With the improvement of global medical treatment capacity, the improvement of industrial safety standards and the deepening of environmental protection control, the demand for on-site production of high-purity oxygen is growing rapidly. Whether it is the continuous supply of oxygen in hospital ICU wards and operating rooms, or industrial welding, ozone reaction, environmental protection water treatment, etc., all of them put forward higher requirements for the purity, stability and intelligence of the oxygen supply system. In this context, PSA (Pressure Swing Adsorption) technology, as the mainstream route in the field of oxygen production, is being more and more end-users are concerned and adopted.
So, what is PSA oxygen generator? How is it fundamentally different from the traditional low-temperature separation and electrolysis of water for oxygen production? What are its working mechanism, core components, output capacity and applicable scenarios? For users with procurement needs, how to determine which type of PSA oxygen generation system they need? This article will systematically explain these key issues and help you establish a clear technical understanding with practical application scenarios.
Whether you are an engineering planner who is new to oxygen equipment, or an O&M manager who needs to evaluate and upgrade an existing oxygen system, this complete guide to both technology and applications will provide you with a practical reference to help you deploy a compliant, safe, and sustainable oxygen solution in a more scientific and cost-effective manner. Read on to learn more about the logic behind PSA oxygen generators and how to select one.
1. Definition and working principle of PSA oxygen generator
1.1 What Does PSA Stand For?
PSA is the abbreviation of Pressure Swing Adsorption, which is translated as “Variable Pressure Adsorption” in Chinese. It is an advanced technology that realizes gas separation by changing gas pressure under normal temperature conditions. A pressure swing adsorption (PSA) oxygen generator utilizes an adsorbent to remove nitrogen from the air and produce oxygen with a purity of 90% to 93%.
Utilizing the fact that adsorbents (synthetic zeolites) adsorb more nitrogen than oxygen under pressure, these generators remove nitrogen from the air by adsorption under pressure to efficiently produce high purity oxygen. Compared with the traditional deep-cooling air separation method (which requires low-temperature liquefaction) or electrolysis (which has high power consumption and low oxygen purity), PSA oxygen production is more energy-efficient and has a smaller equipment size, which makes it particularly suitable for use in medical care, industry, and small gas stations.
Since they can provide a stable supply of oxygen at a lower cost than liquid oxygen, they have been adopted by a large number of facilities that use oxygen.
1.2 Working Principle Overview
The core principle of the PSA oxygen generation system is that
molecular sieve materials (e.g., Zeolite 13X or LiX) have different adsorption capacities for nitrogen and oxygen in the air at different pressures.
When air is compressed into the adsorption tower, nitrogen is preferentially adsorbed by the molecular sieve, while oxygen is collected through the filter layer;
Then the pressure is lowered, the nitrogen is desorbed and discharged, and the molecular sieve is regenerated to start the next cycle.
Usually adopts the structure of double-tower alternating operation: one tower adsorption, one tower regeneration, to realize the continuous and stable output of oxygen.
The system can realize oxygen purity ranging from 93% to 99.5%, depending on the specific configuration and application.
1.3 Analysis of main core components
Component name | Function Description |
Oil-free air compressor | Provide clean and non-polluting compressed air source, which is the “power heart” of the system operation. |
Adsorption tower + molecular sieve material (e.g. Zeolite 13X / LiX) | Realize the core function area of oxygen and nitrogen separation, the service life is usually 8,000~12,000 hours. |
Automatic valve manifold + PLC control system | Automatically switch the tower group, set the rhythm of adsorption/desorption, and realize the unattended operation. |
Buffer tank + Flow meter + Online purity monitor | Balance the fluctuation of the oxygen output to ensure the stability of the air supply; Monitor whether the oxygen concentration meets the standard |
High-end models are usually equipped with a remote monitoring module, which allows real-time viewing of flow, pressure, purity, and operating status, and supports docking with hospital SCADA systems or factory MES platforms.
