PSA (Pressure Swing Adsorption) technology plays a vital role in the field of oxygen production, offering a reliable and efficient method for gas separation. By utilizing the principle of pressure swing adsorption, PSA technology is widely used to separate gases such as oxygen and nitrogen for various industrial applications. Its core mechanism relies on selective adsorption and desorption processes, which ensure high purity and effective gas production. The size and capacity of PSA oxygen generators are essential factors for optimizing their operation, as they directly impact performance, energy efficiency, and overall output.
In this article, we will delve into the critical factors that influence the optimal size and capacity of PSA oxygen generators in industrial settings. We will address key considerations such as required flow rates, purity levels, and operating pressures, offering insights into how these parameters affect system design and efficiency. Our aim is to provide a comprehensive understanding of how to calculate the most suitable size and capacity for PSA oxygen generators to ensure they meet the specific demands of industrial applications while maintaining optimal performance and energy consumption.
By exploring the intricacies of PSA oxygen generator sizing and capacity calculation, this article will serve as a valuable resource for engineers and professionals involved in designing and optimizing PSA systems. We will not only provide a step-by-step approach to understanding the factors that affect PSA system sizing but also offer practical strategies for making informed decisions based on operational requirements. Whether you are designing a new PSA oxygen generator or optimizing an existing system, the knowledge shared here will guide you in achieving more efficient and effective gas separation operations.
I. Key Factors Affecting the Scale and Capacity of PSA Oxygen Generators
Gas Flow Requirement:
In designing PSA oxygen generators, it is crucial to understand the required flow of oxygen for the intended application. This flow rate is a fundamental factor in determining both the size and capacity of the generator.
Different industries, such as medical, chemical, and manufacturing sectors, have varying gas flow requirements.
For instance:
Medical applications require a steady supply of oxygen at a purity of 93% (with a typical flow rate of 5-10 LPM).
Industrial applications require oxygen at a lower purity level (around 90%), but at a much higher flow rate (ranging from 50-200 LPM depending on the size of the operation).
Understanding the flow rate requirement is essential because it directly influences both the design of the adsorption tower and the capacity of the PSA system. A higher flow rate requires a larger system with a higher number of adsorption beds to efficiently process the gas without compromising separation efficiency.
Oxygen Purity Requirements:
The purity level required for the target application plays a crucial role in determining the scale of the PSA system. Purity is typically dictated by the industry standards and safety regulations, such as:
Medical oxygen generally needs to meet a purity level of 93%, with the ability to maintain consistent oxygen quality.
For industrial uses, the oxygen purity might be acceptable at a lower level (90%).
The purity requirement impacts the design of the oxygen separation system, including the selection of molecular sieve materials and the cycle times for adsorption and desorption. A system designed for high purity will often require more advanced molecular sieves, longer processing times, and larger systems to ensure the gas separation is optimal without compromising the operational efficiency.
Pressure and Operational Conditions:
The pressure at which the PSA system operates is critical for its efficiency. High pressures help improve gas adsorption rates, leading to better separation performance. However, higher pressure also means that the system will require more energy to compress the air, increasing operating costs.
For industries requiring higher oxygen purity, such as healthcare, the PSA system typically operates at higher pressures (e.g., 4-6 bars) to improve the adsorption and separation process. At the same time, it is important to balance the increased pressure with the system’s overall energy efficiency. Ensuring that the system operates at optimal pressure levels can significantly impact both system performance and operational costs.
Temperature and Environmental Factors:
The surrounding environmental conditions, such as ambient temperature and humidity, also affect the operation and design of the PSA oxygen generator. Systems designed for high-temperature environments or regions with fluctuating temperatures need to account for these factors in the design stage.
Temperature variations can influence the adsorption properties of the molecular sieves, affecting their ability to separate oxygen from nitrogen. Therefore, designing systems with efficient cooling mechanisms or ensuring that the generator is placed in a stable environment is crucial for maintaining performance.
Moreover, the efficiency of the generator can be impacted by external factors such as high humidity, which can degrade the adsorbent material over time. In such cases, additional filters or pre-treatment processes may be needed to protect the system from premature wear.
