Nitrogen (N₂) is a vital industrial gas used in a variety of applications, including food preservation, plastic injection molding, and fire suppression. Comprising about 78% of Earth’s atmosphere, nitrogen is readily accessible for extraction. One of the most efficient methods for on-site nitrogen production is membrane separation nitrogen technology, which allows industries to generate nitrogen at the required purity levels without relying on external gas suppliers.
Membrane separation nitrogen technology is an efficient process that separates nitrogen from air using special membrane materials. After compressed air enters the membrane module, the membrane materials separate gases based on their varying permeation rates, expelling oxygen and water vapor while retaining nitrogen.
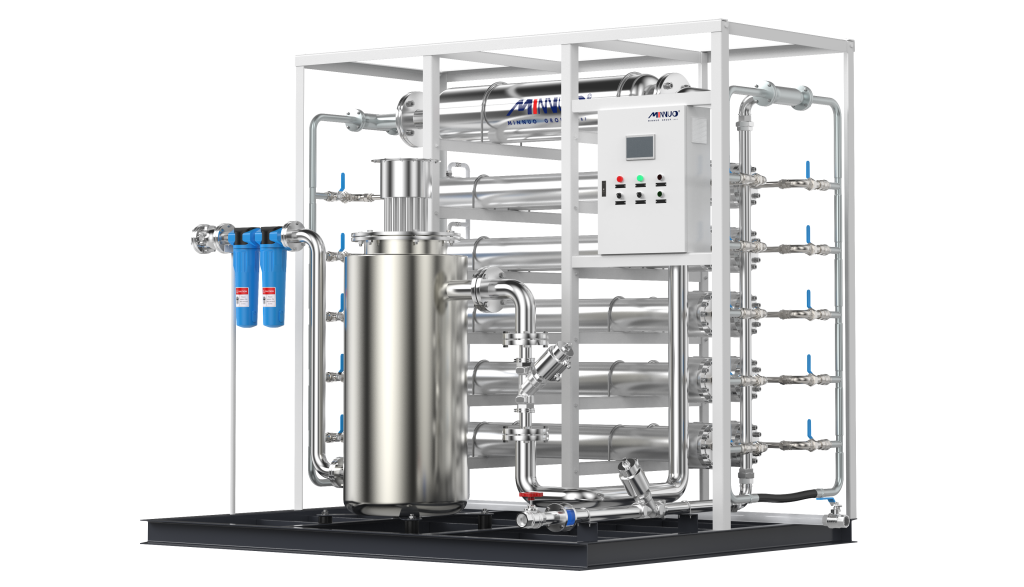
What is Membrane Separation Nitrogen Technology?
Definition
Membrane separation nitrogen technology is a gas separation method that leverages the differing permeation rates of gases through specific membrane materials to efficiently extract and purify nitrogen from air. This technology uses membrane-based nitrogen generation equipment, which takes ambient air as the raw material. Through selective permeation of the membrane, nitrogen is effectively separated from other components of the air, producing nitrogen with the desired purity for a variety of specialized applications.
Key Components
- Membrane Module: The core component of the membrane nitrogen generator is the membrane module, typically consisting of thousands of densely arranged hollow polymer fibers. These hollow fiber membranes have a unique microscopic structure, with pore size distribution and chemical properties carefully engineered to impart selective permeability to different gas molecules.
- Air Compressor: As the source of compressed air, the air compressor is responsible for compressing ambient air to a certain pressure, powering the subsequent gas separation process. It ensures that air enters the membrane module at the appropriate flow rate and pressure, enabling efficient gas separation.
Purity Range
In practical applications, nitrogen produced using membrane separation technology generally has a purity range that can be reliably controlled between 95% and 99.9%. This purity range is sufficient to meet the stringent nitrogen purity requirements in industries such as food preservation, plastic processing, and fire and explosion prevention.
How Membrane Separation Nitrogen Technology Works
The working principle of membrane separation nitrogen technology is based on the dissolution-diffusion mechanism of gases within the membrane material. When compressed air enters the membrane nitrogen generation unit’s membrane module, the membrane material exhibits different affinities and diffusion rates for various gas molecules. Below, we will discuss the key steps involved in membrane separation nitrogen technology: air pre-treatment, the membrane separation process, and tail gas treatment.
Air Pre-treatment
Before the mixed gas enters the membrane separation device, strict pre-treatment is usually required. This is because the raw gas may contain impurities such as solid particles, oil mist, and moisture. If these impurities are not removed, they can clog the membrane pores or affect the membrane’s performance, reducing separation efficiency. The pre-treatment steps include:
- Filtration: Multi-stage filters remove solid particles and other large impurities from the gas, ensuring the gas entering the membrane module is clean and uncontaminated.