Practical advice:
Medical grade users are recommended to choose the equipment with 93±3% stable purity and with online alarm system;
Industrial users (e.g. ozone generators, glass cutting) can choose the ≥95% high purity oxygen version according to their needs.
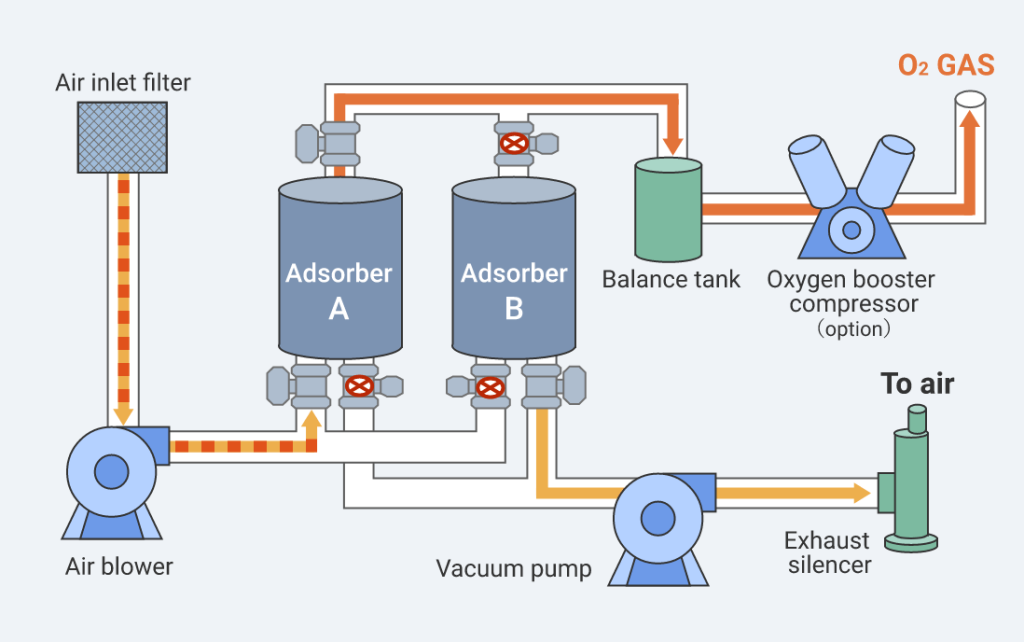
2.Core technical features
2.1 High purity output
One of the biggest technical advantages of PSA oxygen equipment is its flexible oxygen purity adjustment ability, covering the needs of medical, industrial, experimental and other scenarios:
Medical Grade Oxygen: the output is stabilized at 93%±3%, which complies with the standards of China’s YY/T 0298 and the European Pharmacopoeia, and it is widely used in ICUs, operating rooms, and respiratory treatment centers.
Industrial-grade high-purity oxygen: 95%~99.5% (customizable) through double-tower or three-stage refining module, suitable for glass smelting, ozone reaction, metal cutting and other high-purity oxygen source requirements.
✅ Practical advice: for purity-sensitive industries, such as food-grade packaging, electronic chip aging, etc., online oxygen concentration monitor and alarm module can be optional.
2.2 Continuous gas production capacity
PSA oxygen concentrator supports all-weather uninterrupted oxygen supply, which is suitable for the first-line units and high-flow industrial sites with “strong continuity and high operation intensity”:
7×24 hours continuous operation: double adsorption towers are switched alternately to avoid interruption of oxygen supply.
Strong modular expansion capability: the combination of mainframe + expansion tower + pressurization system can flexibly expand the gas volume to 20Nm³/h~300Nm³/h.
Cooperate with buffer gas storage tank: improve the system’s ability to resist fluctuations and stabilize the pressure and flow of oxygen supply.
Recommended application scenarios: large hospital central oxygen supply station, industrial welding workshop, glass furnace continuous oxygen injection.