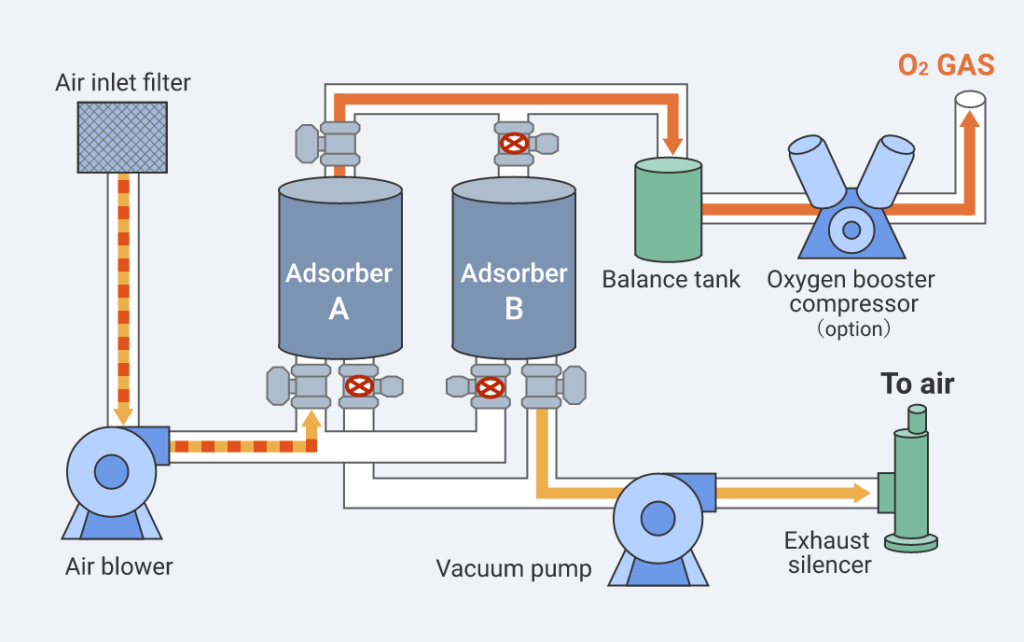
II. Calculating Optimal Size and Capacity
Gas Flow and Oxygen Production Capacity
The capacity of a PSA oxygen generator is primarily determined by the required gas flow rate for the specific application. The key here is calculating the appropriate flow rate that ensures optimal performance without oversizing the system, which could lead to unnecessary energy consumption.
Gas Flow Calculation Formula:
To calculate the optimal size of the oxygen generator, the following formula is used:
Capacity (Nm³/h)=Gas Flow (Nm³/h)×Pressure×Purity
Where:
Gas Flow (Nm³/h) is the volume of gas that the system will handle per hour.
Pressure refers to the operational pressure that influences the adsorption and desorption process.
Purity is the percentage of oxygen required, as dictated by the application (e.g., 93% purity for medical use or 90% for industrial use).
By using this formula, the design of the PSA system can be optimized for both efficiency and cost. The flow rate needs to be accurately determined to avoid waste or underperformance. Moreover, system size should match the required gas flow, considering operational pressure and purity levels.
Optimizing Purity and Flow Rate
Purity is a critical factor in the design and operation of PSA systems. Depending on the application, a specific purity level of oxygen needs to be achieved (e.g., 93% for medical use or 90% for industrial uses). The process involves adjusting the system’s flow rate to maintain the required purity while ensuring the generator is capable of handling higher volumes when necessary.
To optimize the purity and flow rate:
The system must be calibrated to adjust its adsorption cycle according to the required purity.
The design should allow for flexibility in scaling up or down based on demand while maintaining the desired gas quality.
For example, if a PSA system is designed for medical-grade oxygen with a purity of 93%, the design must incorporate sufficient capacity for the necessary adsorbent beds and extended cycle times to achieve this purity consistently.
Capacity Expansion and Scalability
The scalability of the PSA system design is essential for ensuring that the system can handle future growth in demand. As industries grow or the application expands (such as additional facilities or new medical applications), the system should be capable of handling increased volumes of oxygen production without needing an entirely new system.