- Cooling and Condensation: Moisture and oil mist are removed from the gas to prevent these liquid substances from damaging the membrane structure or affecting its permeability.
- Temperature Control: Precisely regulate the inlet temperature, as temperatures that are too high or too low can alter the physical properties of the membrane, affecting its selective permeability to different gases. Generally, the temperature should be maintained within a range that ensures stable performance of the membrane material.
- Pressure Control: Strictly control the inlet pressure, as the right pressure is key to generating an effective driving force for gas permeation across the membrane. Excessive pressure can damage the membrane, while insufficient pressure will hinder efficient gas separation.
This pre-treatment process ensures the stability and efficiency of the membrane separation system, laying a solid foundation for the subsequent nitrogen separation.
Membrane Separation Process
The pre-treated mixed gas enters the membrane separation module. The module typically consists of a large number of hollow fiber membranes or flat membranes, with hollow fiber membranes being widely used in membrane separation technology due to their structural characteristics. The gas flows on the outside of the membrane fibers, and a pressure difference exists across the membrane. This pressure difference drives the gas molecules to begin permeating the membrane wall.
- Gas Dissolution: Small gas molecules such as oxygen and water vapor in the air have a higher solubility on the surface of the membrane material. As a result, they preferentially dissolve into the polymer chains of the membrane.
- Diffusion Process: The dissolved gas molecules in the membrane material diffuse along the thickness of the membrane towards the other side due to the concentration gradient. Due to the selective permeability of the membrane for different gas molecules, gases with faster permeation rates (such as oxygen) will pass through the membrane wall more readily and enter the permeate side, while nitrogen will accumulate on the non-permeate side.
As the gas flows through the membrane module, the purity of the nitrogen gradually increases, ultimately producing nitrogen that meets the required specifications.
Product Gas Collection and Exhaust Gas Treatment
- Nitrogen Collection: On the non-permeable side of the membrane, the concentrated nitrogen is collected as the product gas. The purity of the product nitrogen can be precisely controlled by adjusting operational parameters, such as inlet flow rate, pressure, and the number of membrane stages. Through multi-stage membrane separation, nitrogen purity can be further improved to meet the needs of different industrial applications.
- Exhaust Gas Discharge and Treatment: The gas on the permeable side mainly consists of gases with a high permeation rate, such as oxygen and water vapor, which are typically discharged as exhaust. The treatment of exhaust gas can be further processed based on its composition and concentration, including the recovery of valuable gas components or harmless disposal through methods such as combustion.
Membrane separation nitrogen technology enables efficient nitrogen extraction through proper gas pretreatment, membrane separation, and exhaust gas treatment processes.
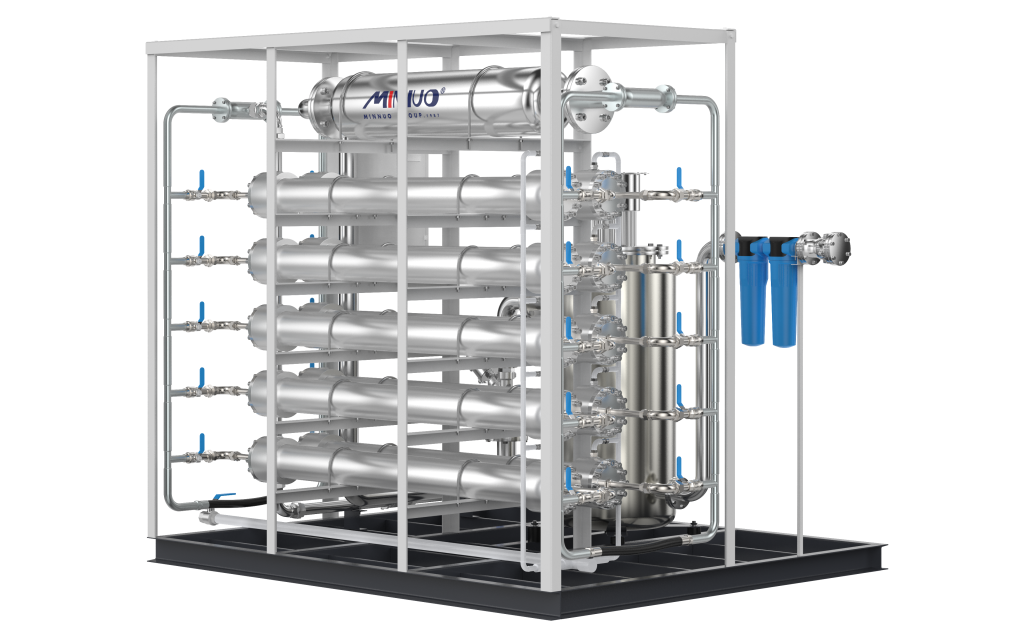
Key Advantages of Membrane Separation Nitrogen Technology
Precise Purity Control and Energy Efficiency
Membrane separation nitrogen technology allows users to precisely set nitrogen purity within a wide range of 95% to 99.9%, depending on specific production processes and application requirements. As the purity of nitrogen increases, there is a direct correlation with the consumption of compressed air, meaning excessively high purity settings can significantly increase energy consumption and operational costs. Therefore, by setting an appropriate nitrogen purity level, users can effectively optimize energy consumption, reduce production costs, and achieve efficient energy utilization while meeting production needs.
