In today’s industrial landscape, on-site nitrogen generation has become a vital solution for businesses seeking cost control, operational independence, and uninterrupted gas supply. Two leading technologies—Pressure Swing Adsorption (PSA) and membrane separation—dominate the market, each offering unique advantages in terms of nitrogen purity, energy consumption, footprint, and maintenance. As more industries shift from cylinder or liquid nitrogen deliveries to on-demand generation systems, understanding the differences between these technologies is essential for smart capital planning and performance optimization.
Choosing the right nitrogen generation system isn’t just about upfront cost—it affects long-term efficiency, output stability, and operational compatibility with your specific application. For example, a food processor concerned with product shelf life may prioritize ultra-high purity, while a tire manufacturer may value low cost and mobility. Therefore, knowing whether membrane or PSA is better suited for your business use case could mean the difference between streamlined production and constant troubleshooting.
This article dives deep into the comparison between PSA and membrane nitrogen generators, analyzing their respective strengths and limitations across six key dimensions: nitrogen purity, flow rate, energy efficiency, system footprint, maintenance, and operating cost. Whether you’re an engineer evaluating specs or a procurement manager planning long-term ROI, this guide is designed to help you make a data-driven, application-specific decision.
I. How the Two Technologies Work
To understand which nitrogen generation method—PSA or membrane—is better for industrial use, it’s essential to first examine how each technology operates, their core mechanisms, and where they excel.
1. PSA (Pressure Swing Adsorption) Overview
PSA technology relies on the principle of selective adsorption, using carbon molecular sieves (CMS) to separate nitrogen from compressed air. Under high pressure, oxygen and other gases are preferentially adsorbed by the sieves, while nitrogen passes through as the product gas. The system then depressurizes to desorb the captured gases and regenerate the adsorbent.
Separation Principle: Selective adsorption of oxygen and other gases onto CMS
Typical Nitrogen Purity Range: 95%–99.999%, suitable for high-end industrial applications
System Configuration: Dual adsorption towers alternate between adsorption and regeneration
Key Advantage: Delivers high-purity nitrogen with stable output, ideal for precision manufacturing
Limitation: Higher initial cost, larger footprint, and more complex controls
PSA is best suited for industries like electronics, laser cutting, food packaging, and pharmaceuticals, where purity and consistency are critical.
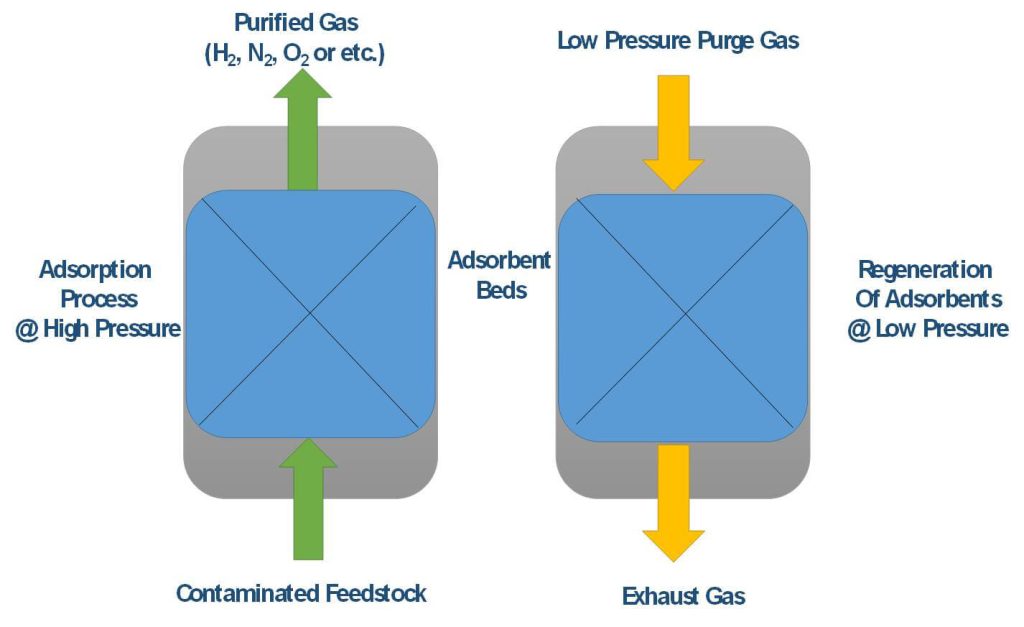
2. Membrane Separation Overview
Membrane nitrogen generation systems use selective gas permeability to separate gases through polymer fiber bundles. Gases like oxygen, carbon dioxide, and water vapor permeate faster through the membrane, while nitrogen passes through at a slower rate, resulting in an enriched nitrogen stream.