2.3 High degree of automation
Modern PSA equipment has been upgraded from “semi-automation” to “full-automation intelligent joint control”, which greatly reduces the risk of manual guarding and improves the operation and maintenance efficiency:
PLC programmable control system: adsorption/desorption cycle can be set to realize one-key start/stop and real-time adjustment of operation parameters. Real-time adjustment of operating parameters.
Automatic purity monitoring and alarm linkage: when the oxygen concentration deviates from the set value, sound and light alarms are triggered to ensure the safety of gas quality.
System linkage control: It can be docked to the hospital central control platform or industrial SCADA system to realize remote diagnosis, data uploading, remote start/stop control, and so on.
Function modules | Description |
PLC control | Automatic operation, remote control, data logging |
In-line sensors | Real-time monitoring of oxygen concentration, flow rate, pressure and other key indicators |
Fault warning system | Alarms for motor overheating, pressure deviation, filter obstruction |
3.Application Scenario Analysis
PSA oxygen generator system has been widely used in various scenarios such as medical treatment, industrial production and special protection due to its compact structure, stable operation and customizable features. The following is a scene analysis from three typical dimensions:
3.1 Medical field
PSA oxygen concentrator, as an important component of the central oxygen supply system, shows significant advantages in meeting the requirements of “immediate oxygen supply, safety and reliability, and convenient operation”, etc.:
ICU and inpatient wards: it can realize all-weather continuous supply of oxygen to ensure the life of critically ill patients and support system operation.
Mobile ambulance: Portable PSA equipment can be integrated into the on-board system to provide a stable oxygen source for patients in transit, with UPS power supply to solve the risk of power failure.
Field/emergency mobile medical station: no need for large infrastructure, support temporary construction, power outage backup, rapid deployment, suitable for field hospitals/post-disaster medical assistance and other scenarios.
✅ Recommended configuration: dual-tower adsorption structure + online purity monitoring + battery backup module to ensure stable system operation in unexpected situations.
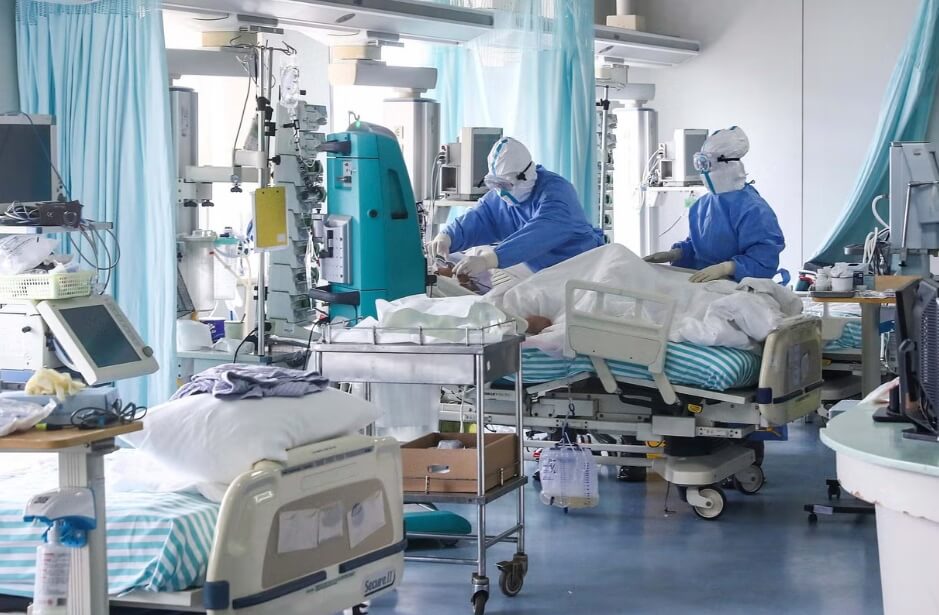
3.2 Industrial field
In the oxygen demand process, industrial PSA oxygen generation system becomes an efficient solution to replace liquid oxygen and cylinder oxygen with high flow rate, high purity and good scalability:
Metal cutting and welding: Oxygen is used for plasma cutting or laser welding, which helps to improve the neatness of the cuts and the combustion efficiency, and it is recommended to use ≥95% industrial-grade high purity oxygen.