Sustainability and Environmental Benefits
By adopting membrane separation nitrogen technology for on-site nitrogen production, companies can avoid the large amounts of greenhouse gas emissions caused by long-distance transportation in traditional nitrogen purchasing models. Furthermore, if the membrane separation nitrogen system is integrated with renewable energy sources, such as solar or wind power, a green, low-carbon nitrogen production system can be established, helping companies achieve zero-carbon emissions in the nitrogen production process and promoting the transition of industrial production toward sustainable development.
Stable Product Quality
Membrane separation nitrogen technology, with its stable separation process and advanced membrane material properties, provides users with nitrogen products of highly stable purity. This stable nitrogen supply is crucial for industries that have strict production environment requirements and high product quality control precision, such as electronic chip manufacturing and high-end food processing. It effectively ensures the continuity of the production process and the consistency of product quality.
Low Maintenance Requirements and Long Service Life
The design of membrane nitrogen generators is relatively simple, with the core membrane separation process operating under a constant flow, requiring no complex moving parts. This characteristic leads to a low mechanical failure rate during operation, significantly reducing the frequency and cost of maintenance. Moreover, due to the excellent chemical stability and mechanical durability of the membrane material, under proper operating conditions, the membrane modules maintain stable performance over the long term, effectively extending the overall service life of the equipment.
Compact Equipment Structure and Space Efficiency
The membrane nitrogen generator adopts a modular, integrated design, resulting in a compact overall structure that takes up minimal floor space. Additionally, the equipment operates with minimal noise, allowing it to be installed directly within production workshops without the need for additional soundproofing or protective measures. This saves valuable production space and improves space utilization.
Convenient Operation and Flexible Scalability
The startup and commissioning process of the membrane nitrogen generator is quick and straightforward. Operators can master the equipment’s operation with short-term training. Furthermore, the equipment’s modular design allows users to easily increase or expand the number of membrane modules according to changes in production scale or increasing demand, enabling a gradual enhancement of nitrogen generation capacity. This makes the equipment highly scalable and adaptable.
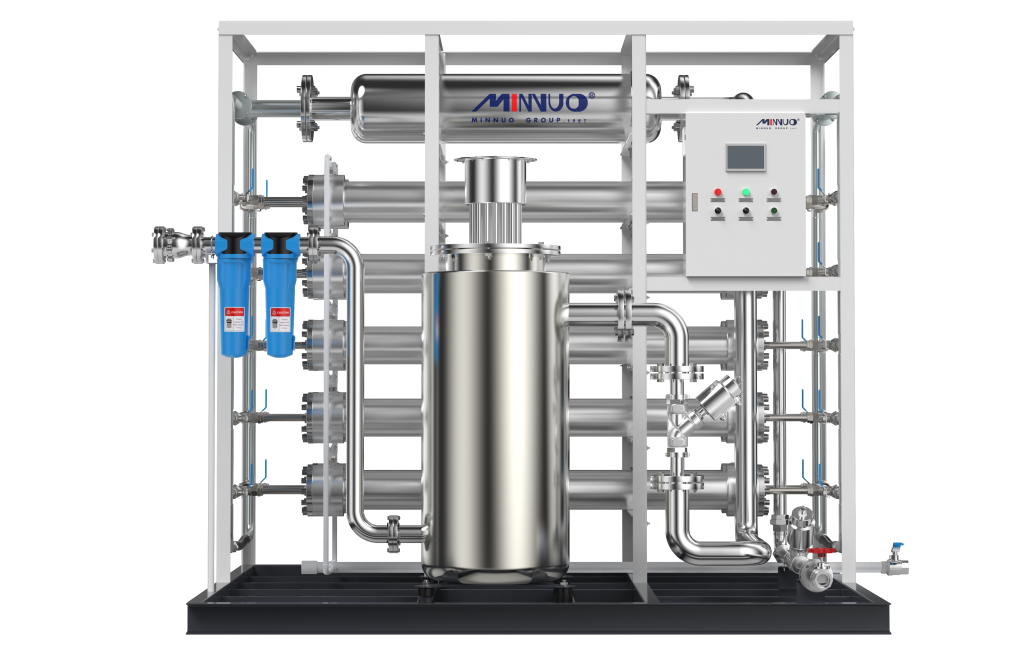
Applications of Membrane Separation Nitrogen Technology
Food Industry
In the field of food storage and preservation, membrane separation nitrogen technology is widely used in modified atmosphere packaging (MAP). By filling the package with high-purity nitrogen, which displaces oxygen and moisture, a low-oxygen, dry environment is created. This effectively inhibits the growth of microorganisms and the oxidation process of food, significantly extending its shelf life and preservation period.