Separation Principle: Selective gas diffusion through hollow fiber membranes
Typical Nitrogen Purity Range: 90%–99%, depending on design and flow rate
System Configuration: Single-stage, continuous-flow with no regeneration cycle
Key Advantage: Compact, low maintenance, quick startup time
Limitation: Limited to medium-purity applications and less precise purity control
Membrane systems are widely used in applications such as tire filling, fire prevention, inerting, and oil & gas offshore installations where simplicity and speed outweigh purity demands.
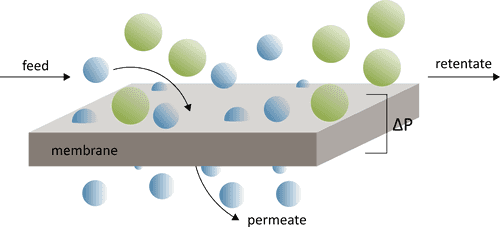
Summary Comparison Table
Feature | PSA System | Membrane System |
Nitrogen Purity | Up to 99.999% | Up to 99% |
Startup Time | Several minutes | <1 minute |
Footprint | Larger | More compact |
Maintenance | Moderate (valves/sieves) | Low (few moving parts) |
Best Use Cases | High-purity manufacturing | On-site, mobile, general inerting |
II. Comparison Criteria
When choosing between membrane and PSA nitrogen generation technologies, industrial decision-makers should consider several key factors that influence performance, cost, and suitability for specific applications. Here’s a comprehensive breakdown of how the two systems compare across six core criteria:
1. Nitrogen Purity
PSA Systems:
PSA technology excels at delivering high-purity nitrogen (typically 95%–99.999%), making it the preferred choice for electronics, food processing, pharmaceuticals, and chemical manufacturing where purity is critical to product quality and compliance.
Membrane Systems:
Best suited for medium-purity applications (90%–99%), such as tire inflation, fire prevention systems, and nitrogen inerting in oil & gas. While they can’t reach ultra-high purity levels, they are often sufficient for general industrial use.
Takeaway: If your application demands >99.5% nitrogen, PSA is the clear winner.
2. Flow Rate and Response Time
Membrane Systems:
Offer instant start-up with minimal warm-up time, providing near-immediate nitrogen output. Ideal for mobile units, intermittent use, or facilities requiring quick access to nitrogen on demand.
PSA Systems:
Require a few minutes to stabilize but offer precise flow control for continuous and regulated supply. This is particularly important for high-purity processes or production lines with consistent demand.
Takeaway: Choose membrane systems for speed, PSA systems for consistency and precision.
3. Energy Efficiency
Membrane Systems:
Typically consume less energy as they operate with continuous low-pressure air and have no adsorption/desorption cycling. This results in a lower energy-per-Nm³ ratio for medium-purity production.
PSA Systems:
Use more energy, especially during frequent cycling and regeneration phases. However, energy efficiency improves with larger systems and optimized compressors.
Takeaway: For low to medium purity, membranes win on energy; for large-scale high-purity, PSA’s energy cost is offset by output quality.
4. System Footprint and Portability
Membrane Systems:
Compact, lightweight, and easier to install in constrained spaces or on mobile platforms (e.g., lab benches, trucks, offshore rigs). Their integration into existing systems is typically more straightforward.
PSA Systems:
Generally larger due to dual towers, compressors, and storage tanks. However, modular PSA skids are increasingly common, enabling flexible layout and expansion.
Takeaway: Membranes suit space-limited or mobile needs; PSA fits fixed or scalable operations.