Ozone Generator Oxygen Supply: Ozone concentration is directly proportional to the purity of the oxygen source, PSA oxygen supply can significantly improve the efficiency of ozone generation, commonly used in drinking water disinfection, swimming pool water purification.
Glass/chemical process kiln: in the high temperature melting process, the introduction of high concentration of oxygen can reduce fuel consumption, improve the precision of temperature control, applicable to float glass, electronic glass and other manufacturing processes.
✅ Recommended configuration: multi-tower joint supply program + oxygen buffer tank + PLC centralized control to guarantee the consistency of oxygen source for multiple stations.
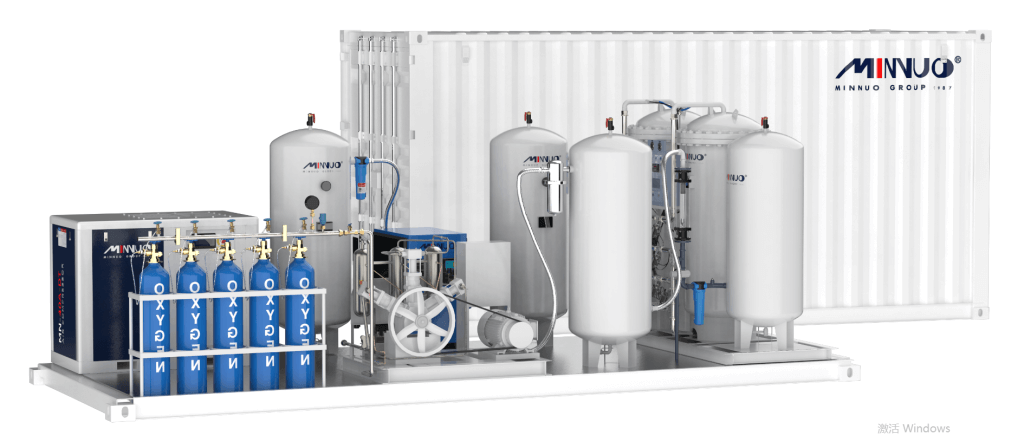
3.3 Special Scenarios
In addition to conventional medical and industrial applications, PSA oxygen generation system can also meet some of the application occasions that require high adaptability to the conditions of use and environment:
Plateau low oxygen supply: such as >3000 meters above sea level, the efficiency of oxygen supply from traditional oxygen cylinders is low, while plateau-type PSA system can still maintain more than 93% of stable oxygen production after the booster unit is configured.
Wartime/disaster emergency protection: such as earthquake command posts, temporary field hospitals, closed tunnels, etc., the modular oxygen generating equipment + mobile gas delivery system, rapid deployment of the “oxygen front line”.
Cold chain transportation/food preservation station: Provide pure oxygen protection for supporting ozone or controlled oxygen storage system to extend the shelf life of fresh agricultural products.