To achieve scalability:
The system design must include flexibility in its configuration (e.g., modular adsorbent beds or flexible piping).
The ability to expand the system’s capacity should be built into the design from the outset. This could include considerations like larger molecular sieve beds or an extra adsorption tower that can be added later.
Designing for Future Capacity
Anticipating future oxygen demand is crucial to ensuring that the PSA system remains effective over its lifespan. Proper design practices should account for future scalability by incorporating efficient control systems, expandable parts, and the use of high-performance adsorbent materials.
For instance, engineers might design a PSA oxygen generator with higher capacity than current demand, taking into account the potential for future demand spikes in industries like healthcare, which may require sudden increases in oxygen supply.
By carefully calculating and designing systems to meet both current and future needs, PSA oxygen generators can avoid premature system upgrades and prevent inefficiencies from unused capacity. Additionally, future-proofing the system helps to accommodate a growing range of applications, from industrial to medical environments, while keeping operational costs low.
III. Practical Considerations for Selecting PSA Oxygen Generator Size
Design Efficiency and Size Optimization
When selecting the size of a PSA oxygen generator, it is crucial to strike a balance between capacity, operational efficiency, and cost-effectiveness. Oversizing the system could lead to unnecessary energy consumption and operating costs, while undersizing it may result in insufficient oxygen production to meet demand, causing system strain and reduced efficiency.
To optimize the system size:
Evaluation of Flow Rates and Power Consumption: The required oxygen flow rate is the most important factor when determining the optimal size of the PSA system. By considering the required purity and flow rate, we can design a system that minimizes energy loss while maximizing performance. For example, larger systems designed for medical use must be sized to provide a consistent flow of oxygen at high purity levels (e.g., 93%), without overloading the system.
Capacity and Energy Consumption Balance: A critical part of selecting the system size is evaluating the relationship between the flow rate and energy consumption. Systems should be designed to minimize energy loss by avoiding overproduction of oxygen that exceeds the system’s requirements. This ensures that operational costs remain sustainable while meeting user demands.
Energy Efficiency and Operational Cost
One of the main goals in selecting the optimal size for a PSA oxygen generator is to minimize energy consumption while ensuring high operational efficiency. The energy cost of running an oversized system can significantly impact the overall cost-effectiveness of the PSA system, which is why a balance between size, energy requirements, and performance should be considered.
Optimizing for Energy Use: It is essential to design a system that uses energy efficiently, thereby reducing operational costs. This can be achieved through efficient cycle time management and regulating pressure swings that prevent energy waste. The design should also account for variable operating conditions, where the system should adapt to fluctuations in demand without compromising efficiency.
Cost Reduction Through Energy Optimization: Another consideration when optimizing for energy is using variable-speed drives or energy-saving devices that allow the system to adjust its energy consumption dynamically based on real-time demand. This approach significantly reduces unnecessary energy use, especially during low-demand periods.
Maintenance and System Longevity
The selection of PSA oxygen generator size also directly impacts its long-term maintenance needs and operational lifespan. A well-designed system should not only fulfill immediate demands but also minimize wear and tear over its operational life.
Impact of System Size on Maintenance: Larger PSA systems tend to require more maintenance due to their increased complexity. For instance, a system designed to handle significantly higher capacities than required might face more frequent repairs or component replacements. On the other hand, under-sized systems may struggle with maintenance issues caused by overuse.
Design for Longevity: It is critical to select the optimal system size that allows for efficient use of components, reducing the frequency of repairs. For example, using high-quality adsorbent materials that provide long-term durability will improve the overall longevity of the system. Similarly, designing the system with modular components allows for easier upgrades and maintenance without disrupting the operation.
Considering Future Growth and Flexibility
The PSA system must also be adaptable to future growth, especially in industries like healthcare and industrial production, where oxygen demand may increase over time. A generator designed with growth in mind can help avoid the need for complete system replacement or major adjustments down the line.
Planning for Future Expansion: The system should be designed to handle future capacity requirements by ensuring that it can be scaled up without significant redesigns or equipment replacements. This can be achieved through modular designs that allow for easy addition of components like additional adsorption beds or compressors.