5. Maintenance and Lifetime
Membrane Systems:
Have fewer moving parts and minimal mechanical wear. Routine maintenance involves only filter replacements and occasional membrane inspection. Service intervals can be long, making them ideal for unmanned or remote sites.
PSA Systems:
Require regular checks on valves, compressors, and sieve beds. The molecular sieve may need replacement every 3–5 years, depending on use and air quality.
Takeaway: Membranes = low maintenance; PSA = long-term durability, but higher upkeep.
6. Operating Costs
Initial Investment:
Membrane systems are generally cheaper upfront due to simpler design and no moving parts.
PSA systems require higher initial costs, especially for high-purity configurations and backup compressors.
Long-Term Cost:
PSA is more cost-effective when producing large volumes of nitrogen at high purity over time.
Membranes are more economical for low-flow or intermittent use.
Takeaway: Consider TCO (Total Cost of Ownership)—membranes save short-term, PSA pays off long-term for high-purity demand.
III. Application Scenarios
Choosing between PSA and membrane nitrogen generators depends heavily on the specific requirements of the application—such as desired purity, usage frequency, environmental constraints, and portability. Below is an in-depth analysis of industries where each technology excels.
1. Industries Best Suited for PSA Systems
PSA nitrogen generators are ideal for applications that demand high purity, stable flow, and continuous operation. Their modular design and advanced control systems make them reliable for mission-critical environments.
Food Packaging
Nitrogen is used to flush out oxygen and moisture from packaged food, extending shelf life and preserving quality. PSA systems provide the consistent >99.5% purity required for sensitive items like meats, dairy, and snacks.
Electronics Manufacturing
Soldering, reflow ovens, and semiconductor processes rely on ultra-high purity nitrogen (99.999%) to avoid oxidation and contamination. PSA systems are capable of achieving these demanding purity levels with stable pressure and flow.
Laser Cutting
Laser cutting of metals (especially stainless steel and aluminum) requires nitrogen to prevent oxidation and produce clean edges. PSA systems provide the high flow and high pressure needed for industrial-scale cutting operations.
Oil & Gas Inerting
In upstream and downstream processes, nitrogen is used to displace oxygen in tanks and pipelines to prevent combustion. PSA generators are better suited for these operations because they offer purity control, larger volumes, and continuous output.
✅ Why PSA?
Choose PSA when purity >95%, steady demand, and integration with automation systems are critical.
2. Industries Best Suited for Membrane Systems
Membrane nitrogen generators excel in medium-purity (<99%), space-limited, and intermittent-use applications. They are portable, low-maintenance, and quick to deploy.
Tire Filling and Transport
Membrane systems are commonly mounted on vehicle service trucks for nitrogen tire inflation. Their compact design, low power consumption, and quick start-up make them perfect for mobile use.
Fire Suppression Systems
Inerting rooms or protecting equipment (e.g., data centers, switchgear rooms) often requires 90–95% purity nitrogen. Membrane systems offer on-demand flow without complex maintenance.
General Nitrogen Blanketing
Applications like chemical drum blanketing or small tank headspace coverage require moderate nitrogen flow with no cycling delays. Membrane systems can deliver this efficiently with minimal overhead.
Offshore and Mobile Use
In marine vessels, offshore platforms, and emergency mobile units, space and energy are limited. Membrane systems offer plug-and-play simplicity, lightweight housing, and can even be solar-powered in remote locations.
✅ Why Membrane?
Choose membrane systems when medium purity (90–98%), compact footprint, and portability are top priorities.
Application Area | Recommended Technology | Key Reason |
Electronics & Semiconductors | PSA | Ultra-high purity (≥99.999%) |
Food Packaging | PSA | Long shelf life, purity ≥99.5% |
Mobile Tire Service | Membrane | Compact, low-maintenance, 95% purity is enough |
Fire Protection Systems | Membrane | Quick-start, 90–95% acceptable |
Laser Cutting | PSA | High flow & pressure, steady supply |
Offshore Platforms | Membrane | Lightweight, plug-and-play, limited space |
IV. Hybrid Systems and Future Trends
As industrial users increasingly demand nitrogen at varying purity levels, traditional single-method nitrogen generation systems—such as PSA or membrane alone—are facing limitations in application scope. In response, the industry is moving toward more flexible and efficient hybrid system designs, supported by intelligent controls, to drive continuous evolution of nitrogen generators across three key dimensions: precision, energy efficiency, and intelligence.