Advantages vs Other Oxygen Supply Methods
Comparison dimensions | PSA Oxygen Generator | Liquid Oxygen Tanks | High Pressure Oxygen Cylinders |
Initial investment | Medium | High | Low |
Operating costs | Low | High | High |
Oxygen purity | 93~99.5% | ≥99.5% | ≥99.5% |
Operational safety | High | Risk of cryogenic/high pressure | High Pressure Risk |
Convenience | Automatic operation | Transportation dependent | Frequent Replacement |
4.Selection Guidelines
Choosing a suitable PSA oxygen concentrator does not only depend on the budget, but should also be systematically evaluated around the specific parameters required for the application scenario. The following are five key dimensions of selection recommendations to help users accurately match the target scenarios and equipment parameters:
4.1 Define the target oxygen purity
Different application scenarios correspond to different oxygen purity requirements:
Application Scenarios | Recommended Oxygen Purity | Description |
Medical Oxygen (Hospital ICU, Clinic) | ≥93% (±3%) | Comply with YY/T 0298 national standard or European Pharmacopoeia standard |
Food Ozone Reaction, Aquaculture | ≥95% | Ensure the reaction efficiency or water oxygen enrichment level |
Industrial Laser Cutting, Glass Combustion | ≥99.5%~99.9% | Suitable for high end processing or exporting requirements |
Recommendation: If export certification is required, select a multi-stage purification module up to 99.9% or greater, with an on-line oxygen concentration monitoring system.
4.2 Verify the Oxygen Flow Rate and Unit (Flow Rate)
The appropriate unit of oxygen production (L/min or Nm³/h) should be selected based on the terminal gas consumption rate of the equipment:
Typical Oxygen Equipment | Recommended flow rate range | Unit description |
Single Bed Ventilator | 5 to 10 L/min | Suitable for small portable units |
Shared Oxygen Supply for 3-5 Beds in Hospitals | 20 to 60 L/min | Suitable for compact all-in-one units |
Medium Ozone Equipment/Welding Station | 5 to 10 Nm³/h | Industrial grade all-in-one or split systems |
Centralized Oxygen Supply in Plants (10+ Terminals) | ≥30 Nm³/h | Equipped with dual tower + buffer tank system |
Suggestion: Considering the pressure loss of the system, it is recommended to keep 10%~20% of redundant gas volume space to avoid unstable oxygen volume affecting the operation of the terminal.
4.3 Clarify the deployment attributes: fixed or mobile (Deployment Mode)
Different places of use have different requirements for mobility:
Fixed deployment scenarios: such as hospital ICUs, factories, oxygen rooms, etc., it is recommended to choose floor-standing or cabinet-type PSA systems, which are convenient for water, electricity and gas arrangement and remote monitoring.
Mobile deployment scenarios: such as field command post, emergency medical, wartime mobile station, should choose trailer type or small all-in-one machine, support rapid on-board/in-tent deployment.
✅ Tips: If future expansion or site adjustment is required, give priority to “modular model” or “distributed local oxygen supply” program.
4.4 Examination of the basic supporting conditions: power, water, air (Infrastructure)
Power conditions: the power of a single machine ranges from 1kW to 15kW, you need to estimate the total power consumption, to confirm whether to support 220V/380V.
Water conditions: such as with a cold dryer or adsorption dryer need to consider the arrangement of the cooling water source or drainage system.
Air compressor / compressed air: some models need to be connected to an external air compressor, pay attention to the selection of power and pressure range match.
✅ Suggestions: If deployed in unstable areas of power or infrastructure, need to configure UPS power supply or diesel generator backup.
4.5 Whether intelligent remote monitoring, automatic protection function (Smart Control) is required
Medical or export scenarios recommend configuration: PLC remote control system + touch HMI + 24h oxygen concentration alarm;
Industrial scenarios recommend integration: SCADA data platform docking + flow/pressure sensors monitoring;
Special scenarios recommend support: one-key fault self-test, one-key shutdown protection + Temperature and humidity protection kit.
✅ Tips: If the user is distributed in multiple plants/floors, it is recommended to adopt “master + branch” architecture for centralized oxygen source control.
❓Frequently Asked Questions (FAQ)
Q1: What are the core advantages of PSA Oxygen Concentrator over traditional liquid/bottle oxygen?