Plastic Industry
In plastic injection molding, nitrogen is often used as an auxiliary gas. Injecting high-purity nitrogen into the mold cavity helps form a uniform pore structure inside the plastic products. This not only improves the molding quality and dimensional accuracy of the products but also reduces residual stress, minimizing deformation and defects in the final products.
Fire Safety Field
In hazardous and explosive environments, such as chemical warehouses and oil depots, membrane separation nitrogen technology can be used to create an inert air environment. By continuously filling the enclosed space with high-purity nitrogen, the oxygen level is reduced to below the combustion threshold of combustible materials, effectively preventing fires and explosions and ensuring the safety of personnel and property.
Oil and Petrochemical Industry
- Oil Field Extraction: Membrane separation nitrogen technology is crucial in oil field extraction, especially in later stages where reservoir pressure decreases. Nitrogen injection improves oil recovery by maintaining pressure and enhancing the oil-water flow ratio, making crude oil easier to extract. In low-permeability fields, this technology significantly boosts production, supporting efficient development.
- Offshore Oil and Gas Production: In the complex, high-risk offshore environment, nitrogen separation technology is widely used. It enhances oil recovery similar to onshore fields and is used for pipeline purging and displacement in natural gas production. High-purity nitrogen displaces air and impurities, preventing risks like explosions. It also helps inert flammable areas, reducing oxygen content and ensuring safety on offshore platforms.
Choosing Between Membrane Nitrogen Generators and PSA Nitrogen Generators
PSA nitrogen generators typically have a lower air factor, resulting in lower operating costs, which might make them seem like the obvious choice. However, membrane nitrogen generators also offer some distinct advantages. Firstly, their simpler operating principle helps reduce maintenance costs and saves space. Additionally, membrane generators have a faster start-up time and produce less noise during operation, whereas PSA generators often generate venting noise at the end of each gas cycle. This makes membrane nitrogen generators more suitable for environments with a high number of personnel. Therefore, when choosing the right type of nitrogen generator, it’s important to consider the specific application and weigh the pros and cons to make an informed decision.
Membrane | PSA | |
Achievable Purity | Up to 99.9% | Up to 99.9999% |
Efficiency | High | Higher |
Performance with Temperature | Higher at high temperatures* | Lower at high temperatures |
System Complexity | Low | Medium |
Maintenance Intensity | Very Low | Low |
Pressure Stability | Stable | Inlet/Outlet fluctuations |
Flow Stability | Stable | Inlet/Outlet fluctuations |
Start-up Speed | Seconds | Minutes/Hours** |
Sensitivity to Water (Vapor) | No liquid water allowed | PDP up to 8°C (typical) |
Sensitivity to Oil | No oil allowed (<0.01mg/m³) | No oil allowed (<0.01mg/m³) |
Noise Level | Very Low | High (venting peaks) |
Weight | Low | Medium |
*Depends on the type of membrane used **Depends on required purity and set-up time |
Conclusion
Membrane separation nitrogen technology offers excellent performance in energy conservation, environmental sustainability, stable product quality, and easy equipment maintenance, providing strong technical support for the development of modern industries.
MINNUO, as a professional gas equipment manufacturer with over 30 years of experience, welcomes any inquiries you may have. Feel free to contact us!