Flexibility in Design: A flexible system design can cater to varying operational conditions, such as seasonal demand fluctuations or changes in regulations. PSA systems should be built to accommodate shifts in operational requirements without major overhauls, allowing for long-term use in a variety of settings.

IV. Case Studies
Case Study 1: Medical Facility PSA Oxygen Generator Design
In medical and healthcare settings, the design of PSA oxygen generators must meet stringent requirements for both size and capacity. Medical facilities require a stable, reliable, and pure oxygen supply to ensure patient safety, especially in critical care environments. These environments require a specific gas flow rate, purity, and pressure level to meet the medical standards for oxygen delivery.
Flow Rate and Purity Requirements in Medical Applications:
For hospitals, the required purity is typically around 93%, while industrial-grade systems may only need 90%. This ensures that the oxygen provided is safe and meets medical standards for patient care. The required flow rate can vary significantly depending on the size and number of patients being served, so the system must be scalable to handle peak demands.
Pressure Considerations:
Pressure requirements also play a critical role. Medical facilities need a reliable source of oxygen with stable pressure to ensure the consistent delivery of oxygen throughout the building. The design of the PSA oxygen generator must accommodate the range of pressures necessary for the distribution system within the hospital. Additionally, consideration must be given to regulatory standards that ensure the equipment meets medical-grade specifications.
Key Design Considerations:
When designing PSA oxygen generators for medical use, one must ensure that the system can maintain continuous operation, even during periods of high demand. Flexibility in the system’s design allows for adaptation to future demand increases, such as those seen in emergency situations or during seasonal surges in healthcare needs. Additionally, considering the long-term durability of the system and ensuring that maintenance requirements are minimal is crucial in a healthcare setting.
Case Study 2: Industrial PSA Oxygen Generator Design
In industrial environments, the need for oxygen generation can vary widely based on the specific industrial applications, such as metal cutting, welding, or chemical manufacturing. The scale of the PSA oxygen generator must be designed to match the flow rates and pressure requirements of the facility’s operations.
Flow Rate and Pressure Needs in Industrial Applications:
Industries that use oxygen for combustion processes or for enhancing production efficiency often have higher flow rate requirements than medical facilities. For instance, large manufacturing plants that use oxygen in furnaces or for chemical reactions may require flow rates ranging from 4,000 to 10,000 Nm³/h. These industrial applications demand a consistent, high-flow supply of oxygen at a specified pressure to ensure efficient operations.
Design Considerations Based on Flow Rate and Purity:
Unlike medical facilities, the purity requirements for industrial PSA oxygen generators may be lower, with many applications only requiring around 90% purity. However, the generator must be able to provide oxygen at high flow rates and under varying load conditions, which is often a critical factor in meeting the productivity goals of industrial applications.
Energy Efficiency and System Design:
In an industrial context, energy efficiency is a top concern, as running large-scale oxygen generators for extended periods can result in significant energy consumption. To mitigate this, the generator must be optimized for energy savings, including the use of advanced technologies such as variable-speed drives and automated cycle time adjustments. Additionally, ensuring that the system is modular allows for easy upgrades as future production needs grow.
Future Scalability:
Considering future expansion, the design of PSA oxygen generators for industrial applications must account for possible increases in oxygen demand. This scalability ensures that the system can handle higher flow rates or meet more stringent purity standards as needed, without requiring a complete system overhaul.
Conclusion
In calculating the optimal size and capacity of PSA oxygen generators for industrial applications, it is essential to focus on factors such as required flow rate, purity, pressure, and system efficiency. Optimizing these factors ensures the generator meets the specific needs of different industries, resulting in a high-quality, energy-efficient, and cost-effective operation.
MINNUO’s advanced PSA oxygen generation solutions are designed with an emphasis on efficiency, energy savings, and scalability to meet the diverse requirements of various industries. By prioritizing factors such as gas flow rate, purity, and pressure optimization, MINNUO ensures that the generated oxygen meets the highest standards for industrial applications, all while considering future growth needs.
With MINNUO’s expertise in PSA system design and its commitment to delivering optimized, reliable, and energy-efficient solutions, industrial applications can achieve high-performance gas generation systems tailored to their needs, helping them increase productivity and reduce operational costs.