1. Use of Membrane + PSA Combinations for Tiered Purity Needs
In many industrial scenarios, nitrogen is required at multiple purity levels, such as:
90–95%: Fire protection, tire inflation, hypoxic environments
95–99.9%: Food packaging, laser cutting
99.999%+: Semiconductors, electronics, pharmaceuticals
To address this, membrane + PSA hybrid processes are becoming mainstream solutions:
Working Mechanism:
Stage 1: Membrane Separation
Removes oxygen and moisture to produce medium-purity nitrogen (90–95%) efficiently with low energy consumption.
Stage 2: PSA Purification
PSA modules further purify nitrogen to 99.9% or higher, meeting the requirements of electronics-grade or sensitive processes.
Advantages:
Significantly reduces PSA load and operating costs
Combines the fast response of membranes with the high-purity capability of PSA
Supports complex scenarios such as tiered nitrogen supply and multi-purpose usage from a single unit
✅ Typical Applications: Electronics nitrogen plants, pharmaceutical production chains, centralized nitrogen supply hubs
2. Advances in Modular PSA and Miniaturized Membrane Systems
Future-oriented designs focus on “small but powerful” systems that combine high performance with superior flexibility and scalability.
Modular PSA Systems:
LEGO-style construction: Compressors, adsorption units, and control modules are divided into standardized components, enabling phased expansion or production line-specific customization
Rapid deployment: Ideal for new production lines, temporary projects, or locations with uncertain demand
Miniaturized Membrane Systems:
Embedded designs: Suitable for 19-inch cabinets, mobile trolleys, and vehicle-mounted supply units
Edge deployment scenarios: Mobile service vehicles, small laboratories, remote mining sites
Miniaturization is driving the transition of nitrogen systems from centralized supply to distributed edge deployment
3. Role of Intelligent Controls in Optimizing System Efficiency
As carbon neutrality and industrial intelligence become dominant themes, both PSA and membrane systems are increasingly adopting AI-driven intelligent control strategies.
Key Technologies:
Sensor networks + edge AI computation: Real-time monitoring of oxygen concentration, pressure, temperature, flow rate, and more
Load-adaptive adjustment algorithms: Automatically reduce system load and extend switching cycles during gas consumption fluctuations, lowering energy consumption
Predictive maintenance: Leverages operational data to detect fault trends early, reducing maintenance costs
✅ Typical Benefits:
10–25% energy savings
Extended equipment lifespan
Improved gas supply stability
Trend | Problem Solved | Application Value |
Membrane + PSA Hybrid | One-stop solution for multiple purity needs, cost-saving | Precision nitrogen supply for multi-process industrial setups |
Modular / Miniaturized | Space constraints, fast deployment, flexible expansion | Deployable to workshops, edge locations, mobile service units |
Intelligent Control Systems | Enhanced automation, reduced energy and fault rates | Cost reduction, efficiency gain, alignment with energy policies |
Concluison
When comparing membrane and PSA nitrogen generators, there is no one-size-fits-all solution. Each technology has its advantages: membrane systems offer compact design, lower upfront costs, and faster response times—ideal for medium-purity needs and mobile or space-constrained environments. In contrast, PSA systems provide higher nitrogen purity, long-term cost-effectiveness, and better performance for demanding industrial processes like electronics manufacturing, laser cutting, and food packaging. The right choice depends on your specific application, desired purity, flow rate, footprint constraints, and energy priorities.
At MINNUO, we specialize in both membrane and PSA nitrogen generation systems, offering tailored solutions to match your unique industrial needs. Whether you’re looking to upgrade a high-volume nitrogen line or implement a mobile nitrogen source for on-site operations, our engineering team will help you select and integrate the best-fit system. With modular designs, intelligent controls, and support for high-purity or energy-sensitive applications, MINNUO delivers efficient, reliable gas generation—empowering industries to reduce costs and operate sustainably.