A: PSA Oxygen Concentrator adopts normal temperature and pressure operation, no need for cryogenic cooling and high-pressure storage, it has the following advantages:
No need for distribution/filling: on-site oxygen production, independent and controllable;
Lower long-term cost: eliminating the need for purchasing, transportation, and manpower handling of bottled oxygen;
Higher safety: avoiding the hidden dangers of evaporation, leakage, or explosion of liquid oxygen;
Stronger continuity: 24/7 continuous supply of oxygen, especially suitable for ICUs, welding lines, ozone reaction, and other occasions. More continuity: 24/7 continuous oxygen supply, especially suitable for ICU, welding line, ozone reaction etc.
Q2: What is the oxygen purity of PSA oxygen concentrator? Is it suitable for medical treatment?
A: The medical standard PSA oxygen concentrator has an oxygen purity of 93%±3%, which is in accordance with the Chinese YY/T 0298 standard and the European Pharmacopoeia. The industrial version can be purified by two-stage purification or LiX molecular sieve to reach **95%~99.5%** or even higher, which is suitable for ozone generator, glass melting furnace and other high-purity demand scenarios.
Q3: Is the PSA oxygen generator stable? Do I need to replace parts frequently?
A: The stable operation of the equipment body can usually reach **≥720 hours/30 days uninterrupted**, daily only need to pay attention to:
molecular sieve life: generally replaced in 3~5 years;
air compressor oil separator core/filter: recommended to be maintained every 4,000~8,000 hours;
Oxygen analyzer/PLC: recommended to be calibrated once a year.
MINNUO equipment supports intelligent alarm, joint control shutdown, remote troubleshooting, which is convenient for engineers to control the operation status remotely.
Q4: Is it suitable for me to use a portable PSA all-in-one or a large fixed system?
A: Refer to the following table for quick judgment:
Applicable conditions | Recommended models |
Need for temporary deployment, field rescue, mobile oxygen supply | Portable all-in-one/vehicle-mounted |
Hospital ICUs, community rehabilitation centers, centralized oxygen supply in welding shops | Fixed medium-large split system |
Plateau/hot and humid/power outage scenarios | Recommended configurations Battery + UPS + wide temperature system |
If you are unsure of the model, please feel free to contact the MINNUO team for one-on-one configuration advice.
Q5: What types of PSA oxygen solutions does MINNUO offer?
A: MINNUO can provide customized service from small 3L/min medical oxygen system to 300Nm³/h industrial large-scale system, the core features include:
Modular design, fast delivery;
Multi-stage purification system, support 93%~99.5% purity;
PLC remote control, support SCADA/hospital system integration;
Equipped with medical oxygen analyzers, filtration module, dual tower alternating operation system, etc.
Q6: Does PSA oxygen system support export or meet international certification?
A: Yes, MINNUO oxygen system can provide CE certification, ISO13485 medical device system certification, EU MDR documentation package, and comply with China YY/T 0298, GB 9706 series standards, widely exported to Europe, America, the Middle East, Africa and Southeast Asia markets.
Conclusion
PSA (Pressure Swing Adsorption) oxygen generation technology has become the mainstream oxygen supply solution in many scenarios, such as hospitals, factories, food production, mobile ambulance and so on, by adsorbing and separating the oxygen in the air with high efficiency. With the advantages of normal temperature and pressure operation, no need for cryogenic liquefaction, and support for automation and remote control, PSA oxygen generation system not only can continuously and stably output 93% to 99.5% of high purity oxygen, but also significantly reduces the operational risk and long-term cost, which is a safe and economical alternative to the supply of bottled oxygen and liquid oxygen.
MINNUO provides one-stop PSA oxygen generation solutions from 10L/min to 300Nm³/h, supporting intelligent functions such as modular deployment, purity monitoring, and residual oxygen joint control, which can be customized and integrated according to customers’ specific needs. Whether you are a hospital ICU, industrial welding, cold chain processing or field emergency user, MINNUO can help you build a high-purity, high-safety, intelligent and controllable oxygen supply system, improve operational efficiency, reduce costs, and realize compliant and safe oxygen protection. Welcome to visit https://minnuogas.com/ for customized advice and solution support.